- お役立ち記事
- The difference between Quality Control and Quality Assurance
月間76,176名の
製造業ご担当者様が閲覧しています*
*2025年3月31日現在のGoogle Analyticsのデータより
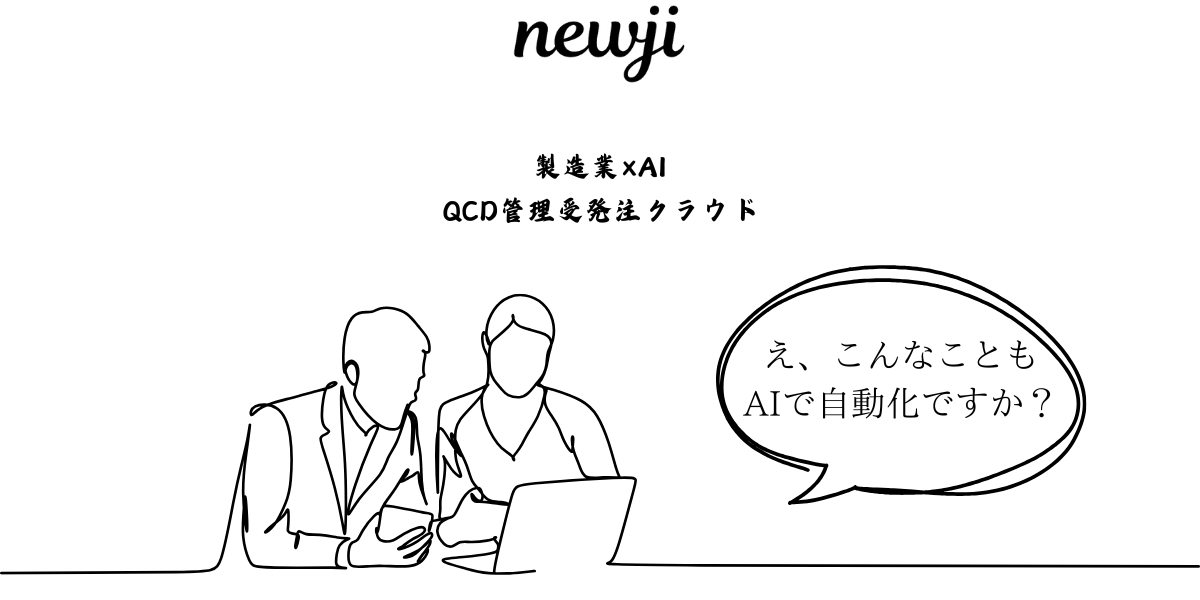
The difference between Quality Control and Quality Assurance
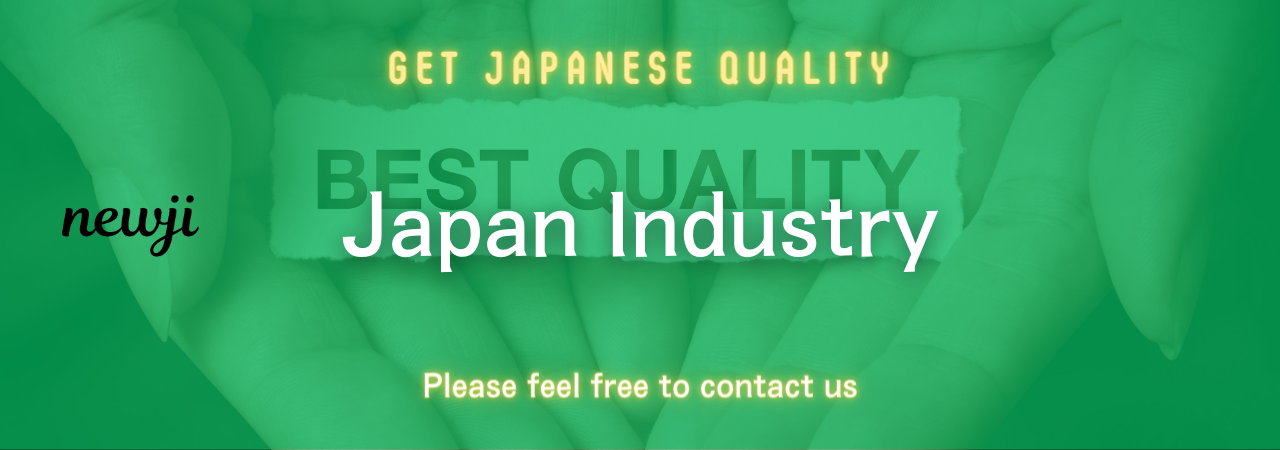
Understanding the difference between quality control (QC) and quality assurance (QA) can be essential for any business focused on delivering top-notch products or services.
Even though the terms are often used interchangeably, they have distinct roles and processes designed to ensure quality.
Clarifying these differences helps teams navigate their tasks more efficiently and ensures that quality remains a top priority.
In this article, we’ll explore these differences in detail.
目次
What is Quality Control?
Quality control is a critical component in the creation of any product or service.
QC primarily focuses on identifying defects in the final products.
It involves detailed inspections and testing to ensure that what’s being delivered meets predefined standards.
This process often entails manual or automated tests that seek out and fix any errors.
The Main Objectives of Quality Control
The primary goal of quality control is to eliminate errors before the product or service reaches the customer.
This helps in maintaining customer satisfaction and upholding the brand’s reputation.
Quality control is highly reactive because it addresses issues as they arise rather than preventing them from occurring in the first place.
How Quality Control Works
QC involves using specific tools and methods to inspect and verify the output.
Some common techniques include statistical process control (SPC), visual inspections, and physical tests.
For instance, if a factory produces thousands of parts daily, QC specialists might use SPC charts to monitor variations in production.
When inconsistencies are spotted, further inspections help determine whether the products need adjustments or can be discarded.
What is Quality Assurance?
Quality assurance, on the other hand, is more focused on preventing defects from occurring in the first place.
QA involves the systematic measurement and comparison of standards, along with continuous improvement practices to ensure processes yield the best possible outcome.
Unlike QC, which is largely product-oriented, QA is process-oriented.
The Main Objectives of Quality Assurance
The goal of quality assurance is to improve and stabilize production and associated processes to avoid handing over defective products to the customer.
QA lays down a framework of processes and procedures that aims at maintaining desired quality levels through planning and systematic activities.
How Quality Assurance Works
QA consists of various planned and systematic activities aimed at providing confidence that quality requirements will be fulfilled.
This can involve simulations, test runs, training, and reviewing process documents.
Companies often use quality management systems (QMS) to manage QA activities effectively.
ISO 9001 is one of the most recognized standards specifying requirements for a QMS.
By adhering to such standards, businesses are better positioned to minimize the risk of defects and enhance overall productivity.
Key Differences Between Quality Control and Quality Assurance
While they share a common goal—ensuring that products or services are high quality—QC and QA use different approaches to achieve this.
Scope and Focus
QC is mainly focused on identifying defects in the actual products after production.
It is product-oriented.
QA, however, is focused on improving processes to prevent defects from arising.
It is process-oriented.
Timing
QC is conducted after the product has been produced.
If any flaws are found, corrective actions are taken.
On the other hand, QA activities are conducted throughout the development lifecycle to ensure processes are efficient and effective from the outset.
Roles and Responsibilities
In most organizations, QC tasks are carried out by inspectors or testers who evaluate the final products.
QA activities, however, generally involve a broader set of personnel, including managers and engineers, who are responsible for implementing quality systems and processes.
Why Both Quality Assurance and Quality Control Are Essential
Employing both QA and QC in your business strategies ensures that you cover all aspects of quality.
While QA helps in setting up robust processes, QC ensures that the final products meet those quality standards.
Combining both ensures higher efficiency and customer satisfaction by minimizing defects and rework.
Cost Benefits
Though investing in comprehensive quality assurance might seem costly initially, it saves substantial amounts in the long run.
By preventing defects, companies can avoid the costs associated with returns, repairs, and customer dissatisfaction.
Quality control, when used together with QA, minimizes wastage and ensures any defects are caught before reaching the customer, again saving costs related to returned goods and customer complaints.
Customer Trust and Brand Loyalty
Consistent quality, ensured by both QA and QC, leads to higher customer trust and brand loyalty.
Clients are more likely to return and spread positive reviews, further enhancing your brand’s reputation.
Implementing Quality Control and Quality Assurance in Your Business
To effectively implement QC and QA, start by understanding your specific business requirements.
Conduct a thorough assessment to identify critical control points and areas needing improvement.
Setting Up Quality Standards
Establish clear quality standards based on industry benchmarks and customer expectations.
These standards will serve as the foundation for both your QC and QA activities.
Training Your Team
Both QA and QC require skilled professionals to be effective.
Invest in training programs to ensure your team understands the importance of quality and how to implement various QC and QA techniques.
Monitoring and Continuous Improvement
Keep track of your QC and QA activities to identify areas for improvement continually.
Regular audits and customer feedback can provide valuable insights to refine your processes and improve product quality.
Understanding the distinct roles and methods of quality control and quality assurance is crucial in ensuring your products and services meet the highest standards.
By properly integrating both into your business operations, you not only maintain quality but also enhance efficiency, customer satisfaction, and long-term profitability.
資料ダウンロード
QCD管理受発注クラウド「newji」は、受発注部門で必要なQCD管理全てを備えた、現場特化型兼クラウド型の今世紀最高の受発注管理システムとなります。
ユーザー登録
受発注業務の効率化だけでなく、システムを導入することで、コスト削減や製品・資材のステータス可視化のほか、属人化していた受発注情報の共有化による内部不正防止や統制にも役立ちます。
NEWJI DX
製造業に特化したデジタルトランスフォーメーション(DX)の実現を目指す請負開発型のコンサルティングサービスです。AI、iPaaS、および先端の技術を駆使して、製造プロセスの効率化、業務効率化、チームワーク強化、コスト削減、品質向上を実現します。このサービスは、製造業の課題を深く理解し、それに対する最適なデジタルソリューションを提供することで、企業が持続的な成長とイノベーションを達成できるようサポートします。
製造業ニュース解説
製造業、主に購買・調達部門にお勤めの方々に向けた情報を配信しております。
新任の方やベテランの方、管理職を対象とした幅広いコンテンツをご用意しております。
お問い合わせ
コストダウンが利益に直結する術だと理解していても、なかなか前に進めることができない状況。そんな時は、newjiのコストダウン自動化機能で大きく利益貢献しよう!
(β版非公開)