- お役立ち記事
- The difference between Material Management and Parts Management
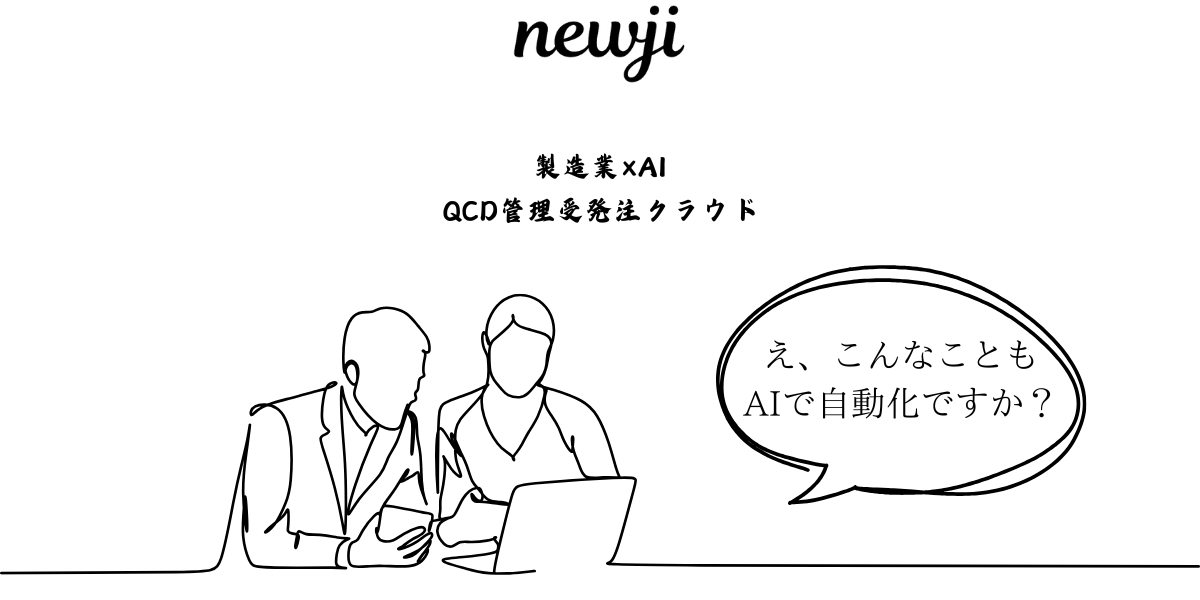
The difference between Material Management and Parts Management
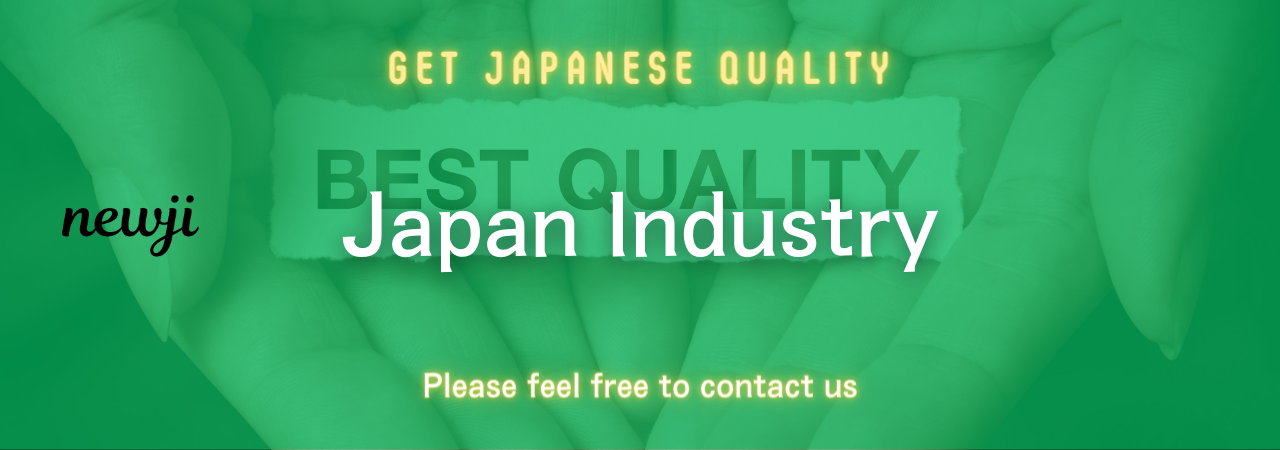
Material management and parts management are crucial aspects of any industry that relies on physical goods to produce products or services.
These two concepts might seem similar on the surface, but they have distinct differences and functions.
Understanding these differences can greatly improve an organization’s efficiency, inventory control, and overall profitability.
Let’s delve into the specifics of each to clarify their roles and responsibilities.
目次
What is Material Management?
Material management is a broad term that covers a wide range of activities involving the planning, sourcing, purchasing, transporting, storing, and controlling of materials.
The main goal is to ensure that the necessary materials are delivered to the right place, at the right time, and in the right quantities to meet production schedules and other operational needs.
Components of Material Management
Material Planning: This involves forecasting future material requirements based on production schedules and historical data.
Effective material planning helps prevent both shortages and overstock situations.
Purchasing: This includes selecting suppliers, negotiating contracts, and ensuring that high-quality materials are procured at competitive prices.
Storage and Inventory Control: Proper storage techniques are crucial to maintain the quality and usability of materials.
Inventory control methods, such as Just-In-Time (JIT) or ABC analysis, help in keeping track of the materials and ensuring optimal stock levels.
Transportation and Distribution: Ensuring that materials are transported efficiently from suppliers to warehouses and then to production units is essential for smooth operations.
Importance of Material Management
Cost Efficiency: Proper material management minimizes waste and reduces excess inventory costs.
It also helps in taking advantage of bulk purchasing discounts.
Quality Control: By sourcing high-quality materials and properly storing them, the overall quality of the final product is improved.
Improved Production: Timely availability of materials ensures that production schedules are met without delays.
What is Parts Management?
Parts management, on the other hand, is more specific and usually falls under the umbrella of material management.
It focuses on the handling, tracking, and controlling of individual parts or components required to assemble a final product.
This specialized branch of material management is especially critical in industries like automotive, aerospace, and electronics, where numerous parts and components are involved.
Components of Parts Management
Inventory Control: Similar to material management but more specialized, parts inventory control focuses on tracking numerous small components.
Methods such as barcode scanning and RFID tags are often used for accurate tracking.
Demand Forecasting: Predicting the need for specific parts based on historical data, production schedules, and market trends.
Procurement: This involves sourcing parts from suppliers, ensuring they meet the required specifications, and negotiating favorable terms.
Storage and Handling: Proper storage techniques are crucial to maintain the quality and usability of parts.
Specialized storage solutions, such as bin shelving or automated storage systems, are often used.
Importance of Parts Management
Minimized Downtime: Effective parts management ensures that all necessary components are available when needed, reducing production delays.
Cost Savings: By accurately forecasting demand and controlling inventory levels, companies can avoid the costs associated with overstocking or stockouts.
Improved Efficiency: Proper parts management ensures that production lines run smoothly and efficiently, thereby enhancing overall productivity.
Key Differences Between Material Management and Parts Management
Scope
Material management has a broader scope, dealing with a wide range of raw materials and supplies needed for production.
Parts management, however, is specifically focused on individual components or parts.
Complexity
While both require careful planning and control, parts management is often more complex due to the sheer number of individual items that need to be tracked and managed.
This complexity is particularly evident in industries like automotive or electronics, where a single product may require thousands of individual parts.
Techniques and Tools
Material management often uses tools and techniques like Material Requirements Planning (MRP), Enterprise Resource Planning (ERP) systems, and various inventory control methods.
On the other hand, parts management may employ more specialized tools like barcode scanning, RFID tagging, and automated storage and retrieval systems (ASRS).
Objectives
The primary objectives of material management are to ensure the timely availability of materials, maintain quality, and minimize costs.
Parts management focuses more on reducing downtime, maintaining inventory accuracy, and ensuring the seamless operation of production lines.
Industry Specificity
Material management is applicable to a wide range of industries, from manufacturing and construction to retail and healthcare.
Parts management is more specific to industries that rely heavily on numerous components, such as automotive, aerospace, and electronics.
Conclusion
Understanding the difference between material management and parts management is crucial for optimizing operations and improving efficiency.
While material management offers a broad view of handling all materials required for production, parts management focuses on the intricate details of managing individual components.
Both are essential for the smooth operation and success of any business.
Implementing effective strategies in these areas can lead to substantial cost savings, improved quality, and enhanced productivity.
By recognizing their differences and understanding their unique contributions, companies can better manage their resources and achieve their operational goals.
資料ダウンロード
QCD調達購買管理クラウド「newji」は、調達購買部門で必要なQCD管理全てを備えた、現場特化型兼クラウド型の今世紀最高の購買管理システムとなります。
ユーザー登録
調達購買業務の効率化だけでなく、システムを導入することで、コスト削減や製品・資材のステータス可視化のほか、属人化していた購買情報の共有化による内部不正防止や統制にも役立ちます。
NEWJI DX
製造業に特化したデジタルトランスフォーメーション(DX)の実現を目指す請負開発型のコンサルティングサービスです。AI、iPaaS、および先端の技術を駆使して、製造プロセスの効率化、業務効率化、チームワーク強化、コスト削減、品質向上を実現します。このサービスは、製造業の課題を深く理解し、それに対する最適なデジタルソリューションを提供することで、企業が持続的な成長とイノベーションを達成できるようサポートします。
オンライン講座
製造業、主に購買・調達部門にお勤めの方々に向けた情報を配信しております。
新任の方やベテランの方、管理職を対象とした幅広いコンテンツをご用意しております。
お問い合わせ
コストダウンが利益に直結する術だと理解していても、なかなか前に進めることができない状況。そんな時は、newjiのコストダウン自動化機能で大きく利益貢献しよう!
(Β版非公開)