- お役立ち記事
- The difference between Material Management and Parts Management
The difference between Material Management and Parts Management
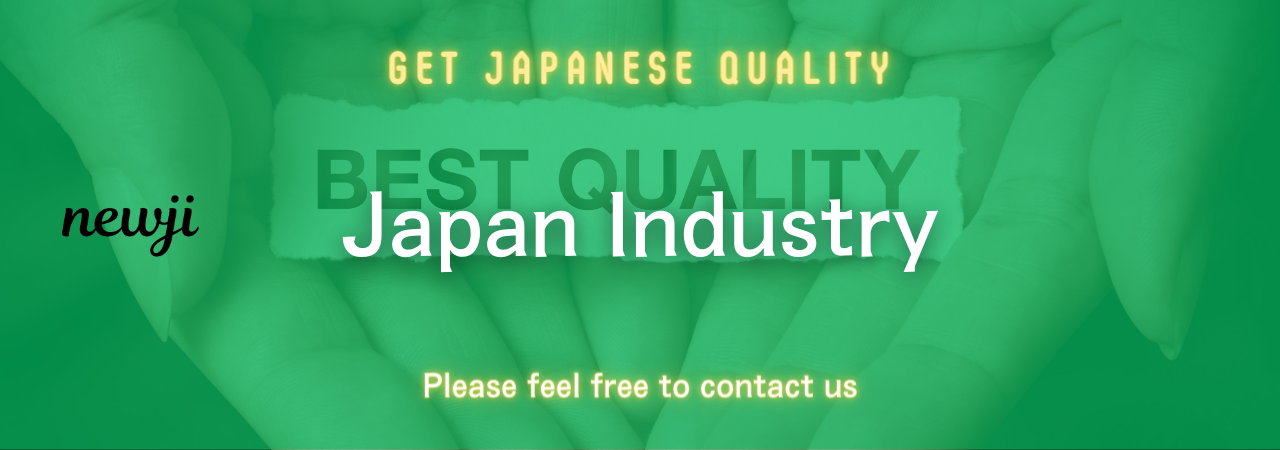
In the world of supply chain and logistics, understanding the finer details of processes such as material management and parts management can be crucial for efficiency and success.
These terms are often used interchangeably, but they encompass different facets of managing resources within an organization.
Let’s delve into the key differences and why each is essential for a smooth operational flow.
目次
What is Material Management?
Material management is a critical function within any manufacturing or production-focused organization.
It involves the planning, organizing, and controlling of all activities related to the materials required for production.
This process ensures that the right materials are available at the right time, in the right quantity, and at the right cost.
It typically includes activities such as purchasing, inventory control, warehousing, and distribution.
Functions of Material Management
Material management encompasses several important functions:
1. Procurement
Procurement is the process of acquiring all necessary materials.
This includes the selection of suppliers, negotiation of contracts, and ensuring timely delivery of materials.
2. Inventory Control
Efficient inventory control prevents excess stock while ensuring materials are available for production.
This balance helps reduce holding costs and avoids production delays.
3. Warehousing
Proper warehousing ensures materials are stored safely and can be accessed quickly when needed.
This function also includes managing the storage environment to prevent damage.
4. Distribution
This involves the effective transportation and distribution of materials to various departments within the organization.
It’s crucial for maintaining a steady flow of production.
What is Parts Management?
Parts management, on the other hand, is a subset of material management focusing specifically on the organization and handling of spare parts and components.
These parts are often used for equipment maintenance and repairs.
Effective parts management ensures that the necessary parts are available for scheduled maintenance and unexpected repairs, preventing downtime and extending the life of machinery and equipment.
Functions of Parts Management
Just like material management, parts management includes several critical activities:
1. Identification and Cataloging
Parts management starts with the proper identification and cataloging of all spare parts.
Each part is given a unique identifier, and relevant information such as specifications, supplier details, and usage history is recorded.
2. Storage
Proper storage of parts is vital to keep them in good condition and easily accessible.
This involves organizing the parts in a logical manner and ensuring appropriate environmental conditions to prevent deterioration.
3. Inventory Management
This function ensures that the right parts are available when needed.
It involves keeping track of stock levels, forecasting needs based on equipment usage, and reordering parts in a timely manner.
4. Distribution and Handling
Efficient distribution processes ensure that parts are delivered to the maintenance teams quickly, minimizing downtime.
Handling also includes tracking the usage and movement of parts to maintain accurate inventory records.
Key Differences Between Material Management and Parts Management
While material management and parts management share some similarities, there are fundamental differences worth noting:
1. Scope
Material management has a broader scope as it deals with all materials required for production.
In contrast, parts management focuses exclusively on spare parts and components used for maintenance and repair.
2. Purpose
The primary purpose of material management is to ensure the smooth production process by making sure that all necessary materials are available.
Parts management, however, aims to ensure the longevity and reliability of equipment through effective maintenance and repair.
3. Activities Involved
Material management involves activities like procurement, inventory control, warehousing, and distribution of various materials.
Parts management activities include identification, cataloging, storage, and inventory management of spare parts.
4. Inventory Requirements
Material management often deals with larger inventories and more significant quantities of materials.
Parts management typically deals with smaller quantities but requires precise tracking due to the critical nature of the parts.
The Importance of Integrating Both Functions
For an organization to function optimally, it is vital to integrate material management and parts management effectively.
This integration ensures a seamless flow of materials and parts, reducing downtime and enhancing productivity.
Reducing Costs
Efficient material and parts management helps in reducing inventory costs, minimizing waste, and preventing costly production stoppages due to lack of materials or spare parts.
Improving Reliability
By ensuring the timely availability of materials and spare parts, organizations can maintain a steady production process and reliable operation of equipment.
This leads to higher customer satisfaction and a stronger market reputation.
Enhancing Efficiency
Streamlining the functions of both material management and parts management contributes to overall operational efficiency.
This allows organizations to respond quickly to market demands and stay competitive.
Conclusion
Understanding the differences between material management and parts management is essential for any organization involved in production and maintenance.
While material management deals with the broader scope of ensuring all necessary materials are available for production, parts management focuses on maintaining and repairing equipment through systematic handling of spare parts.
Effectively managing both elements is crucial for reducing costs, improving reliability, and enhancing overall efficiency.
By integrating these functions, organizations can ensure smooth operations, meet customer demands effectively, and maintain a competitive edge in the market.
資料ダウンロード
QCD調達購買管理クラウド「newji」は、調達購買部門で必要なQCD管理全てを備えた、現場特化型兼クラウド型の今世紀最高の購買管理システムとなります。
ユーザー登録
調達購買業務の効率化だけでなく、システムを導入することで、コスト削減や製品・資材のステータス可視化のほか、属人化していた購買情報の共有化による内部不正防止や統制にも役立ちます。
NEWJI DX
製造業に特化したデジタルトランスフォーメーション(DX)の実現を目指す請負開発型のコンサルティングサービスです。AI、iPaaS、および先端の技術を駆使して、製造プロセスの効率化、業務効率化、チームワーク強化、コスト削減、品質向上を実現します。このサービスは、製造業の課題を深く理解し、それに対する最適なデジタルソリューションを提供することで、企業が持続的な成長とイノベーションを達成できるようサポートします。
オンライン講座
製造業、主に購買・調達部門にお勤めの方々に向けた情報を配信しております。
新任の方やベテランの方、管理職を対象とした幅広いコンテンツをご用意しております。
お問い合わせ
コストダウンが利益に直結する術だと理解していても、なかなか前に進めることができない状況。そんな時は、newjiのコストダウン自動化機能で大きく利益貢献しよう!
(Β版非公開)