- お役立ち記事
- The difference between PLC and DCS
月間76,176名の
製造業ご担当者様が閲覧しています*
*2025年3月31日現在のGoogle Analyticsのデータより
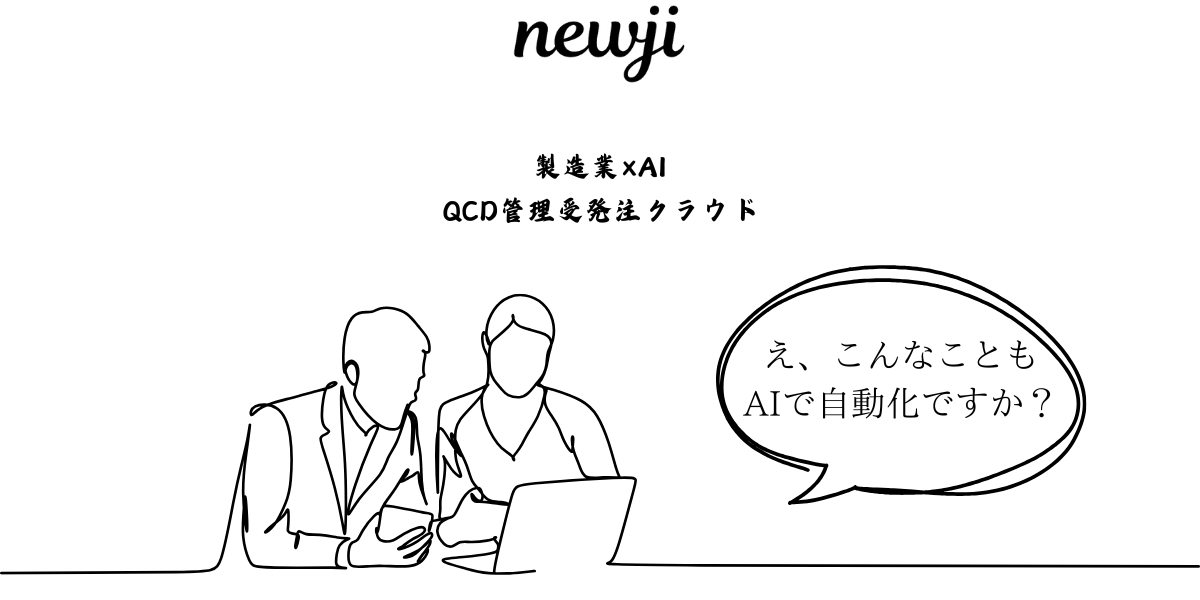
The difference between PLC and DCS
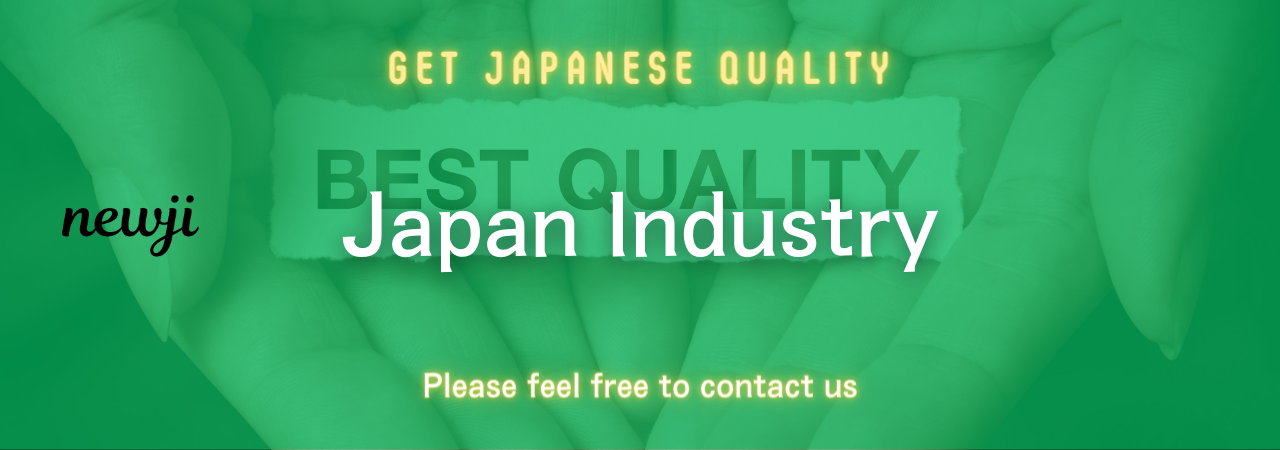
In today’s rapidly evolving industrial landscape, automation systems play a crucial role in ensuring efficient and accurate operations.
Two of the most common systems used in industrial automation are Programmable Logic Controllers (PLC) and Distributed Control Systems (DCS).
While both are integral to enhancing productivity and maintaining control over complex processes, there are significant differences between them.
Understanding these differences can help industries choose the right system for their specific needs and applications.
目次
What is a Programmable Logic Controller (PLC)?
A Programmable Logic Controller, or PLC, is a specialized computer used for the automation of industrial processes.
It is designed to withstand harsh conditions and is often used to control machinery on factory assembly lines, amusement rides, or lighting systems.
PLCs are programmed using a specialized language called ladder logic or other programming languages such as Structured Text or Function Block Diagram.
Key Features of PLC
PLCs are highly versatile and can be used for a wide range of applications.
Here are some of the key features:
– **Robustness**: PLCs are built to endure extreme temperatures, moisture, and dust, making them ideal for industrial environments.
– **Real-time operations**: They provide real-time responses to input changes, which is crucial for precise control and safety.
– **Expandability**: PLCs are modular, allowing for easy expansion by adding additional input/output (I/O) modules as needed.
– **Programming Flexibility**: They can be reprogrammed as required to adapt to new tasks or process changes.
Applications of PLC
PLCs are widely used in various industries due to their adaptability and robustness.
Common applications include:
– **Manufacturing and Assembly Lines**: PLCs control machinery and synchronize assembly processes to enhance productivity and reduce errors.
– **Amusement Parks**: They manage the operation of rides, ensuring safety and efficiency.
– **Building Automation**: PLCs are used in managing lighting systems, HVAC (Heating, Ventilation, and Air Conditioning) systems, and security systems.
– **Food and Beverage Industry**: They control processing and packaging machinery, ensuring consistency and quality.
What is a Distributed Control System (DCS)?
A Distributed Control System, or DCS, is an advanced automated control system that consists of multiple interconnected controllers distributed throughout a plant or process.
Unlike a centralized control system, DCS offers a hierarchical structure where controllers are placed close to the process operation and are connected via a high-speed communication network.
Key Features of DCS
DCS is designed for large-scale, complex processes that require precise control and monitoring.
Key features include:
– **Scalability**: DCS systems can handle thousands of I/O points and can be scaled up or down based on the complexity of the process.
– **Redundancy**: For critical applications, DCS offers redundancy in controllers and communication networks to ensure uninterrupted operation.
– **Integrated Control and Monitoring**: DCS provides seamless integration of control and monitoring functions, offering real-time data collection and analysis.
– **Centralized Management**: Despite having distributed controllers, DCS offers centralized management and visualization, making it easier for operators to manage processes.
Applications of DCS
DCS is particularly suited for large-scale and complex processes where centralized control and data analysis are critical.
Common applications include:
– **Oil and Gas**: DCS manages drilling, extraction, and refining processes, ensuring safety and efficiency.
– **Chemical Processing**: It controls complex chemical reactions and ensures consistent product quality.
– **Power Generation**: DCS manages power plant operations, from fuel handling to electricity generation.
– **Water Treatment**: It optimizes water purification and distribution processes, ensuring clean and safe water supply.
Key Differences Between PLC and DCS
While both PLC and DCS are used for automation, they serve different purposes and are suitable for different types of applications.
Here are the main differences:
System Architecture
PLCs typically have a centralized architecture where a single controller or a few controllers manage the entire process.
In contrast, DCS uses a distributed architecture with multiple controllers spread out across the plant, each managing a specific part of the process.
Scalability and Complexity
PLCs are suited for smaller, less complex tasks with fewer I/O points.
They can be scaled up by adding more modules, but they are generally not designed for large-scale applications.
DCS, on the other hand, is designed to handle complex processes with thousands of I/O points, making it highly scalable.
Redundancy and Reliability
DCS systems offer high levels of redundancy, ensuring that a failure in one part of the system does not lead to a complete shutdown.
This is critical for applications where reliability is paramount.
PLCs can also be designed for redundancy but typically to a lesser extent than DCS.
Cost and Implementation
PLCs are generally more cost-effective and easier to implement, making them ideal for smaller applications.
DCS systems are more expensive and complex to install and maintain, but they offer greater control and data management capabilities for large-scale applications.
Choosing the Right System for Your Needs
Selecting between PLC and DCS depends on the specific requirements of your application.
Here are some factors to consider:
Application Size and Complexity
For smaller applications or those with relatively simple processes, PLCs are usually the better choice due to their cost-effectiveness and ease of implementation.
For large-scale, complex processes that require tight integration and extensive data analysis, DCS is more suitable.
Redundancy and Reliability Requirements
If your process cannot afford downtime and requires high reliability, a DCS with built-in redundancy and robust communication networks is the better option.
For less critical applications, a PLC may suffice.
Budget Constraints
Cost is a significant factor in deciding between PLC and DCS.
PLCs are generally cheaper upfront and in terms of maintenance.
DCS systems, while more expensive, offer long-term benefits in terms of control and data management capabilities.
Conclusion
Both PLC and DCS play vital roles in industrial automation, each with its strengths and ideal applications.
Understanding the key differences between them can help you make an informed decision, ensuring that you choose the right system for your specific needs and goals.
Whether you opt for a PLC or a DCS, both will contribute significantly to enhancing the efficiency and productivity of your industrial operations.
資料ダウンロード
QCD管理受発注クラウド「newji」は、受発注部門で必要なQCD管理全てを備えた、現場特化型兼クラウド型の今世紀最高の受発注管理システムとなります。
ユーザー登録
受発注業務の効率化だけでなく、システムを導入することで、コスト削減や製品・資材のステータス可視化のほか、属人化していた受発注情報の共有化による内部不正防止や統制にも役立ちます。
NEWJI DX
製造業に特化したデジタルトランスフォーメーション(DX)の実現を目指す請負開発型のコンサルティングサービスです。AI、iPaaS、および先端の技術を駆使して、製造プロセスの効率化、業務効率化、チームワーク強化、コスト削減、品質向上を実現します。このサービスは、製造業の課題を深く理解し、それに対する最適なデジタルソリューションを提供することで、企業が持続的な成長とイノベーションを達成できるようサポートします。
製造業ニュース解説
製造業、主に購買・調達部門にお勤めの方々に向けた情報を配信しております。
新任の方やベテランの方、管理職を対象とした幅広いコンテンツをご用意しております。
お問い合わせ
コストダウンが利益に直結する術だと理解していても、なかなか前に進めることができない状況。そんな時は、newjiのコストダウン自動化機能で大きく利益貢献しよう!
(β版非公開)