- お役立ち記事
- The difference between Process Capability and Quality Capability
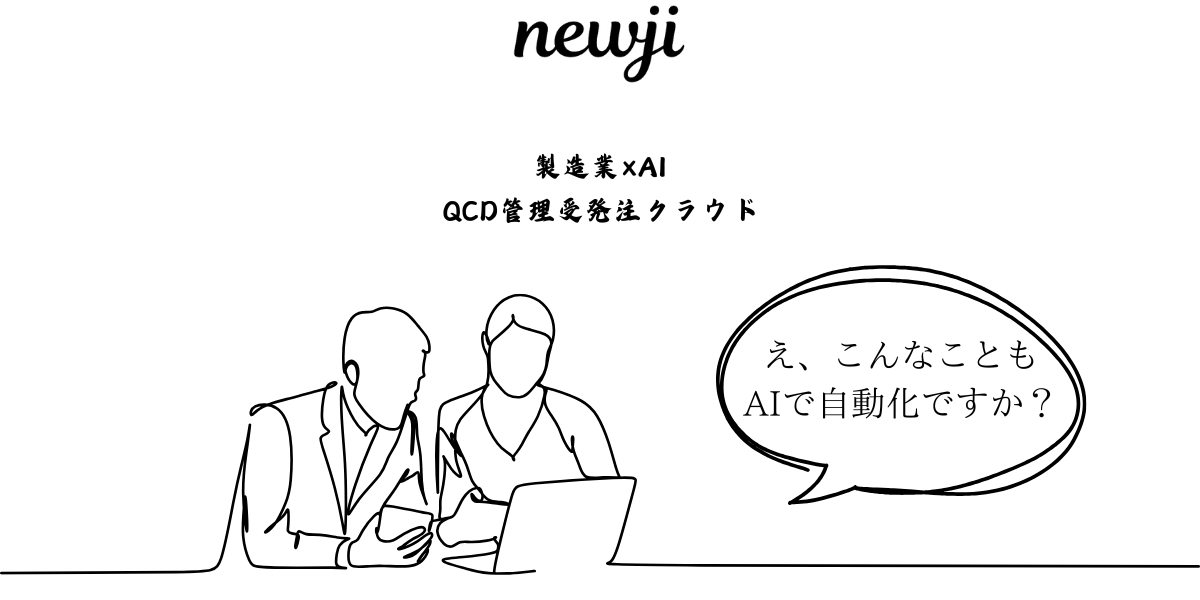
The difference between Process Capability and Quality Capability
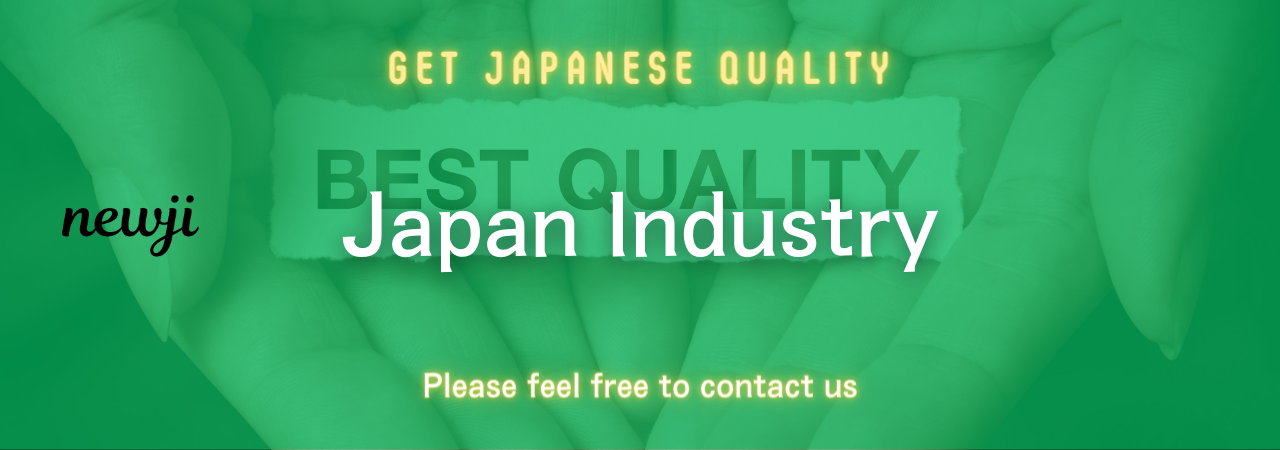
In the world of manufacturing and business, terms like “process capability” and “quality capability” get thrown around a lot.
They might sound similar, but they refer to different aspects of production and quality management.
Understanding the difference between these two terms is crucial for optimizing your operations and delivering top-notch products to your customers.
目次
What is Process Capability?
Process capability is a metric used to determine how well a process can produce items within specified limits.
It’s essentially an assessment of what your process can achieve under the best possible circumstances.
When we talk about process capability, we usually focus on two main indicators: Cp and Cpk.
Understanding Cp and Cpk
Cp, or Process Capability Index, measures how well your process can fit within the specified limits when everything is ideal.
Cp looks at the spread of your data, which means it considers how consistent your process is.
A higher Cp value indicates a more capable process.
Cpk, or Process Capability Index considering the mean, takes it a step further.
While Cp just looks at the spread, Cpk also considers how centered the process is within the specifications.
If a process is running well but is off-center, Cpk will reflect that by showing a lower value.
In simpler terms, Cpk is a more realistic measure of capability because it accounts for both spread and centering.
What is Quality Capability?
Quality capability, on the other hand, evaluates the overall ability of a company to produce quality products consistently.
It involves more than just the process.
Quality capability is a broader term that encompasses the entire production system, including raw materials, equipment, employee training, and more.
Quality Capability Indices
One of the key indicators of quality capability is Pp and Ppk.
These are similar to Cp and Cpk but are used for assessing the overall system performance over a period of time.
Pp, or Preliminary Process Capability, measures the total variability in your production system.
It gives a snapshot of how your system performs, taking into account all sources of variation.
Ppk, or Preliminary Process Capability Index considering the mean, evaluates the performance of the entire production system, similar to how Cpk evaluates a single process.
Ppk takes into account how well the system is centered as well as its overall spread.
Why the Difference Matters
Understanding the difference between process capability and quality capability can make a significant impact.
While a highly capable process (high Cp and Cpk) is an excellent start, it doesn’t guarantee overall product quality if other parts of the production system are lacking.
Suppose a process consistently produces items within the specified limits, but the raw materials are subpar.
In that case, the final product might still be of low quality.
Conversely, robust quality capability ensures that the entire production setup works harmoniously, leading to better and more consistent outcomes.
Improving Process Capability
To improve process capability, focus on reducing variability.
This can be achieved by adopting Six Sigma methodologies, which aim to minimize defects and improve process performance.
Regularly monitor your Cp and Cpk values to identify areas needing attention.
Provide comprehensive training to operators.
Ensuring they understand and adhere to the standard operating procedures can reduce human error, which is a significant source of process variability.
Enhancing Quality Capability
Step one in enhancing quality capability is a holistic approach.
Ensure all aspects of the production system, including raw materials, machinery, and human resources, are of high quality.
Invest in advanced quality control tools to continuously monitor the entire production system.
Regular audits and feedback loops can help in identifying bottlenecks and areas needing improvement.
Automation and Quality Capability
Automation can be a game-changer when it comes to improving quality capability.
Automated systems are consistent and reliable, reducing the likelihood of human error.
They can also monitor and adjust processes in real-time, ensuring the production system operates at its optimal capacity.
However, automation should be complemented with regular maintenance and updates to keep the system running smoothly.
The Role of Employee Training
Employees play a crucial role in both process and quality capability.
Regular training sessions help in keeping them updated with the latest practices and technologies.
A well-trained workforce can significantly reduce errors and improve both process and quality capability.
Encourage a culture of continuous improvement and root cause analysis to make your workforce more proactive in resolving issues.
Long-Term Benefits
Investing in both process and quality capability brings substantial long-term benefits.
It leads to fewer defects, lower production costs, and higher customer satisfaction.
Consistently delivering high-quality products can build brand reputation, giving you a competitive edge in the market.
Additionally, a well-capable process and production system can adapt more readily to changes, be it new regulations or shifts in customer demands.
Understanding the difference between process capability and quality capability is more than just semantics.
It’s about grasping where to focus your efforts for the greatest impact.
While process capability focuses on a specific part of production, quality capability takes a broader view.
Both are essential for ensuring that you not only meet but exceed customer expectations.
By continuously improving both, you set your business up for long-term success, sustainability, and growth.
資料ダウンロード
QCD調達購買管理クラウド「newji」は、調達購買部門で必要なQCD管理全てを備えた、現場特化型兼クラウド型の今世紀最高の購買管理システムとなります。
ユーザー登録
調達購買業務の効率化だけでなく、システムを導入することで、コスト削減や製品・資材のステータス可視化のほか、属人化していた購買情報の共有化による内部不正防止や統制にも役立ちます。
NEWJI DX
製造業に特化したデジタルトランスフォーメーション(DX)の実現を目指す請負開発型のコンサルティングサービスです。AI、iPaaS、および先端の技術を駆使して、製造プロセスの効率化、業務効率化、チームワーク強化、コスト削減、品質向上を実現します。このサービスは、製造業の課題を深く理解し、それに対する最適なデジタルソリューションを提供することで、企業が持続的な成長とイノベーションを達成できるようサポートします。
オンライン講座
製造業、主に購買・調達部門にお勤めの方々に向けた情報を配信しております。
新任の方やベテランの方、管理職を対象とした幅広いコンテンツをご用意しております。
お問い合わせ
コストダウンが利益に直結する術だと理解していても、なかなか前に進めることができない状況。そんな時は、newjiのコストダウン自動化機能で大きく利益貢献しよう!
(Β版非公開)