- お役立ち記事
- The difference between Process Design and Factory Layout
月間76,176名の
製造業ご担当者様が閲覧しています*
*2025年3月31日現在のGoogle Analyticsのデータより
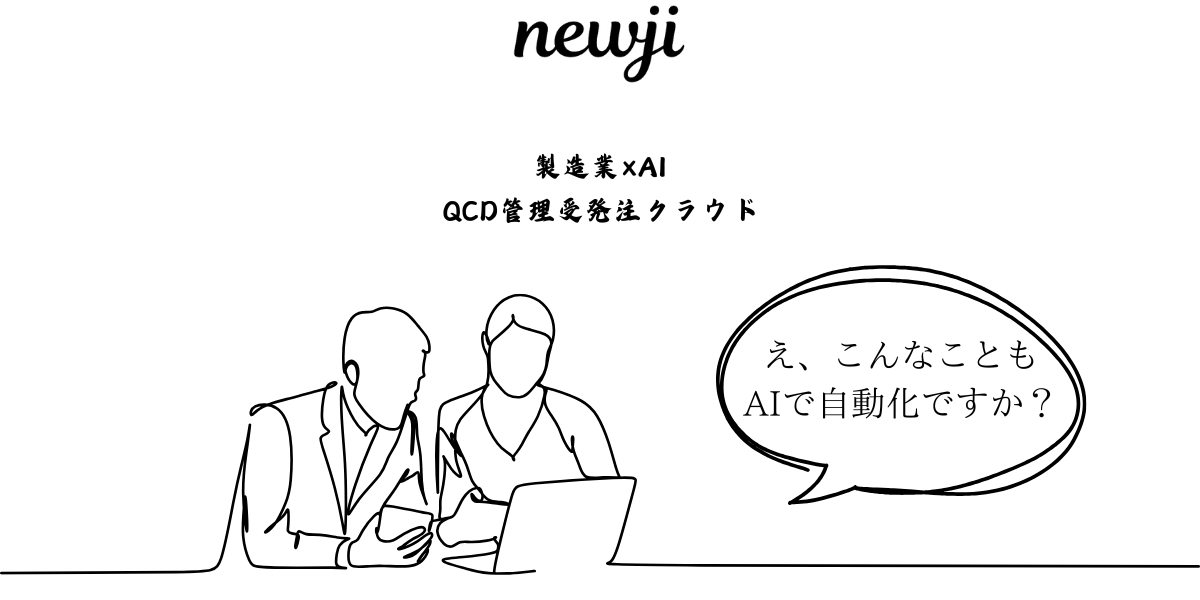
The difference between Process Design and Factory Layout
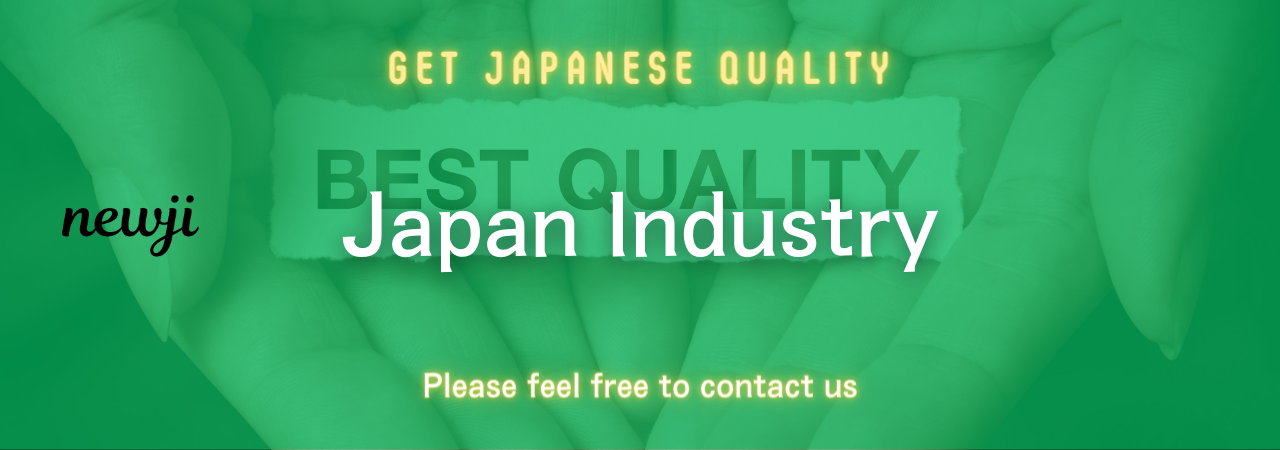
Understanding the differences between process design and factory layout can help businesses improve productivity, optimize operations, and enhance overall workflow efficiency. Though these two concepts are interconnected, they serve distinct purposes within a manufacturing or production environment. This article delves into the specifics of each aspect and outlines their significance in successful manufacturing operations.
目次
What is Process Design?
Process design refers to the planning and structuring of the sequence of steps or activities required to produce a product or provide a service. It involves determining the most efficient and effective methods of converting raw materials into finished goods. The ultimate goal is to create a streamlined process that minimizes waste, reduces costs, and ensures high-quality output.
Key Components of Process Design
Several key elements make up process design. Here are some of the most important:
1. Task Identification: Identifying the specific tasks needed to achieve the end product is the first step. This involves breaking down the production process into individual activities.
2. Workflow Sequencing: Determining the optimal order in which tasks should be performed is crucial for efficiency. Proper sequencing can reduce unnecessary steps and transitions.
3. Resource Allocation: Allocating the right resources, including labor, machinery, and materials, ensures that each task can be performed effectively.
4. Quality Control: Implementing measures to ensure that each step meets quality standards helps maintain product consistency.
5. Time Management: Analyzing and optimizing the time required for each task can help streamline the process and reduce production time.
Why is Process Design Important?
Process design is essential for several reasons:
1. Efficiency: A well-designed process eliminates unnecessary steps, reducing the time and resources needed for production.
2. Cost Reduction: Efficient processes minimize waste and lower production costs.
3. Quality Improvement: Ensuring that each step is performed correctly and consistently improves the overall quality of the product.
4. Flexibility: A well-structured process can easily adapt to changes in demand or production requirements.
5. Employee Satisfaction: Clear processes make it easier for employees to understand their roles and responsibilities, leading to higher job satisfaction.
What is Factory Layout?
Factory layout, also known as plant layout, involves the physical arrangement of machinery, equipment, and workstations within a manufacturing facility. The goal is to optimize the flow of materials and work through the production process while ensuring worker safety and comfort.
Key Components of Factory Layout
Several factors contribute to an effective factory layout:
1. Space Utilization: Efficient use of available space ensures that machinery, equipment, and workstations are placed optimally.
2. Workflow: The layout should support a smooth flow of materials and work, minimizing bottlenecks and delays.
3. Safety: Ensuring that the layout adheres to safety standards protects workers from potential hazards.
4. Accessibility: Equipment and materials should be easily accessible to minimize delays and improve efficiency.
5. Flexibility: The layout should be adaptable to changes in production requirements or the introduction of new machinery.
Why is Factory Layout Important?
The importance of factory layout cannot be overstated. Here are some key benefits:
1. Increased Productivity: An optimized layout reduces the time and effort required to move materials and complete tasks.
2. Reduced Costs: Efficient use of space and resources lowers operational costs.
3. Enhanced Safety: A well-designed layout minimizes the risk of accidents and injuries.
4. Improved Quality: Streamlined workflows reduce the chances of errors and defects.
5. Employee Comfort: A comfortable and safe working environment can improve employee morale and productivity.
Comparing Process Design and Factory Layout
While both process design and factory layout aim to improve efficiency and productivity, they focus on different aspects of the production environment.
Focus Areas
Process design is concerned with the sequence of tasks and activities required to produce a product. It focuses on workflow, task sequencing, resource allocation, and quality control.
Factory layout, on the other hand, deals with the physical arrangement of machinery, equipment, and workstations. It emphasizes space utilization, workflow, safety, and accessibility.
Goals
The primary goal of process design is to create a streamlined, efficient, and effective production process. It seeks to minimize waste, reduce costs, and ensure high-quality output.
The factory layout aims to optimize the physical space within the manufacturing facility. It focuses on improving the flow of materials and work, reducing bottlenecks, and ensuring worker safety.
Interdependence
Though distinct, process design and factory layout are highly interdependent. An efficient process design can significantly influence the layout of a factory, and vice versa. For example, a process that requires frequent movement of materials may benefit from a layout that minimizes travel distances. Conversely, an optimized factory layout can enhance the efficiency of the production process.
Implementing Process Design and Factory Layout
Effectively implementing process design and factory layout requires careful planning and collaboration. Here are some steps businesses can take:
Analyze Current Operations
Begin by analyzing current operations to identify areas for improvement. Collect data on production times, resource usage, and workflows.
Set Clear Objectives
Define clear objectives for both process design and factory layout. These could include reducing production time, lowering costs, improving quality, or enhancing worker safety.
Involve Stakeholders
Involve key stakeholders, including employees, in the planning process. Their insights and feedback can help identify potential issues and areas for improvement.
Develop and Test Plans
Develop detailed plans for both process design and factory layout. Test these plans on a small scale to identify potential issues and make necessary adjustments.
Implement Changes
Once the plans have been tested and refined, implement the changes across the entire facility. Monitor progress and make adjustments as needed to ensure continuous improvement.
Understanding and implementing effective process design and factory layout can significantly enhance a manufacturing facility’s efficiency, productivity, and overall success. By focusing on the distinct but interrelated aspects of these concepts, businesses can create a streamlined and optimized production environment that benefits both employees and customers.
資料ダウンロード
QCD管理受発注クラウド「newji」は、受発注部門で必要なQCD管理全てを備えた、現場特化型兼クラウド型の今世紀最高の受発注管理システムとなります。
ユーザー登録
受発注業務の効率化だけでなく、システムを導入することで、コスト削減や製品・資材のステータス可視化のほか、属人化していた受発注情報の共有化による内部不正防止や統制にも役立ちます。
NEWJI DX
製造業に特化したデジタルトランスフォーメーション(DX)の実現を目指す請負開発型のコンサルティングサービスです。AI、iPaaS、および先端の技術を駆使して、製造プロセスの効率化、業務効率化、チームワーク強化、コスト削減、品質向上を実現します。このサービスは、製造業の課題を深く理解し、それに対する最適なデジタルソリューションを提供することで、企業が持続的な成長とイノベーションを達成できるようサポートします。
製造業ニュース解説
製造業、主に購買・調達部門にお勤めの方々に向けた情報を配信しております。
新任の方やベテランの方、管理職を対象とした幅広いコンテンツをご用意しております。
お問い合わせ
コストダウンが利益に直結する術だと理解していても、なかなか前に進めることができない状況。そんな時は、newjiのコストダウン自動化機能で大きく利益貢献しよう!
(β版非公開)