- お役立ち記事
- The difference between Multiaxis Milling and Single-spindle Milling
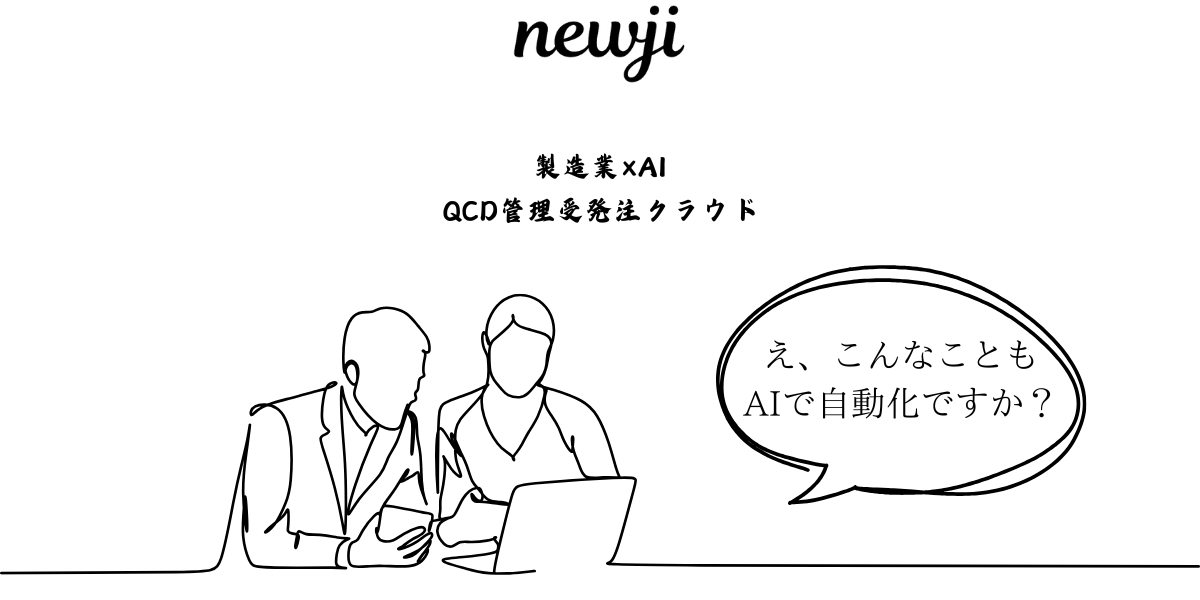
The difference between Multiaxis Milling and Single-spindle Milling
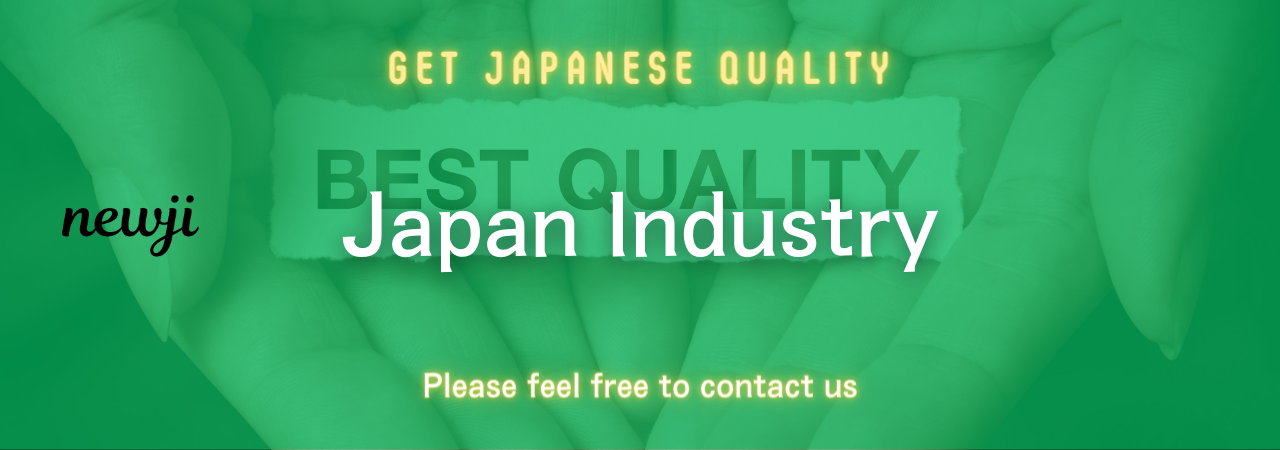
When it comes to the world of metalworking and machining, understanding the various milling techniques can make a significant difference in your project’s efficiency and output quality.
Two widely discussed methods are multiaxis milling and single-spindle milling.
Both have unique features, benefits, and applications.
Let’s delve into the differences between these two popular milling techniques.
目次
What is Multiaxis Milling?
Multiaxis milling refers to a machining process where the cutting tool can move in multiple directions.
Standard milling machines typically operate on three axes: X (horizontal), Y (vertical), and Z (depth).
However, multiaxis milling extends this capability, often adding a fourth (A-axis) or even a fifth (B-axis) to allow the cutting tool to approach the workpiece from different angles.
How Multiaxis Milling Works
Multiaxis milling machines employ advanced CNC (computer numerical control) technology to enable the cutting tool to rotate and tilt.
This facilitates more complex and precise shapes to be machined, which would be challenging, if not impossible, with traditional three-axis milling.
The extra axes provide increased dimensional flexibility, allowing for the creation of intricate parts with fewer operations.
Advantages of Multiaxis Milling
One of the most significant benefits of multiaxis milling is its ability to produce highly complex geometries.
This makes it ideal for industries such as aerospace, automotive, and medical devices, where precision is crucial.
Another advantage is the reduced need for multiple setups.
With the additional axes, operators can complete many facets of a workpiece without having to reposition it, thereby saving time and reducing the risk of human error.
The improved cutting angles and approaches also lead to better surface finishes and increased tool life.
Limitations of Multiaxis Milling
Despite its advantages, multiaxis milling is not without its limitations.
The machines are generally more expensive than single-spindle milling machines, making the initial investment higher.
They also require more skilled operators who can handle the complex programming and setup involved.
Maintenance costs can also be higher due to the intricate nature of the equipment.
What is Single-spindle Milling?
Single-spindle milling is a more traditional form of milling where a single cutter is used to shape the workpiece.
The spindle holds the cutting tool and rotates it at high speeds, removing material from the workpiece based on the programmed path.
Most single-spindle milling machines operate on three axes: X, Y, and Z.
How Single-spindle Milling Works
Single-spindle milling machines use a spindle that moves along the X, Y, and Z axes.
The workpiece is usually fixed in place, and the cutting tool does the moving.
The machine follows a programmed path to cut, shape, and drill the material.
This method is particularly useful for simpler shapes and parts, like gears, slots, and basic contours.
Advantages of Single-spindle Milling
The primary advantage of single-spindle milling is its simplicity and cost-effectiveness.
These machines are generally less expensive than their multiaxis counterparts and are easier to operate and maintain.
This makes them an excellent choice for small workshops or for tasks that don’t require high complexity.
The straightforward design also makes it easier to train operators, reducing the learning curve significantly.
Limitations of Single-spindle Milling
However, single-spindle milling comes with its own set of limitations.
The most significant constraint is the lack of complexity in the shapes and parts that can be produced.
For intricate designs that require multiple angles and dimensions, the workpiece would need to be re-positioned and re-machined multiple times.
This not only prolongs the machining process but also increases the risk of inaccuracies and errors.
Additionally, the surface finish may not be as refined as what can be achieved with multiaxis milling.
Key Differences Between Multiaxis and Single-spindle Milling
When comparing multiaxis and single-spindle milling, several key differences stand out.
Complexity and Precision
Multiaxis milling allows for the creation of intricate parts with a high level of precision.
On the other hand, single-spindle milling is better suited for simpler shapes and tasks.
Setup and Operation
Multiaxis milling requires fewer setups and can complete more operations in a single run.
Single-spindle milling, however, often necessitates multiple setups and adjustments, particularly for complex parts.
Cost
Single-spindle milling machines are generally more affordable, both in terms of the initial investment and ongoing maintenance.
Multiaxis machines are more expensive but offer greater capabilities and efficiencies, which can offset the higher costs in the long run.
Skill Level
Operating a multiaxis milling machine typically requires more advanced skills and knowledge.
In contrast, single-spindle milling machines are easier to operate, making them more accessible for less experienced operators.
Choosing the Right Milling Technique
Selecting the appropriate milling technique largely depends on your specific needs and resources.
If your projects involve complex geometries and require high precision, investing in a multiaxis milling machine might be the best option.
However, if your work primarily involves simpler parts and you’re looking for a cost-effective solution, single-spindle milling could be more suitable.
Future Trends
As technology continues to evolve, we can expect both multiaxis and single-spindle milling techniques to improve.
Multiaxis milling may become more accessible and affordable, while single-spindle machines could see enhancements in their capabilities and efficiencies.
Staying informed about these advancements can help you make better decisions for your manufacturing needs.
Understanding the differences between multiaxis milling and single-spindle milling can significantly impact your manufacturing process’s efficiency and output quality.
By knowing the strengths and limitations of each method, you can better choose the right approach for your specific project requirements.
This knowledge not only helps in optimizing production but also in ensuring the highest standards of precision and quality.
資料ダウンロード
QCD調達購買管理クラウド「newji」は、調達購買部門で必要なQCD管理全てを備えた、現場特化型兼クラウド型の今世紀最高の購買管理システムとなります。
ユーザー登録
調達購買業務の効率化だけでなく、システムを導入することで、コスト削減や製品・資材のステータス可視化のほか、属人化していた購買情報の共有化による内部不正防止や統制にも役立ちます。
NEWJI DX
製造業に特化したデジタルトランスフォーメーション(DX)の実現を目指す請負開発型のコンサルティングサービスです。AI、iPaaS、および先端の技術を駆使して、製造プロセスの効率化、業務効率化、チームワーク強化、コスト削減、品質向上を実現します。このサービスは、製造業の課題を深く理解し、それに対する最適なデジタルソリューションを提供することで、企業が持続的な成長とイノベーションを達成できるようサポートします。
オンライン講座
製造業、主に購買・調達部門にお勤めの方々に向けた情報を配信しております。
新任の方やベテランの方、管理職を対象とした幅広いコンテンツをご用意しております。
お問い合わせ
コストダウンが利益に直結する術だと理解していても、なかなか前に進めることができない状況。そんな時は、newjiのコストダウン自動化機能で大きく利益貢献しよう!
(Β版非公開)