- お役立ち記事
- The difference between Productivity and Capacity
月間76,176名の
製造業ご担当者様が閲覧しています*
*2025年3月31日現在のGoogle Analyticsのデータより
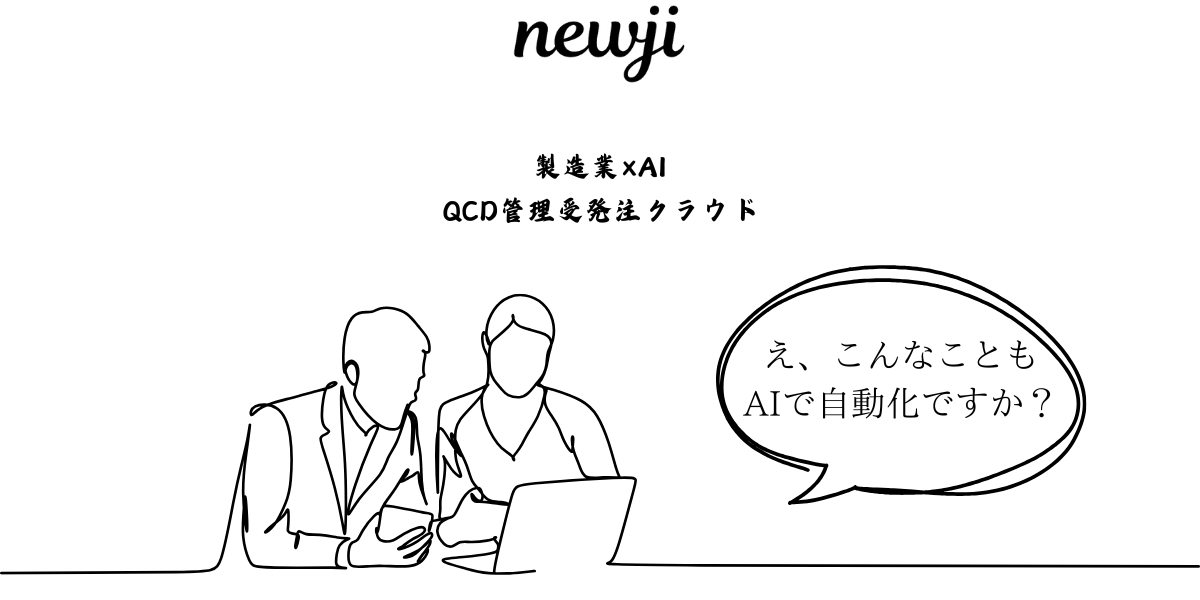
The difference between Productivity and Capacity
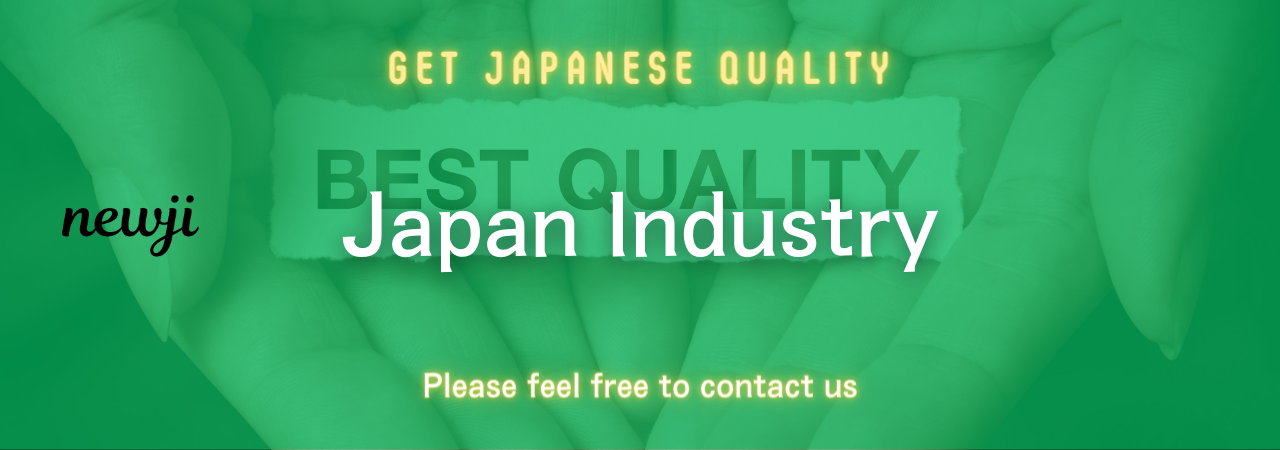
Understanding the difference between productivity and capacity is crucial, whether you’re running a business, managing a project, or just trying to improve your own efficiency.
These terms are often used interchangeably, but they have distinct meanings and implications.
目次
What is Productivity?
Productivity refers to the efficiency with which outputs are produced from inputs.
In simpler terms, it measures how effectively resources like time, money, and labor are utilized to produce goods or services.
A common way to express productivity is through the formula:
Productivity = Output / Input.
For example, if a factory produces 100 widgets using 50 hours of labor, the productivity is 2 widgets per hour.
Higher productivity means you are getting more output for the same or fewer resources, which is beneficial for any business.
What is Capacity?
Capacity, on the other hand, refers to the maximum level of output that can be produced given available resources, under normal business conditions.
It indicates the potential level of productivity, assuming all resources are used efficiently.
Capacity can be measured in various ways, such as the maximum number of products a factory can manufacture in a day or the number of clients a service provider can accommodate in a month.
It’s important to note that capacity is a fixed number in the short term and can only be increased by adding more resources or improving processes in the long term.
Key Differences Between Productivity and Capacity
Focus on Efficiency vs. Potential
Productivity focuses on how efficiently resources are used to produce output.
It looks at the actual performance and aims to optimize it.
Capacity, however, is concerned with the potential maximum output, assuming optimal resource utilization.
Measurable Units
Productivity is usually measured in units that combine both output and input.
For instance, units can be “widgets per hour” or “tasks completed per day.”
Capacity, on the other hand, is measured in absolute terms, such as “100 widgets per day” or “200 clients per month.”
Time Frame
Productivity can fluctuate on a daily or even hourly basis.
Factors like employee motivation, machine breakdowns, or supply chain issues can temporarily affect productivity.
Capacity tends to be a more stable measure in the short term but can change with strategic investments or process improvements in the long term.
Short-term vs. Long-term Perspective
Productivity improvements can often be achieved in the short term by optimizing current processes and resources.
Capacity enhancement usually requires long-term planning, investments in new technologies, or hiring additional staff.
Why Understanding Both Matters
Knowing the difference between productivity and capacity is essential for effective resource management.
Misinterpreting these terms can lead to unrealistic expectations and poor decision-making.
For instance, pushing employees to work harder to improve productivity without considering capacity limitations can lead to burnout and errors.
Resource Allocation
Effective resource allocation requires understanding both productivity and capacity.
If your capacity is maxed out, focusing on productivity improvements can help you get more out of existing resources.
Conversely, if productivity is high but capacity is low, you might need to invest in more resources to meet demand.
Strategic Planning
Businesses can better plan for growth and expansion by knowing their capacity limits.
It helps in setting realistic targets and ensuring that incentive programs are aligned with what is achievable.
Strategic planning also involves recognizing when it’s time to scale up operations to meet increasing demand.
Performance Measurement
Both productivity and capacity are vital metrics for performance evaluation.
Productivity metrics can help identify areas for improvement in daily operations, while capacity metrics can guide long-term strategic decisions.
Improving Productivity and Capacity
Understanding the difference between productivity and capacity is the first step, but improving both requires deliberate actions and investments.
Invest in Training
Well-trained employees are generally more productive.
Investing in training programs can equip your workforce with the skills needed to optimize their tasks, thereby improving productivity.
Upgrade Equipment
Sometimes, outdated machinery or technology can be a bottleneck for both productivity and capacity.
Modernizing your equipment can lead to more efficient production processes and potentially increase your capacity.
Streamline Processes
Eliminating inefficiencies in your workflow can boost productivity.
Techniques like lean manufacturing and Six Sigma can help identify and eliminate waste, thereby improving productivity.
Scale Up Resources
If your business consistently hits capacity limits, it might be time to scale up.
This could involve hiring more staff, expanding facilities, or investing in new technologies.
Monitor and Adjust
Regular monitoring of productivity and capacity metrics can provide valuable insights.
This helps in making informed decisions and adjustments as needed, ensuring that both productivity and capacity are aligned with business goals.
Understanding the difference between productivity and capacity allows you to manage your resources more effectively, thereby improving efficiency and achieving your business objectives.
資料ダウンロード
QCD管理受発注クラウド「newji」は、受発注部門で必要なQCD管理全てを備えた、現場特化型兼クラウド型の今世紀最高の受発注管理システムとなります。
ユーザー登録
受発注業務の効率化だけでなく、システムを導入することで、コスト削減や製品・資材のステータス可視化のほか、属人化していた受発注情報の共有化による内部不正防止や統制にも役立ちます。
NEWJI DX
製造業に特化したデジタルトランスフォーメーション(DX)の実現を目指す請負開発型のコンサルティングサービスです。AI、iPaaS、および先端の技術を駆使して、製造プロセスの効率化、業務効率化、チームワーク強化、コスト削減、品質向上を実現します。このサービスは、製造業の課題を深く理解し、それに対する最適なデジタルソリューションを提供することで、企業が持続的な成長とイノベーションを達成できるようサポートします。
製造業ニュース解説
製造業、主に購買・調達部門にお勤めの方々に向けた情報を配信しております。
新任の方やベテランの方、管理職を対象とした幅広いコンテンツをご用意しております。
お問い合わせ
コストダウンが利益に直結する術だと理解していても、なかなか前に進めることができない状況。そんな時は、newjiのコストダウン自動化機能で大きく利益貢献しよう!
(β版非公開)