- お役立ち記事
- The difference between Preventive Maintenance and Condition-based Maintenance
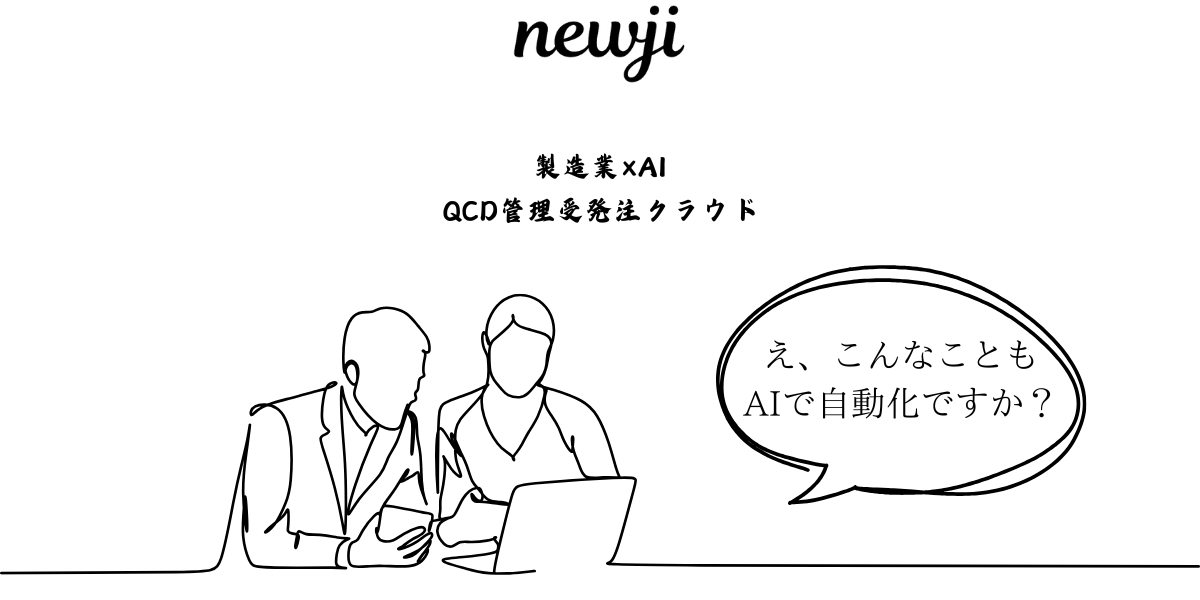
The difference between Preventive Maintenance and Condition-based Maintenance
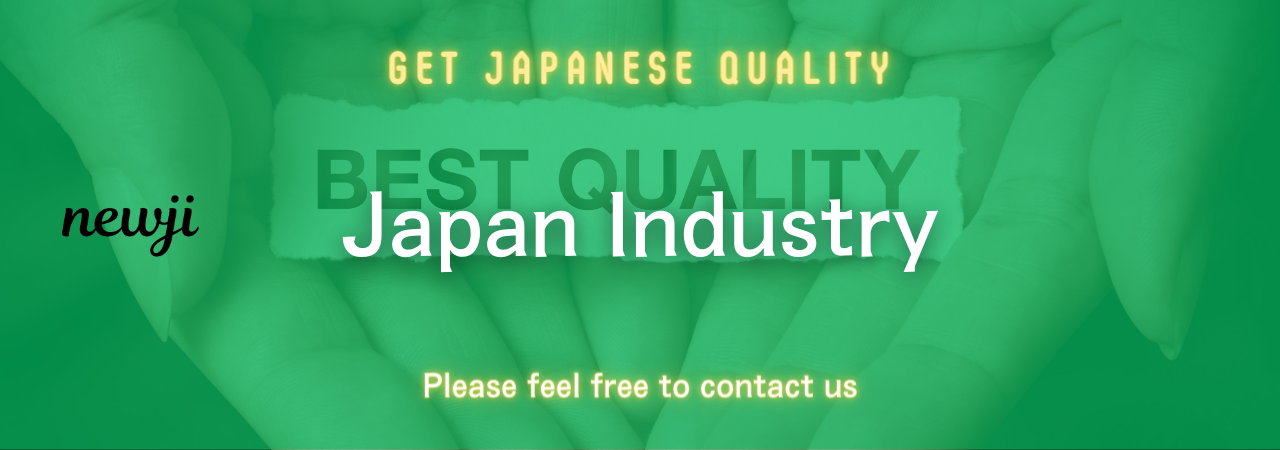
When it comes to maintaining machines and equipment, there are several strategies that industries can adopt to optimize their operations.
Two such strategies are Preventive Maintenance (PM) and Condition-based Maintenance (CBM).
Both maintenance approaches aim to enhance equipment reliability and performance but they differ significantly in their methodologies and execution.
目次
What is Preventive Maintenance?
Preventive Maintenance is a proactive approach.
This strategy involves scheduling regular inspections and servicing of equipment, regardless of its current condition.
The main goal is to prevent equipment failures before they happen.
By adhering to a set maintenance schedule, companies aim to minimize unexpected breakdowns and extend the lifespan of their machinery.
How Preventive Maintenance Works
In PM, maintenance activities are planned based on time intervals or usage measures.
For example, an air conditioning unit might undergo maintenance every six months.
This might include cleaning filters, checking coolant levels, and inspecting other critical components.
These periodic checks aim to catch potential issues before they escalate into significant problems.
Benefits of Preventive Maintenance
Implementing a Preventive Maintenance strategy comes with several advantages:
– **Reduced Downtime**: Regular maintenance can prevent sudden equipment failures that cause production stoppages.
– **Extended Equipment Lifespan**: Consistent care helps prolong the functional life of machinery by ensuring it operates efficiently.
– **Cost Savings**: Regular upkeep can be more cost-effective than dealing with major repairs or complete equipment replacement.
What is Condition-based Maintenance?
Condition-based Maintenance, on the other hand, takes a more reactive stance.
It involves monitoring the actual condition of equipment to decide whether maintenance is needed.
CBM relies heavily on technology to track various performance indicators such as vibration, temperature, and oil quality.
How Condition-based Maintenance Works
In a CBM approach, sensors and other diagnostic tools continuously monitor equipment health.
For instance, a vibration sensor on a motor might detect unusual oscillations, signaling a potential bearing issue.
When the data indicates that equipment performance is deviating from the norm, maintenance actions are triggered.
Benefits of Condition-based Maintenance
Adopting CBM offers its own set of advantages:
– **Optimized Maintenance Intervals**: Maintenance is performed only when needed, rather than on a fixed schedule.
– **Early Problem Detection**: Continuous monitoring can catch issues in their early stages, reducing the risk of catastrophic failures.
– **Efficient Resource Utilization**: Labor and parts are used more effectively since maintenance tasks are performed only when necessary.
Comparing Preventive and Condition-based Maintenance
While both maintenance strategies aim to optimize equipment reliability, they differ in several key aspects.
Proactivity vs. Reactivity
Preventive Maintenance is proactive, focusing on regular intervals regardless of equipment condition.
Condition-based Maintenance is reactive, relying on real-time data to guide maintenance decisions.
Technology Dependence
Preventive Maintenance typically requires less advanced technology, relying more on scheduled routines and manual inspections.
Condition-based Maintenance demands sophisticated monitoring systems and diagnostic tools.
Cost Implications
While PM may involve regular costs for inspections and minor fixes, it can save money by avoiding major breakdowns.
CBM can be cost-effective by minimizing unnecessary maintenance but requires an initial investment in monitoring technology.
Flexibility
Preventive Maintenance has a rigid schedule, making it easier to plan but less flexible.
Condition-based Maintenance offers more flexibility, as it adjusts to the actual state of the equipment.
Choosing the Right Strategy
Selecting the appropriate maintenance strategy depends on various factors, including the type of equipment, operational demands, and available resources.
Industry Requirements
Different industries have unique needs.
For example, manufacturing plants with continuous production lines might benefit more from Preventive Maintenance to maintain steady output.
Conversely, industries with critical, costly machinery might opt for Condition-based Maintenance to protect their investments.
Equipment Criticality
Highly critical equipment that can cause significant downtime if it fails is often better suited for Condition-based Maintenance.
Less critical equipment might be adequately served by a Preventive Maintenance schedule.
Resource Availability
Preventive Maintenance can be resource-intensive due to its regular scheduling.
Condition-based Maintenance might require fewer resources but necessitates advanced monitoring capabilities.
Combining Maintenance Strategies
In many cases, the optimal approach is not strictly one or the other.
Hybrid maintenance strategies that combine elements of both PM and CBM can offer a balanced solution.
Implementing a Hybrid Strategy
An organization might use Preventive Maintenance for less critical equipment while employing Condition-based Maintenance for key machinery.
This hybrid approach can optimize resource utilization and improve overall operational efficiency.
Real-world Example
Consider a transportation company with a fleet of vehicles.
Regular oil changes and brake inspections (PM) can keep the vehicles running smoothly.
Meanwhile, installing sensors to monitor engine health (CBM) can prevent more severe issues like engine failure.
Conclusion
Understanding the difference between Preventive Maintenance and Condition-based Maintenance is crucial for any organization looking to optimize its operations.
Both strategies offer unique benefits and limitations.
The choice between them should be guided by the specific needs, resources, and objectives of the organization.
In many cases, a hybrid approach can provide the best of both worlds, ensuring maximum efficiency, reliability, and cost-effectiveness.
資料ダウンロード
QCD調達購買管理クラウド「newji」は、調達購買部門で必要なQCD管理全てを備えた、現場特化型兼クラウド型の今世紀最高の購買管理システムとなります。
ユーザー登録
調達購買業務の効率化だけでなく、システムを導入することで、コスト削減や製品・資材のステータス可視化のほか、属人化していた購買情報の共有化による内部不正防止や統制にも役立ちます。
NEWJI DX
製造業に特化したデジタルトランスフォーメーション(DX)の実現を目指す請負開発型のコンサルティングサービスです。AI、iPaaS、および先端の技術を駆使して、製造プロセスの効率化、業務効率化、チームワーク強化、コスト削減、品質向上を実現します。このサービスは、製造業の課題を深く理解し、それに対する最適なデジタルソリューションを提供することで、企業が持続的な成長とイノベーションを達成できるようサポートします。
オンライン講座
製造業、主に購買・調達部門にお勤めの方々に向けた情報を配信しております。
新任の方やベテランの方、管理職を対象とした幅広いコンテンツをご用意しております。
お問い合わせ
コストダウンが利益に直結する術だと理解していても、なかなか前に進めることができない状況。そんな時は、newjiのコストダウン自動化機能で大きく利益貢献しよう!
(Β版非公開)