- お役立ち記事
- The difference between Punching and Stamping
月間76,176名の
製造業ご担当者様が閲覧しています*
*2025年3月31日現在のGoogle Analyticsのデータより
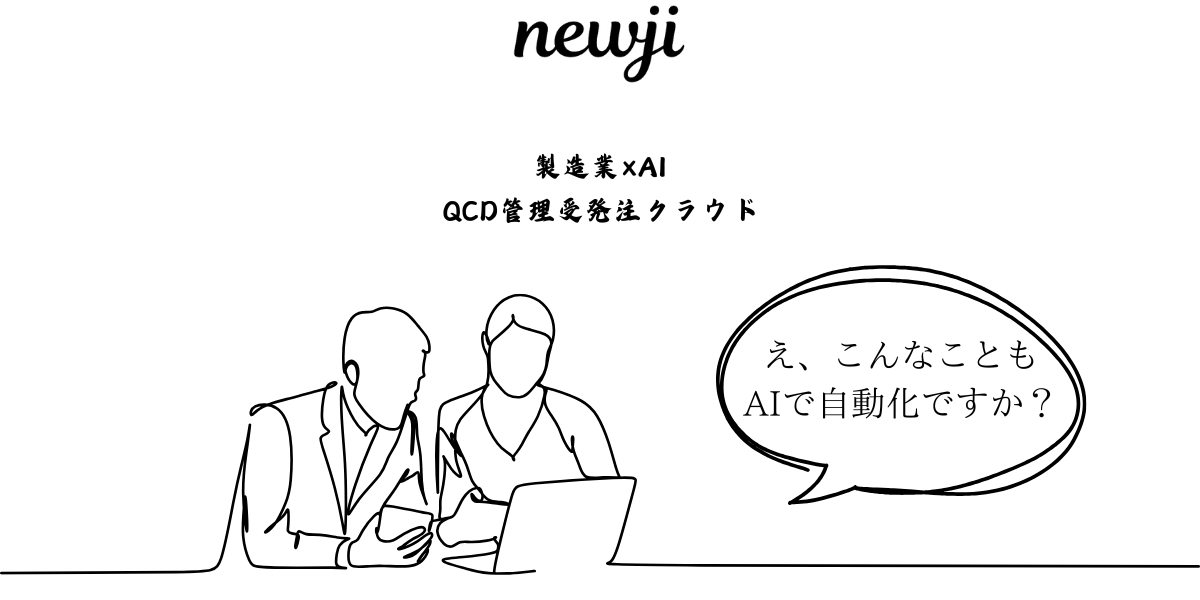
The difference between Punching and Stamping
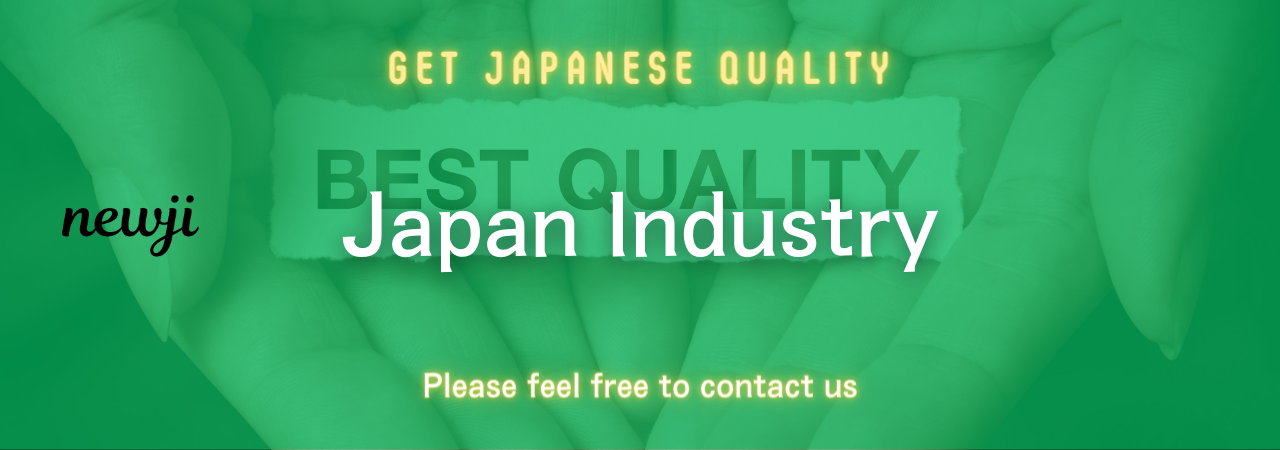
Punching and stamping are common methods used in manufacturing to shape and modify materials, especially metals.
These techniques are highly efficient for producing a wide range of components in various industries, such as automotive, aerospace, electronics, and more.
While both processes may seem similar at first glance, they serve distinct purposes and operate differently.
This article will delve into the differences between punching and stamping, explaining their unique characteristics and applications.
目次
What is Punching?
Punching is a metal forming process where a punch press is used to create holes or shapes in a material by applying a significant amount of force.
The material, usually sheet metal, is positioned on a die with the desired shape.
The punch, a precise tool, then strikes the material to cut out the desired shape, leaving a hole or a specific form.
How Punching Works
The punching process involves several key components: the punch, die, and press.
The punch is the part that moves downward with force to exert pressure on the material.
The die is a tool that sits beneath the material and supports it during the punching action.
When the punch descends, it shears the material against the die, creating a clean, accurate hole or shape.
Types of Punching Processes
There are various types of punching processes, each tailored to different requirements:
– Single-punching: Involves a single strike to create a hole.
– Multiple-punching: Uses multiple strikes to create several holes or shapes at once.
– Blanking: In this process, the punched-out piece is the finished product rather than the remaining sheet.
What is Stamping?
Stamping is another metal forming technique that involves using a press and die to shape or emboss materials into specific designs.
While it shares similarities with punching, the main difference lies in the purpose and method of shaping the material.
Stamping can involve a combination of processes such as bending, coining, embossing, and flanging to achieve the desired form.
How Stamping Works
In the stamping process, sheet metal is placed between a die and a press.
The press then exerts force, pressing the material into the die’s shape.
The material is permanently deformed into the desired shape, which can include intricate designs and complex geometries.
Stamping can be done in progressive stages, with each stage forming part of the final product.
Types of Stamping Processes
Similar to punching, stamping includes various processes to achieve different results:
– Progressive die stamping: Involves multiple dies to carry out successive operations in a single press stroke.
– Transfer die stamping: Moves parts from one station to another, each station performing a different operation.
– Deep drawing: Involves pulling material into the die to create a deep shape, such as a cup or cylinder.
Key Differences Between Punching and Stamping
Primary Purpose
The primary purpose of punching is to create holes or cut-outs in the material.
Stamping, on the other hand, aims to shape or emboss the material into a desired form or design.
While punching is predominantly a cutting process, stamping encompasses various forming techniques.
Material Removal
Punching involves the removal of material to create holes or shapes.
In contrast, stamping often involves deforming the material without necessarily removing any of it.
This distinction is crucial in understanding the applications and outcomes of each process.
Tooling and Equipment
Both punching and stamping use presses and dies, but their tooling and equipment can differ significantly.
Punching typically requires high precision punches and dies, especially for creating intricate holes.
Stamping may involve complex dies with multiple stages and forms to achieve intricate designs.
End Products
The end products of punching are usually simple, featuring holes or cut-outs.
Blanks created from punching may be used in further processing or assembly.
Stamping, however, produces more complex and finished components, often ready for use in their intended applications without additional processing.
Applications of Punching and Stamping
Common Uses of Punching
Punching is widely used in industries where creating holes or shapes quickly and accurately is essential.
Common applications include:
– Fabrication of metal frames and brackets.
– Production of electronic enclosures and housings.
– Creation of ventilation grills and filters.
Common Uses of Stamping
Stamping finds applications in industries that demand intricate shapes and designs.
It’s particularly prevalent in:
– Automotive manufacturing for creating body panels and components.
– Production of household appliances and electronic devices.
– Aerospace industry for crafting specialized parts and assemblies.
Choosing Between Punching and Stamping
When deciding between punching and stamping, several factors should be considered:
– **Design Complexity**: If the design is simple and involves primarily creating holes, punching is more suitable. For intricate shapes and detailed designs, stamping is the better choice.
– **Production Volume**: Both processes are efficient for high-volume production, but stamping is often preferred for large-scale operations due to its versatility and capability to perform multiple steps in one cycle.
– **Material Characteristics**: The type and thickness of the material play a significant role in choosing the appropriate process. Punching works well with a variety of metals and thicknesses, while stamping is better suited for materials that can withstand deformation without cracking.
Conclusion
Understanding the differences between punching and stamping is crucial for selecting the right manufacturing process for your needs.
Punching is ideal for creating holes and simple shapes, while stamping excels in shaping and forming complex designs.
Both processes offer distinct advantages and are integral to modern manufacturing, catering to diverse industries and applications.
By considering the specific requirements of your project, you can determine which method best suits your needs, ensuring efficiency, precision, and high-quality end products.
資料ダウンロード
QCD管理受発注クラウド「newji」は、受発注部門で必要なQCD管理全てを備えた、現場特化型兼クラウド型の今世紀最高の受発注管理システムとなります。
ユーザー登録
受発注業務の効率化だけでなく、システムを導入することで、コスト削減や製品・資材のステータス可視化のほか、属人化していた受発注情報の共有化による内部不正防止や統制にも役立ちます。
NEWJI DX
製造業に特化したデジタルトランスフォーメーション(DX)の実現を目指す請負開発型のコンサルティングサービスです。AI、iPaaS、および先端の技術を駆使して、製造プロセスの効率化、業務効率化、チームワーク強化、コスト削減、品質向上を実現します。このサービスは、製造業の課題を深く理解し、それに対する最適なデジタルソリューションを提供することで、企業が持続的な成長とイノベーションを達成できるようサポートします。
製造業ニュース解説
製造業、主に購買・調達部門にお勤めの方々に向けた情報を配信しております。
新任の方やベテランの方、管理職を対象とした幅広いコンテンツをご用意しております。
お問い合わせ
コストダウンが利益に直結する術だと理解していても、なかなか前に進めることができない状況。そんな時は、newjiのコストダウン自動化機能で大きく利益貢献しよう!
(β版非公開)