- お役立ち記事
- The difference between PDM (Product Data Management) and PLM (Product Lifecycle Management)
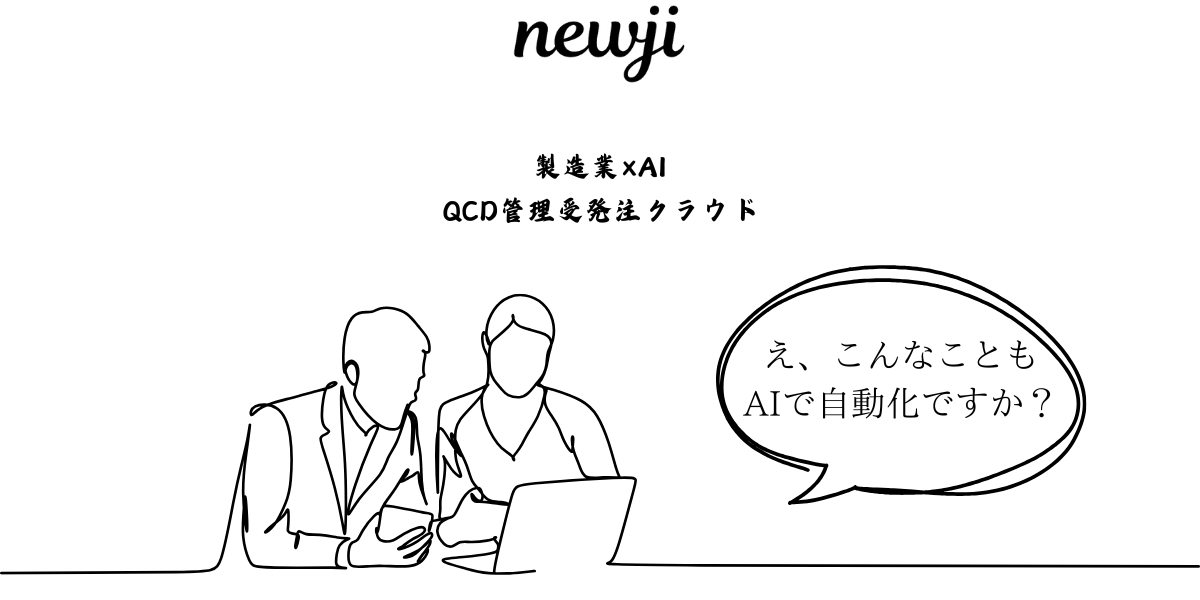
The difference between PDM (Product Data Management) and PLM (Product Lifecycle Management)
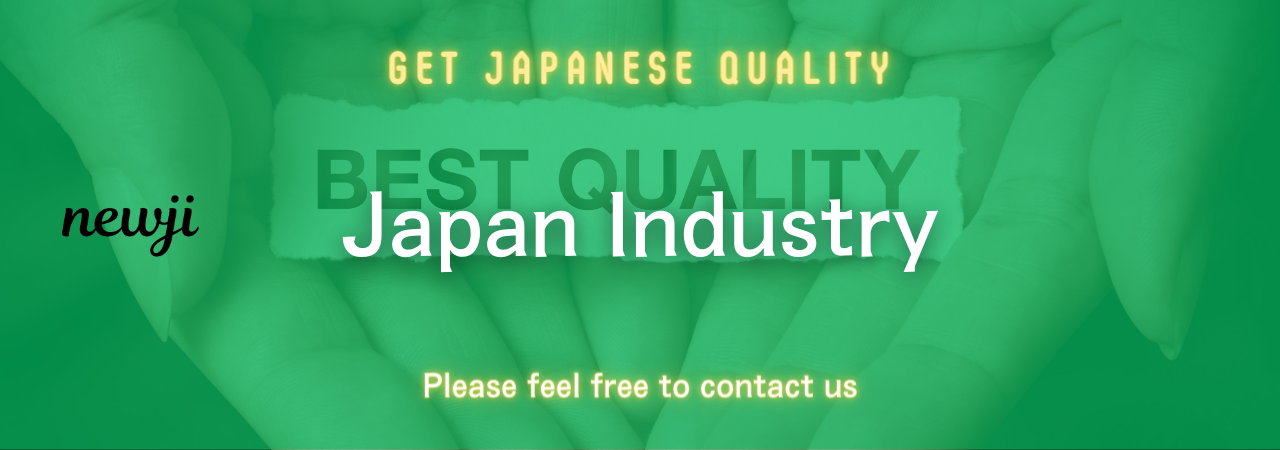
Understanding the differences between PDM and PLM can be quite insightful, especially if you work in product development or manufacturing. While both PDM (Product Data Management) and PLM (Product Lifecycle Management) are crucial systems in managing various aspects related to products, they serve different functions. In this article, we’ll delve into what PDM and PLM are, their key differences, as well as how they benefit an organization.
目次
What is PDM?
PDM stands for Product Data Management. It primarily focuses on managing and controlling the data related to a product. PDM systems are most commonly used during the design and engineering phases of a product lifecycle. They allow teams to store, manage, and share product-related information such as CAD files, bill of materials (BOM), and design specifications.
Key Features of PDM
– **Centralized Data Repository**: A PDM system provides a single source of truth by centralizing product data.
– **Version Control**: It manages the various versions of data files, ensuring that team members are working with the latest and most accurate information.
– **Access Control**: Defines who can access specific data, ensuring that sensitive information is protected.
– **Collaboration Tools**: Facilitates collaboration among team members, even if they are in different locations.
– **Data Security**: Implements security measures to protect the integrity and confidentiality of product data.
What is PLM?
PLM stands for Product Lifecycle Management. PLM is a more holistic approach that encompasses the entire lifecycle of a product, from conception through design, manufacturing, service, and disposal. PLM systems are designed to streamline processes, foster innovation, and enable collaboration across different departments within an organization.
Key Features of PLM
– **Lifecycle Management**: Manages all stages of a product from inception to disposal.
– **Unified Platform**: Integrates various tools and systems within one platform, providing a comprehensive overview.
– **Collaboration Across Departments**: Facilitates collaboration not just between designers and engineers but also marketing, sales, and supply chain management.
– **Project Management**: Offers tools for project management, including scheduling, resource allocation, and task tracking.
– **Compliance and Regulatory Management**: Ensures that products meet industry standards and regulations.
The Core Differences
Scope of Application
The primary difference between PDM and PLM lies in their scope. PDM focuses specifically on data management within product design and engineering. It’s designed to manage CAD files, design documents, and other technical specifications.
In contrast, PLM encompasses a broader array of functions, integrating all aspects of a product’s life, including initial idea, design, development, production, and even end-of-life procedures.
Data vs. Lifecycle Management
PDM is concerned strictly with managing the data and paperwork involved in creating a product. PLM, however, manages the entire lifecycle of a product, from conception through retirement.
Collaboration Scope
PDM systems are confined to collaboration within the engineering and design teams. On the other hand, PLM systems facilitate collaboration across various departments, including engineering, manufacturing, and even marketing and sales.
Tools and Features
While both systems offer some overlapping tools, PLM systems generally provide more comprehensive features, like project management, supply chain integration, and compliance management. PDM systems, however, are more streamlined and focused on data control and security.
Benefits of PDM
Enhanced Collaboration
By centralizing product data, PDM systems make it easier for team members to collaborate. Everyone can access the same files, reducing miscommunications and errors.
Improved Data Security
Access controls ensure that only authorized personnel can view or edit sensitive data. This minimizes the risk of data breaches and ensures data integrity.
Efficiency in Design Process
With version control and workflow management, PDM systems streamline the design process, reducing time-to-market and improving overall productivity.
Benefits of PLM
Integrated Workflow
By offering a unified platform, PLM systems break down departmental silos, enabling smoother workflows and better coordination.
End-to-End Visibility
PLM provides real-time insights into the entire product lifecycle, from design to end-of-life, helping organizations make data-driven decisions.
Regulatory Compliance
With built-in compliance management tools, PLM systems help companies adhere to industry standards and regulations, reducing the risk of non-compliance penalties.
When to Use PDM
If your primary need is to manage design and engineering data, a PDM system is most appropriate. It offers all the tools necessary for version control, data security, and efficient collaboration within a design team.
When to Use PLM
When you need a holistic approach to managing the entire lifecycle of a product, a PLM system is the way to go. PLM is particularly useful for organizations looking to streamline workflows, improve cross-departmental collaboration, and manage compliance and regulatory issues.
Conclusion
Both PDM and PLM systems play crucial roles in the product development and manufacturing processes. While PDM focuses on managing design-related data and facilitating collaboration within engineering teams, PLM offers a more comprehensive approach that encompasses the entire product lifecycle.
Understanding the key differences between PDM and PLM can help you choose the right system for your specific organizational needs. Whether you decide to implement a PDM system for managing detailed design data or a full-fledged PLM system to oversee the entire product lifecycle, both will undoubtedly provide significant benefits and streamline your processes.
In the end, the choice between PDM and PLM will depend on your organization’s specific needs, goals, and the complexity of the products you are developing.
資料ダウンロード
QCD調達購買管理クラウド「newji」は、調達購買部門で必要なQCD管理全てを備えた、現場特化型兼クラウド型の今世紀最高の購買管理システムとなります。
ユーザー登録
調達購買業務の効率化だけでなく、システムを導入することで、コスト削減や製品・資材のステータス可視化のほか、属人化していた購買情報の共有化による内部不正防止や統制にも役立ちます。
NEWJI DX
製造業に特化したデジタルトランスフォーメーション(DX)の実現を目指す請負開発型のコンサルティングサービスです。AI、iPaaS、および先端の技術を駆使して、製造プロセスの効率化、業務効率化、チームワーク強化、コスト削減、品質向上を実現します。このサービスは、製造業の課題を深く理解し、それに対する最適なデジタルソリューションを提供することで、企業が持続的な成長とイノベーションを達成できるようサポートします。
オンライン講座
製造業、主に購買・調達部門にお勤めの方々に向けた情報を配信しております。
新任の方やベテランの方、管理職を対象とした幅広いコンテンツをご用意しております。
お問い合わせ
コストダウンが利益に直結する術だと理解していても、なかなか前に進めることができない状況。そんな時は、newjiのコストダウン自動化機能で大きく利益貢献しよう!
(Β版非公開)