- お役立ち記事
- The difference between Outer Diameter Grinding and Inner Diameter Grinding
月間76,176名の
製造業ご担当者様が閲覧しています*
*2025年3月31日現在のGoogle Analyticsのデータより
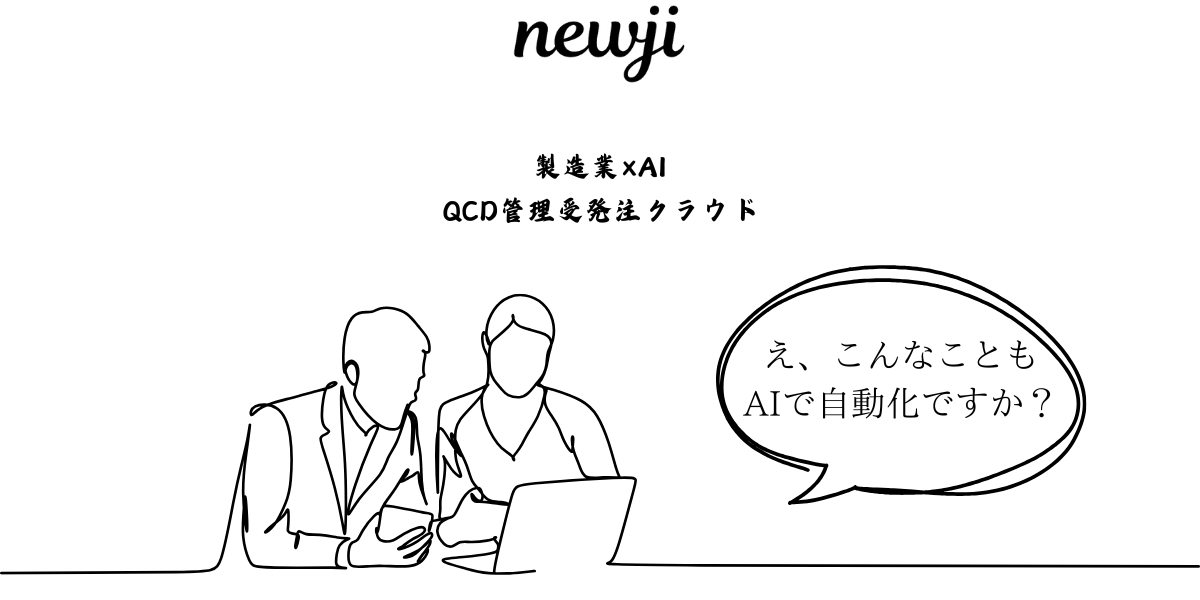
The difference between Outer Diameter Grinding and Inner Diameter Grinding
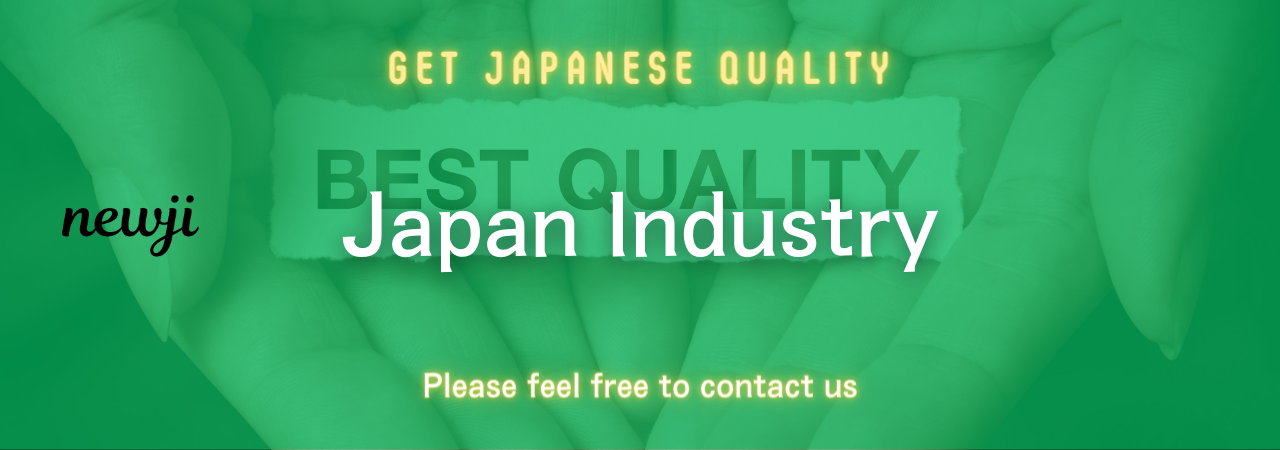
Grinding is a machining process that has been employed for centuries. It’s used to refine surfaces and is a crucial step in manufacturing and assembly. There are two main types of cylindrical grinding processes: outer diameter (OD) grinding and inner diameter (ID) grinding. Both are essential for different applications and yield specific results based on the needs of the machinery or components in question. Below, we will explore the differences between OD and ID grinding to help you understand their unique functionalities and applications.
目次
Understanding Outer Diameter Grinding
Outer diameter (OD) grinding is a method of grinding that is used to refine the outer surface of a cylindrical object. This process involves a rotating workpiece and a grinding wheel.
How OD Grinding Works
In OD grinding, the workpiece is usually held between centers or in a chuck. A grinding wheel rotates against the outer surface, removing material and refining the outer diameter. The grinder typically moves along the workpiece length, ensuring uniformity and precision across the entire external surface.
Applications of OD Grinding
OD grinding is commonly used in the automotive and aerospace industries, where high precision is required for components like shafts, pipes, and tubes. It’s particularly useful for applications requiring tight finishes and small tolerances.
Understanding Inner Diameter Grinding
Inner diameter (ID) grinding, on the other hand, focuses on refining the internal surface of a cylindrical object. This method also involves a rotating workpiece but targets the inner diameter.
How ID Grinding Works
In ID grinding, the workpiece is usually secured on a magnetic chuck or between two centers, much like OD grinding. However, a smaller grinding wheel is inserted into the inner cavity of the workpiece. The grinding wheel then rotates to remove material from the inner surface, shaping and refining the internal diameter.
Applications of ID Grinding
ID grinding is heavily utilized in the production of pipes, gears, and bearings. It is crucial for applications where the internal dimensions of a component must meet high standards of precision and finish. This makes it indispensable in industries like medical device manufacturing, automotive, and aerospace.
Key Differences Between OD and ID Grinding
Surface Target
The most obvious difference between OD grinding and ID grinding is the surface they target:
– OD grinding focuses on the outer surface.
– ID grinding targets the inner surface.
Grinding Wheel Size
In OD grinding, the grinding wheel is usually larger compared to ID grinding. ID grinding requires smaller wheels because they need to fit inside the internal cavity of the workpiece.
Machine Setup and Operation
While both processes require precise setup and operation:
– OD grinding machines often come with external features like different types of chucks or centers to hold the workpiece.
– ID grinding machines usually feature a smaller spindle to maneuver the grinding wheel into the inner surfaces.
Application Specifics
OD grinding is more commonly used to finish the external surfaces of cylindrical objects, making it ideal for shafts, tubes, and pins.
In contrast, ID grinding is used to finish internal surfaces like those found in bearings, gears, and pipes.
The Importance of Precision in Grinding
Whether it’s OD or ID grinding, the focus is on achieving high precision and an excellent surface finish.
Tolerances in these processes can be incredibly tight, sometimes down to a few micrometers. This precision is critical for ensuring that parts fit together perfectly in their applications, reducing wear and tear and increasing the lifespan of the components.
Common Challenges in OD and ID Grinding
Material Hardness
Different materials can pose challenges in both types of grinding. Harder materials cause more wear on the grinding wheels, requiring more frequent maintenance and replacement.
Temperature Management
Grinding generates significant heat due to the friction between the grinding wheel and the workpiece. Managing this heat is crucial to prevent damage or deformation. Coolants and lubricants are often used to maintain the temperature within safe limits.
Maintaining Consistency
Achieving uniformity across the entire surface, whether internal or external, can be challenging. This requires precise control over the grinding process, often involving advanced machinery and highly skilled operators.
Conclusion
Understanding the differences between outer diameter (OD) grinding and inner diameter (ID) grinding is essential for selecting the right method for a given application.
Both processes come with their unique set of tools, techniques, and challenges. They are indispensable in various industrial applications, offering the precision and finishes required for high-quality components. By knowing when and how to use each grinding process, manufacturers can produce parts that meet rigorous standards, ensuring high performance and longevity.
資料ダウンロード
QCD管理受発注クラウド「newji」は、受発注部門で必要なQCD管理全てを備えた、現場特化型兼クラウド型の今世紀最高の受発注管理システムとなります。
ユーザー登録
受発注業務の効率化だけでなく、システムを導入することで、コスト削減や製品・資材のステータス可視化のほか、属人化していた受発注情報の共有化による内部不正防止や統制にも役立ちます。
NEWJI DX
製造業に特化したデジタルトランスフォーメーション(DX)の実現を目指す請負開発型のコンサルティングサービスです。AI、iPaaS、および先端の技術を駆使して、製造プロセスの効率化、業務効率化、チームワーク強化、コスト削減、品質向上を実現します。このサービスは、製造業の課題を深く理解し、それに対する最適なデジタルソリューションを提供することで、企業が持続的な成長とイノベーションを達成できるようサポートします。
製造業ニュース解説
製造業、主に購買・調達部門にお勤めの方々に向けた情報を配信しております。
新任の方やベテランの方、管理職を対象とした幅広いコンテンツをご用意しております。
お問い合わせ
コストダウンが利益に直結する術だと理解していても、なかなか前に進めることができない状況。そんな時は、newjiのコストダウン自動化機能で大きく利益貢献しよう!
(β版非公開)