- お役立ち記事
- The difference between Material Management and Parts Management
The difference between Material Management and Parts Management
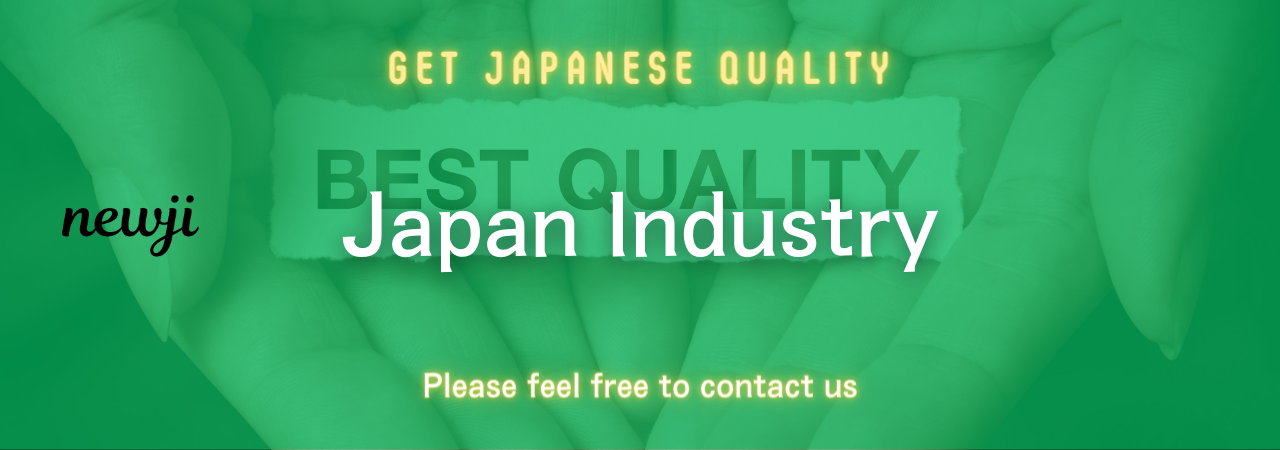
目次
Understanding Material Management
Material management refers to the process of planning, acquiring, storing, and distributing materials that are required for a company’s operations.
This process ensures that the right materials are available at the right time and in the right quantity to meet production demands.
Effective material management helps companies minimize costs, avoid delays, and maintain efficient workflow.
In any industry, materials can include raw materials, semi-finished goods, and components that are used to manufacture a product.
Material management is crucial for maintaining the quality and consistency of production processes.
Importance of Material Management
Material management is vital for several reasons.
First, it helps in optimizing the use of resources.
Efficiently managing materials reduces waste and lowers costs.
This directly impacts a company’s bottom line.
Second, it ensures that production processes are uninterrupted.
Unavailability of materials can lead to production delays, which can be costly.
Proper material management ensures that materials are available when needed, ensuring smooth operations.
Third, it aids in maintaining the quality of the final product.
Proper storage and handling of materials prevent damage and degradation, maintaining their quality.
Lastly, material management enhances supply chain efficiency.
By coordinating with suppliers and managing inventory levels, companies can streamline their supply chain processes.
Exploring Parts Management
Parts management, on the other hand, refers to the process of managing the various parts and components that are used in manufacturing and maintaining machinery, equipment, and products.
Parts management involves tracking parts usage, maintaining inventory levels, and ensuring that parts are available when needed.
In many industries, parts can be small components or even critical pieces required to keep machinery running smoothly.
Effective parts management is essential for the maintenance and repair of equipment, ensuring that production processes are not disrupted by equipment failure.
Importance of Parts Management
Parts management is crucial for a variety of reasons.
Primarily, it ensures the availability of spare parts when machinery and equipment need repairs.
This helps in minimizing downtime and maintaining continuous production processes.
Secondly, parts management helps in controlling inventory costs.
By maintaining optimal inventory levels, companies can avoid overstocking, which can tie up capital and increase storage costs.
Conversely, avoiding understocking prevents delays in repairs and maintenance.
Additionally, it aids in prolonging the lifespan of machinery and equipment.
Properly managing and maintaining parts ensures that equipment operates efficiently and lasts longer, reducing the need for frequent replacements.
Furthermore, parts management helps in enhancing operational efficiency.
By keeping track of parts usage and planning for maintenance, companies can prevent unexpected equipment failures and optimize their production schedule.
Key Differences Between Material Management and Parts Management
While both material management and parts management are essential for efficient operations, they differ in several key aspects.
Scope of Management
Material management covers a broad range of activities, including planning, purchasing, storing, and distributing materials needed for production.
It encompasses raw materials, semi-finished goods, and other components used in manufacturing.
In contrast, parts management specifically focuses on managing spare parts and components required for the maintenance and repair of machinery and equipment.
Its scope is narrower, concentrating on ensuring the availability of parts necessary to keep equipment operational.
Inventory Management
Material management involves managing a wide range of inventory, which includes raw materials, work-in-progress items, and finished goods.
It requires a comprehensive approach to ensure that the entire production process runs smoothly.
Parts management, however, deals primarily with maintaining an inventory of spare parts and components.
This involves tracking parts usage, forecasting demand, and ensuring the availability of critical parts for maintenance purposes.
Objective
The primary objective of material management is to ensure the availability of necessary materials for production while minimizing costs and maximizing efficiency.
It focuses on the overall production process and the timely availability of materials.
On the other hand, the main objective of parts management is to ensure that spare parts are available when needed for the maintenance and repair of equipment.
It aims to reduce downtime and maintain the operational efficiency of machinery.
Cost Considerations
Material management aims to minimize the costs associated with purchasing, storing, and handling materials.
It involves negotiating with suppliers, managing inventory levels, and optimizing storage to reduce expenses.
Parts management focuses on controlling costs related to spare parts inventory.
This includes managing stock levels, avoiding overstocking, and ensuring timely procurement to prevent production delays.
Integrating Material and Parts Management
While material management and parts management are distinct functions, integrating them can lead to significant benefits for a company.
By coordinating these processes, companies can achieve greater operational efficiency and cost savings.
For instance, integrating material management with parts management can help in better forecasting and planning.
By understanding the material requirements for production and the parts needed for maintenance, companies can optimize their procurement and inventory management processes.
Additionally, integrating these functions can streamline communication between departments.
This ensures that there is a consistent flow of information regarding material and parts requirements, reducing the risk of miscommunication and delays.
Furthermore, integrated management can enhance overall supply chain efficiency.
By aligning material and parts management processes, companies can streamline their supply chains, reduce lead times, and improve responsiveness to changes in demand.
Conclusion
In summary, both material management and parts management play crucial roles in the efficient operation of a company.
While material management focuses on the broader scope of acquiring, storing, and distributing materials for production, parts management concentrates on managing spare parts for maintenance and repair.
Understanding the differences between these two functions is essential for optimizing operations and achieving cost savings.
By integrating material and parts management processes, companies can enhance their overall efficiency, reduce costs, and ensure smooth production workflows.
By maintaining a well-organized system for managing both materials and parts, businesses can stay competitive and responsive to market demands.
資料ダウンロード
QCD調達購買管理クラウド「newji」は、調達購買部門で必要なQCD管理全てを備えた、現場特化型兼クラウド型の今世紀最高の購買管理システムとなります。
ユーザー登録
調達購買業務の効率化だけでなく、システムを導入することで、コスト削減や製品・資材のステータス可視化のほか、属人化していた購買情報の共有化による内部不正防止や統制にも役立ちます。
NEWJI DX
製造業に特化したデジタルトランスフォーメーション(DX)の実現を目指す請負開発型のコンサルティングサービスです。AI、iPaaS、および先端の技術を駆使して、製造プロセスの効率化、業務効率化、チームワーク強化、コスト削減、品質向上を実現します。このサービスは、製造業の課題を深く理解し、それに対する最適なデジタルソリューションを提供することで、企業が持続的な成長とイノベーションを達成できるようサポートします。
オンライン講座
製造業、主に購買・調達部門にお勤めの方々に向けた情報を配信しております。
新任の方やベテランの方、管理職を対象とした幅広いコンテンツをご用意しております。
お問い合わせ
コストダウンが利益に直結する術だと理解していても、なかなか前に進めることができない状況。そんな時は、newjiのコストダウン自動化機能で大きく利益貢献しよう!
(Β版非公開)