- お役立ち記事
- The difference between Plastic Deformation Processing and Material Removal Processing
The difference between Plastic Deformation Processing and Material Removal Processing
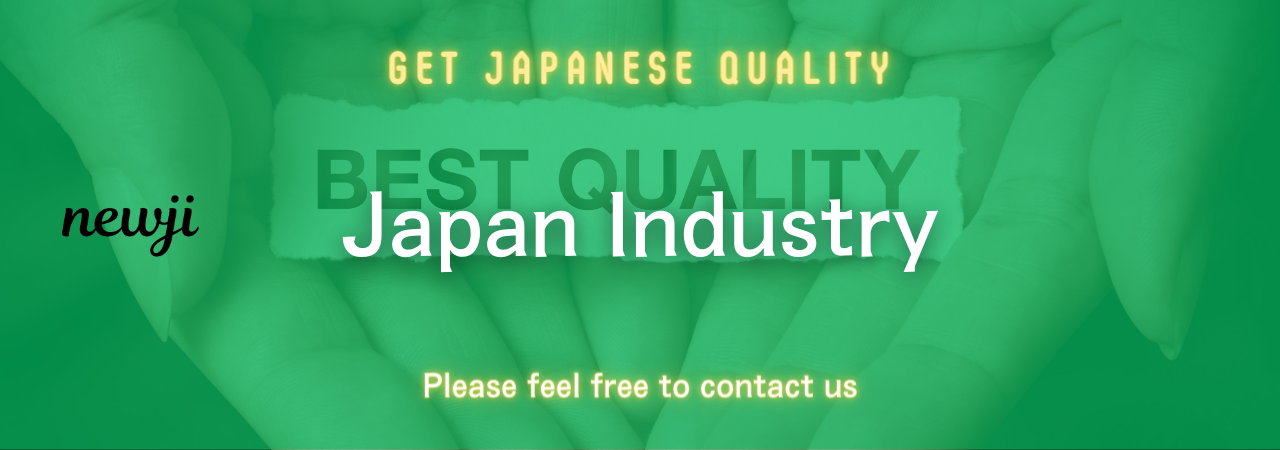
Plastic deformation processing and material removal processing are two fundamental approaches used in manufacturing to shape and modify materials.
Understanding the differences between these methods is crucial for appropriately selecting the right technique for specific applications.
Let’s delve into their distinct characteristics, advantages, and limitations.
目次
What is Plastic Deformation Processing?
Plastic deformation processing refers to a group of techniques where the material is reshaped by applying forces that exceed its yield strength.
This causes the material to deform plastically rather than elastically, permanently changing its shape without removing material.
Common methods include forging, extrusion, rolling, and stamping.
How It Works
In plastic deformation, forces are applied to the material until it yields and permanently deforms.
This deformation occurs at the atomic level, where atoms are displaced but remain bonded.
The material retains its mass and density, resulting in a changed shape without losses in the total mass.
Applications
Plastic deformation processes are widely used across various industries.
For example, forging shapes metal parts like gears and crankshafts, ensuring high strength and durability.
Rolling produces sheets and coils of metal, essential in construction and automotive industries.
Extrusion forms long, continuous shapes for pipes and profiles.
Advantages
One major advantage of plastic deformation processing is material efficiency.
Since no material is removed, waste is minimal.
Additionally, these processes often enhance the material’s mechanical properties, such as strength and toughness, due to work hardening.
The resulting parts typically have better surface finishes and higher structural integrity.
Limitations
However, plastic deformation is not without its challenges.
It usually requires significant energy to apply the necessary forces and may need specialized equipment like presses and hammers.
Another limitation is the potential for residual stresses within the material, which could affect performance if not properly managed.
Also, some materials might not be suitable for plastic deformation due to their brittleness.
What is Material Removal Processing?
Material removal processing involves techniques that shape materials by removing parts of them.
This category includes machining processes like milling, turning, drilling, and grinding.
The goal is to cut away excess material to achieve the desired geometry.
How It Works
In these processes, material is removed through mechanical means, usually with tools that cut, grind, or erode the material.
For example, in milling, a rotating cutter removes material from a workpiece to create various shapes.
In grinding, an abrasive wheel shapes or finishes the surface by wearing away the material.
Applications
Material removal processes are critical in many sectors, including aerospace, automotive, and electronics.
For instance, precision machining is essential for creating intricate components with tight tolerances.
Drilling is indispensable in manufacturing bolted connections, while grinding provides fine surface finishes for tools and dies.
Advantages
One of the main advantages of material removal processing is the ability to produce complex and detailed shapes with high precision.
These processes are highly adaptable and can work with a wide range of materials, including metals, plastics, and composites.
Additionally, they often offer better control over the final dimensions and surface qualities of the product.
Limitations
Despite their versatility, material removal processes generate waste material in the form of chips or shavings, which may need to be recycled.
These methods can also be slower than plastic deformation techniques, potentially resulting in higher production costs.
Moreover, tool wear is a common issue, requiring regular maintenance or replacements to ensure consistent quality.
Comparing Plastic Deformation and Material Removal Processing
Understanding the differences between these two methods helps in selecting the appropriate manufacturing technique.
Efficiency and Waste
Plastic deformation excels in material efficiency, as there’s minimal waste generated.
In contrast, material removal processes produce significant waste, which must be managed or recycled.
Applications and Suitability
Plastic deformation is ideal for applications demanding high strength and durability, such as automotive and aerospace components.
Material removal processes are perfect for machining intricate details and achieving high precision, making them suitable for complex parts like engine components and electronic devices.
Energy and Equipment
Plastic deformation often requires heavy machinery and higher energy inputs to generate the necessary forces.
Material removal can be done with a range of equipment, from basic drill presses to advanced CNC machines.
However, they may involve significant downtime for tool maintenance.
Choosing the Right Process
The choice between plastic deformation processing and material removal processing depends on multiple factors, including material properties, desired product characteristics, production volume, and cost considerations.
Material Properties
Consider the material’s ductility and brittleness.
Plastic deformation is unsuitable for brittle materials, which are better suited to material removal methods.
Product Characteristics
If the end product requires enhanced strength and toughness, plastic deformation processes are favorable.
For parts needing high precision and intricate shapes, material removal processes are more appropriate.
Production Volume and Costs
High-volume production may benefit from plastic deformation due to its efficiency and lower waste generation.
However, the initial investment in heavy machinery can be high.
Material removal processes, although potentially slower, can be more economical for small-batch production with complex designs.
Choosing the right manufacturing process is pivotal in achieving the desired balance between efficiency, cost, and product quality.
資料ダウンロード
QCD調達購買管理クラウド「newji」は、調達購買部門で必要なQCD管理全てを備えた、現場特化型兼クラウド型の今世紀最高の購買管理システムとなります。
ユーザー登録
調達購買業務の効率化だけでなく、システムを導入することで、コスト削減や製品・資材のステータス可視化のほか、属人化していた購買情報の共有化による内部不正防止や統制にも役立ちます。
NEWJI DX
製造業に特化したデジタルトランスフォーメーション(DX)の実現を目指す請負開発型のコンサルティングサービスです。AI、iPaaS、および先端の技術を駆使して、製造プロセスの効率化、業務効率化、チームワーク強化、コスト削減、品質向上を実現します。このサービスは、製造業の課題を深く理解し、それに対する最適なデジタルソリューションを提供することで、企業が持続的な成長とイノベーションを達成できるようサポートします。
オンライン講座
製造業、主に購買・調達部門にお勤めの方々に向けた情報を配信しております。
新任の方やベテランの方、管理職を対象とした幅広いコンテンツをご用意しております。
お問い合わせ
コストダウンが利益に直結する術だと理解していても、なかなか前に進めることができない状況。そんな時は、newjiのコストダウン自動化機能で大きく利益貢献しよう!
(Β版非公開)