- お役立ち記事
- The difference between Quality Trend Analysis and Quality Abnormality Analysis
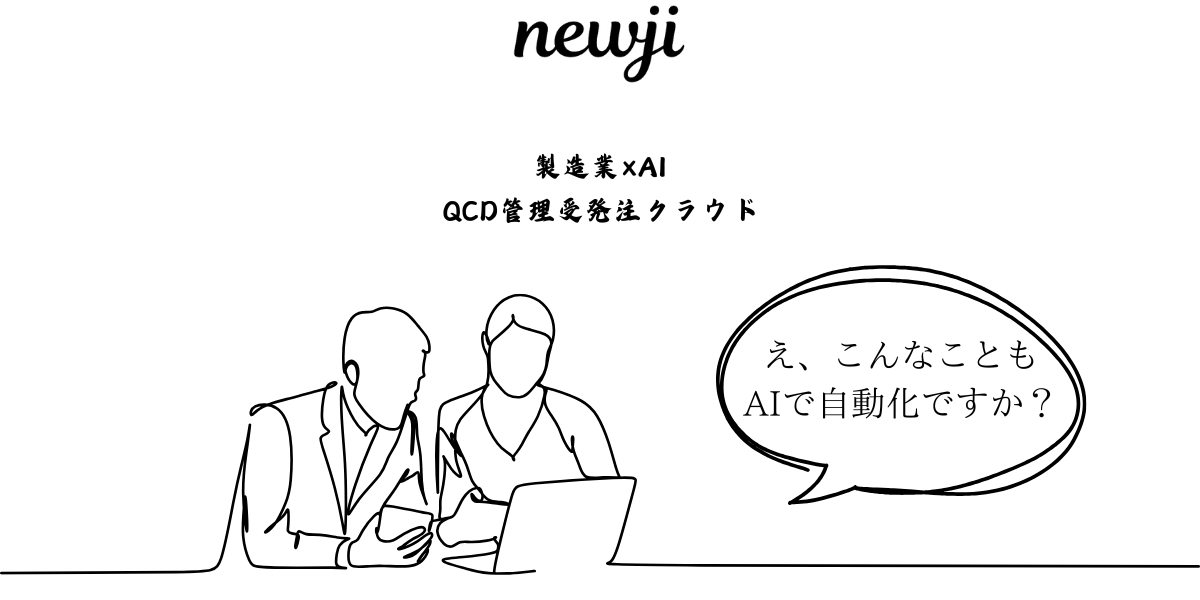
The difference between Quality Trend Analysis and Quality Abnormality Analysis
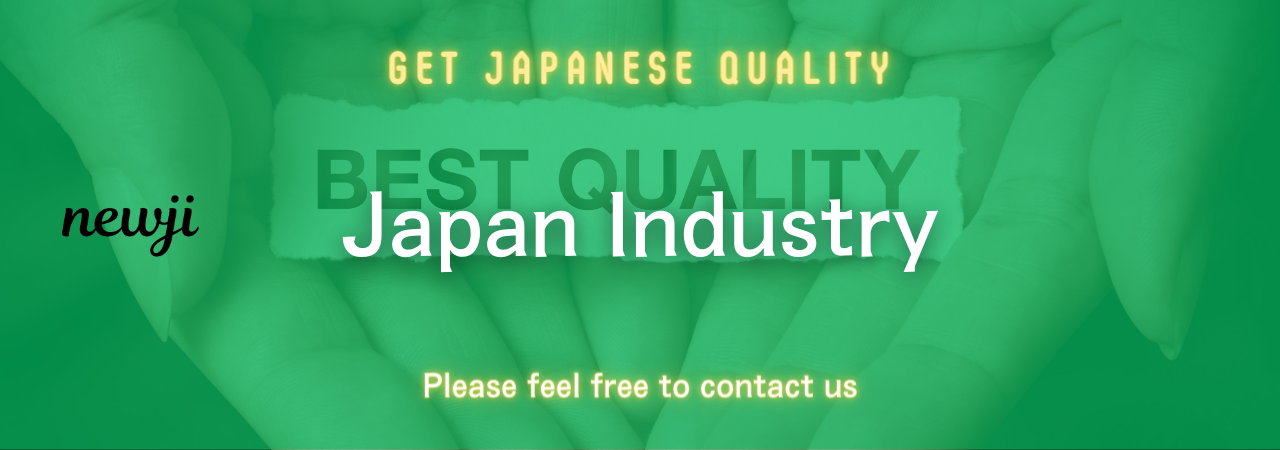
Quality is a vital aspect of any product or service.
It ensures that the end users receive something that meets or exceeds their expectations.
When companies want to measure and improve their quality, they often use different types of analysis.
Two common types are Quality Trend Analysis and Quality Abnormality Analysis.
Although they might sound similar, they focus on different aspects of quality management.
目次
Understanding Quality Trend Analysis
Quality Trend Analysis focuses on tracking and interpreting the changes in quality over a period of time.
It’s like looking at a graph of data points to see if things are getting better, worse, or staying the same.
This analysis helps identify long-term trends and patterns.
Why is Quality Trend Analysis Important?
By understanding the trends in quality, companies can make informed decisions.
For example, if the trend shows a gradual improvement in product quality, the company might continue with its current processes.
However, if there’s a decline, it might indicate the need for an investigation and corrective action.
Key Elements of Quality Trend Analysis
There are some critical components to consider in Quality Trend Analysis:
1. **Data Collection**: Gather data on various quality parameters over a specific period.
This could include metrics like defect rates, customer complaints, or product returns.
2. **Visualization**: Create charts or graphs to visualize the data.
This helps in easily identifying trends and patterns.
3. **Analysis**: Interpret the visualized data.
Look for patterns such as seasonal variations, gradual improvements, or sudden drops in quality.
Steps to Conduct Quality Trend Analysis
1. **Identify Key Metrics**: Determine which quality metrics are most critical for your product or service.
2. **Collect Data**: Gather historical data on these metrics.
3. **Visualize Data**: Use charts or graphs to display the data over time.
4. **Interpret Trends**: Analyze the visualized data to identify trends.
5. **Make Decisions**: Based on the identified trends, make informed decisions to improve or maintain quality.
Understanding Quality Abnormality Analysis
Unlike Quality Trend Analysis, Quality Abnormality Analysis focuses on identifying and investigating unusual occurrences in quality.
It aims to pinpoint anomalies or discrepancies that deviate from the norm.
Why is Quality Abnormality Analysis Important?
Detecting and addressing quality abnormalities is crucial to maintain overall quality levels.
Abnormalities can lead to customer dissatisfaction, increased costs, and damage to the brand reputation.
Key Elements of Quality Abnormality Analysis
Quality Abnormality Analysis also involves several essential components:
1. **Detection**: The first step is identifying the abnormality.
This could happen through various means, such as quality control inspections, automated monitoring systems, or customer feedback.
2. **Classification**: Categorize the abnormality based on its nature and severity.
This helps prioritize which issues to address first.
3. **Investigation**: Conduct a root cause analysis to determine why the abnormality occurred.
Tools like Fishbone Diagrams, Pareto Charts, or 5 Whys can assist in this process.
4. **Corrective Actions**: Develop and implement solutions to fix the root cause and prevent future occurrences.
5. **Verification**: After implementing corrective actions, verify their effectiveness through further monitoring and analysis.
Comparing Quality Trend Analysis and Quality Abnormality Analysis
Both types of analysis are essential for comprehensive quality management.
Yet, they serve different purposes and provide unique insights.
Scope and Focus
Quality Trend Analysis has a broader scope.
It looks at overall trends and patterns over time.
In contrast, Quality Abnormality Analysis has a narrower focus, zeroing in on specific anomalies.
Data and Tools
For Quality Trend Analysis, tools like line charts, control charts, and histograms are commonly used to visualize data.
In Quality Abnormality Analysis, tools like Fishbone Diagrams, Pareto Charts, and Root Cause Analysis are more prevalent.
Applications
Use Quality Trend Analysis when you need to understand long-term changes and patterns in quality.
This helps in strategic planning and continuous improvement.
Opt for Quality Abnormality Analysis when you need to address specific issues that could harm product or service quality immediately.
Integrating Both Analyses for Better Quality Management
For effective quality management, it’s best to integrate both analyses.
By doing so, you can cover both the broad and specific aspects of quality.
Start with Quality Trend Analysis to understand the overall direction in which your quality is heading.
Use this information to implement strategic changes.
Simultaneously, perform Quality Abnormality Analysis to tackle specific, immediate issues that could disrupt your overall trend.
Practical Steps for Integration
1. **Routine Monitoring**: Establish a system for regular data collection and monitoring.
This should include parameters for both trend and abnormality detection.
2. **Combined Reporting**: Create a reporting format that includes insights from both analyses.
This ensures a balanced view of long-term trends and specific issues.
3. **Cross-Functional Teams**: Form teams that include members from different departments.
This promotes a holistic approach to identifying and solving quality issues.
4. **Feedback Loops**: Implement feedback loops to ensure that insights from both analyses lead to actionable improvements.
This helps in continuously refining your quality management strategies.
By understanding the differences between Quality Trend Analysis and Quality Abnormality Analysis, you’ll be better equipped to ensure that your product or service remains top-notch.
Both analyses are crucial, offering different but complementary insights into quality management.
Integrating them will provide a comprehensive understanding, helping you maintain and improve quality in the long run.
資料ダウンロード
QCD調達購買管理クラウド「newji」は、調達購買部門で必要なQCD管理全てを備えた、現場特化型兼クラウド型の今世紀最高の購買管理システムとなります。
ユーザー登録
調達購買業務の効率化だけでなく、システムを導入することで、コスト削減や製品・資材のステータス可視化のほか、属人化していた購買情報の共有化による内部不正防止や統制にも役立ちます。
NEWJI DX
製造業に特化したデジタルトランスフォーメーション(DX)の実現を目指す請負開発型のコンサルティングサービスです。AI、iPaaS、および先端の技術を駆使して、製造プロセスの効率化、業務効率化、チームワーク強化、コスト削減、品質向上を実現します。このサービスは、製造業の課題を深く理解し、それに対する最適なデジタルソリューションを提供することで、企業が持続的な成長とイノベーションを達成できるようサポートします。
オンライン講座
製造業、主に購買・調達部門にお勤めの方々に向けた情報を配信しております。
新任の方やベテランの方、管理職を対象とした幅広いコンテンツをご用意しております。
お問い合わせ
コストダウンが利益に直結する術だと理解していても、なかなか前に進めることができない状況。そんな時は、newjiのコストダウン自動化機能で大きく利益貢献しよう!
(Β版非公開)