- お役立ち記事
- The difference between Process Improvement and Quality Improvement
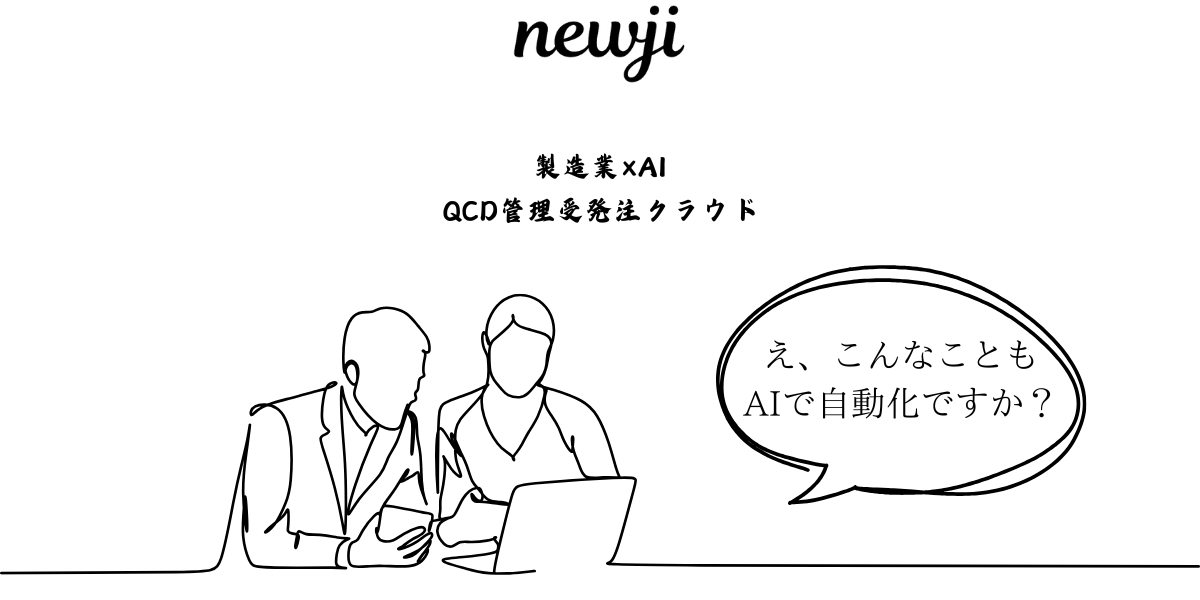
The difference between Process Improvement and Quality Improvement
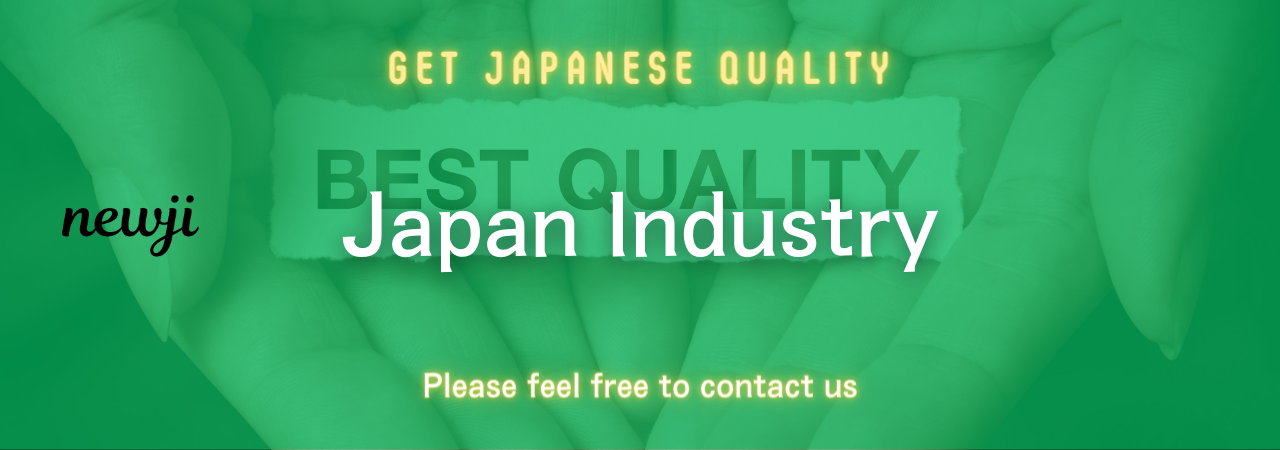
Process and quality improvement are two concepts often discussed in business management and operations. Both play critical roles in enhancing organizational efficiency and ensuring that customers receive high-quality products or services. However, while the terms may appear similar on the surface, they serve different purposes and involve distinct approaches. Understanding these differences is essential for businesses aiming for operational excellence and customer satisfaction.
目次
What is Process Improvement?
Process improvement refers to the systematic approach to enhancing business procedures to achieve better efficiency and effectiveness. It involves the identification, analysis, and modification of existing processes to reduce inefficiencies, cut costs, and increase productivity. By improving processes, organizations can make their operations more streamlined, which in turn, enhances overall performance.
Key Elements of Process Improvement
The critical elements of process improvement include identifying bottlenecks, reducing cycle time, eliminating waste, and enhancing workflow. Tools like Six Sigma, Lean Manufacturing, and Total Quality Management (TQM) are often used in process improvement initiatives. These methodologies provide structured frameworks for analyzing and improving processes.
Examples of Process Improvement
An example of process improvement might be a manufacturing company reducing the time it takes to assemble a product by reorganizing the assembly line and automating specific tasks. Another example could be a service-based business streamlining its customer service process to resolve inquiries faster by implementing new software.
What is Quality Improvement?
Quality improvement, on the other hand, focuses on enhancing the quality of products or services delivered by an organization. The goal is to meet or exceed customer expectations consistently. This involves not just improving processes but also monitoring outcomes, ensuring that the final output is of the highest possible standard.
Key Elements of Quality Improvement
Key elements include setting quality benchmarks, monitoring performance, analyzing outcomes, and implementing corrective actions. Tools like Control Charts, Pareto Analysis, and Root Cause Analysis are often employed to monitor and improve quality. Unlike process improvement, which focuses on the operations, quality improvement zeroes in on the product or service delivered to the customer.
Examples of Quality Improvement
An example of quality improvement could be a company conducting rigorous product testing to identify defects and implement changes in the manufacturing process to eliminate these issues. In a service context, an example could be a healthcare facility analyzing patient feedback to improve the quality of patient care.
Differences Between Process Improvement and Quality Improvement
While both process improvement and quality improvement aim for efficiency and customer satisfaction, they differ in focus and approach.
Focus Areas
Process improvement is primarily concerned with optimizing the steps involved in producing a product or delivering a service. It looks at how tasks are performed and seeks ways to make them more efficient. On the other hand, quality improvement focuses on the final output, ensuring that the product or service meets established standards and fulfills customer expectations.
Approaches and Methodologies
Process improvement often employs methodologies like Lean and Six Sigma, which provide structured approaches for identifying inefficiencies and making improvements. Quality improvement uses tools like Control Charts and Pareto Analysis to monitor quality levels and identify areas for enhancement. While both methods may overlap, their specific tools and strategies differ.
Outcome Metrics
The success of process improvement is usually measured through metrics like reduced cycle time, lower production costs, and increased throughput. For quality improvement, metrics include defect rates, customer satisfaction scores, and adherence to industry standards. While both sets of metrics aim to improve organizational performance, they focus on different aspects of the operation.
How They Work Together
While process improvement and quality improvement have distinct focuses, they are not mutually exclusive. In fact, they often complement each other. A business may start with process improvement to streamline operations and then move on to quality improvement to ensure that the enhanced processes produce high-quality outcomes. Alternatively, addressing quality issues may highlight inefficiencies in processes, leading to process improvement initiatives.
Integrated Approach
Many organizations adopt an integrated approach, combining elements of both process and quality improvement. This ensures that operations are efficient and the quality of products or services is high. For instance, a manufacturing company might use Lean principles to improve process efficiency and Six Sigma for quality control, creating a balanced approach that covers both areas.
Benefits of Understanding the Difference
Understanding the difference between process improvement and quality improvement helps organizations to allocate resources more effectively and address their specific needs. It enables businesses to take a more targeted approach, focusing on the areas that require the most attention. This, in turn, leads to better outcomes, higher customer satisfaction, and increased profitability.
Enhanced Decision-Making
By knowing where to focus their efforts, companies can make more informed decisions. For example, if the primary issue is inefficiency, process improvement initiatives can be prioritized. If the main concern is product defects, quality improvement measures can take precedence.
Optimal Resource Allocation
Understanding these differences allows for optimal allocation of resources, whether it’s time, money, or personnel. Resources can be directed to the most critical areas, ensuring that initiatives yield the highest returns.
Process improvement and quality improvement are essential components of effective business management. While they have different focuses and employ different methodologies, they share the common goal of enhancing overall organizational performance. Recognizing and understanding the distinctions between them allows businesses to implement targeted strategies, leading to more efficient operations and higher-quality outcomes. Through a balanced approach that integrates both process and quality improvement, organizations can achieve lasting success and customer satisfaction.
資料ダウンロード
QCD調達購買管理クラウド「newji」は、調達購買部門で必要なQCD管理全てを備えた、現場特化型兼クラウド型の今世紀最高の購買管理システムとなります。
ユーザー登録
調達購買業務の効率化だけでなく、システムを導入することで、コスト削減や製品・資材のステータス可視化のほか、属人化していた購買情報の共有化による内部不正防止や統制にも役立ちます。
NEWJI DX
製造業に特化したデジタルトランスフォーメーション(DX)の実現を目指す請負開発型のコンサルティングサービスです。AI、iPaaS、および先端の技術を駆使して、製造プロセスの効率化、業務効率化、チームワーク強化、コスト削減、品質向上を実現します。このサービスは、製造業の課題を深く理解し、それに対する最適なデジタルソリューションを提供することで、企業が持続的な成長とイノベーションを達成できるようサポートします。
オンライン講座
製造業、主に購買・調達部門にお勤めの方々に向けた情報を配信しております。
新任の方やベテランの方、管理職を対象とした幅広いコンテンツをご用意しております。
お問い合わせ
コストダウンが利益に直結する術だと理解していても、なかなか前に進めることができない状況。そんな時は、newjiのコストダウン自動化機能で大きく利益貢献しよう!
(Β版非公開)