- お役立ち記事
- The difference between PDCA and OODA
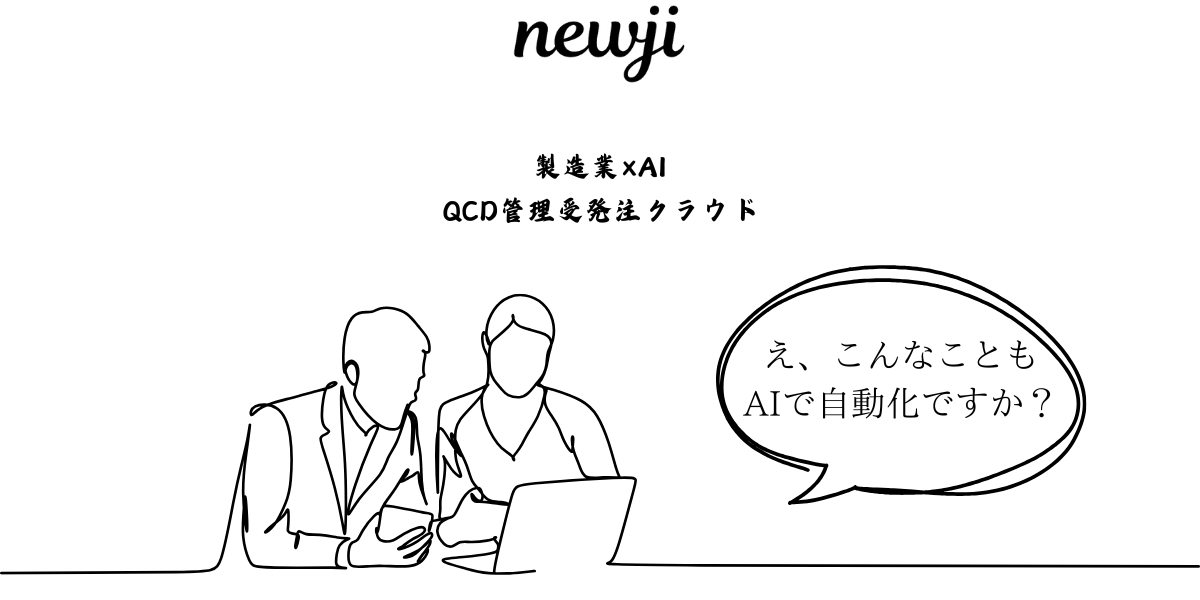
The difference between PDCA and OODA
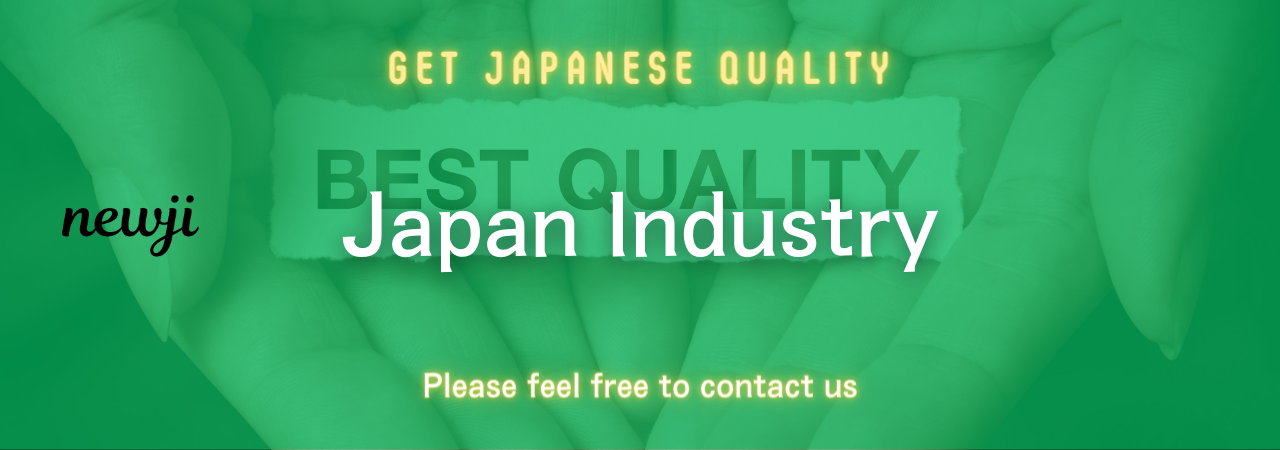
In the realm of business management and organizational development, there are various methodologies designed to enhance efficiency, productivity, and continual improvement.
Among these, PDCA and OODA are two widely recognized frameworks.
Both are cyclical models aimed at process optimization, but they differ in their applications, origins, and core principles.
Understanding the differences between PDCA and OODA can empower you to make informed decisions about which model best suits your organizational needs.
目次
What is PDCA?
PDCA stands for Plan-Do-Check-Act.
It is a four-step management method used for the control and continual improvement of processes and products.
Developed by Dr. W. Edwards Deming, PDCA is a cornerstone of quality management frameworks.
Plan
In the “Plan” phase, you identify an opportunity for improvement and establish objectives.
This involves gathering data, diagnosing issues, and designing potential solutions.
Planning is critical as it lays the groundwork for all subsequent actions.
Do
The “Do” phase involves implementing the plan on a small scale to test its effectiveness.
This is essentially a trial run aimed at observing the preliminary outcomes.
Check
During the “Check” phase, you evaluate the data collected from the “Do” phase.
This helps to assess whether the plan is achieving the desired results.
If the outcomes are not as expected, adjustments must be made.
Act
Finally, in the “Act” phase, you implement the plan on a larger scale if it has proven to be successful in the “Check” phase.
Alternatively, you can make further adjustments based on the insights gained.
What is OODA?
OODA stands for Observe-Orient-Decide-Act.
It is a cyclical decision-making model originally developed by military strategist John Boyd.
Unlike PDCA, OODA is primarily used in contexts that require rapid responses and decision-making.
Observe
In the “Observe” phase, you gather information from a wide array of sources.
This includes monitoring the environment, analyzing situations, and identifying any patterns or anomalies.
The goal is to have a comprehensive understanding of the current conditions.
Orient
The “Orient” phase involves synthesizing the information gathered during the “Observe” phase.
This includes drawing from cultural traditions, previous experiences, and new information to make sense of the observations.
Orientation is a critical step because it sets the stage for effective decision-making.
Decide
In the “Decide” phase, you select a course of action based on the synthesis of information.
This is where strategic options are weighed and a decision is made.
Act
The final phase is to implement the decided course of action.
Following this, you re-enter the Observation phase to see the effects of your actions and adapt as needed.
Comparing PDCA and OODA
Speed of Implementation
One of the primary differences between PDCA and OODA is the speed at which these processes are executed.
PDCA is generally a slower, more methodical process designed for long-term improvements.
It emphasizes thorough analysis and planning before taking action.
OODA, on the other hand, is designed for rapid decision-making and quick adaptations.
It is particularly useful in situations where speed is crucial and there is a need to respond to immediate changes.
Application Domains
PDCA is widely applied in quality management, manufacturing, and other areas where process optimization and continual improvement are crucial.
It is often used in environments where the primary focus is on reducing variability and enhancing quality.
OODA is more suited for high-stakes environments like military operations, emergency response, and any other fields that require swift decisions in the face of uncertainty.
Its flexibility and speed make it ideal for competitive and fast-changing settings.
Focus and Approach
PDCA focuses on a systematic approach to problem-solving.
It seeks to improve existing processes by identifying inefficiencies and planning strategic changes.
The emphasis is on continual improvement and long-term gains.
Conversely, OODA focuses on agility and adaptability.
It aims to outpace competitors by making quicker and more informed decisions.
While it also involves a cyclical process, the emphasis is on the dynamic interplay between different phases and the speed of execution.
Advantages and Disadvantages
PDCA Advantages
– Provides a structured framework for problem-solving and continuous improvement.
– Encourages thorough planning and data analysis.
– Suitable for long-term projects and quality management.
PDCA Disadvantages
– Can be slow and cumbersome.
– Less suited for rapidly changing environments.
– Requires detailed documentation and rigorous adherence to the process.
OODA Advantages
– Allows for fast, adaptive decision-making.
– Suitable for high-stakes and competitive environments.
– Focuses on real-time adjustments and agility.
OODA Disadvantages
– Can be less thorough in terms of analysis and preparation.
– May lead to hasty decisions in the absence of adequate information.
– Less structured, which could lead to inconsistencies in implementation.
Choosing the Right Model
When selecting between PDCA and OODA, it’s essential to consider the specific needs and characteristics of your organization.
If your primary goal is to implement long-term improvements and focus on quality, PDCA may be more suitable.
However, if you operate in a dynamic, competitive environment where quick decision-making is crucial, OODA could be the better option.
For optimal results, some organizations opt to integrate elements of both frameworks.
By doing so, they leverage the systematic, quality-focused approach of PDCA with the agile, adaptive nature of OODA.
This hybrid approach can offer a balanced pathway to achieving both continual improvement and rapid adaptability.
Each framework offers unique benefits and can be tailored to meet the specific demands of various environments.
By understanding their differences, you can strategically choose the model that aligns best with your organizational goals and operational needs.
資料ダウンロード
QCD調達購買管理クラウド「newji」は、調達購買部門で必要なQCD管理全てを備えた、現場特化型兼クラウド型の今世紀最高の購買管理システムとなります。
ユーザー登録
調達購買業務の効率化だけでなく、システムを導入することで、コスト削減や製品・資材のステータス可視化のほか、属人化していた購買情報の共有化による内部不正防止や統制にも役立ちます。
NEWJI DX
製造業に特化したデジタルトランスフォーメーション(DX)の実現を目指す請負開発型のコンサルティングサービスです。AI、iPaaS、および先端の技術を駆使して、製造プロセスの効率化、業務効率化、チームワーク強化、コスト削減、品質向上を実現します。このサービスは、製造業の課題を深く理解し、それに対する最適なデジタルソリューションを提供することで、企業が持続的な成長とイノベーションを達成できるようサポートします。
オンライン講座
製造業、主に購買・調達部門にお勤めの方々に向けた情報を配信しております。
新任の方やベテランの方、管理職を対象とした幅広いコンテンツをご用意しております。
お問い合わせ
コストダウンが利益に直結する術だと理解していても、なかなか前に進めることができない状況。そんな時は、newjiのコストダウン自動化機能で大きく利益貢献しよう!
(Β版非公開)