- お役立ち記事
- The difference between Quality Assurance (QA) and Quality Control (QC)
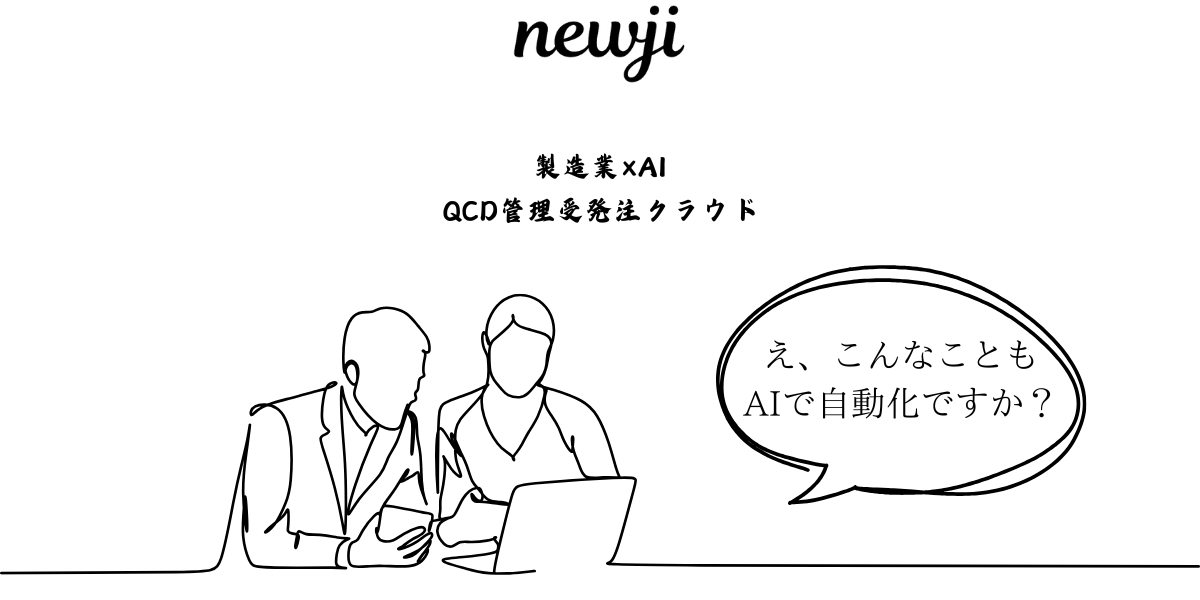
The difference between Quality Assurance (QA) and Quality Control (QC)
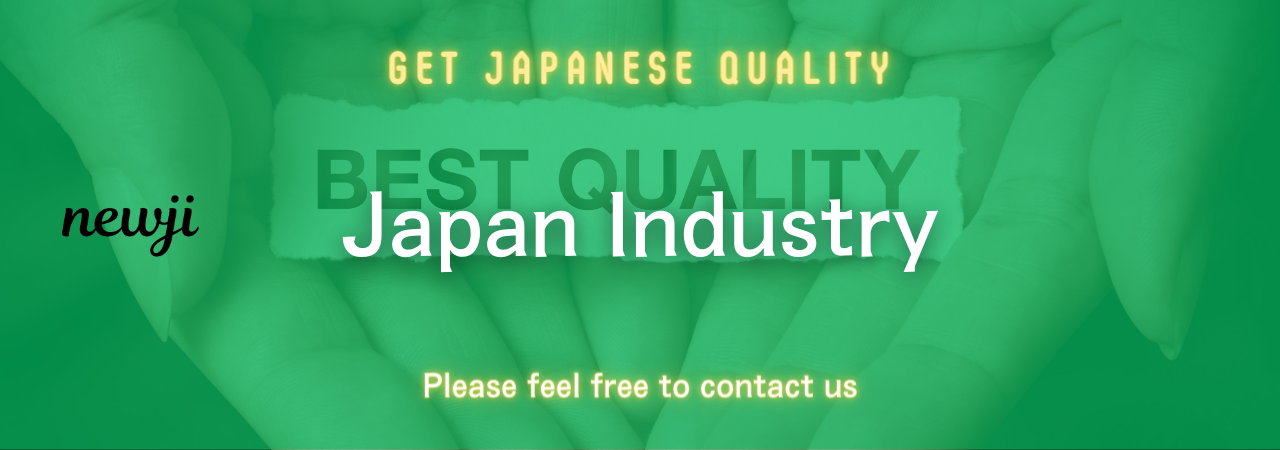
When it comes to ensuring products are up to standards, two terms are often used interchangeably: Quality Assurance (QA) and Quality Control (QC). However, they are distinct processes, each playing a vital role in the lifecycle of a product. This article aims to clarify the difference between QA and QC, helping you understand their unique functions and importance.
目次
Understanding Quality Assurance (QA)
Quality Assurance (QA) is a proactive process that focuses on setting up systems and procedures to prevent defects in products. It is all about creating and following the right processes to ensure the final product meets the desired quality standards.
The Role of QA
QA involves planning and systematic activities implemented in a quality system. These activities and processes help to provide confidence that the product or service will satisfy given requirements for quality.
QA is not solely about testing. It’s a holistic approach that encompasses many facets of production, from the inception of an idea to the release of the final product.
Key Elements of QA
1. **Process Definition:** QA involves defining processes, standards, and methodologies that need to be followed during the production lifecycle.
2. **Documentation:** Detailed documentation helps in standardizing the processes and ensures consistency across the board.
3. **Training:** Ensuring that the team is well-trained to follow the established processes is crucial. Regular training sessions and updates help maintain high standards.
4. **Review and Audits:** Regular reviews and audits are conducted to ensure that the processes are being followed correctly. Any discrepancies are noted and rectified.
Understanding Quality Control (QC)
Quality Control (QC) is a reactive process that focuses on identifying and fixing defects in the final products. Unlike QA, which is process-oriented, QC is product-oriented, concentrating on the output rather than the processes.
The Role of QC
QC involves the operational techniques and activities used to fulfill requirements for quality. It includes testing and examining products to ensure they meet the predefined standards.
Key Elements of QC
1. **Inspection:** Inspection involves examining the product for any defects. This can be done at various stages of the production process as well as on the final product.
2. **Testing:** Various tests, often predefined, are conducted to ensure that the product meets the standards. This can include functional testing, performance testing, etc.
3. **Defect Identification:** When defects are found, they are documented, analyzed, and fixed. This step is crucial for ensuring that the final product is free from defects.
4. **Corrective Actions:** Based on the identification of defects, corrective actions are taken to rectify any issues. This helps in making the product compliant with quality standards.
Key Differences Between QA and QC
While QA and QC might appear to overlap, they serve different purposes and involve different approaches. Here are some key differences:
Proactive vs. Reactive
QA is proactive, focusing on preventing defects by improving the processes. On the other hand, QC is reactive, identifying and fixing defects after they have occurred.
Process-Oriented vs. Product-Oriented
QA is process-oriented, ensuring that the right procedures are in place to deliver a quality product. QC, however, is product-oriented, inspecting and testing the final product.
Overall Approach
QA takes a broader approach, encompassing the entire production process, from designing to delivery. QC focuses narrowly on the product being delivered.
Benefits of QA and QC
Both QA and QC are essential for maintaining high standards, but their benefits differ based on their approaches.
Benefits of QA
1. **Consistency:** By standardizing processes, QA ensures consistency in the final product. This helps in building a reliable and trustworthy brand.
2. **Prevention of Defects:** By focusing on process improvements, QA helps in preventing defects before they occur. This reduces wastage and rework, saving both time and money.
3. **Improved Efficiency:** Streamlined processes mean fewer hurdles and more efficient production cycles. This can lead to quicker time-to-market.
Benefits of QC
1. **Defect Detection:** QC helps in identifying defects in the final product, ensuring that only quality products reach the customer.
2. **Customer Satisfaction:** By delivering defect-free products, QC ensures higher customer satisfaction and loyalty.
3. **Continuous Improvement:** The feedback from QC testing can be used to improve the processes, contributing to continuous improvement.
QA and QC in Different Industries
The principles of QA and QC can be applied to almost any industry, though their implementations will vary.
Manufacturing
In manufacturing, QA might involve setting up assembly lines and standard operating procedures, while QC includes inspections at various stages of production and final product testing.
Software Development
In software development, QA involves setting coding standards, conducting code reviews, and running process audits. QC, however, includes running tests on the software to detect bugs and performance issues.
Conclusion
Understanding the differences between Quality Assurance (QA) and Quality Control (QC) is critical for any business aiming to produce high-quality products. While QA is about setting up the right processes to prevent defects, QC is about identifying and fixing defects in the final product. Both are essential and complement each other in the overall quality management system.
By implementing robust QA and QC practices, businesses can ensure higher product quality, improved customer satisfaction, and reduced costs associated with defects and rework.
Quality is not an act, it’s a habit. Embracing both QA and QC can significantly elevate the standard of your products and services, making them reliable and market-ready.
資料ダウンロード
QCD調達購買管理クラウド「newji」は、調達購買部門で必要なQCD管理全てを備えた、現場特化型兼クラウド型の今世紀最高の購買管理システムとなります。
ユーザー登録
調達購買業務の効率化だけでなく、システムを導入することで、コスト削減や製品・資材のステータス可視化のほか、属人化していた購買情報の共有化による内部不正防止や統制にも役立ちます。
NEWJI DX
製造業に特化したデジタルトランスフォーメーション(DX)の実現を目指す請負開発型のコンサルティングサービスです。AI、iPaaS、および先端の技術を駆使して、製造プロセスの効率化、業務効率化、チームワーク強化、コスト削減、品質向上を実現します。このサービスは、製造業の課題を深く理解し、それに対する最適なデジタルソリューションを提供することで、企業が持続的な成長とイノベーションを達成できるようサポートします。
オンライン講座
製造業、主に購買・調達部門にお勤めの方々に向けた情報を配信しております。
新任の方やベテランの方、管理職を対象とした幅広いコンテンツをご用意しております。
お問い合わせ
コストダウンが利益に直結する術だと理解していても、なかなか前に進めることができない状況。そんな時は、newjiのコストダウン自動化機能で大きく利益貢献しよう!
(Β版非公開)