- お役立ち記事
- The difference between Precision Turning and Rough Turning
月間76,176名の
製造業ご担当者様が閲覧しています*
*2025年3月31日現在のGoogle Analyticsのデータより
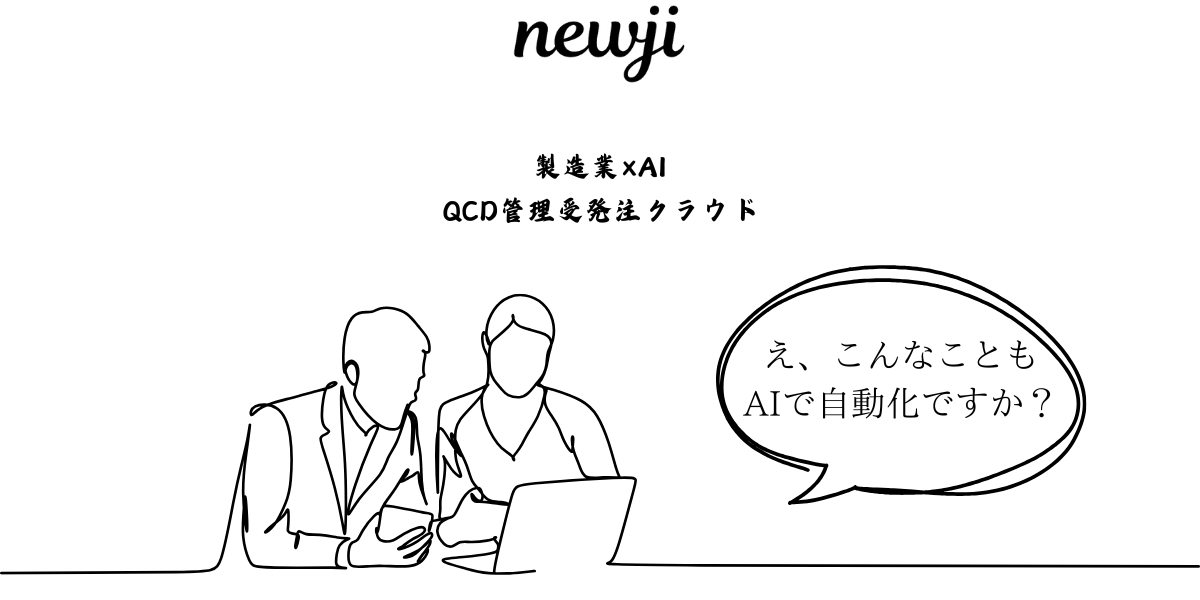
The difference between Precision Turning and Rough Turning
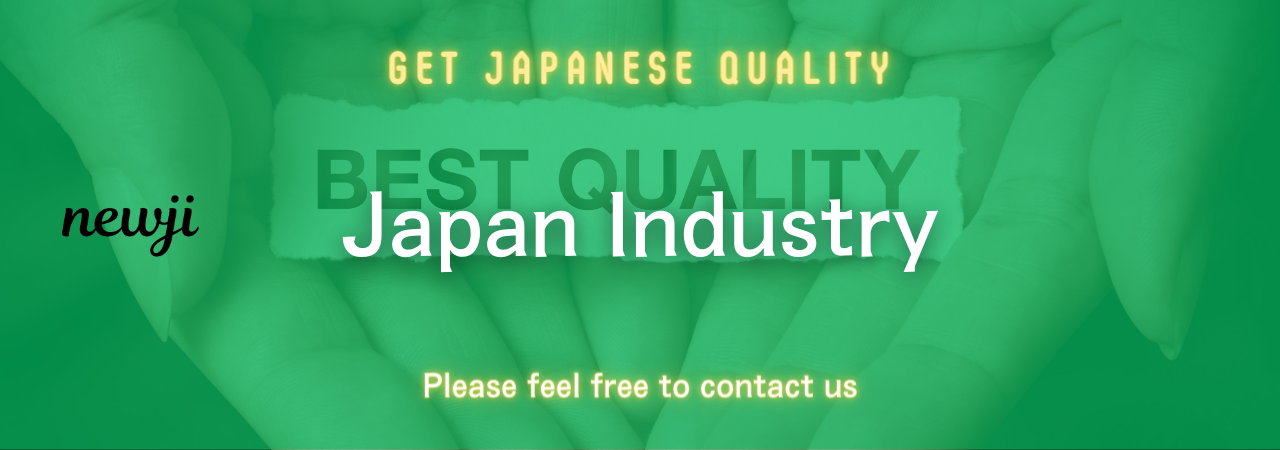
When it comes to the fascinating world of machining and manufacturing, there are many techniques professionals use to shape and refine metal parts.
Two commonly discussed methods are precision turning and rough turning.
While both of these techniques are integral to the machining process, they serve distinct purposes and produce different results.
Understanding the differences between precision turning and rough turning can help you make more informed decisions for your projects.
目次
What is Turning?
Before diving into the specifics of precision turning and rough turning, it’s essential to understand what turning means in the context of machining.
Turning is a machining process where a cutting tool removes material from the surface of a rotating workpiece.
The workpiece is usually clamped onto a lathe and spun at high speeds while the cutting tool shapes it into the desired form.
Understanding Rough Turning
Definition and Purpose
Rough turning is the initial step in the turning process where a large amount of material is removed from the workpiece.
The main aim of rough turning is to quickly reduce the diameter and shape the workpiece into a rough approximation of its final form.
This process is generally faster and uses higher feed rates and greater depths of cut.
The focus is not on achieving a smooth surface finish but on removing material as efficiently as possible.
Rough turning is usually the first stage before more refined machining methods are applied.
Tools and Techniques
In rough turning, carbide inserts are commonly used because of their durability and efficiency in material removal.
The tools used in rough turning are designed to withstand the high levels of stress and heat generated during the process.
A heavier machine setup with a robust chuck and secure clamping mechanisms is often required to handle the forces involved.
A cooling system is sometimes used to manage the heat produced, thereby extending the life of the tools.
Applications
Rough turning is most often used in industries where time efficiency and material removal rate are critical.
Common applications include the aerospace, automotive, and heavy machinery sectors.
Typical workpieces that undergo rough turning may include large shafts, rolls, and heavy-duty mechanical parts.
Understanding Precision Turning
Definition and Purpose
Precision turning is the process utilized after rough turning to fine-tune the workpiece and achieve a high degree of accuracy.
The objective is to achieve a precise dimension and smooth surface finish, often to meet stringent tolerances.
Precision turning operates at slower speeds and lower depths of cut compared to rough turning.
The focus here is not on material removal but on achieving the exact specifications required for the part.
Tools and Techniques
Precision turning employs high-precision cutting tools, often made from hard materials like carbide or ceramic.
These tools are designed to produce fine cuts and maintain a long tool life.
Advanced CNC lathes are often used for precision turning to ensure the highest level of accuracy.
Specialized techniques such as diamond turning may also be employed to achieve extremely smooth surfaces.
Applications
Precision turning finds its place in industries where exact specifications are crucial.
Notable examples include the medical device industry, watchmaking, and high-end electronics manufacturing.
It’s also used in the production of intricate components like gears, spindles, and micro-mechanical parts.
Key Differences Between Precision Turning and Rough Turning
Material Removal Rate
One of the most noticeable differences between precision turning and rough turning is the material removal rate.
Rough turning is focused on removing as much material as quickly as possible, using high feed rates and larger depths of cut.
Precision turning, on the other hand, is concerned with smaller, more accurate cuts to achieve the desired final dimensions.
Surface Finish
Rough turning generally leaves a rough surface finish due to the aggressive cutting.
In contrast, precision turning aims to produce a smooth, finely finished surface.
For many applications, a high-quality surface finish is crucial for the part’s functionality and aesthetics.
Speed and Feed Rates
Speed and feed rates differ significantly between the two processes.
Rough turning employs higher speeds and feed rates to expedite material removal.
In contrast, precision turning uses slower speeds and feed rates to ensure that the final product meets exact specifications.
Tool Wear and Durability
Tools used in rough turning experience more wear and tear due to the aggressive nature of the cuts.
These tools are generally robust and designed for durability.
Conversely, the tools for precision turning are often more delicate and designed for accuracy, sacrificing some durability in favor of precision.
Choosing the Right Process
The choice between precision turning and rough turning depends on various factors, including the project requirements, material type, and desired outcome.
Often, both processes are used sequentially to achieve the final product. Rough turning may be employed first to shape the material, followed by precision turning to refine it and meet the specified tolerances.
Considerations for Rough Turning
If your priority is to remove a large amount of material quickly, rough turning is the way to go.
It’s particularly useful for preparing a workpiece before it undergoes further machining processes like finishing, grinding, or precision turning.
Also, consider the material hardness and the machine capability to handle rough cuts efficiently.
Considerations for Precision Turning
Precision turning is necessary when your project demands high accuracy and a smooth surface finish.
This process is ideal for final machining steps where achieving exact dimensions is crucial.
Make sure you have advanced CNC machinery and high-precision cutting tools to carry out precision turning effectively.
Conclusion
Understanding the differences between precision turning and rough turning is crucial for anyone involved in machining and manufacturing.
While rough turning focuses on rapidly removing material to bring the workpiece close to its final shape, precision turning is dedicated to fine-tuning and achieving a high degree of accuracy and surface quality.
Both processes are indispensable in their own right and often work hand in hand to produce a finished product that meets all necessary specifications.
By knowing when and how to utilize each method, you can significantly enhance the efficiency and quality of your machining projects.
資料ダウンロード
QCD管理受発注クラウド「newji」は、受発注部門で必要なQCD管理全てを備えた、現場特化型兼クラウド型の今世紀最高の受発注管理システムとなります。
ユーザー登録
受発注業務の効率化だけでなく、システムを導入することで、コスト削減や製品・資材のステータス可視化のほか、属人化していた受発注情報の共有化による内部不正防止や統制にも役立ちます。
NEWJI DX
製造業に特化したデジタルトランスフォーメーション(DX)の実現を目指す請負開発型のコンサルティングサービスです。AI、iPaaS、および先端の技術を駆使して、製造プロセスの効率化、業務効率化、チームワーク強化、コスト削減、品質向上を実現します。このサービスは、製造業の課題を深く理解し、それに対する最適なデジタルソリューションを提供することで、企業が持続的な成長とイノベーションを達成できるようサポートします。
製造業ニュース解説
製造業、主に購買・調達部門にお勤めの方々に向けた情報を配信しております。
新任の方やベテランの方、管理職を対象とした幅広いコンテンツをご用意しております。
お問い合わせ
コストダウンが利益に直結する術だと理解していても、なかなか前に進めることができない状況。そんな時は、newjiのコストダウン自動化機能で大きく利益貢献しよう!
(β版非公開)