- お役立ち記事
- The difference between Parts Inspection and Final Product Inspection
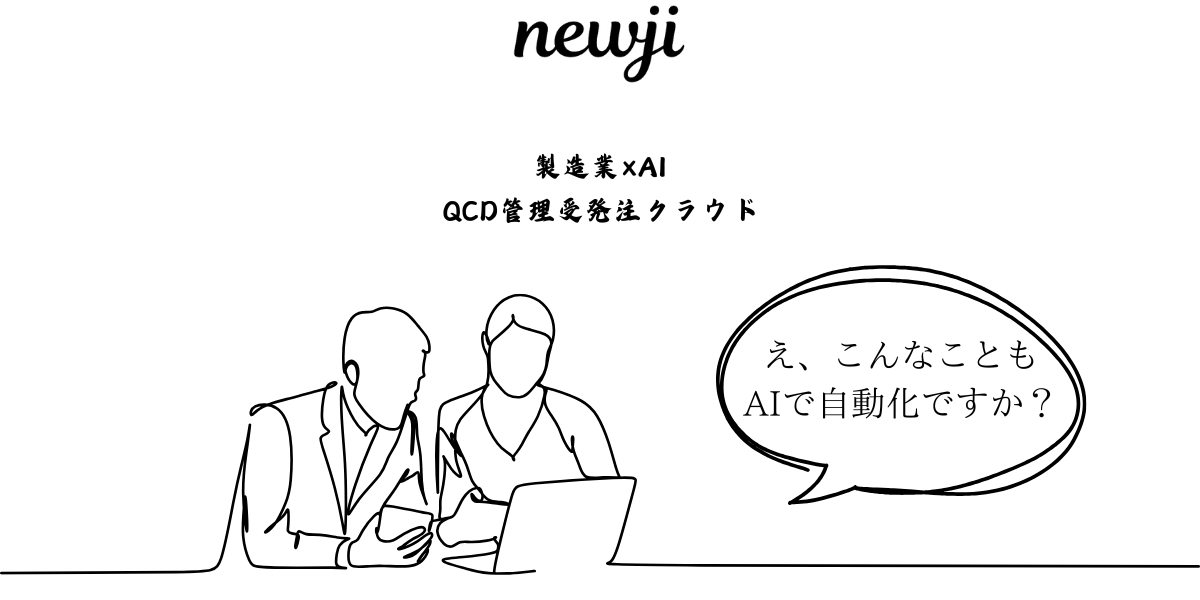
The difference between Parts Inspection and Final Product Inspection
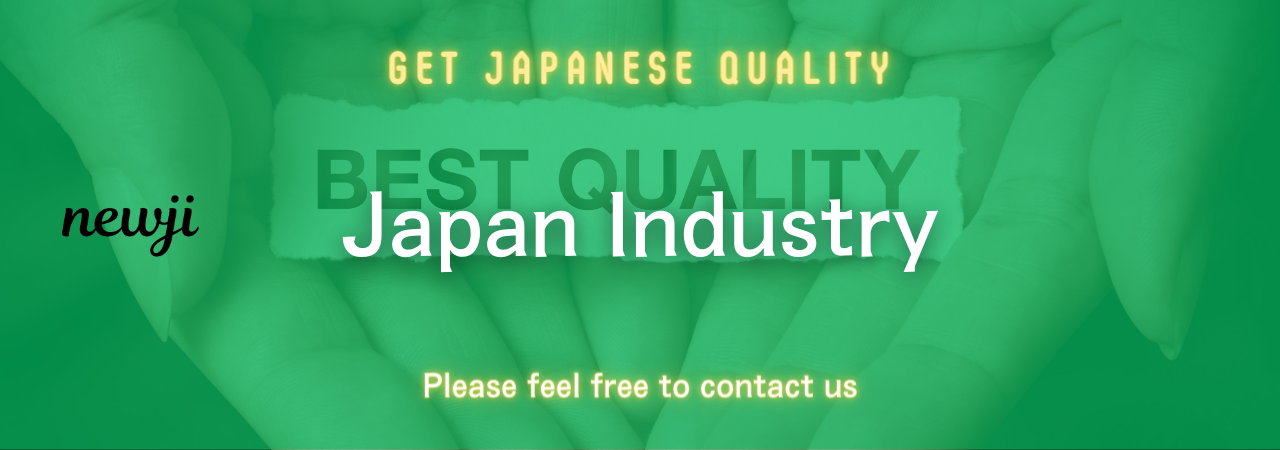
Understanding the difference between parts inspection and final product inspection is vital in achieving top-notch product quality.
While they may seem similar, each has a distinct role in the manufacturing and quality control processes.
This article will explore the nuances of both inspection methods and explain why they are essential for producing reliable, high-quality products.
目次
What is Parts Inspection?
Parts inspection, also known as component inspection, focuses on examining individual parts before they are assembled into a final product.
It is an essential step in ensuring that each component meets specific quality standards and specifications.
Parts inspection helps in catching defects early in the production process, preventing issues that could arise in the final product.
Why is Parts Inspection Important?
Parts inspection is crucial for several reasons.
Firstly, it helps in maintaining consistency and reliability in the manufacturing process.
Identifying and eliminating defective parts early reduces waste and saves costs.
Secondly, parts inspection ensures that all components fit together correctly during the assembly stage.
This is particularly important in complex products where even a slight deviation can lead to significant issues.
Lastly, parts inspection improves customer satisfaction.
By ensuring that only high-quality components are used, manufacturers can offer more reliable and durable products.
In turn, this builds trust and strengthens the brand’s reputation.
Types of Parts Inspection
There are several types of parts inspection methods, each suited for various aspects of quality control.
Dimensional Inspection
Dimensional inspection involves measuring the physical dimensions of a part to ensure they align with design specifications.
Tools such as calipers, micrometers, and CMM (Coordinate Measuring Machines) are commonly used.
Visual Inspection
This type of inspection involves checking the part for visible defects, such as cracks, scratches, or surface finish issues.
It is usually performed manually or with the help of magnification devices.
Functional Testing
Functional testing verifies that the part performs its intended function correctly.
For example, an electronic component may be tested for electrical continuity and resistance.
What is Final Product Inspection?
Final product inspection occurs after the entire product has been assembled.
It ensures that the final product meets all quality standards and is ready for distribution or shipment to customers.
Final product inspection verifies that the product functions correctly, is free of defects, and meets the customer’s requirements.
Why is Final Product Inspection Important?
Final product inspection is essential for several reasons.
First and foremost, it serves as the last line of defense against defective products reaching customers.
It minimizes the risk of returns, complaints, and warranty claims, which can be costly and damaging to a brand’s reputation.
Secondly, final product inspection ensures compliance with industry standards and regulations.
This is particularly important in industries such as aerospace, automotive, and medical devices, where non-compliance can have severe consequences.
Additionally, final product inspection validates the effectiveness of the manufacturing process.
It allows manufacturers to identify and address any recurring issues, ensuring continuous improvement and higher quality standards.
Types of Final Product Inspection
Various methods are employed during the final product inspection to ensure comprehensive quality control.
Visual Inspection
Similar to parts inspection, visual inspection at the final product stage checks for any visible defects or issues.
It is conducted manually or with specialized equipment.
Functional Testing
Final product functional testing ensures that the product operates as intended.
This may involve running the product through various scenarios to ensure it performs reliably.
Performance Testing
Performance testing evaluates the product’s overall performance, often under extreme conditions.
For instance, an electronic device might be subjected to temperature variations and stress tests to ensure it maintains its functionality.
Key Differences Between Parts Inspection and Final Product Inspection
While parts inspection and final product inspection share the common goal of ensuring product quality, several key differences set them apart.
Scope of Inspection
Parts inspection focuses solely on individual components, while final product inspection examines the assembled, finished product.
This difference in scope means that parts inspection is more detailed in nature, scrutinizing every aspect of each component.
Timing
Parts inspection occurs early in the production process, during or after the manufacturing of individual components.
In contrast, final product inspection takes place after the product has been fully assembled.
This timing difference allows for early detection of issues with parts inspection and final validation of the entire product with final product inspection.
Objectives
The primary objective of parts inspection is to ensure that each component meets its design specifications and quality standards.
Final product inspection aims to confirm that the overall product is functional, reliable, and compliant with all requirements.
Impact on Production
Defects caught during parts inspection typically lead to the rejection of specific components, avoiding costly rework or scrapping of the entire product.
In contrast, defects found during final product inspection may require comprehensive rework, as the entire product must be disassembled and repaired.
This makes parts inspection generally more cost-effective and efficient in terms of addressing quality issues.
Combining Both Inspections for Optimal Quality
While both parts inspection and final product inspection are crucial, combining both methods offers the best approach to quality control.
By inspecting components individually and validating the final product, manufacturers can create more reliable, high-quality products.
Benefits of Combining Both Inspections
One significant benefit of combining both inspections is the comprehensive quality control it provides.
Issues are identified early through parts inspection, reducing waste and production costs.
Moreover, final product inspection ensures that no defective product reaches the customer, maintaining brand trust and customer satisfaction.
Additionally, the dual approach allows for continuous improvement.
Data from both inspections can be analyzed to identify recurring issues, enabling manufacturers to refine their processes and enhance quality over time.
Best Practices for Effective Inspections
To maximize the benefits of both parts and final product inspections, manufacturers should follow several best practices.
Implement Standard Operating Procedures (SOPs)
Establish clear and detailed SOPs for both parts and final product inspections.
Ensure that these procedures are consistently followed and updated as needed.
Invest in Quality Equipment
Utilize high-precision tools and equipment for inspections to ensure accurate and reliable results.
Regularly calibrate and maintain inspection equipment to maintain their effectiveness.
Train Inspectors
Provide thorough training for inspectors to ensure they are skilled in both parts and final product inspections.
Regular training updates should be conducted to keep inspectors informed of the latest techniques and standards.
Continuous Improvement
Regularly review data from inspections to identify trends and areas for improvement.
Use this information to refine manufacturing processes and enhance overall product quality.
In summary, understanding the distinction between parts inspection and final product inspection is crucial for maintaining high-quality standards in manufacturing.
Both inspection methods play unique roles in the production process, and when combined, they offer a comprehensive approach to ensuring product reliability and customer satisfaction.
By implementing best practices and maintaining rigorous inspection protocols, manufacturers can continually enhance their product quality and remain competitive in the market.
資料ダウンロード
QCD調達購買管理クラウド「newji」は、調達購買部門で必要なQCD管理全てを備えた、現場特化型兼クラウド型の今世紀最高の購買管理システムとなります。
ユーザー登録
調達購買業務の効率化だけでなく、システムを導入することで、コスト削減や製品・資材のステータス可視化のほか、属人化していた購買情報の共有化による内部不正防止や統制にも役立ちます。
NEWJI DX
製造業に特化したデジタルトランスフォーメーション(DX)の実現を目指す請負開発型のコンサルティングサービスです。AI、iPaaS、および先端の技術を駆使して、製造プロセスの効率化、業務効率化、チームワーク強化、コスト削減、品質向上を実現します。このサービスは、製造業の課題を深く理解し、それに対する最適なデジタルソリューションを提供することで、企業が持続的な成長とイノベーションを達成できるようサポートします。
オンライン講座
製造業、主に購買・調達部門にお勤めの方々に向けた情報を配信しております。
新任の方やベテランの方、管理職を対象とした幅広いコンテンツをご用意しております。
お問い合わせ
コストダウンが利益に直結する術だと理解していても、なかなか前に進めることができない状況。そんな時は、newjiのコストダウン自動化機能で大きく利益貢献しよう!
(Β版非公開)