- お役立ち記事
- The difference between Process Capacity and Equipment Capacity
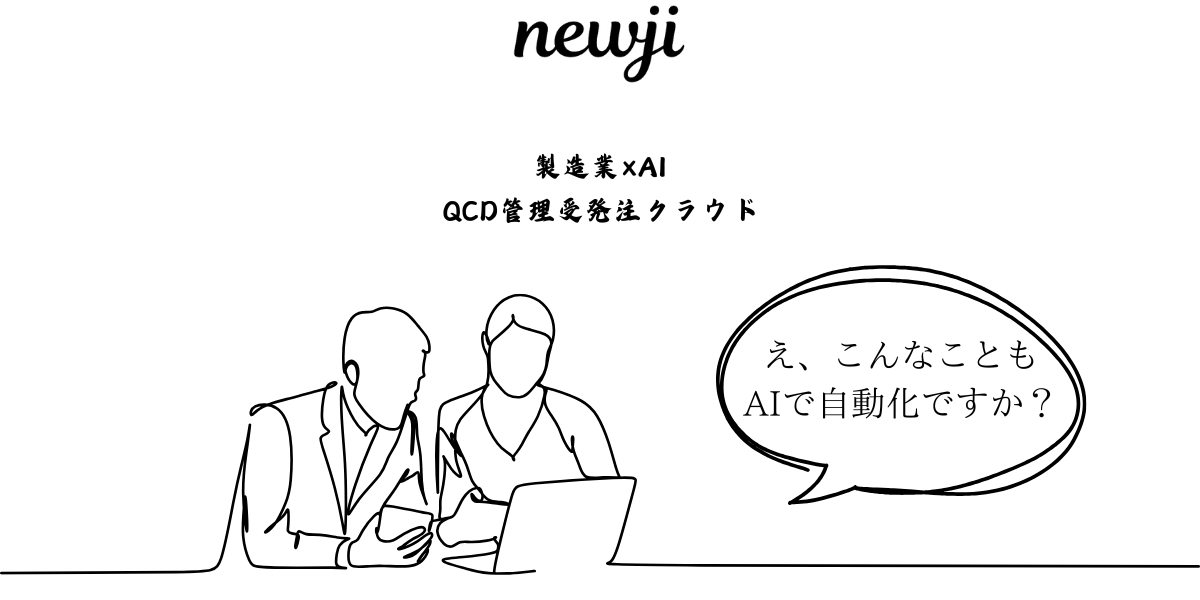
The difference between Process Capacity and Equipment Capacity
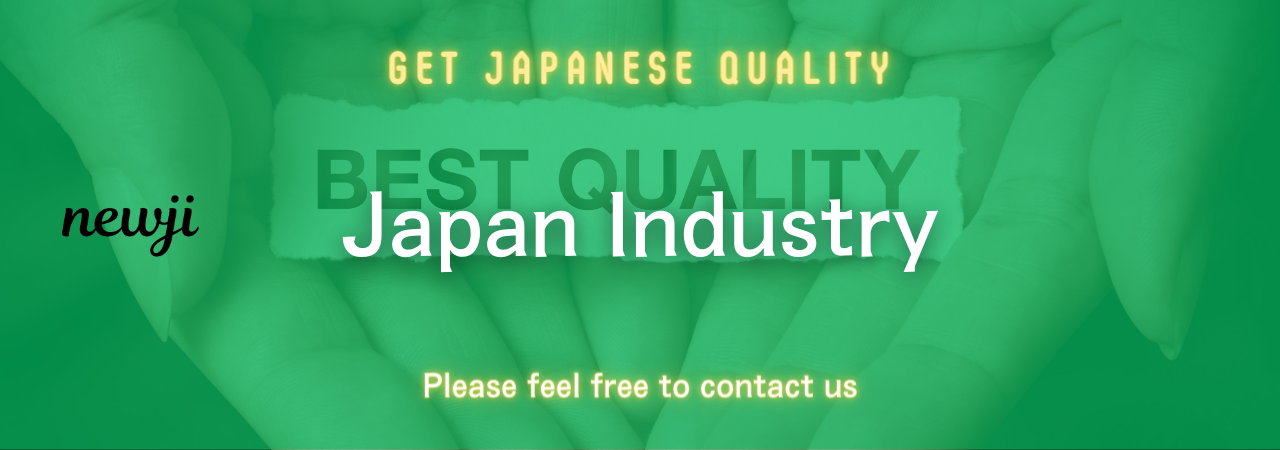
When it comes to manufacturing and production, understanding the capacity of both processes and equipment is essential.
It helps businesses plan, execute, and optimize their workflows efficiently.
However, terms like process capacity and equipment capacity often confuse people, so let’s break them down and explore their key differences.
目次
What is Process Capacity?
Process capacity refers to the maximum output that a specific process can handle within a given period of time.
It is usually measured in units of output per hour, day, or month, depending on the type of production system in place.
Process capacity focuses on the performance of the entire production process rather than individual equipment.
Factors Influencing Process Capacity
Several factors contribute to process capacity:
**Workforce Efficiency:**
The skill level and efficiency of employees directly impact how much work can be accomplished in a specific timeframe.
Proper training and motivation can significantly elevate process capacity.
**Workflow Design:**
How tasks are sequenced and arranged affects overall efficiency.
A well-designed workflow optimizes process capacity by reducing bottlenecks and idle times.
**Quality Control:**
Quality management ensures that fewer defects occur during the production process.
Lower defect rates mean higher effective process capacity as less time is wasted on reworks or repairs.
**Material Flow:**
Efficient movement of raw materials and finished goods through the production line ensures higher process capacity.
Inefficiencies in material handling can slow down the entire process.
What is Equipment Capacity?
On the other hand, equipment capacity refers to the maximum output that individual machinery or equipment can produce in a given period of time.
It is typically measured in terms of pieces per hour, tons per day, or similar units.
Equipment capacity is more focused, dealing with individual machines or stations within the broader production process.
Factors Influencing Equipment Capacity
Various factors affect equipment capacity:
**Machine Specifications:**
The design and capabilities specified by the machinery manufacturer set the upper limits for equipment capacity.
Highly advanced machinery generally comes with better specifications.
**Maintenance:**
Regular maintenance ensures that equipment runs at optimal performance levels.
Neglected maintenance can significantly reduce equipment capacity due to breakdowns or inefficiency.
**Operator Skill:**
The experience and skill of the machine operator can affect how efficiently the equipment is used.
Highly skilled operators can often push machinery to its limits without causing damage.
**Environmental Conditions:**
Extreme temperatures, humidity, or poor working conditions can affect the performance and lifespan of equipment.
Maintaining ideal environmental conditions can help preserve equipment capacity.
Key Differences Between Process Capacity and Equipment Capacity
While both process capacity and equipment capacity aim to determine the maximum output, they focus on different aspects.
Scope
Process capacity takes a holistic view of the entire production line, considering all steps and resources involved.
It encapsulates the broad efficiency of the workflow from start to finish.
On the contrary, equipment capacity focuses on the performance of individual machines or workstations.
Measurement
Process capacity often gets measured in units of output such as tons per day or units per hour but considers the collective output from all involved processes.
Equipment capacity is typically measured in terms specific to the machine, like pieces per minute or gallons per hour.
Influence
Process capacity is affected by factors like workforce efficiency, workflow design, and quality control, emphasizing human elements and overall process organization.
Meanwhile, equipment capacity is more influenced by machine specifications, maintenance schedules, and operator skill, placing importance on the machinery itself.
Optimization
Optimizing process capacity might involve reengineering workflows, redistributing tasks among employees, or implementing quality control measures.
However, optimizing equipment capacity generally revolves around upgrading machinery, improving maintenance protocols, and training operators.
Practical Examples to Illustrate the Differences
Let’s look at practical examples to better understand these differences.
Example of Process Capacity
Consider a bakery that produces cakes.
The process capacity would consider the combined rate of mixing ingredients, baking cakes, decorating them, and packaging.
It examines the bakery’s entire workflow, from raw materials to finished, packaged cakes.
An inefficiency in any of these steps will affect the overall capacity.
Example of Equipment Capacity
Now imagine one of the machines in the bakery, such as the oven.
The equipment capacity will consider how many cakes the oven can bake in an hour.
High-quality ovens with advanced temperature controls may have higher capacities compared to older models.
Additionally, how frequently the oven is cleaned and maintained will affect its performance.
Why Both Are Important
Understanding both process and equipment capacity helps organizations plan their production schedules more effectively.
By distinguishing between the two, businesses can identify specific areas needing improvement.
For instance, if a company identifies its process capacity as the bottleneck, it may focus on optimizing workflow or training employees.
Conversely, if the equipment capacity is lagging, investing in new machinery or enhancing maintenance can help.
Both metrics also play a crucial role in capacity planning and forecasting.
By understanding process and equipment capacities, companies can more accurately predict their ability to meet future demand.
Conclusion
Knowing the difference between process capacity and equipment capacity is essential for efficient production management.
While process capacity deals with the entire workflow and various influencing factors, equipment capacity focuses on the performance and capabilities of individual machines.
Understanding these distinctions helps businesses optimize overall production, plan effectively, and improve both their workforce and machinery.
So, whether you’re running a small workshop or a large manufacturing plant, grasping these concepts will undoubtedly contribute to your operational success.
資料ダウンロード
QCD調達購買管理クラウド「newji」は、調達購買部門で必要なQCD管理全てを備えた、現場特化型兼クラウド型の今世紀最高の購買管理システムとなります。
ユーザー登録
調達購買業務の効率化だけでなく、システムを導入することで、コスト削減や製品・資材のステータス可視化のほか、属人化していた購買情報の共有化による内部不正防止や統制にも役立ちます。
NEWJI DX
製造業に特化したデジタルトランスフォーメーション(DX)の実現を目指す請負開発型のコンサルティングサービスです。AI、iPaaS、および先端の技術を駆使して、製造プロセスの効率化、業務効率化、チームワーク強化、コスト削減、品質向上を実現します。このサービスは、製造業の課題を深く理解し、それに対する最適なデジタルソリューションを提供することで、企業が持続的な成長とイノベーションを達成できるようサポートします。
オンライン講座
製造業、主に購買・調達部門にお勤めの方々に向けた情報を配信しております。
新任の方やベテランの方、管理職を対象とした幅広いコンテンツをご用意しております。
お問い合わせ
コストダウンが利益に直結する術だと理解していても、なかなか前に進めることができない状況。そんな時は、newjiのコストダウン自動化機能で大きく利益貢献しよう!
(Β版非公開)