- お役立ち記事
- The difference between QC Circle and Value Engineering (VE) Activities
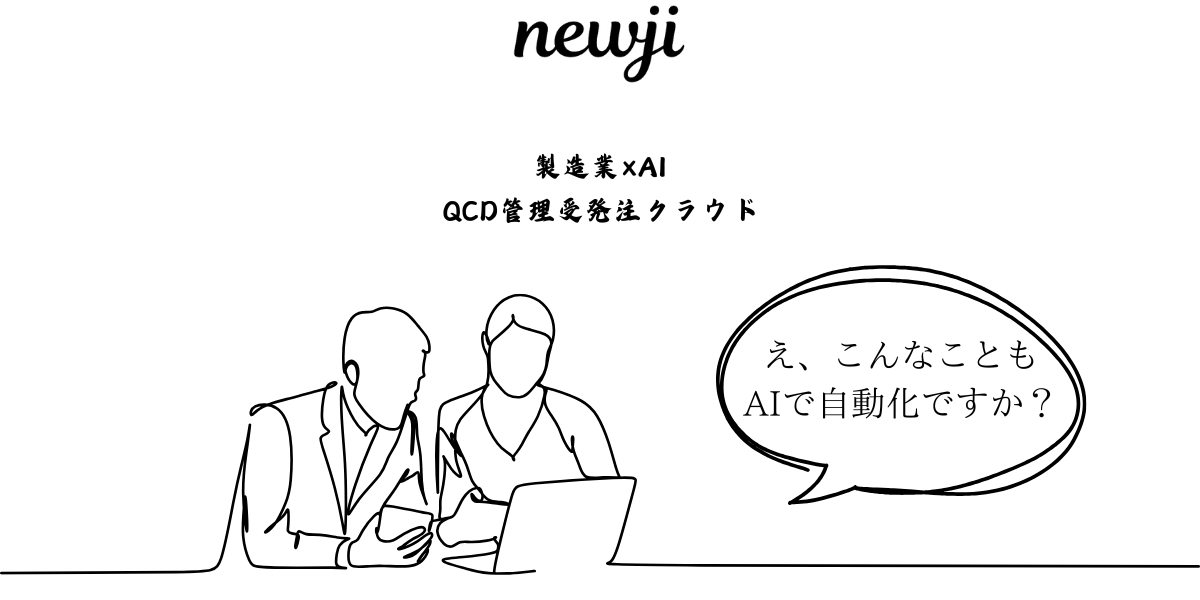
The difference between QC Circle and Value Engineering (VE) Activities
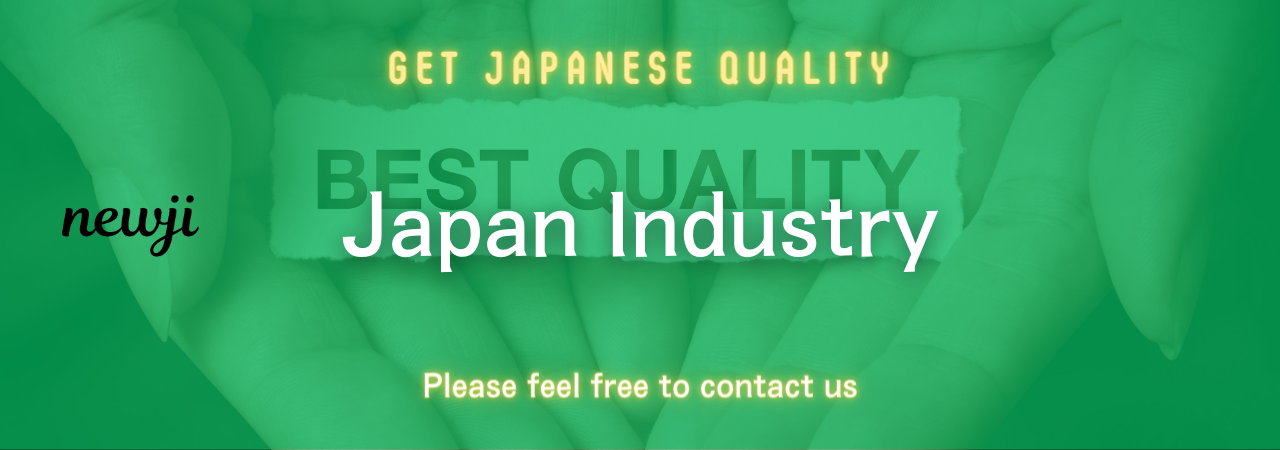
When working in manufacturing or other industries, it’s common to hear about QC Circle and Value Engineering (VE) activities.
Both concepts focus on improving processes and outcomes, but they do it in different ways.
Understanding the differences between QC Circle and VE activities can help you apply the right approach to your work.
目次
What is a QC Circle?
A QC Circle is a small group of workers who voluntarily come together to address quality control issues in their workplace.
QC stands for Quality Control.
The group’s main purpose is to identify, analyze, and solve problems related to their specific work area.
Because the members are directly involved in the work, they often have valuable insights into potential issues.
History of QC Circles
The concept originated in Japan during the 1960s.
It was part of the broader Total Quality Control (TQC) movement aimed at improving quality and efficiency across industries.
Initially, manufacturing companies embraced QC Circles, but the idea eventually spread to various sectors, including healthcare and education.
How QC Circles Work
A QC Circle follows a structured approach to problem-solving, often using a cycle known as PDCA (Plan-Do-Check-Act).
1. Plan: Identify the problem and develop a plan to address it.
2. Do: Implement the plan on a small scale to test its effectiveness.
3. Check: Evaluate the results to determine if the plan worked.
4. Act: If successful, implement the solution on a larger scale; if not, revise the plan and repeat the cycle.
Benefits of QC Circles
QC Circles offer several benefits to organizations, including:
– Improved product quality
– Enhanced employee engagement and morale
– Better teamwork and communication
– Increased efficiency and productivity
– Quick identification and resolution of issues
What is Value Engineering (VE)?
Value Engineering (VE) is a systematic method to improve the “value” of goods or products by using an examination of function.
Value, as defined in VE, is the ratio of function to cost.
It aims to maximize function while minimizing cost.
VE is commonly applied during the design and development stages of a product but can also be used in various phases of a project.
History of Value Engineering
The concept of Value Engineering was developed during World War II by Lawrence Miles, an engineer working for General Electric.
Due to material shortages, Miles and his team needed to find ways to maintain product quality while reducing costs.
This led to the development of “value analysis,” which later evolved into what we know today as Value Engineering.
How Value Engineering Works
Value Engineering follows a specific set of steps to achieve its goals.
1. Information: Gather all relevant information about the project or product.
2. Function Analysis: Determine the primary and secondary functions of the project or product.
3. Creative Phase: Brainstorm ideas to enhance functions or reduce costs.
4. Evaluation Phase: Assess the feasibility of the ideas generated.
5. Development Phase: Develop the best ideas into actionable plans.
6. Presentation: Present the final plan to the stakeholders for approval.
Benefits of Value Engineering
The application of Value Engineering can lead to several positive outcomes:
– Reduced costs without compromising quality
– Improved product functionality
– Enhanced project performance
– Greater innovation and creative problem-solving
– Increased customer satisfaction
Key Differences Between QC Circle and Value Engineering
While both QC Circle and VE focus on improvement, they differ in several key aspects.
Focus Areas
QC Circles focus mainly on quality control issues within a specific work area.
The aim is to identify and solve immediate problems affecting the quality of work or products.
On the other hand, Value Engineering has a broader focus that includes improving product functionality and reducing costs.
VE is generally more strategic, often applied in the design and development stages.
Approach and Methodology
QC Circles use a problem-solving approach known as PDCA (Plan-Do-Check-Act).
This method helps teams to identify and resolve issues in a systematic way.
VE, however, follows a more detailed, multi-step process that includes function analysis and creative brainstorming to find cost-effective solutions.
Scope of Application
QC Circles are usually limited to small groups within a specific work area or department.
They focus on localized problems that team members can directly influence.
VE, however, is often applied at a higher organizational level and can affect various aspects of a project or product, from design to production.
Participant Involvement
Participants in QC Circles are typically workers who are directly involved in the work processes being examined.
Their hands-on experience gives them unique insights into the issues at hand.
Participants in VE activities are often a mix of engineers, designers, managers, and other stakeholders.
This approach ensures that multiple perspectives are considered in the decision-making process.
Outcomes
The outcomes of QC Circles are usually immediate and tangible, such as improved quality or efficiency in a specific work area.
The results of VE, however, may take longer to materialize but often have a more significant impact on overall project cost and functionality.
When to Use QC Circle and When to Use Value Engineering
Choosing between QC Circle and Value Engineering depends on your specific needs and goals.
When to Use QC Circle
– When dealing with immediate quality control issues
– When aiming to engage employees in problem-solving
– When focusing on specific work areas or departments
– When quick results are needed
When to Use Value Engineering
– When looking to reduce costs while enhancing functionality
– When working on product design or development
– When needing a comprehensive analysis of functions and costs
– When seeking long-term improvements and innovations
Understanding the differences between QC Circle and Value Engineering activities can help you choose the right methodology for your needs.
Both have their unique strengths and applications, and knowing when and how to use them can lead to significant improvements in quality, efficiency, and cost-effectiveness.
資料ダウンロード
QCD調達購買管理クラウド「newji」は、調達購買部門で必要なQCD管理全てを備えた、現場特化型兼クラウド型の今世紀最高の購買管理システムとなります。
ユーザー登録
調達購買業務の効率化だけでなく、システムを導入することで、コスト削減や製品・資材のステータス可視化のほか、属人化していた購買情報の共有化による内部不正防止や統制にも役立ちます。
NEWJI DX
製造業に特化したデジタルトランスフォーメーション(DX)の実現を目指す請負開発型のコンサルティングサービスです。AI、iPaaS、および先端の技術を駆使して、製造プロセスの効率化、業務効率化、チームワーク強化、コスト削減、品質向上を実現します。このサービスは、製造業の課題を深く理解し、それに対する最適なデジタルソリューションを提供することで、企業が持続的な成長とイノベーションを達成できるようサポートします。
オンライン講座
製造業、主に購買・調達部門にお勤めの方々に向けた情報を配信しております。
新任の方やベテランの方、管理職を対象とした幅広いコンテンツをご用意しております。
お問い合わせ
コストダウンが利益に直結する術だと理解していても、なかなか前に進めることができない状況。そんな時は、newjiのコストダウン自動化機能で大きく利益貢献しよう!
(Β版非公開)