- お役立ち記事
- The difference between Overall Equipment Effectiveness (OEE) and Machine Operating Rate
The difference between Overall Equipment Effectiveness (OEE) and Machine Operating Rate
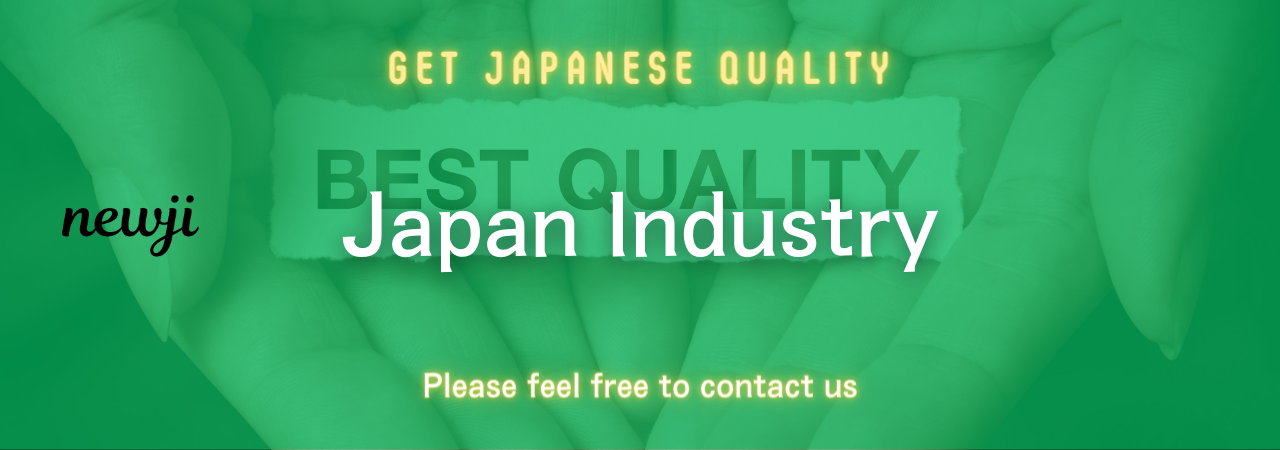
Overall Equipment Effectiveness (OEE) and Machine Operating Rate are two crucial metrics for optimizing manufacturing processes.
While they often get used interchangeably, they actually measure different aspects of equipment performance.
Understanding the difference between these two metrics can help manufacturers make more informed decisions, improve productivity, and reduce costs.
目次
Understanding Overall Equipment Effectiveness (OEE)
OEE is a comprehensive metric used to gauge the efficiency and effectiveness of manufacturing equipment.
It takes into account three key factors: Availability, Performance, and Quality.
Availability
Availability measures the proportion of time that the equipment is ready for production.
It considers both planned downtime (like scheduled maintenance) and unplanned downtime (like unexpected breakdowns).
Increasing availability means reducing both types of downtime, leading to a more streamlined operation.
Performance
Performance measures how well the equipment runs compared to its maximum potential speed.
It accounts for factors such as slow cycles and minor stops, aiming to highlight inefficiencies in the production process.
Improving performance involves optimizing machine speed and reducing minor interruptions.
Quality
Quality measures the proportion of good parts produced versus the total parts produced.
It focuses on reducing defects and improving the overall output quality.
High-quality metrics signify fewer defects and less rework, leading to better customer satisfaction and reduced costs.
Understanding Machine Operating Rate
Machine Operating Rate is a simpler metric that primarily focuses on the operating time of the equipment.
It measures the proportion of time the machine is running during the planned production time.
Operation Time
Operation time is the actual time the machine spends in production mode.
It excludes any time spent on maintenance, setting up, or other non-productive activities.
Calculation
The Machine Operating Rate is calculated by dividing the operation time by the planned production time and multiplying by 100 to get a percentage.
For example, if a machine was expected to run for 10 hours but was operational for only 8 hours, the Machine Operating Rate would be 80%.
Key Differences Between OEE and Machine Operating Rate
While both metrics are valuable, they serve different purposes and should be used in tandem for a more holistic understanding of equipment performance.
Comprehensiveness
OEE is a more comprehensive metric as it considers not just operation time but also performance efficiency and quality.
Machine Operating Rate, on the other hand, focuses solely on the operational aspect of the equipment.
Actionable Insights
OEE provides more actionable insights for improving various aspects of the production process.
It identifies specific areas that need attention, whether it’s minimizing downtime, boosting machine speed, or reducing defects.
Machine Operating Rate is less detailed but can quickly indicate whether equipment is being utilized effectively.
Implementation Complexity
OEE requires more data collection and analysis, making it somewhat complex to implement.
However, the benefits of using OEE can significantly outweigh the initial effort.
Machine Operating Rate is easier to calculate and doesn’t require intricate data collection, making it simpler to implement but less informative.
When to Use OEE and Machine Operating Rate
Both metrics are valuable but are best suited for different scenarios.
Using OEE
If you’re looking for a comprehensive evaluation of your production process, OEE is the go-to metric.
It’s ideal for long-term improvement projects and for identifying specific areas that need optimization.
Manufacturers aiming for a competitive edge often rely on OEE to help them achieve world-class manufacturing standards.
Using Machine Operating Rate
Machine Operating Rate is useful for quick assessments and for operations where simplicity and speed are essential.
It can be particularly useful in environments where quick decision-making is crucial, such as during shifts or in small-scale operations.
Conclusion
Understanding the difference between Overall Equipment Effectiveness and Machine Operating Rate can significantly impact your manufacturing efficiency.
While OEE offers a comprehensive, detailed analysis of various performance factors, the Machine Operating Rate provides a quick snapshot of operational efficiency.
Utilizing both metrics enables you to make informed, data-driven decisions that can lead to improved productivity, higher quality, and cost savings.
Each metric has its place in the manufacturing landscape, and knowing when and how to use them can be a game-changer for your operations.
So next time you’re looking to evaluate your equipment performance, remember that OEE and Machine Operating Rate offer complementary insights that can help you optimize your production process.
資料ダウンロード
QCD調達購買管理クラウド「newji」は、調達購買部門で必要なQCD管理全てを備えた、現場特化型兼クラウド型の今世紀最高の購買管理システムとなります。
ユーザー登録
調達購買業務の効率化だけでなく、システムを導入することで、コスト削減や製品・資材のステータス可視化のほか、属人化していた購買情報の共有化による内部不正防止や統制にも役立ちます。
NEWJI DX
製造業に特化したデジタルトランスフォーメーション(DX)の実現を目指す請負開発型のコンサルティングサービスです。AI、iPaaS、および先端の技術を駆使して、製造プロセスの効率化、業務効率化、チームワーク強化、コスト削減、品質向上を実現します。このサービスは、製造業の課題を深く理解し、それに対する最適なデジタルソリューションを提供することで、企業が持続的な成長とイノベーションを達成できるようサポートします。
オンライン講座
製造業、主に購買・調達部門にお勤めの方々に向けた情報を配信しております。
新任の方やベテランの方、管理職を対象とした幅広いコンテンツをご用意しております。
お問い合わせ
コストダウンが利益に直結する術だと理解していても、なかなか前に進めることができない状況。そんな時は、newjiのコストダウン自動化機能で大きく利益貢献しよう!
(Β版非公開)