- お役立ち記事
- The difference between Process Capability Index (Cpk) and Process Performance Index (Ppk)
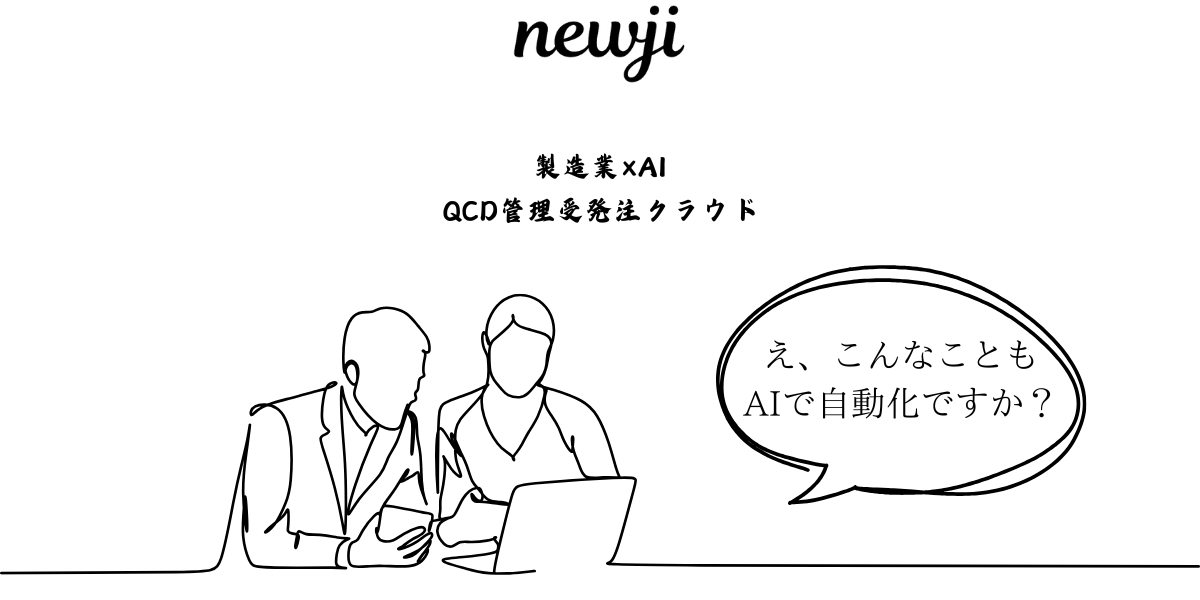
The difference between Process Capability Index (Cpk) and Process Performance Index (Ppk)
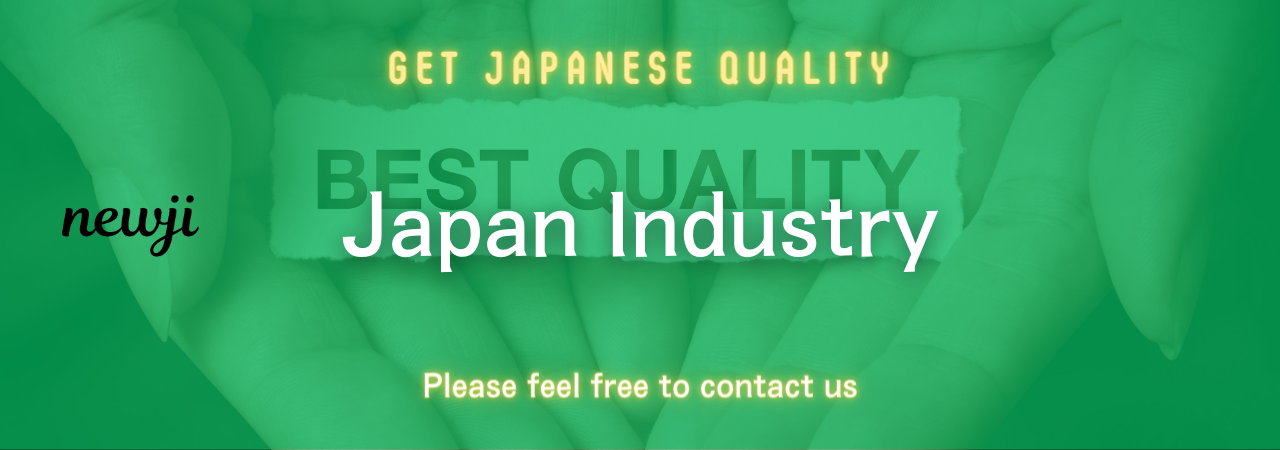
When it comes to understanding the quality of a manufacturing process, two important metrics stand out: the Process Capability Index (Cpk) and the Process Performance Index (Ppk).
These indices help us understand how well a process is performing relative to specified limits.
But what are the differences between Cpk and Ppk, and why do they matter?
目次
Understanding Cpk
The Process Capability Index, or Cpk, measures how well a process can produce output within specified limits.
It takes into account both the process mean (average) and the standard deviation (variation).
Cpk is utilized to determine how close the process is to the target and how consistent it is.
How is Cpk Calculated?
To calculate Cpk, you need to determine the Upper Specification Limit (USL), the Lower Specification Limit (LSL), the process mean, and the standard deviation.
The formula for Cpk is:
Cpk = min ((USL – Mean) / (3*Standard Deviation), (Mean – LSL) / (3*Standard Deviation))
This formula calculates two values: one for the upper side and one for the lower side.
The smaller of the two is taken as the Cpk value.
The result reveals how centered the process is and how much it deviates from the mean.
Interpreting Cpk Values
Typically, a Cpk value of 1.33 or higher is considered acceptable for most industries.
A Cpk value of 1.33 means that the process produces within specifications 99.73% of the time.
If Cpk is less than 1, it suggests the process is not capable of meeting specifications consistently.
A higher Cpk value usually means a more stable process with less variation.
Understanding Ppk
The Process Performance Index, or Ppk, measures the actual performance of a process over time.
Unlike Cpk, which uses sample data, Ppk takes into account the entire process data and examines it against the specifications to evaluate performance.
Because of this, Ppk reflects the real-world performance including all variations.
How is Ppk Calculated?
Similar to Cpk, the formula for Ppk involves using the process mean and standard deviation, along with the USL and LSL.
The formula for Ppk is:
Ppk = min ((USL – Mean) / (3*Standard Deviation), (Mean – LSL) / (3*Standard Deviation))
Here, the standard deviation is taken from the overall process data rather than a sample subset.
This distinction makes Ppk a more comprehensive indicator of process performance.
Interpreting Ppk Values
A Ppk value of 1.33 or higher indicates a well-performing process.
A lower value suggests room for improvement.
Because Ppk includes all variability in the data, it can often be lower than Cpk.
Comparing Ppk and Cpk can help identify areas where the process may have potential issues.
Key Differences Between Cpk and Ppk
While both indices use similar formulas and assess process performance, they do so in different contexts.
Data Source
Cpk is based on sample data from the process.
It’s a theoretical measure assuming the process will continue to perform exactly as it did during the sample period.
On the other hand, Ppk uses the entire dataset from the process.
It evaluates actual historical performance.
This makes Ppk a more realistic measure of process performance.
Variation
Cpk focuses on short-term variation, providing insight into the process capability over a limited timeframe.
It assumes that the process is in control and stable.
Ppk includes long-term variation, encompassing all the variability that occurs over time.
This makes Ppk a more dynamic measure of the process’s real-world performance.
Stability and Control
Cpk is most useful when the process is stable and in control.
It helps predict future performance based on current conditions.
For continuous improvement, examining Cpk can guide efforts to improve process capability.
Ppk, however, is valuable for assessing the overall performance of the process, including any instability and lack of control.
It measures what the process is truly achieving, not just its potential.
Practical Applications
In practice, both Cpk and Ppk are invaluable tools for quality assurance and process improvement.
When to Use Cpk
Use Cpk when you want to understand the potential capability of your process.
It’s particularly useful for new processes or changes where you need to predict future performance.
When to Use Ppk
Ppk is ideal for evaluating the actual performance of an established process.
It’s beneficial for long-term assessments and identifying areas where the process may be encountering issues.
Combining Both Indices
For a comprehensive view of process performance, consider using both Cpk and Ppk metrics together.
Comparing them can provide insights into both short-term capability and long-term performance.
Discrepancies between Cpk and Ppk can highlight areas where the process may need adjustments or further analysis.
Final Thoughts
Understanding the differences between Cpk and Ppk is crucial for maintaining high-quality standards in manufacturing processes.
While Cpk offers insight into potential capability, Ppk provides a realistic measurement of actual performance.
By leveraging both indices, quality assurance teams can gain a holistic view of the process and make informed decisions to drive continuous improvement.
Remember, a stable, well-controlled process is key to producing consistent, high-quality products.
So, keep an eye on both Cpk and Ppk to ensure your processes are running smoothly and meeting specifications effectively.
資料ダウンロード
QCD調達購買管理クラウド「newji」は、調達購買部門で必要なQCD管理全てを備えた、現場特化型兼クラウド型の今世紀最高の購買管理システムとなります。
ユーザー登録
調達購買業務の効率化だけでなく、システムを導入することで、コスト削減や製品・資材のステータス可視化のほか、属人化していた購買情報の共有化による内部不正防止や統制にも役立ちます。
NEWJI DX
製造業に特化したデジタルトランスフォーメーション(DX)の実現を目指す請負開発型のコンサルティングサービスです。AI、iPaaS、および先端の技術を駆使して、製造プロセスの効率化、業務効率化、チームワーク強化、コスト削減、品質向上を実現します。このサービスは、製造業の課題を深く理解し、それに対する最適なデジタルソリューションを提供することで、企業が持続的な成長とイノベーションを達成できるようサポートします。
オンライン講座
製造業、主に購買・調達部門にお勤めの方々に向けた情報を配信しております。
新任の方やベテランの方、管理職を対象とした幅広いコンテンツをご用意しております。
お問い合わせ
コストダウンが利益に直結する術だと理解していても、なかなか前に進めることができない状況。そんな時は、newjiのコストダウン自動化機能で大きく利益貢献しよう!
(Β版非公開)