- お役立ち記事
- The difference between Part Number Management and Lot Management
月間76,176名の
製造業ご担当者様が閲覧しています*
*2025年3月31日現在のGoogle Analyticsのデータより
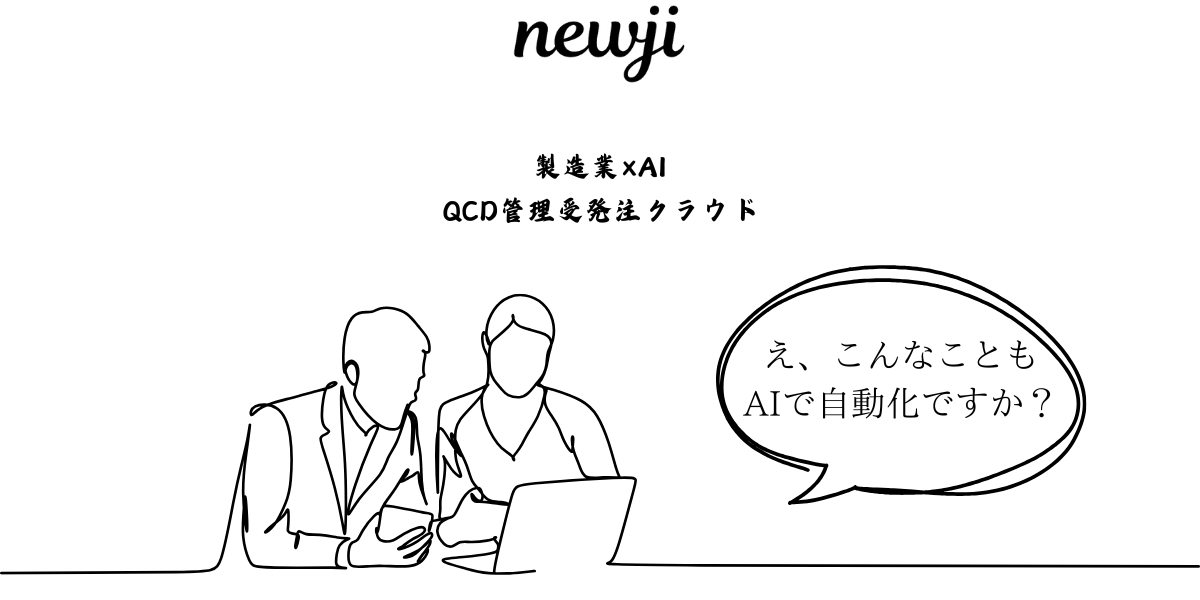
The difference between Part Number Management and Lot Management
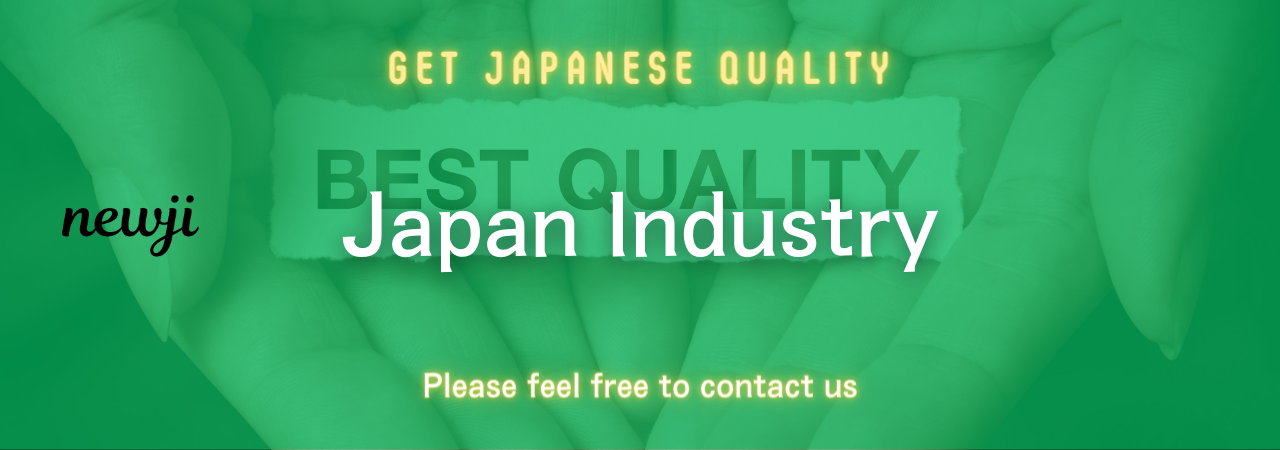
Managing inventory is a crucial part of any business involved in manufacturing, retail, or supply chain management.
Two key concepts in this domain are part number management and lot management.
Though they may sound similar, they serve different purposes and are essential for different reasons.
Let’s break down the difference between part number management and lot management to understand them better.
目次
What is Part Number Management?
Part number management refers to the process of assigning and managing unique identification codes, or part numbers, to each product or component in your inventory.
Each part number is unique and serves as an identifier for that specific item.
This system helps in tracking, organizing, and managing inventory effectively.
Why Part Numbers are Important
Part numbers are essential for several reasons.
Firstly, they simplify the identification process.
Instead of remembering long descriptions, employees can refer to a short, unique code.
Secondly, part numbers help in maintaining consistency.
Different departments within an organization can refer to the same part number, ensuring that everyone is on the same page.
Lastly, they facilitate better inventory management.
By tracking the part numbers, businesses can monitor stock levels, reorder points, and usage rates.
Components of a Part Number
A part number can be a simple numeric or alphanumeric code, or it can be more complex with several segments indicating various attributes of the part.
For instance, a part number may include information about the manufacturer, item type, size, and other specific characteristics.
Example:
Part Number: ABC123XYZ
– ABC: Manufacturer Code
– 123: Item Type
– XYZ: Specific Attributes
What is Lot Management?
Lot management, on the other hand, deals with tracking batches or lots of products rather than individual items.
A lot is a batch of products manufactured or purchased at the same time and is identified by a unique lot number.
Lot management ensures that each batch can be tracked from production to sale or use, and beyond.
Importance of Lot Management
Lot management is vital for several reasons.
Firstly, it helps in maintaining product quality.
By tracking lots, businesses can monitor the quality of each batch and identify any issues.
Secondly, it aids in compliance.
Many industries have regulatory requirements that mandate lot tracking for traceability and accountability.
Lastly, lot management is crucial for recall processes.
If a defect is found in a particular batch, the lot number helps in efficiently recalling only the affected products instead of the entire inventory.
Components of a Lot Number
Similar to part numbers, lot numbers are unique identifiers for each batch.
They can be simple or detailed, depending on the requirements of the business.
A lot number typically includes information about the production date, location, and other relevant details.
Example:
Lot Number: 2023-05-AB1001
– 2023: Year of Production
– 05: Month of Production
– AB1001: Batch Code
Key Differences Between Part Number Management and Lot Management
While both part number management and lot management involve unique identifiers, their purposes and applications are different.
Scope
Part number management focuses on individual items or components.
It provides a way to uniquely identify each product or part in the inventory.
Lot management, on the other hand, deals with batches of products.
It ensures that each batch can be traced throughout its lifecycle.
Usage
Part numbers are used primarily for inventory control, purchasing, and manufacturing processes.
They help in identifying, tracking, and managing individual items.
Lot numbers are used for quality control, compliance, and recall processes.
They ensure that each batch of products can be traced back to its origin, making it easier to monitor quality and address any issues.
Information
Part numbers usually contain information about the product’s attributes, such as manufacturer, type, size, and other specific characteristics.
Lot numbers include details about the batch, such as production date, location, and batch code.
Tracking
Part number management focuses on the individual tracking of items within the inventory.
It helps in monitoring stock levels, usage rates, and reorder points.
Lot management tracks batches of products.
It ensures that each batch can be traced from production to sale or use, and beyond, facilitating quality control and recall processes.
Integrated Approach
While part number management and lot management serve different purposes, they can be used together for a more comprehensive inventory management system.
By integrating both systems, businesses can achieve better control over their inventory, ensure product quality, and maintain compliance with regulatory requirements.
Benefits of Integration
An integrated approach to part number and lot management offers several benefits.
Firstly, it enhances traceability.
By combining both systems, businesses can track individual items and batches, ensuring complete traceability throughout the supply chain.
Secondly, it improves efficiency.
With a comprehensive inventory management system, businesses can streamline their processes, reduce errors, and save time.
Lastly, it supports better decision-making.
Having detailed information about both individual items and batches helps businesses make informed decisions about production, purchasing, and inventory management.
Implementation Tips
To effectively integrate part number and lot management, consider the following tips.
Firstly, use a consistent coding system.
Ensure that both part and lot numbers follow a standardized format that is easy to understand and use.
Secondly, leverage technology.
Implement inventory management software that supports both part number and lot management.
Lastly, train your team.
Ensure that all employees understand the importance of both systems and how to use them effectively.
In conclusion, part number management and lot management are essential components of effective inventory management.
While they serve different purposes, integrating both systems can provide businesses with comprehensive control over their inventory.
By understanding the differences between part number and lot management, businesses can implement these systems effectively and achieve better inventory control, quality assurance, and compliance.
資料ダウンロード
QCD管理受発注クラウド「newji」は、受発注部門で必要なQCD管理全てを備えた、現場特化型兼クラウド型の今世紀最高の受発注管理システムとなります。
ユーザー登録
受発注業務の効率化だけでなく、システムを導入することで、コスト削減や製品・資材のステータス可視化のほか、属人化していた受発注情報の共有化による内部不正防止や統制にも役立ちます。
NEWJI DX
製造業に特化したデジタルトランスフォーメーション(DX)の実現を目指す請負開発型のコンサルティングサービスです。AI、iPaaS、および先端の技術を駆使して、製造プロセスの効率化、業務効率化、チームワーク強化、コスト削減、品質向上を実現します。このサービスは、製造業の課題を深く理解し、それに対する最適なデジタルソリューションを提供することで、企業が持続的な成長とイノベーションを達成できるようサポートします。
製造業ニュース解説
製造業、主に購買・調達部門にお勤めの方々に向けた情報を配信しております。
新任の方やベテランの方、管理職を対象とした幅広いコンテンツをご用意しております。
お問い合わせ
コストダウンが利益に直結する術だと理解していても、なかなか前に進めることができない状況。そんな時は、newjiのコストダウン自動化機能で大きく利益貢献しよう!
(β版非公開)