- お役立ち記事
- The difference between Preventive Maintenance and Corrective Maintenance
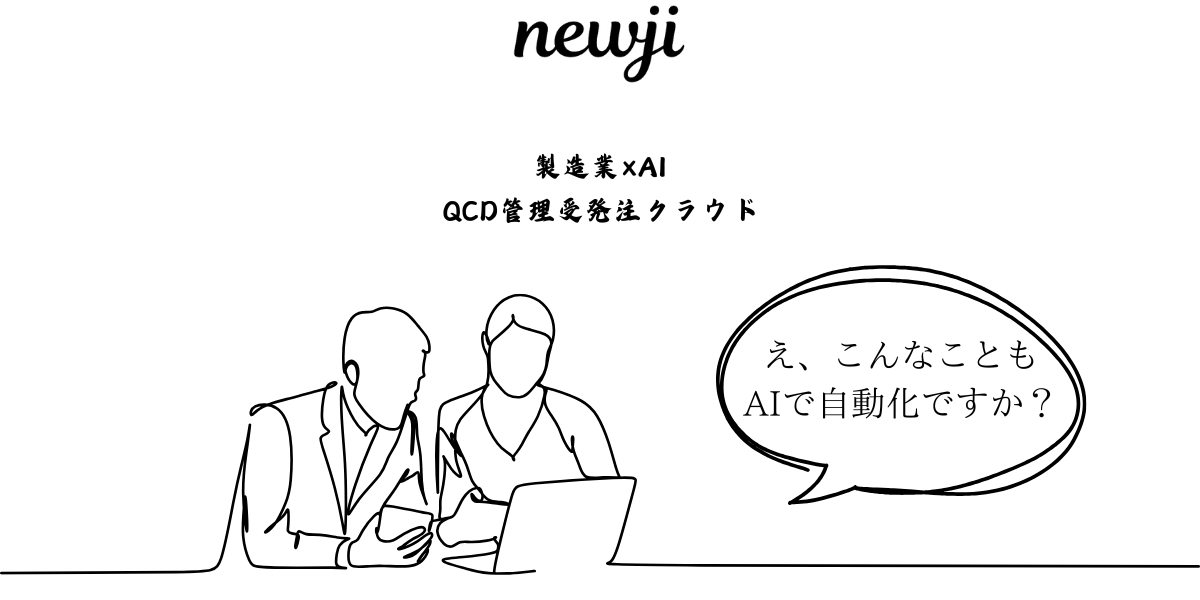
The difference between Preventive Maintenance and Corrective Maintenance
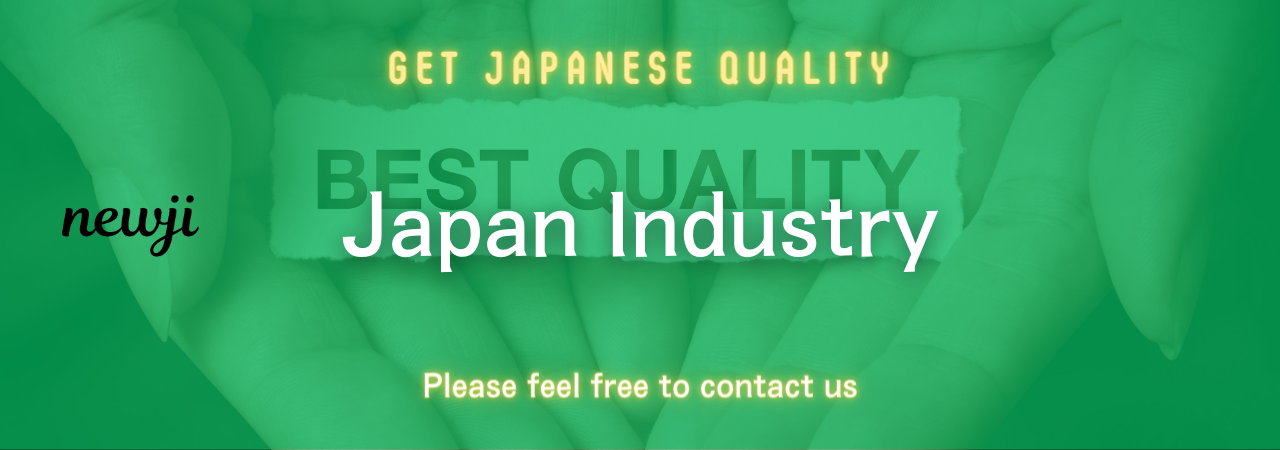
When it comes to maintaining machinery, equipment, or even facilities, two main types of maintenance practices come into play: preventive maintenance and corrective maintenance.
Understanding the differences between these two can play a crucial role in ensuring the longevity, efficiency, and safety of any operational system.
This article will delve into the distinct features of preventive and corrective maintenance, why each is crucial, and how they can benefit your operations.
目次
What is Preventive Maintenance?
Preventive maintenance, as the name implies, is maintenance performed regularly on equipment or systems to prevent unexpected failures.
The idea is to keep equipment in top-notch condition through routine checks, servicing, and minor repairs.
This type of maintenance is usually scheduled at regular intervals, regardless of whether the equipment shows any issues or not.
Types of Preventive Maintenance
There are several types of preventive maintenance, including:
Time-Based Maintenance: This involves servicing equipment at regular intervals, such as daily, weekly, or monthly.
Usage-Based Maintenance: This type is performed after a specific amount of usage, like an engine oil change after a certain number of miles.
Predictive Maintenance: Using advanced data analytics and sensors, predictive maintenance forecasts when an equipment failure might occur.
Condition-Based Maintenance: Maintenance based on equipment’s real-time performance metrics and operating conditions.
Benefits of Preventive Maintenance
Preventive maintenance offers numerous advantages:
Extended Equipment Lifespan: Regular maintenance helps to reduce wear and tear, extending the lifespan of equipment.
Reduced Operational Costs: By addressing minor issues before they become major problems, businesses can save on costly repairs.
Increased Safety: Regular inspections and maintenance can spot potential safety hazards before they cause accidents.
Higher Efficiency: Well-maintained equipment operates more efficiently, leading to better productivity.
What is Corrective Maintenance?
Corrective maintenance, on the other hand, is performed after a fault or issue has been identified.
This type of maintenance aims to restore the equipment to its original operating condition after a breakdown or failure has occurred.
Corrective maintenance can be immediate or deferred, depending on the severity of the problem and the criticality of the equipment.
Types of Corrective Maintenance
Corrective maintenance can be further divided into two types:
Immediate Corrective Maintenance: This occurs right after a fault is detected to prevent further damage or safety risks.
Deferred Corrective Maintenance: This is planned for a later time, usually when the equipment is not in critical use, to minimize disruption.
Benefits of Corrective Maintenance
While often misunderstood, corrective maintenance has its set of unique advantages:
Cost-Effectiveness: In some cases, it is more cost-effective to repair equipment only when issues arise rather than performing regular maintenance.
Resource Allocation: Allows maintenance teams to focus on critical repairs rather than routine, sometimes unnecessary checks.
Quick Turnaround: Immediate corrective measures can quickly bring downed equipment back to operational status.
Preventive vs. Corrective Maintenance: Key Differences
Proactive vs. Reactive
Preventive maintenance is proactive.
It aims to prevent equipment failures before they occur.
Corrective maintenance is reactive, dealing with issues after they arise.
Cost Implications
Initially, preventive maintenance may seem more expensive due to routine checks and minor repairs.
However, over the long term, it tends to be cost-effective by preventing major issues.
Corrective maintenance may save money upfront but can lead to higher costs in the long run due to unexpected failures and emergency repairs.
Operational Downtime
Preventive maintenance usually involves scheduled downtimes, which are generally less disruptive.
Corrective maintenance often results in unexpected downtimes, which can impact productivity and operational efficiency.
Safety and Reliability
Preventive maintenance tends to offer better safety and reliability.
Routine checks can spot potential issues before they become hazardous.
Corrective maintenance may involve dealing with equipment failures that could pose risks to safety and reliability.
Resource Management
Preventive maintenance requires a consistent allocation of resources for routine checks and minor repairs.
Corrective maintenance allows for more flexible allocation of resources but may demand immediate attention and resources during a breakdown.
When to Use Preventive and Corrective Maintenance
A balanced approach is often the best strategy.
For critical equipment that must be operational at all times, preventive maintenance is indispensable.
It minimizes the risk of unexpected failures and ensures the safety and reliability of the equipment.
For non-critical equipment, corrective maintenance might be more practical and cost-effective.
Industry-Specific Considerations
Different industries may have varying requirements for maintenance strategies.
For example, the healthcare industry, which deals with life-critical equipment, heavily relies on preventive maintenance.
In contrast, industries dealing with less critical machinery may opt for a combination of both maintenance types.
Technological Advancements
Advancements in predictive maintenance technologies and IoT (Internet of Things) have blurred the lines between preventive and corrective maintenance.
These technologies allow for a more dynamic approach, forecasting potential failures and making maintenance schedules more efficient.
Conclusion
Understanding the differences between preventive and corrective maintenance is crucial for making informed decisions about maintenance strategies.
While preventive maintenance offers long-term benefits in terms of safety, efficiency, and cost savings, corrective maintenance can be more practical for non-critical equipment.
A balanced approach, tailored to the specific needs of your operations, is often the best way to achieve optimal performance and reliability.
資料ダウンロード
QCD調達購買管理クラウド「newji」は、調達購買部門で必要なQCD管理全てを備えた、現場特化型兼クラウド型の今世紀最高の購買管理システムとなります。
ユーザー登録
調達購買業務の効率化だけでなく、システムを導入することで、コスト削減や製品・資材のステータス可視化のほか、属人化していた購買情報の共有化による内部不正防止や統制にも役立ちます。
NEWJI DX
製造業に特化したデジタルトランスフォーメーション(DX)の実現を目指す請負開発型のコンサルティングサービスです。AI、iPaaS、および先端の技術を駆使して、製造プロセスの効率化、業務効率化、チームワーク強化、コスト削減、品質向上を実現します。このサービスは、製造業の課題を深く理解し、それに対する最適なデジタルソリューションを提供することで、企業が持続的な成長とイノベーションを達成できるようサポートします。
オンライン講座
製造業、主に購買・調達部門にお勤めの方々に向けた情報を配信しております。
新任の方やベテランの方、管理職を対象とした幅広いコンテンツをご用意しております。
お問い合わせ
コストダウンが利益に直結する術だと理解していても、なかなか前に進めることができない状況。そんな時は、newjiのコストダウン自動化機能で大きく利益貢献しよう!
(Β版非公開)