- お役立ち記事
- The difference between Production Lead Time and Procurement Lead Time
月間76,176名の
製造業ご担当者様が閲覧しています*
*2025年3月31日現在のGoogle Analyticsのデータより
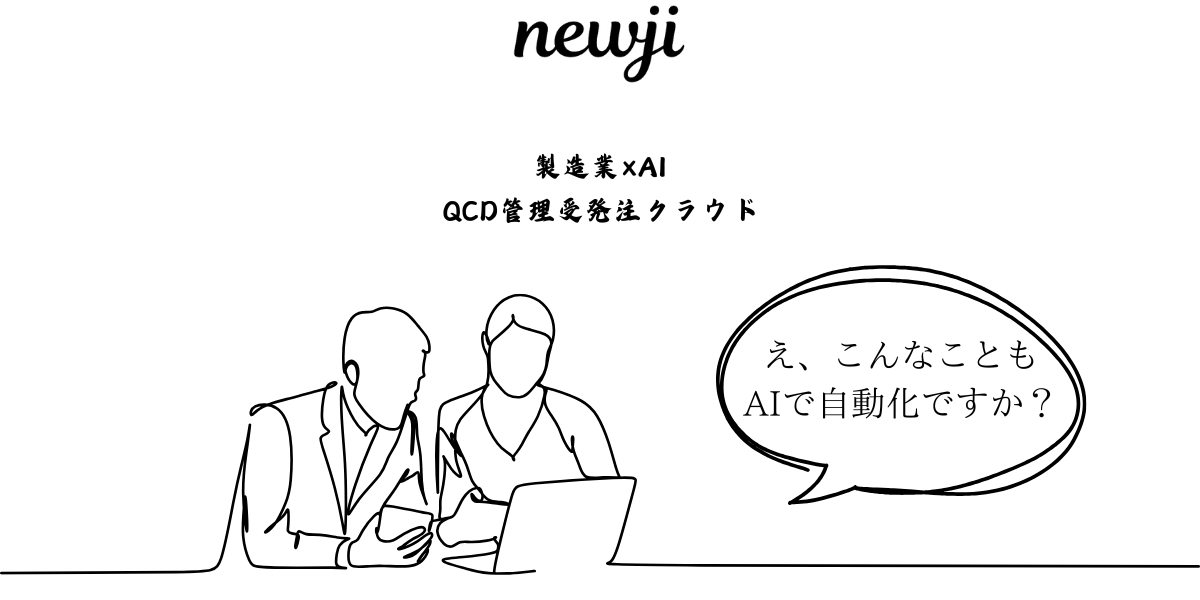
The difference between Production Lead Time and Procurement Lead Time
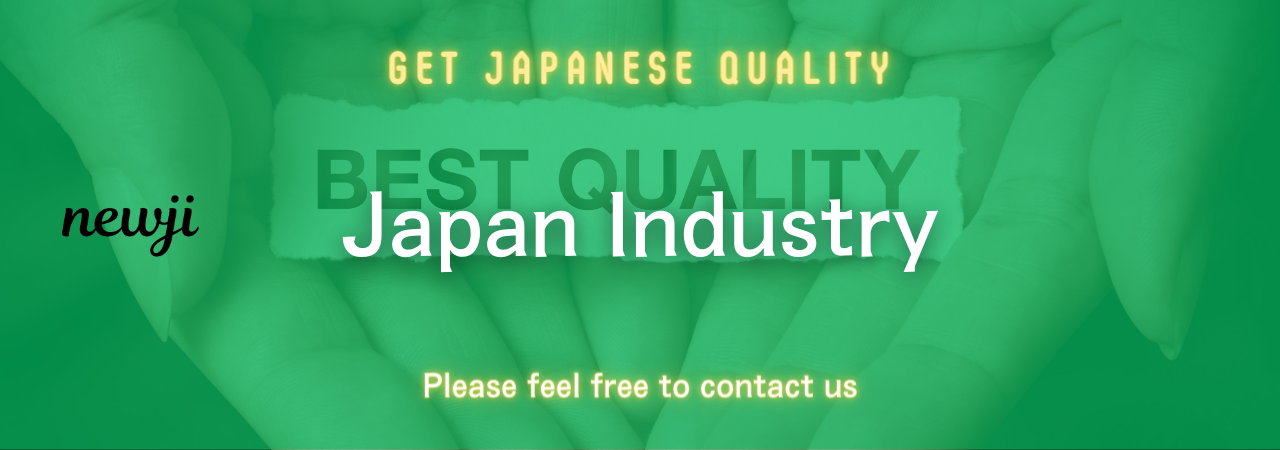
Understanding the differences between production lead time and procurement lead time is important for managing your supply chain effectively.
Both terms relate to the timeline of getting a product from an idea to a completed item ready for customer delivery.
However, they focus on distinct parts of the supply chain process.
In this article, we’ll delve into what each term means, how they differ, and why understanding these differences matters.
目次
What is Production Lead Time?
Production lead time is the period required to manufacture a product, starting from when you receive a customer order to the moment the product is ready to ship.
This timeframe includes many stages, such as obtaining raw materials, actual manufacturing, quality checks, and packaging.
Production lead time can vary greatly depending on the complexity of the product, the efficiency of the manufacturing process, and the availability of resources.
Factors Affecting Production Lead Time
Several factors can influence production lead time.
Firstly, the complexity of the product plays a significant role.
A simple product like a pencil has a shorter lead time than a complex gadget with multiple components.
Secondly, the availability of raw materials can either shorten or lengthen the lead time.
If materials are readily available, production can start immediately.
Otherwise, there can be delays.
Additionally, the efficiency of the manufacturing process is crucial.
Automated and streamlined processes often result in shorter lead times.
Importance of Managing Production Lead Time
Managing production lead time efficiently is crucial for meeting customer expectations and maintaining a competitive edge.
A shorter production lead time enables quicker delivery to customers, improving satisfaction and potentially increasing repeat business.
It also allows you to react more rapidly to market changes or new customer demands.
What is Procurement Lead Time?
Procurement lead time focuses on the period required to acquire the materials or components necessary for production.
It starts when you place an order with a supplier and ends when those materials are delivered to your facility.
Procurement lead time is essential for planning production schedules and ensuring that all needed materials are available when production begins.
Factors Affecting Procurement Lead Time
Several elements impact procurement lead time.
Shipping distance is a significant factor; materials sourced from local suppliers generally arrive faster than those from international vendors.
Supplier reliability also matters—consistent and dependable suppliers can drastically reduce procurement lead times.
Lastly, order quantities can affect lead time.
Larger orders might take longer to fulfill, especially if the supplier needs to produce additional stock.
Importance of Managing Procurement Lead Time
Effective management of procurement lead time can significantly improve the overall efficiency of the supply chain.
A shorter procurement lead time reduces the risk of production delays owing to material shortages.
It also enables better inventory management, reducing the cost associated with holding excessive stock.
Moreover, reliable procurement schedules can improve relationships with suppliers, leading to more favorable terms and conditions.
Key Differences Between Production Lead Time and Procurement Lead Time
While both production and procurement lead times are integral to the supply chain, they focus on different stages and processes.
Production lead time deals with the timeframe to manufacture a product.
On the other hand, procurement lead time concerns the period required to obtain the necessary materials or components for production.
Another critical difference lies in the factors that influence each lead time.
Production lead time is primarily affected by the complexity of the product, the efficiency of the manufacturing process, and the availability of internal resources.
In contrast, procurement lead time is influenced mainly by external factors like supplier reliability, shipping distance, and order quantities.
Furthermore, the management strategies for each lead time differ.
Reducing production lead time often involves streamlining manufacturing processes, improving internal communication, and setting realistic production schedules.
On the other hand, managing procurement lead time effectively requires building strong relationships with suppliers, choosing reliable vendors, and possibly diversifying the supplier base to mitigate risks.
Why Understanding These Differences Matters
Recognizing the distinction between production and procurement lead times is crucial for effective supply chain management.
Misunderstanding these terms can lead to poor planning, resulting in delays, increased costs, and unsatisfied customers.
Understanding production lead time helps you streamline your manufacturing process, ensuring quicker turnaround and higher efficiency.
You can identify bottlenecks, implement process improvements, and set realistic production schedules.
On the other hand, understanding procurement lead time allows you to improve your material acquisition process.
You can build better relationships with suppliers, negotiate more favorable terms, and ensure a steady supply of required materials.
This understanding helps you mitigate the risks of delays in production due to material shortages.
Conclusion
In summary, both production lead time and procurement lead time are essential components of an efficient supply chain.
While they pertain to different stages of the process, both ultimately aim to ensure timely and cost-effective delivery of products to customers.
By understanding and managing these lead times effectively, you can improve your overall operational efficiency, reduce costs, and enhance customer satisfaction.
The key to success lies in recognizing the distinct factors that influence each lead time and adopting tailored strategies to manage them.
資料ダウンロード
QCD管理受発注クラウド「newji」は、受発注部門で必要なQCD管理全てを備えた、現場特化型兼クラウド型の今世紀最高の受発注管理システムとなります。
ユーザー登録
受発注業務の効率化だけでなく、システムを導入することで、コスト削減や製品・資材のステータス可視化のほか、属人化していた受発注情報の共有化による内部不正防止や統制にも役立ちます。
NEWJI DX
製造業に特化したデジタルトランスフォーメーション(DX)の実現を目指す請負開発型のコンサルティングサービスです。AI、iPaaS、および先端の技術を駆使して、製造プロセスの効率化、業務効率化、チームワーク強化、コスト削減、品質向上を実現します。このサービスは、製造業の課題を深く理解し、それに対する最適なデジタルソリューションを提供することで、企業が持続的な成長とイノベーションを達成できるようサポートします。
製造業ニュース解説
製造業、主に購買・調達部門にお勤めの方々に向けた情報を配信しております。
新任の方やベテランの方、管理職を対象とした幅広いコンテンツをご用意しております。
お問い合わせ
コストダウンが利益に直結する術だと理解していても、なかなか前に進めることができない状況。そんな時は、newjiのコストダウン自動化機能で大きく利益貢献しよう!
(β版非公開)