- お役立ち記事
- The difference between QC Activities and VE Activities
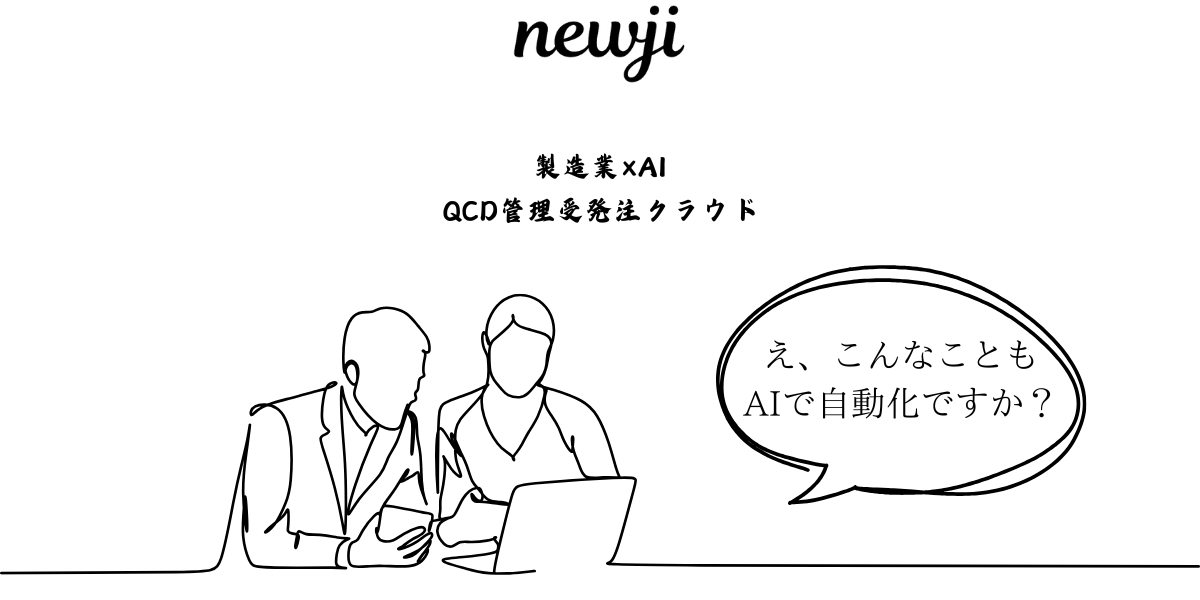
The difference between QC Activities and VE Activities
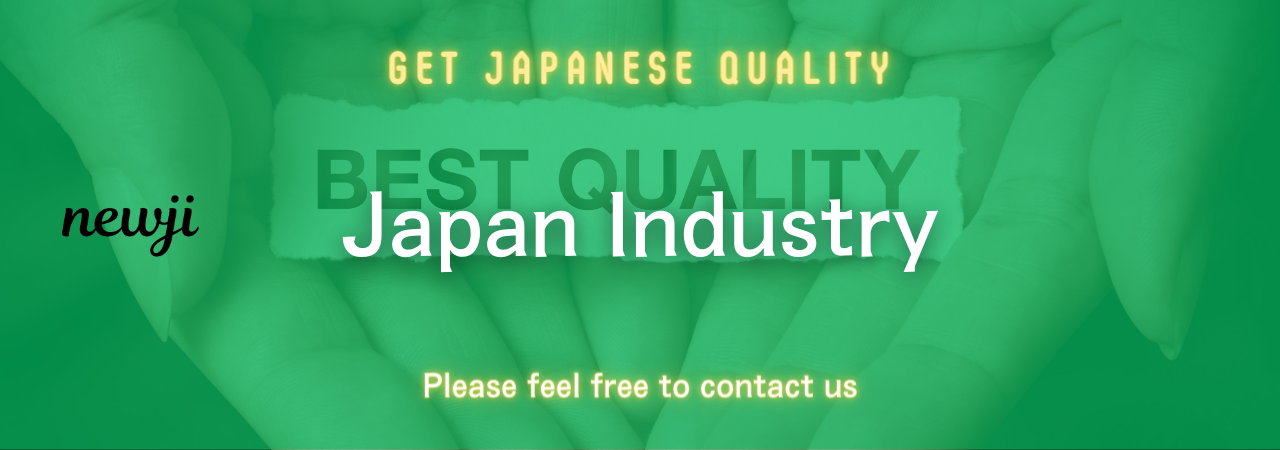
目次
Understanding QC Activities
Quality Control (QC) activities are processes and actions taken to ensure a specific level of quality in a product or service.
The goal is to confirm that the final product meets the required standards and satisfies customer expectations.
QC activities often involve inspections, testing, and various procedures designed to detect and correct defects during production.
What Are QC Activities?
Quality Control can be broken down into several main activities.
First, there is the inspection of raw materials.
By examining materials before they enter the production process, companies can identify defects early.
Next, there is in-process inspection, which involves checking products at different stages of production.
This early detection helps to address issues before they become more significant problems.
Testing is another critical part of QC.
Products are put through various tests to ensure they meet specific criteria.
Examples include durability tests, safety tests, and performance evaluations.
If a product fails any of these tests, it’s either discarded or sent for rework to rectify the issues.
Documentation also plays a vital role in QC activities.
Detailed records of inspections, tests, and corrective actions are kept.
These records help to identify trends and recurring issues, providing valuable data for continuous improvement.
Diving Into VE Activities
Value Engineering (VE) activities focus on improving the value of a product by optimizing its function and reducing costs without compromising quality.
The idea is to achieve the most cost-effective balance between performance, reliability, and safety.
What Are VE Activities?
Value Engineering is a systematic and organized approach.
The process starts with identifying the functions of a product or service.
Each function is then analyzed to determine its value and the cost associated with it.
The next step is brainstorming alternatives.
Teams look for ways to perform the same function at a lower cost or with improved performance.
This often involves thinking outside the box and re-imagining components, materials, and even production methods.
Evaluating and selecting alternatives is crucial in VE activities.
Potential solutions are assessed based on numerous factors such as cost, feasibility, and impact on quality.
The best alternatives are implemented, resulting in better value for both the manufacturer and the consumer.
Documentation is also essential in VE, similar to QC activities.
Every step of the value engineering process is meticulously documented to ensure that improvements are systematic, reproducible, and aligned with overall objectives.
Key Differences Between QC and VE Activities
Primary Focus
Firstly, the primary focus of QC activities is on maintaining a specific quality level.
QC aims to detect and rectify defects to ensure products meet predetermined standards.
In contrast, VE focuses on maximizing value.
This might involve reducing costs, improving performance, or optimizing functionality.
Approach and Methods
QC activities are often reactive.
Inspections and tests are generally conducted after specific production stages to identify defects.
The approach is to correct any issues found before the product reaches the customer.
On the other hand, VE activities are more proactive.
The aim is to improve the design and manufacturing process to avoid potential issues altogether.
Instead of merely correcting defects, VE looks for ways to enhance the product’s overall value.
Impact on Costs
While QC activities can indirectly affect costs by reducing the number of defective products and returns, their primary goal is not cost reduction.
They focus more on ensuring quality.
VE activities, however, have a direct impact on costs.
One of the main goals of VE is to find cost-effective ways to achieve the desired product performance and functionality without compromising quality.
How QC and VE Complement Each Other
Although QC and VE activities have different focuses and approaches, they complement each other well.
Together, they create a comprehensive strategy for maximizing product quality and value.
QC activities help maintain a high standard of product quality, ensuring that customers receive reliable and defect-free products.
By identifying defects early in the process, QC ensures that potential problems are addressed promptly, thus maintaining overall product quality.
VE activities, on the other hand, contribute to continuous improvement.
By optimizing function and reducing costs, VE helps companies remain competitive and innovative.
The cost savings achieved through VE can be reinvested into quality control measures, further enhancing the product’s value and quality.
Applying QC and VE in Different Industries
Different industries may emphasize QC or VE activities more, depending on their specific requirements.
Manufacturing
In manufacturing, both QC and VE activities are critical.
QC ensures that the products meet specified standards, while VE helps optimize manufacturing processes to reduce costs and improve efficiency.
Healthcare
In the healthcare industry, QC activities focus on ensuring that medical devices, pharmaceuticals, and procedures are safe and effective.
VE activities might involve finding more cost-effective treatments or optimizing hospital workflows to improve patient care.
Construction
In construction, QC activities can include site inspections and material quality checks.
VE activities involve designing buildings in ways that meet safety standards while reducing costs and enhancing functionality.
Conclusion
Quality Control and Value Engineering are both vital aspects of maintaining and improving product quality.
While QC focuses on identifying and correcting defects, VE looks at optimizing functionality and reducing costs.
By understanding the differences and leveraging both approaches, companies can significantly enhance their products’ quality and value, ultimately benefiting the customer and the organization alike.
資料ダウンロード
QCD調達購買管理クラウド「newji」は、調達購買部門で必要なQCD管理全てを備えた、現場特化型兼クラウド型の今世紀最高の購買管理システムとなります。
ユーザー登録
調達購買業務の効率化だけでなく、システムを導入することで、コスト削減や製品・資材のステータス可視化のほか、属人化していた購買情報の共有化による内部不正防止や統制にも役立ちます。
NEWJI DX
製造業に特化したデジタルトランスフォーメーション(DX)の実現を目指す請負開発型のコンサルティングサービスです。AI、iPaaS、および先端の技術を駆使して、製造プロセスの効率化、業務効率化、チームワーク強化、コスト削減、品質向上を実現します。このサービスは、製造業の課題を深く理解し、それに対する最適なデジタルソリューションを提供することで、企業が持続的な成長とイノベーションを達成できるようサポートします。
オンライン講座
製造業、主に購買・調達部門にお勤めの方々に向けた情報を配信しております。
新任の方やベテランの方、管理職を対象とした幅広いコンテンツをご用意しております。
お問い合わせ
コストダウンが利益に直結する術だと理解していても、なかなか前に進めることができない状況。そんな時は、newjiのコストダウン自動化機能で大きく利益貢献しよう!
(Β版非公開)