- お役立ち記事
- The difference between Quality Assurance and Reliability Assurance
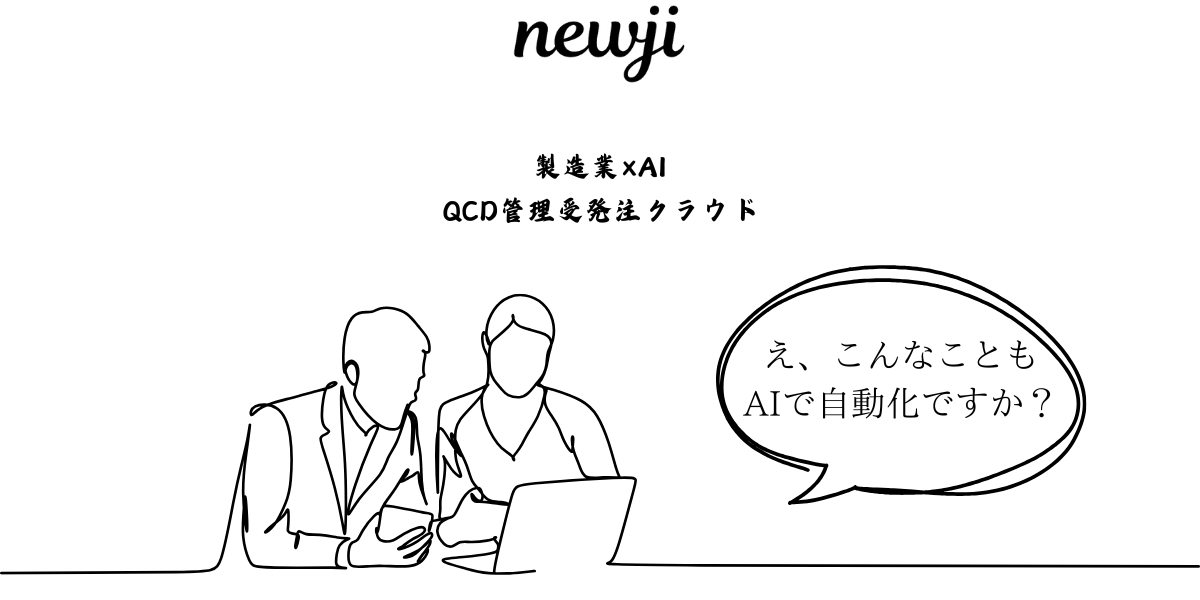
The difference between Quality Assurance and Reliability Assurance
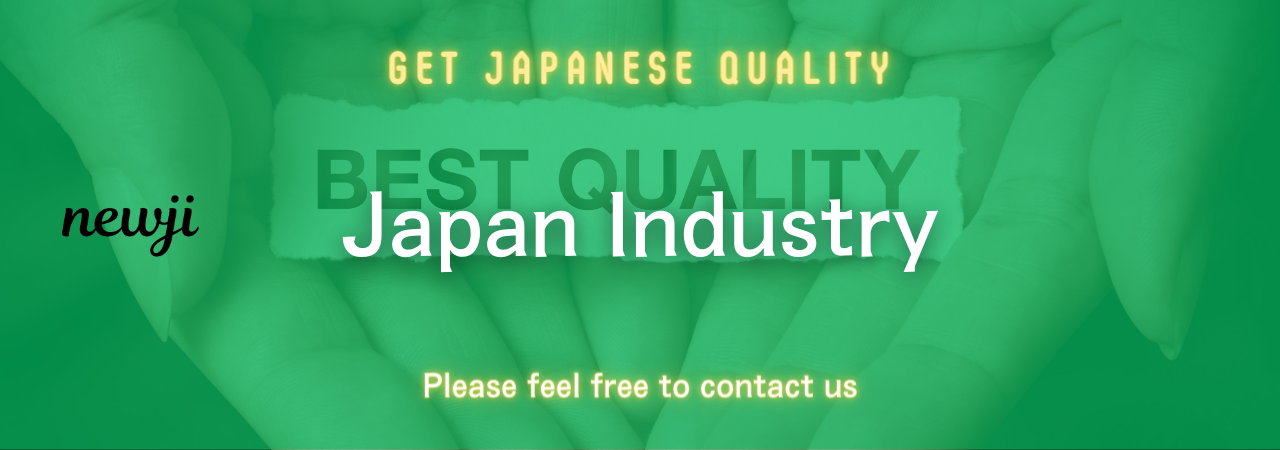
Understanding the distinction between Quality Assurance (QA) and Reliability Assurance (RA) can be crucial for businesses aiming to deliver top-notch products and services.
These terms are often used interchangeably, but they represent different aspects of product development and maintenance.
Let’s dive into what sets these two concepts apart and how they work together to ensure product excellence.
目次
What is Quality Assurance?
Quality Assurance is a systematic process designed to ensure that products and services meet specified requirements.
It focuses on the procedures and activities that provide confidence in a product’s quality.
QA involves planning, fulfilling, and monitoring activities to ensure the product is designed and produced correctly.
Key Components of Quality Assurance
To understand QA fully, let’s consider some of its key components:
1. **Process Control**: QA emphasizes monitoring and controlling the processes involved in production.
It includes defining standards, methods, and procedures to maintain quality throughout production.
2. **Preventive Actions**: Unlike quality control, which identifies defects in finished products, QA takes preventive measures to avoid defects.
It ensures potential issues are addressed before they become problems.
3. **Continuous Improvement**: QA involves continuous evaluation and improvement of processes.
It includes regularly updating standards and procedures based on feedback and performance metrics.
4. **Compliance and Standards**: QA ensures that products comply with industry standards and regulations.
Adherence to these standards guarantees that products are safe, reliable, and of high quality.
What is Reliability Assurance?
Reliability Assurance focuses on the ability of a product to perform consistently over its expected lifespan.
It involves activities aimed at ensuring a product or system performs its intended function without failure under specified conditions.
Key Components of Reliability Assurance
Let’s explore some essential aspects of RA:
1. **Reliability Testing**: RA includes various tests to measure how long a product can perform without failure.
These tests can involve stress testing, life testing, and environmental testing.
2. **Failure Analysis**: When failures occur, RA involves analyzing the reasons behind them to prevent recurrence.
It ensures that the root cause of failure is identified and addressed.
3. **Reliability Predictions**: RA employs statistical models to predict the likelihood of failures over time.
It helps in forecasting the product’s lifespan and identifying potential risks.
4. **Maintenance and Support**: RA involves planning maintenance schedules and providing support to maintain product reliability.
It ensures that the product remains functional throughout its expected lifespan.
Differences Between Quality Assurance and Reliability Assurance
While QA and RA share the common goal of enhancing product excellence, there are distinct differences between them:
Focus and Scope
– **Quality Assurance**: QA focuses on the processes and procedures that ensure a product meets quality standards.
It is oriented towards preventing defects through process control and improvement.
– **Reliability Assurance**: RA focuses on the product’s performance and longevity.
It aims to ensure that the product continues to function correctly over time and under various conditions.
Time Frame
– **Quality Assurance**: QA activities are carried out throughout the development and production process.
It is an ongoing effort to maintain quality standards.
– **Reliability Assurance**: RA is concerned with the product’s performance after it has been developed and released.
It covers the entire lifecycle of the product, focusing on long-term reliability.
Methods and Techniques
– **Quality Assurance**: QA employs methods like process audits, quality planning, and preventive actions.
It also utilizes tools like checklists and standard operating procedures.
– **Reliability Assurance**: RA uses techniques such as reliability testing, failure analysis, and reliability predictions.
It often involves statistical methods to predict and improve product reliability.
How Do QA and RA Work Together?
Although QA and RA have different primary focuses, they complement each other to ensure overall product excellence.
Here’s how they integrate:
Holistic View of Product Quality
QA ensures that the product development process is robust and that the initial quality levels are high.
RA, on the other hand, ensures that this quality is sustained over time by focusing on the product’s reliability.
Together, they provide a comprehensive approach to quality from the initial stages to the end of the product’s lifecycle.
Feedback Loop
QA and RA create a feedback loop where information from reliability testing and maintenance can inform future quality assurance activities.
For instance, if a reliability test reveals a recurring issue, QA can adjust processes and standards to prevent this issue in future products.
Risk Management
Both QA and RA contribute to risk management.
QA minimizes the risk of initial defects, while RA manages the risk of product failure over time.
By addressing different types of risks, they enhance the overall reliability and safety of the product.
Implementing QA and RA in Your Organization
For businesses looking to excel in both quality and reliability, integrating QA and RA practices is essential.
Here are some steps to effectively implement these practices:
Develop a Comprehensive QA Plan
Create a detailed QA plan that outlines standards, procedures, and preventive actions.
Ensure that every stage of the development process includes QA activities to maintain high quality.
Conduct Regular Reliability Testing
Regularly test your products under various conditions to assess their reliability.
Use the data collected from these tests to predict potential failures and address them proactively.
Train Your Team
Ensure that your team is well-trained in both QA and RA practices.
Provide ongoing training and resources to keep them updated on best practices and industry standards.
Establish a Feedback System
Set up a feedback system that allows information from reliability assessments to be fed back into QA processes.
Continuous feedback and improvement ensure that both quality and reliability are maintained.
In conclusion, both Quality Assurance and Reliability Assurance are vital for delivering superior products and services.
While QA focuses on preventing defects during development and production, RA ensures that products perform reliably over time.
By integrating both practices, organizations can achieve a balanced approach that guarantees high-quality, durable, and dependable products.
資料ダウンロード
QCD調達購買管理クラウド「newji」は、調達購買部門で必要なQCD管理全てを備えた、現場特化型兼クラウド型の今世紀最高の購買管理システムとなります。
ユーザー登録
調達購買業務の効率化だけでなく、システムを導入することで、コスト削減や製品・資材のステータス可視化のほか、属人化していた購買情報の共有化による内部不正防止や統制にも役立ちます。
NEWJI DX
製造業に特化したデジタルトランスフォーメーション(DX)の実現を目指す請負開発型のコンサルティングサービスです。AI、iPaaS、および先端の技術を駆使して、製造プロセスの効率化、業務効率化、チームワーク強化、コスト削減、品質向上を実現します。このサービスは、製造業の課題を深く理解し、それに対する最適なデジタルソリューションを提供することで、企業が持続的な成長とイノベーションを達成できるようサポートします。
オンライン講座
製造業、主に購買・調達部門にお勤めの方々に向けた情報を配信しております。
新任の方やベテランの方、管理職を対象とした幅広いコンテンツをご用意しております。
お問い合わせ
コストダウンが利益に直結する術だと理解していても、なかなか前に進めることができない状況。そんな時は、newjiのコストダウン自動化機能で大きく利益貢献しよう!
(Β版非公開)