- お役立ち記事
- The difference between Process Design and Equipment Design
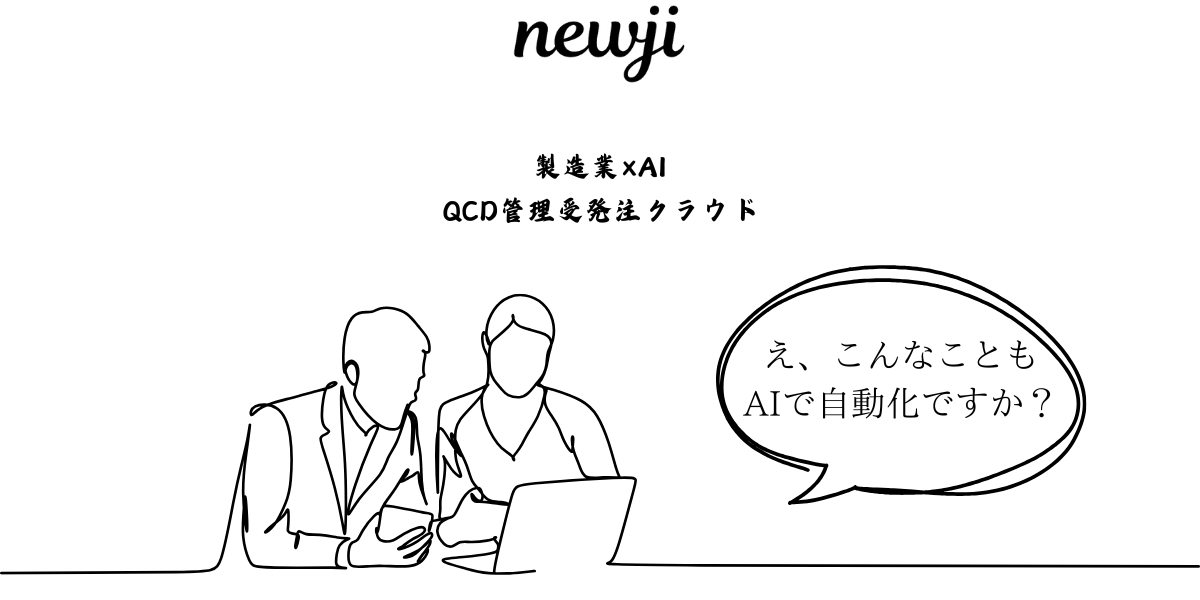
The difference between Process Design and Equipment Design
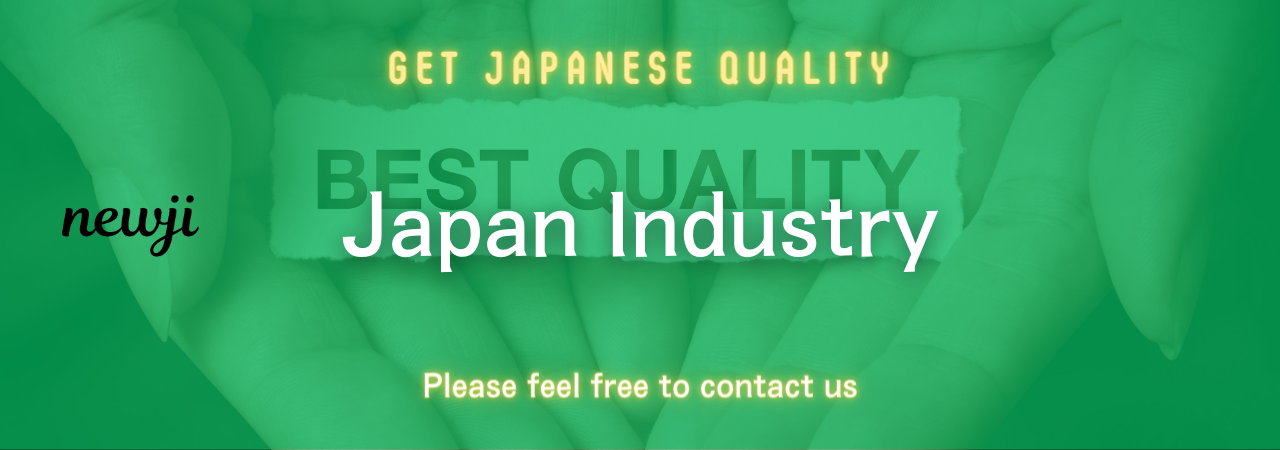
When it comes to the world of engineering and manufacturing, understanding the different roles and responsibilities is essential. Process design and equipment design are two crucial areas in this field. Even though these terms often get used interchangeably, they are quite different from each other. Let’s explore the distinctions between process design and equipment design to see how they impact industries.
目次
Understanding Process Design
Process design is all about creating and optimizing the processes involved in producing a product or providing a service. Think of it as mapping out the journey of a product from its raw materials to the finished goods.
Steps Involved in Process Design
1. **Defining Objectives:** The first step in process design is defining what you want to achieve. This could be improving efficiency, enhancing product quality, or reducing costs.
2. **Flowchart Creation:** Next, engineers create detailed flowcharts that outline each step of the process. This includes every action from input to output.
3. **Testing and Analysis:** Before implementation, the process is tested and analyzed. Engineers look for potential problems and try to find the best solutions.
4. **Optimization:** Lastly, the process is fine-tuned. This involves making adjustments based on the analysis and finding ways to streamline operations.
Importance of Process Design
Process design is vital because it sets the stage for everything that follows. An effective process design can lead to significant cost savings, higher productivity, and better-quality products. Moreover, it ensures that operations run smoothly and efficiently with minimal waste.
Understanding Equipment Design
Equipment design, on the other hand, focuses on the actual machinery and tools used in the production process. This is about designing the physical devices that will be used to carry out the steps outlined in the process design.
Steps Involved in Equipment Design
1. **Requirements Gathering:** The first step is to understand what the equipment needs to achieve. This involves understanding the specifications and requirements of the process.
2. **Concept Development:** Engineers then develop different concepts and models. They consider factors like functionality, cost, and compatibility with the process.
3. **Prototyping:** A prototype of the equipment is built to test its functionality and design. This helps identify potential problems early on.
4. **Final Design:** Finally, the equipment design is finalized, and manufacturing begins.
Importance of Equipment Design
Quality equipment design is essential for ensuring the reliability and efficiency of the production process. The right equipment can increase productivity, improve product quality, and reduce downtime. It also ensures that the process is safe for workers and meets regulatory standards.
Key Differences Between Process Design and Equipment Design
Focus
The primary focus of process design is on creating and optimizing the sequence of operations needed to produce a product or service. It’s more about planning and strategizing.
In contrast, equipment design centers on creating the physical machines and tools that will be used to execute the processes. It’s more about the technical and engineering aspects.
End Goal
The end goal of process design is to ensure that the overall production process is as efficient and effective as possible. It aims to minimize waste and maximize productivity.
On the other hand, the goal of equipment design is to create machinery that meets the needs of the process. The equipment must be reliable, safe, and efficient.
Scope
Process design generally has a broader scope. It involves multiple disciplines, including chemistry, physics, and various engineering fields. It requires a holistic approach to understand how each part of the process interacts with the others.
Equipment design tends to be more specialized. It requires a deep understanding of mechanical, electrical, and sometimes software engineering to create sophisticated machinery.
Interaction with Other Fields
Process design often involves working closely with quality control, supply chain management, and even marketing teams. This is because the process impacts various aspects of the business, from product quality to customer satisfaction.
Equipment design usually requires close collaboration with manufacturing and maintenance teams. These teams are responsible for ensuring the equipment runs smoothly and efficiently.
Why Both are Essential
While process design and equipment design are distinct disciplines, they are both essential for the success of any production operation. A well-designed process without the right equipment won’t be effective. Similarly, even the most advanced equipment won’t be useful without a good process to guide it.
In industries like pharmaceuticals, automotive manufacturing, and food production, both types of design play a crucial role. The integration of process and equipment design leads to a seamless and efficient production environment.
Conclusion
Understanding the difference between process design and equipment design is crucial for anyone involved in manufacturing or production. Process design lays the groundwork by mapping out the steps needed to produce a product efficiently. Equipment design, in turn, creates the machines that execute these steps.
Both are essential for achieving high productivity, quality, and efficiency. While they have different focuses and end goals, they work together to ensure the smooth operation of the production process. By integrating effective process and equipment design, businesses can achieve significant improvements in performance and profitability.
資料ダウンロード
QCD調達購買管理クラウド「newji」は、調達購買部門で必要なQCD管理全てを備えた、現場特化型兼クラウド型の今世紀最高の購買管理システムとなります。
ユーザー登録
調達購買業務の効率化だけでなく、システムを導入することで、コスト削減や製品・資材のステータス可視化のほか、属人化していた購買情報の共有化による内部不正防止や統制にも役立ちます。
NEWJI DX
製造業に特化したデジタルトランスフォーメーション(DX)の実現を目指す請負開発型のコンサルティングサービスです。AI、iPaaS、および先端の技術を駆使して、製造プロセスの効率化、業務効率化、チームワーク強化、コスト削減、品質向上を実現します。このサービスは、製造業の課題を深く理解し、それに対する最適なデジタルソリューションを提供することで、企業が持続的な成長とイノベーションを達成できるようサポートします。
オンライン講座
製造業、主に購買・調達部門にお勤めの方々に向けた情報を配信しております。
新任の方やベテランの方、管理職を対象とした幅広いコンテンツをご用意しております。
お問い合わせ
コストダウンが利益に直結する術だと理解していても、なかなか前に進めることができない状況。そんな時は、newjiのコストダウン自動化機能で大きく利益貢献しよう!
(Β版非公開)