- お役立ち記事
- The difference between Production Management and Quality Management
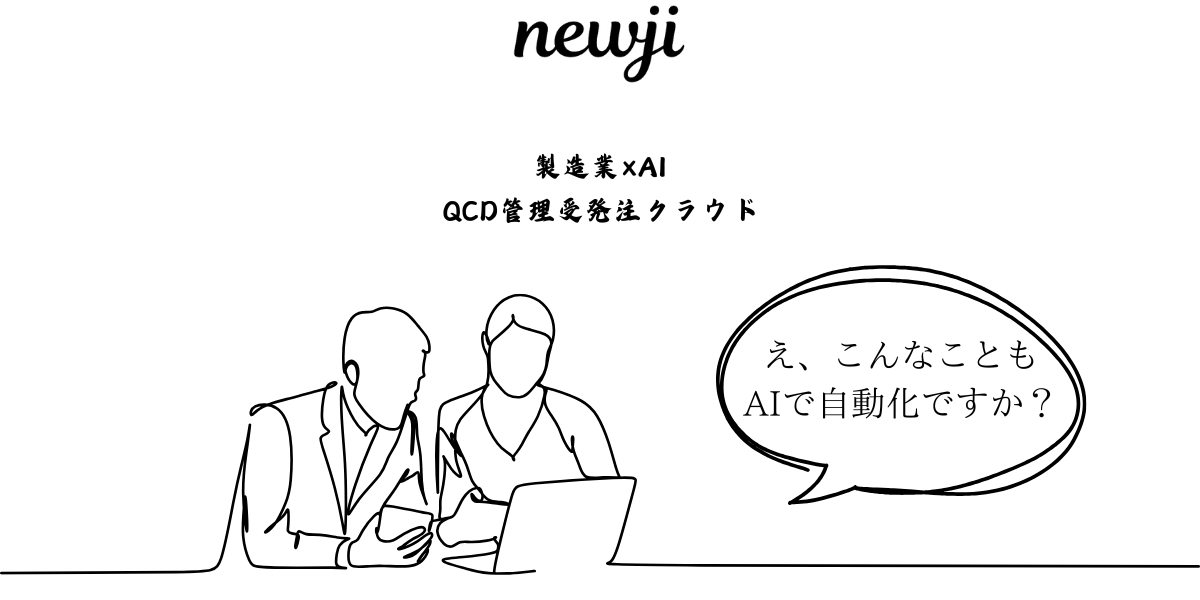
The difference between Production Management and Quality Management
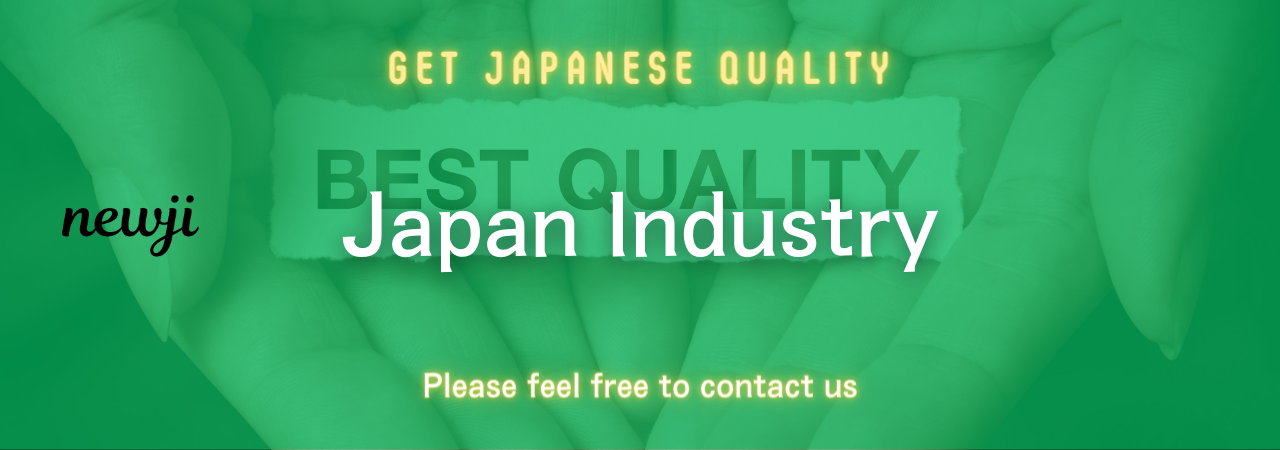
In any manufacturing or service industry, both production management and quality management hold vital roles.
Though they are closely related, they serve distinct purposes and are crucial for the efficient functioning of an organization.
Understanding the difference between production management and quality management can help businesses strike a balance between these two essential aspects.
目次
Understanding Production Management
Production management is primarily concerned with the planning, coordination, and control of the manufacturing process.
It aims to ensure that goods are produced efficiently, at the right cost, and meet the demands of the market.
Key objectives of production management include maximizing output, optimizing resources, reducing production costs, and ensuring timely production.
Planning and Scheduling
One of the primary functions of production management is planning.
This involves designing production processes, estimating costs, and determining the resources required.
Scheduling, on the other hand, ensures that these plans are executed timely.
Effective planning and scheduling help in minimizing production delays and maintaining a steady workflow.
Resource Allocation
Production management also deals with the optimal allocation of resources such as machinery, labor, and raw materials.
Proper resource allocation ensures that production processes run smoothly without any interruptions.
It aims to reduce waste and improve efficiency.
Process Control
Maintaining control over production processes is another key aspect of production management.
Process control involves monitoring production activities to ensure they adhere to planned schedules and quality standards.
It helps in identifying and rectifying any deviations promptly, ensuring a smooth production flow.
Cost Management
An essential part of production management is managing costs effectively.
This includes budgeting, cost estimation, and cost control measures.
The goal is to ensure that production is carried out within budget and unnecessary expenses are minimized.
Understanding Quality Management
Quality management focuses on ensuring that products or services meet certain standards and are consistent in quality.
It’s about maintaining high standards throughout the production process and ensuring consumer satisfaction.
Key components of quality management include quality planning, quality control, quality assurance, and continuous improvement.
Quality Planning
Quality planning involves identifying the standards and specifications that products or services must meet.
This step is crucial for setting clear benchmarks for quality and ensuring consistency.
It involves developing procedures and protocols to achieve desired quality levels.
Quality Control
Quality control is the process of inspecting products or services to ensure they meet the established standards.
It involves routine checks and tests during production to identify and address any defects or issues.
Effective quality control helps in reducing product recalls and customer complaints.
Quality Assurance
Quality assurance focuses on preventing defects by improving production processes and implementing stringent checks.
It’s about building quality into the production process rather than just inspecting the final product.
Quality assurance ensures that processes are followed correctly and consistently to produce high-quality outcomes.
Continuous Improvement
A crucial aspect of quality management is the commitment to continuous improvement.
This involves regularly reviewing and refining processes to enhance quality and efficiency.
It encourages a culture of constant innovation and excellence within the organization.
The Interplay between Production Management and Quality Management
While production management and quality management have distinct roles, their effective interplay is vital for operational success.
Efficient production management aims to produce goods promptly and cost-effectively.
Quality management ensures those goods meet high standards.
Both processes must align to deliver products that satisfy customer needs without compromising on quality or efficiency.
Balancing Efficiency and Quality
Achieving the right balance between efficiency and quality is crucial.
Efficient production has no value if the final product fails to meet quality standards.
Conversely, impeccable quality can lead to high costs and delays if production is not managed effectively.
Businesses must integrate both aspects to achieve optimal results.
Role in Customer Satisfaction
Customer satisfaction depends heavily on both timely delivery and product quality.
Production management ensures that products are available when needed, avoiding stockouts or delays.
Quality management ensures that these products meet or exceed customer expectations.
Together, they play a critical role in maintaining customer loyalty and trust.
Reducing Costs and Waste
Both production management and quality management aim to minimize costs and waste.
Efficient production processes reduce waste of materials and time, while rigorous quality checks prevent faulty products from reaching the market.
By working together, these two functions can significantly enhance overall efficiency and cost-effectiveness.
Enhancing Competitiveness
In a competitive market, the ability to produce high-quality products efficiently gives businesses a competitive edge.
Effective production management ensures agility and responsiveness to market demands.
Quality management builds a reputation for reliability and excellence.
Together, they help businesses stand out and attract more customers.
Conclusion
Understanding the difference between production management and quality management is crucial for any organization aiming for success.
While production management focuses on efficiency, resource optimization, and cost control, quality management ensures that products meet high standards and customer satisfaction.
By balancing these two functions effectively, businesses can achieve operational excellence, reduce costs, and maintain a competitive advantage in the market.
Both aspects are essential for delivering value to customers and achieving long-term success.
資料ダウンロード
QCD調達購買管理クラウド「newji」は、調達購買部門で必要なQCD管理全てを備えた、現場特化型兼クラウド型の今世紀最高の購買管理システムとなります。
ユーザー登録
調達購買業務の効率化だけでなく、システムを導入することで、コスト削減や製品・資材のステータス可視化のほか、属人化していた購買情報の共有化による内部不正防止や統制にも役立ちます。
NEWJI DX
製造業に特化したデジタルトランスフォーメーション(DX)の実現を目指す請負開発型のコンサルティングサービスです。AI、iPaaS、および先端の技術を駆使して、製造プロセスの効率化、業務効率化、チームワーク強化、コスト削減、品質向上を実現します。このサービスは、製造業の課題を深く理解し、それに対する最適なデジタルソリューションを提供することで、企業が持続的な成長とイノベーションを達成できるようサポートします。
オンライン講座
製造業、主に購買・調達部門にお勤めの方々に向けた情報を配信しております。
新任の方やベテランの方、管理職を対象とした幅広いコンテンツをご用意しております。
お問い合わせ
コストダウンが利益に直結する術だと理解していても、なかなか前に進めることができない状況。そんな時は、newjiのコストダウン自動化機能で大きく利益貢献しよう!
(Β版非公開)