- お役立ち記事
- The difference between Process Improvement and Quality Improvement
月間76,176名の
製造業ご担当者様が閲覧しています*
*2025年3月31日現在のGoogle Analyticsのデータより
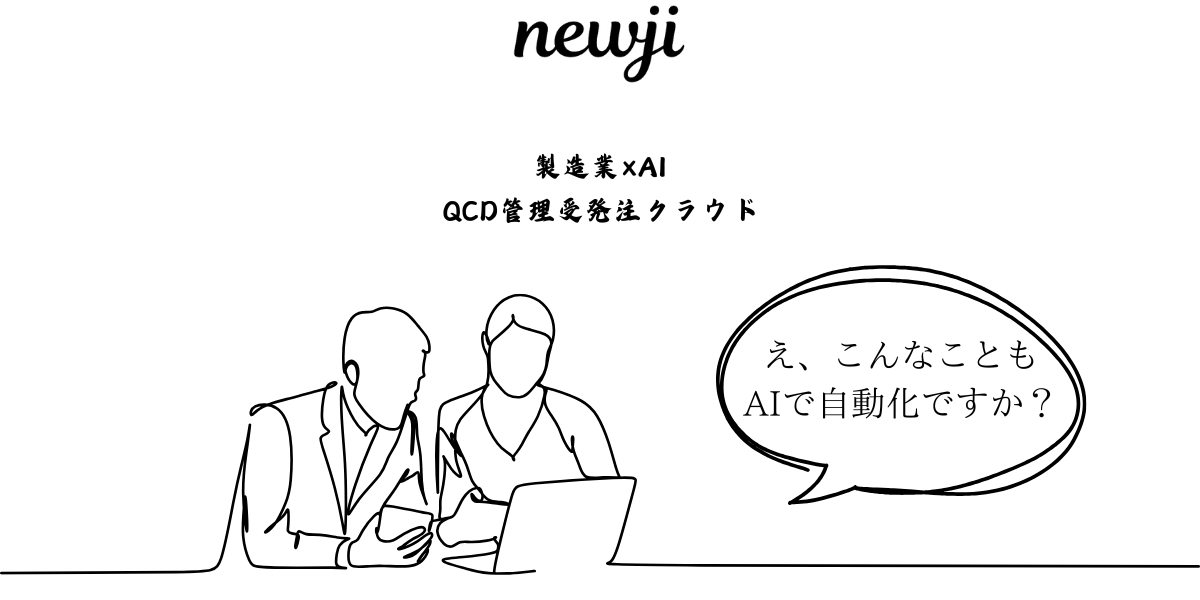
The difference between Process Improvement and Quality Improvement
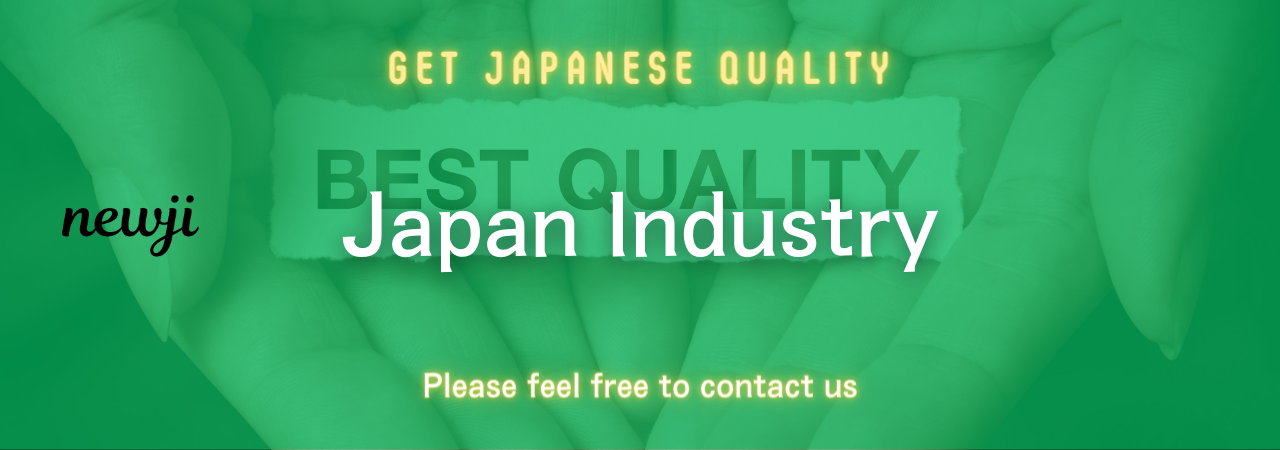
In today’s competitive business environment, organizations continually seek ways to enhance efficiency and deliver superior products and services.
Two critical strategies to achieve these goals are Process Improvement and Quality Improvement.
While they may sound similar, and indeed are closely related, they are distinct concepts.
Understanding the difference between these two approaches can significantly influence a company’s performance and growth.
In this article, we will explore the nuances between Process Improvement and Quality Improvement.
目次
Understanding Process Improvement
Definition
Process Improvement focuses on the processes within an organization.
It aims to enhance the way tasks and operations are performed, reducing waste, increasing efficiency, and improving overall workflow.
It primarily looks at the “how” of operations.
Objectives
The primary objective of Process Improvement is to streamline processes to make them more efficient.
This can result in cost savings, reduced time, and improved resource utilization.
For example, if a manufacturing plant reduces the time it takes to switch equipment from producing one product to another, it achieves Process Improvement.
Methodologies
Various methodologies are employed in Process Improvement, including Lean, Six Sigma, and Value Stream Mapping.
Lean focuses on eliminating waste, whereas Six Sigma aims at reducing variations and defects.
Value Stream Mapping helps visualize the entire process flow to identify areas for improvement.
By utilizing these methodologies, businesses can create more efficient and effective processes.
Examples
Let’s consider a customer service department as an example.
Through Process Improvement, the company may decide to automate some aspects of customer inquiry handling, which decreases response times and frees up staff for more complex tasks.
Another example could involve a construction company refining its project management processes to ensure projects are completed on time and within budget.
These improvements help in creating more predictable and efficient systems.
Understanding Quality Improvement
Definition
Quality Improvement, on the other hand, focuses on the outcome or deliverable of a process.
Its goal is to enhance the quality of products or services being produced.
This means looking at the “what” of operations.
Objectives
The main objective of Quality Improvement is to ensure that the final product or service meets or exceeds customer expectations.
This can lead to higher customer satisfaction, repeat business, and enhanced reputation.
For example, if a software company introduces additional testing phases to ensure their product is bug-free before launch, it is engaging in Quality Improvement.
Methodologies
Common methodologies used in Quality Improvement include Total Quality Management (TQM), Continuous Quality Improvement (CQI), and the Plan-Do-Check-Act (PDCA) cycle.
TQM focuses on long-term success through customer satisfaction, while CQI seeks to continually enhance processes over time.
The PDCA cycle is a repetitive four-stage model used to achieve ongoing improvements in processes and outcomes.
These methodologies guide businesses in implementing quality improvement initiatives.
Examples
Imagine a car manufacturing company.
Through Quality Improvement, the company may decide to implement stricter quality checks at each stage of assembly to ensure no defective parts make it to the final product.
Another example could be a hospital introducing new protocols to reduce patient infection rates during surgeries.
These improvements ensure the end product or service is safe, reliable, and of high quality.
Comparing Process Improvement and Quality Improvement
Primary Focus
While Process Improvement is concerned with enhancing the processes and workflows within an organization, Quality Improvement concentrates on the quality of the end product or service.
Both are aimed at improvement, but their focal points differ significantly.
Approaches and Techniques
The approaches and techniques used in Process and Quality Improvement often overlap, but the application and focus are different.
For example, Lean and Six Sigma can be used for both, but Lean is more commonly associated with Process Improvement, and Six Sigma is frequently linked with Quality Improvement.
Understanding which technique to apply depends on whether the aim is to enhance efficiency (Process) or quality (Product/Service).
Impact on Business
Improving processes can lead to cost savings, faster delivery times, and better resource utilization.
Quality Improvement, on the other hand, can lead to higher customer satisfaction, reduced returns, and a stronger brand reputation.
Both types of improvement can have significant and complementary impacts on an organization.
For instance, streamlined processes can contribute to improving the quality of the final product and vice versa.
How to Decide Which One to Focus On
Assessing Business Needs
To determine whether your organization should focus more on Process Improvement or Quality Improvement, assess your current challenges and goals.
If inefficiencies and high operational costs are major issues, Process Improvement might be the best approach.
Conversely, if customer complaints about product quality are prevalent, focusing on Quality Improvement could be more beneficial.
Combining Both Approaches
Many successful organizations do not choose one over the other but instead integrate both approaches.
By improving processes, they also enhance quality, and by ensuring high-quality output, they often streamline their processes necessitated by fewer reworks and defects.
Combining these approaches can create a holistic improvement environment.
Conclusion
Understanding and differentiating between Process Improvement and Quality Improvement is crucial for any organization aiming for excellence.
While Process Improvement emphasizes the efficiency of workflows and operations, Quality Improvement targets the final product or service’s excellence.
Both approaches are essential and often interlinked.
Evaluating your business needs and integrating both strategies can lead to substantial overall improvements, driving a company towards sustained success.
資料ダウンロード
QCD管理受発注クラウド「newji」は、受発注部門で必要なQCD管理全てを備えた、現場特化型兼クラウド型の今世紀最高の受発注管理システムとなります。
ユーザー登録
受発注業務の効率化だけでなく、システムを導入することで、コスト削減や製品・資材のステータス可視化のほか、属人化していた受発注情報の共有化による内部不正防止や統制にも役立ちます。
NEWJI DX
製造業に特化したデジタルトランスフォーメーション(DX)の実現を目指す請負開発型のコンサルティングサービスです。AI、iPaaS、および先端の技術を駆使して、製造プロセスの効率化、業務効率化、チームワーク強化、コスト削減、品質向上を実現します。このサービスは、製造業の課題を深く理解し、それに対する最適なデジタルソリューションを提供することで、企業が持続的な成長とイノベーションを達成できるようサポートします。
製造業ニュース解説
製造業、主に購買・調達部門にお勤めの方々に向けた情報を配信しております。
新任の方やベテランの方、管理職を対象とした幅広いコンテンツをご用意しております。
お問い合わせ
コストダウンが利益に直結する術だと理解していても、なかなか前に進めることができない状況。そんな時は、newjiのコストダウン自動化機能で大きく利益貢献しよう!
(β版非公開)