- お役立ち記事
- The difference between Processing Cost and Manufacturing Cost
月間76,176名の
製造業ご担当者様が閲覧しています*
*2025年3月31日現在のGoogle Analyticsのデータより
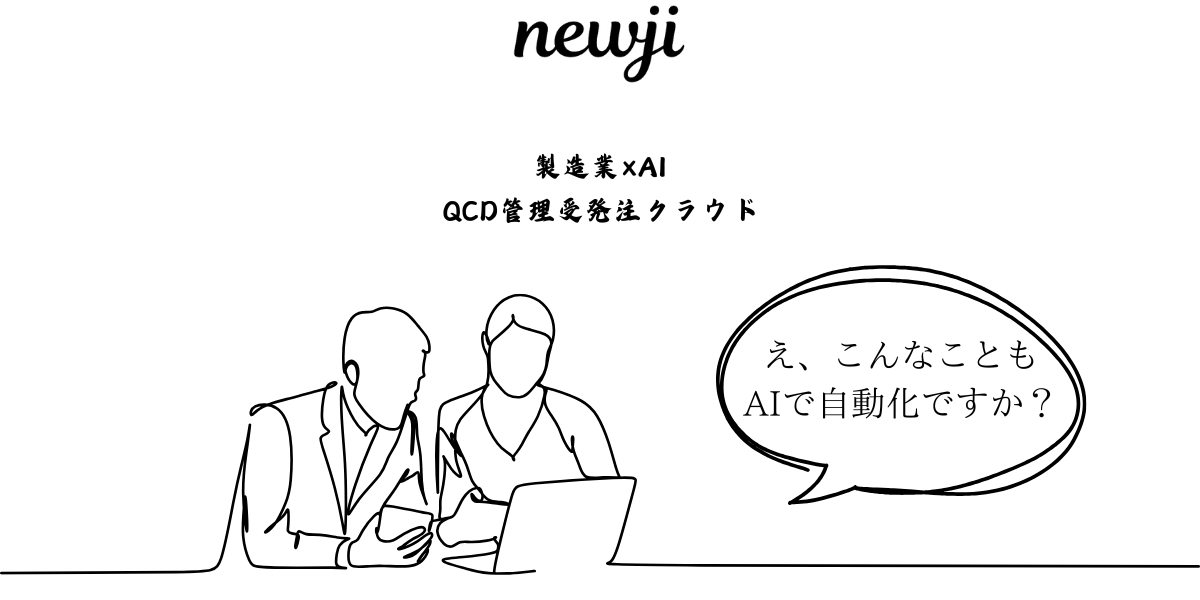
The difference between Processing Cost and Manufacturing Cost
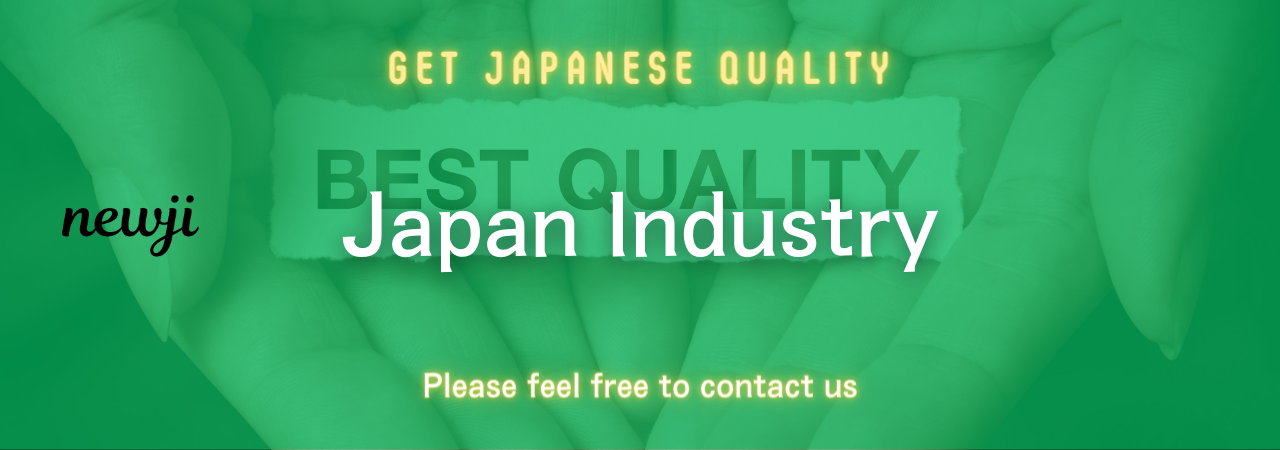
In the world of manufacturing, understanding the costs associated with production is crucial for effective budgeting and pricing.
Two key terms often come up: processing cost and manufacturing cost.
Though they may seem similar, they have distinct meanings and implications.
Let’s dive into what sets them apart.
目次
Definition of Processing Cost
Processing cost refers to the expenses incurred during the transformation of raw materials into a finished product.
This includes costs related to labor, utilities, and operational expenses.
It focuses on the costs that directly affect the production process, excluding any expenses before or after this phase.
For example, the electricity used to run machinery or the wages paid to the workers operating these machines are part of the processing costs.
Components of Processing Cost
1. **Direct Labor:** This involves the wages and benefits given to the employees directly engaged in the production process.
2. **Utilities:** Costs associated with electricity, water, and gas used during production.
3. **Maintenance:** Regular maintenance of the machinery and equipment used in the production line.
4. **Supplies:** All the consumables required like lubricants, cleaning agents, and safety equipment.
Definition of Manufacturing Cost
Manufacturing cost encompasses all expenses related to producing a product, from obtaining raw materials to delivering the final product.
This broad category includes processing costs but also considers additional elements such as raw materials and overhead costs.
To put it simply, manufacturing cost gives the total financial input required to create and sell a product.
Components of Manufacturing Cost
1. **Raw Materials:** The initial materials needed to start production.
2. **Processing Cost:** As outlined earlier, this involves the direct costs associated with production.
3. **Overhead Costs:** Indirect costs that include facility rent, administrative salaries, and depreciation of equipment.
Key Differences Between Processing Cost and Manufacturing Cost
While both terms deal with expenses in production, their scopes are different.
Processing cost covers only the direct expenses tied to transforming raw materials into finished products.
In contrast, manufacturing cost includes a broader range of expenses necessary for complete production, from material acquisition to final delivery.
Scope and Coverage
Processing cost is narrower in scope, focusing solely on direct production expenses.
It’s a subset of manufacturing cost, directly tied to the actual process of making a product.
Manufacturing cost, however, takes a more comprehensive view, incorporating every expense involved in the journey from raw material to finished product.
Expense Categories
Processing costs are mainly concerned with direct labor, utilities, maintenance, and production supplies.
They do not account for raw material costs or overarching expenses like facility rent or administrative salaries.
Manufacturing costs cover all these categories, providing a complete picture of the financial commitment required for production.
Importance of Understanding the Differences
Knowing the distinction between processing cost and manufacturing cost is essential for several reasons, especially for budgeting and financial planning within a company.
Budgeting
Being clear about these costs helps in accurate budgeting.
By separating processing costs from overall manufacturing costs, businesses can pinpoint where they might save money or need to invest more.
Pricing Strategy
Understanding these costs allows companies to set more accurate prices for their products.
Manufacturers can ensure they cover all expenses and still make a profit by accurately calculating the total manufacturing cost.
Financial Analysis
Clear differentiation aids in financial analysis, helping companies identify which areas are most cost-effective.
This can lead to better decision-making and improved financial health for the company.
How to Calculate These Costs
Accurately calculating processing and manufacturing costs requires careful data collection and analysis.
Calculating Processing Cost
1. **Identify Direct Labor Costs:** Sum up the wages and benefits of all employees directly involved in production.
2. **Calculate Utilities:** Track the energy consumption and any other utilities used during the production process.
3. **Add Maintenance Costs:** Estimate the regular maintenance expenses of machinery and equipment.
4. **Sum Consumables:** Include costs of all the supplies used up in the production process.
Calculating Manufacturing Cost
1. **Combine Processing Costs:** Start with the total processing costs you’ve already calculated.
2. **Add Raw Material Costs:** Include the expenses for all raw materials required for production.
3. **Incorporate Overhead Costs:** Sum up indirect expenses such as facility rent, administrative salaries, and equipment depreciation.
Real-World Application
Understanding and accurately computing these costs are crucial for any manufacturing business.
For instance, a toy factory might use raw materials such as plastic and paint.
The process of converting these raw materials into finished toys involves direct labor, electricity to run the molding machines, and maintenance of these machines.
All these constitute the processing cost.
However, to get the manufacturing cost, the factory also needs to add the cost of raw materials and overhead expenses like factory rent and salaries of non-production staff.
Case Study: Reducing Processing Costs
Let’s consider a case where a company wants to reduce its processing costs.
Upon analysis, it finds that energy consumption is a significant portion.
By investing in energy-efficient machinery, the company can lower its electricity bills.
Additionally, regular maintenance can ensure machines run more efficiently, preventing costly breakdowns.
Case Study: Controlling Manufacturing Costs
Another company might focus on controlling overall manufacturing costs.
This could involve negotiating better prices for raw materials, reducing overhead by optimizing administrative processes, or improving logistics to reduce delivery costs.
Conclusion
Understanding the difference between processing cost and manufacturing cost is crucial for effective financial management in manufacturing.
Processing cost is a subset of manufacturing cost, focusing on the direct expenses of turning raw materials into finished products.
In contrast, manufacturing cost covers the entire gamut of expenses, from raw materials to overheads.
By accurately identifying and calculating these costs, businesses can make informed decisions about budgeting, pricing, and financial planning.
This, in turn, can lead to improved profitability and long-term success.
資料ダウンロード
QCD管理受発注クラウド「newji」は、受発注部門で必要なQCD管理全てを備えた、現場特化型兼クラウド型の今世紀最高の受発注管理システムとなります。
ユーザー登録
受発注業務の効率化だけでなく、システムを導入することで、コスト削減や製品・資材のステータス可視化のほか、属人化していた受発注情報の共有化による内部不正防止や統制にも役立ちます。
NEWJI DX
製造業に特化したデジタルトランスフォーメーション(DX)の実現を目指す請負開発型のコンサルティングサービスです。AI、iPaaS、および先端の技術を駆使して、製造プロセスの効率化、業務効率化、チームワーク強化、コスト削減、品質向上を実現します。このサービスは、製造業の課題を深く理解し、それに対する最適なデジタルソリューションを提供することで、企業が持続的な成長とイノベーションを達成できるようサポートします。
製造業ニュース解説
製造業、主に購買・調達部門にお勤めの方々に向けた情報を配信しております。
新任の方やベテランの方、管理職を対象とした幅広いコンテンツをご用意しております。
お問い合わせ
コストダウンが利益に直結する術だと理解していても、なかなか前に進めることができない状況。そんな時は、newjiのコストダウン自動化機能で大きく利益貢献しよう!
(β版非公開)