- お役立ち記事
- The difference between Quality Analysis and Quality Diagnosis
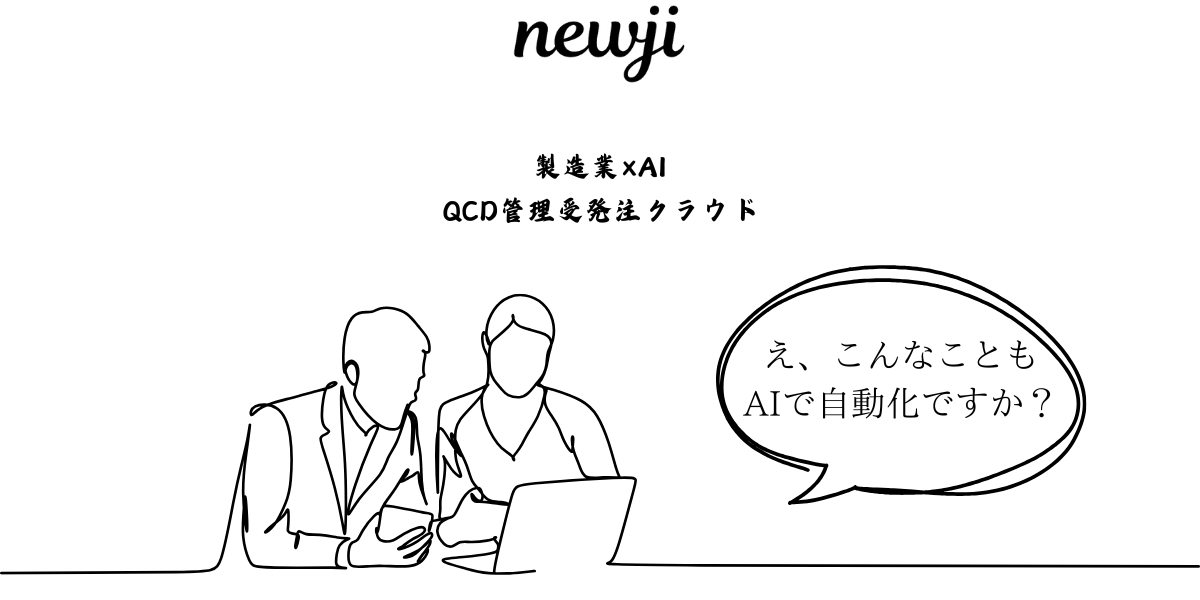
The difference between Quality Analysis and Quality Diagnosis
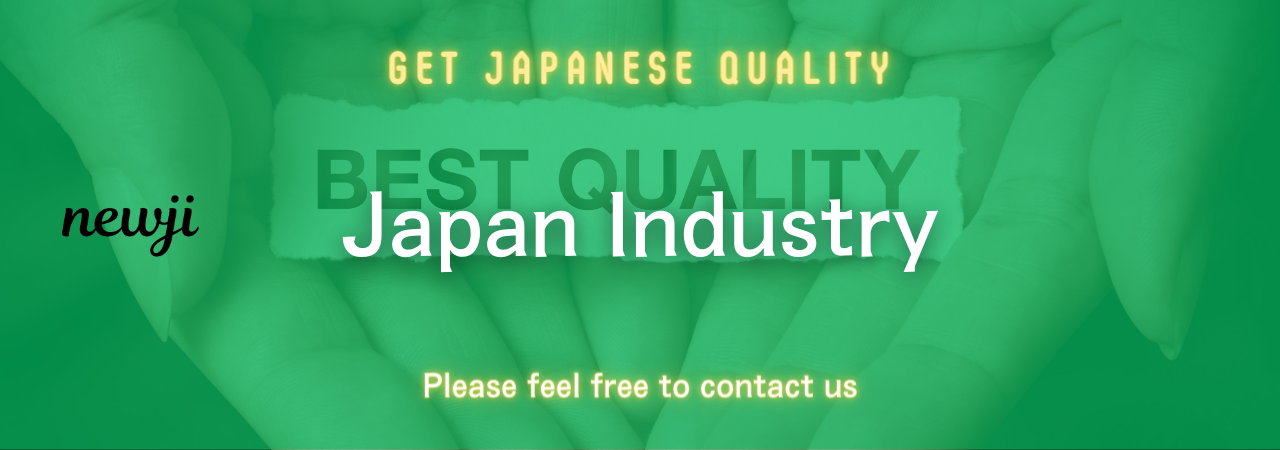
目次
Understanding Quality Analysis
Quality analysis is a process used by businesses and organizations to measure the standard of their products or services.
It involves collecting data through various methods to understand how well a product performs.
This process often includes testing different aspects of a product, like its durability, functionality, and appearance.
One common way to perform quality analysis is through inspections.
During an inspection, a product is carefully examined to ensure it meets the required standards.
For example, in a car manufacturing plant, cars may be inspected to make sure they run smoothly and are safe to drive.
Another method is statistical analysis, where data is collected and analyzed to identify trends and patterns.
This helps businesses understand the performance of their products over time.
For instance, if a company notices a high number of customer complaints about a particular feature of their product, they can use this data to make improvements.
Why is Quality Analysis Important?
Quality analysis is crucial for several reasons.
First, it helps ensure customer satisfaction.
When products consistently meet high standards, customers are more likely to be happy with their purchase.
Second, quality analysis helps identify problems early.
By catching issues before products reach customers, businesses can save time and money on potential recalls or repairs.
Finally, maintaining high-quality standards can give businesses a competitive edge.
When customers know they can rely on a company’s products, they are more likely to remain loyal.
Exploring Quality Diagnosis
Quality diagnosis, on the other hand, focuses on identifying and addressing the root causes of quality issues.
While quality analysis measures and monitors product performance, quality diagnosis digs deeper to understand why problems occur.
This process often involves a systematic approach to problem-solving.
For example, if a company finds that their products are frequently breaking down, they might use quality diagnosis to investigate the issue.
This could involve examining the production process, the materials used, or even the design of the product.
Quality diagnosis often uses tools like root cause analysis (RCA), which involves identifying the main cause of a problem and finding ways to fix it.
Other methods include using fishbone diagrams, which help visualize the potential causes of a problem, and the “5 Whys” technique, which involves asking “why” multiple times to get to the heart of an issue.
The Importance of Quality Diagnosis
Like quality analysis, quality diagnosis is essential for maintaining high standards.
By understanding the root causes of problems, businesses can take steps to prevent them from happening again.
This not only improves product quality but also increases efficiency by streamlining processes and reducing waste.
Quality diagnosis also fosters continuous improvement.
By regularly diagnosing issues and implementing solutions, businesses can continuously enhance their product offerings and stay ahead of competitors.
Key Differences Between Quality Analysis and Quality Diagnosis
While both quality analysis and quality diagnosis aim to ensure high-quality products, they have distinct differences.
Focus and Approach
Quality analysis is primarily concerned with measuring and monitoring product performance.
It involves collecting data, conducting tests, and analyzing trends to ensure products meet certain standards.
On the other hand, quality diagnosis focuses on identifying the underlying causes of quality issues.
It uses problem-solving techniques to understand why problems occur and how to fix them.
Timing
Quality analysis is often an ongoing process.
Businesses continuously perform quality analysis to maintain high standards and monitor product performance over time.
Quality diagnosis, however, is usually conducted when a specific problem is identified.
Once a quality issue is detected, businesses use diagnostic methods to investigate and resolve the problem.
Techniques and Tools
Different techniques and tools are used in each process.
Quality analysis relies on methods like inspections, statistical analysis, and performance testing.
In contrast, quality diagnosis uses tools like root cause analysis, fishbone diagrams, and the “5 Whys” technique to pinpoint and address problems.
When to Use Each Method
Understanding when to use quality analysis versus quality diagnosis is crucial for effective quality management.
Use Quality Analysis When…
– You need to monitor and measure product performance regularly.
– Ensuring products meet certain standards is a priority.
– You want to track trends and identify areas for improvement over time.
Use Quality Diagnosis When…
– A specific quality issue has been identified.
– Understanding the root cause of a problem is necessary.
– Implementing solutions to prevent recurring issues is essential.
Integrating Both Methods for Better Quality Management
To achieve the highest quality standards, businesses should integrate both quality analysis and quality diagnosis.
Quality analysis helps monitor product performance and ensures standards are consistently met.
When an issue is discovered, quality diagnosis can be used to find and address the root cause, preventing future problems.
By combining these methods, businesses can maintain high-quality standards, improve customer satisfaction, and stay competitive in their industry.
Practical Example
Imagine a smartphone manufacturer.
They use quality analysis to test each phone for functionality, battery life, and durability before it reaches the market.
If they notice an increase in battery-related complaints, they use quality diagnosis to investigate.
This might involve examining the battery manufacturing process, testing different batches, or even redesigning certain components.
By addressing the root cause, they not only fix the issue but also improve the overall product quality.
In conclusion, while quality analysis and quality diagnosis serve different purposes, they are both essential for effective quality management.
By understanding and using these methods appropriately, businesses can ensure their products are of the highest quality, leading to greater customer satisfaction and success.
資料ダウンロード
QCD調達購買管理クラウド「newji」は、調達購買部門で必要なQCD管理全てを備えた、現場特化型兼クラウド型の今世紀最高の購買管理システムとなります。
ユーザー登録
調達購買業務の効率化だけでなく、システムを導入することで、コスト削減や製品・資材のステータス可視化のほか、属人化していた購買情報の共有化による内部不正防止や統制にも役立ちます。
NEWJI DX
製造業に特化したデジタルトランスフォーメーション(DX)の実現を目指す請負開発型のコンサルティングサービスです。AI、iPaaS、および先端の技術を駆使して、製造プロセスの効率化、業務効率化、チームワーク強化、コスト削減、品質向上を実現します。このサービスは、製造業の課題を深く理解し、それに対する最適なデジタルソリューションを提供することで、企業が持続的な成長とイノベーションを達成できるようサポートします。
オンライン講座
製造業、主に購買・調達部門にお勤めの方々に向けた情報を配信しております。
新任の方やベテランの方、管理職を対象とした幅広いコンテンツをご用意しております。
お問い合わせ
コストダウンが利益に直結する術だと理解していても、なかなか前に進めることができない状況。そんな時は、newjiのコストダウン自動化機能で大きく利益貢献しよう!
(Β版非公開)