- お役立ち記事
- The difference between Procurement Cost and Manufacturing Cost
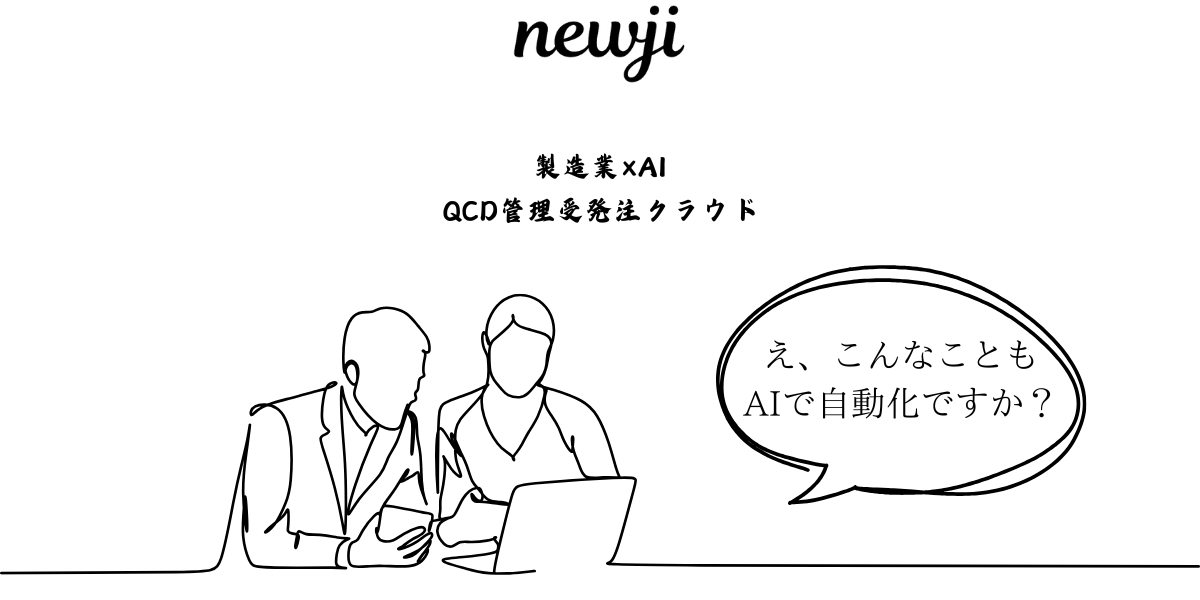
The difference between Procurement Cost and Manufacturing Cost
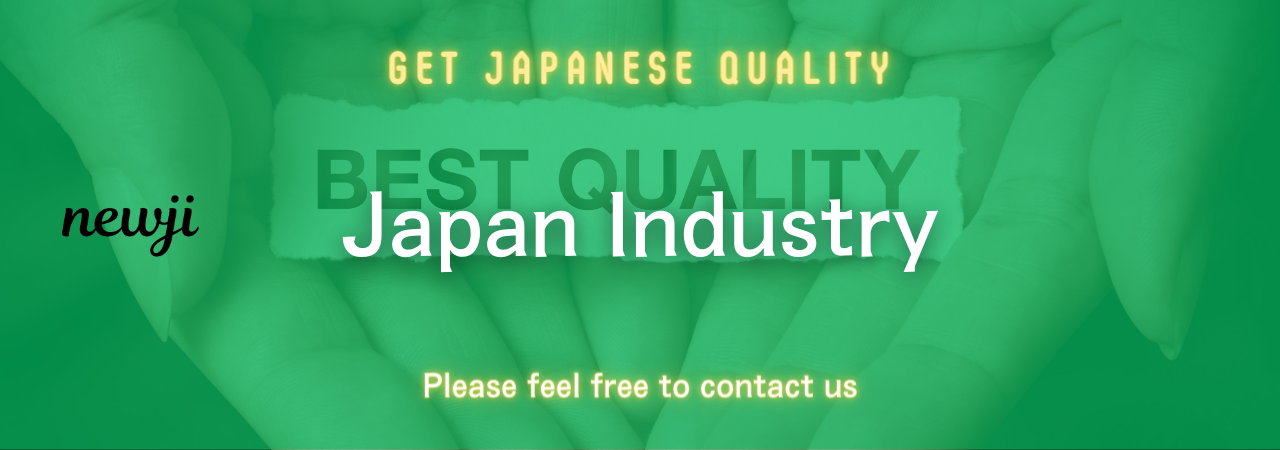
Understanding the difference between procurement cost and manufacturing cost is essential for anyone involved in business, especially in production and supply chain management.
These two types of costs are integral to the overall expenditure of any business, and distinguishing between them helps in better financial planning and pricing strategies.
目次
What is Procurement Cost?
Procurement cost refers to the expenses incurred to acquire raw materials, components, or goods needed for production.
This cost encompasses several elements that go beyond the mere price of the item being purchased.
Components of Procurement Cost
– **Purchase Price:** The amount paid to the supplier for the raw materials or products.
– **Shipping and Handling:** Cost of transporting goods from the supplier’s location to the production facility. This can include fuel, freight charges, and logistics fees.
– **Duties and Taxes:** Any import duties, tariffs, or taxes that need to be paid to bring the items into the country.
– **Inspection and Quality Control:** Expenses linked to assessing the quality of the procured goods. This might involve testing, quality checks, and certifications.
– **Storage:** Costs associated with warehousing and storing the raw materials until they are used in production.
– **Administrative Costs:** Any overheads related to the procurement process such as salaries for procurement staff, IT systems, and software.
What is Manufacturing Cost?
Manufacturing cost refers to the total expenses incurred in the production of goods.
This cost is composed of three main elements: direct materials, direct labor, and manufacturing overhead.
Components of Manufacturing Cost
– **Direct Materials:** Raw materials and components that are directly used in the production of the final product.
– **Direct Labor:** Wages and salaries of all employees who are directly involved in the manufacturing process.
– **Manufacturing Overhead:** Indirect costs related to production. These can include utilities (electricity, water), depreciation of manufacturing equipment, rent for the production facility, and the salaries of supervisory staff.
Contrasting Procurement and Manufacturing Costs
While procurement cost deals primarily with the acquisition of goods and materials, manufacturing cost deals with the transformation of those materials into finished products.
Procurement cost is incurred before the production process begins, whereas manufacturing cost is incurred during the production process.
Why the Distinction Matters
Understanding the difference between procurement cost and manufacturing cost is crucial for efficient budgeting and cost management.
This differentiation helps businesses identify areas where they can cut costs and improve efficiency.
Cost Reduction Opportunities
– **Procurement Cost:** Negotiating better deals with suppliers, optimizing shipping routes, reducing waste during storage, and automating procurement processes to reduce administrative costs.
– **Manufacturing Cost:** Streamlining production processes, investing in technology that enhances productivity, regular maintenance to prevent equipment breakdowns, and efficient labor management.
Pricing Strategies
Knowing both procurement and manufacturing costs helps in setting the right prices for products.
By understanding these costs, businesses can accurately calculate their break-even point and set prices that cover all expenses and generate profit.
Use Cases in Real-World Scenarios
Consider a smartphone manufacturer.
Procurement Cost Example
– The company needs to procure microchips from a supplier in another country.
– The purchase price of microchips, shipping cost from the supplier’s country to the assembly plant, import duties, and quality inspection all constitute the procurement cost.
Manufacturing Cost Example
– Once the microchips and other components are received, they are assembled in the manufacturing plant.
– The cost of the microchips (as direct materials), wages of assembly line workers (direct labor), and facility rent (manufacturing overhead) constitute the manufacturing cost.
Tracking and Managing Costs
Accurate tracking and management of both procurement and manufacturing costs are essential for maintaining profitability.
Maintaining systematic records and employing software tools can help automate these processes, thereby reducing human error and increasing efficiency.
Procurement Cost Management
– Utilize procurement management software to keep track of purchase orders, suppliers, and costs.
– Regularly review and renegotiate supplier contracts to ensure favorable terms.
Manufacturing Cost Management
– Implement Manufacturing Resource Planning (MRP) systems to manage production schedules, inventory, and labor efficiently.
– Conduct regular audits to identify any inefficiencies or areas where costs can be cut.
Conclusion
Distinguishing between procurement cost and manufacturing cost is fundamental for effective financial management in any production-based business.
Each type of cost involves different components and strategies for optimization.
By clearly understanding and tracking these costs, businesses can make informed decisions that contribute to their bottom line and overall efficiency.
資料ダウンロード
QCD調達購買管理クラウド「newji」は、調達購買部門で必要なQCD管理全てを備えた、現場特化型兼クラウド型の今世紀最高の購買管理システムとなります。
ユーザー登録
調達購買業務の効率化だけでなく、システムを導入することで、コスト削減や製品・資材のステータス可視化のほか、属人化していた購買情報の共有化による内部不正防止や統制にも役立ちます。
NEWJI DX
製造業に特化したデジタルトランスフォーメーション(DX)の実現を目指す請負開発型のコンサルティングサービスです。AI、iPaaS、および先端の技術を駆使して、製造プロセスの効率化、業務効率化、チームワーク強化、コスト削減、品質向上を実現します。このサービスは、製造業の課題を深く理解し、それに対する最適なデジタルソリューションを提供することで、企業が持続的な成長とイノベーションを達成できるようサポートします。
オンライン講座
製造業、主に購買・調達部門にお勤めの方々に向けた情報を配信しております。
新任の方やベテランの方、管理職を対象とした幅広いコンテンツをご用意しております。
お問い合わせ
コストダウンが利益に直結する術だと理解していても、なかなか前に進めることができない状況。そんな時は、newjiのコストダウン自動化機能で大きく利益貢献しよう!
(Β版非公開)