- お役立ち記事
- The difference between Quality Verification and Quality Validation
月間76,176名の
製造業ご担当者様が閲覧しています*
*2025年3月31日現在のGoogle Analyticsのデータより
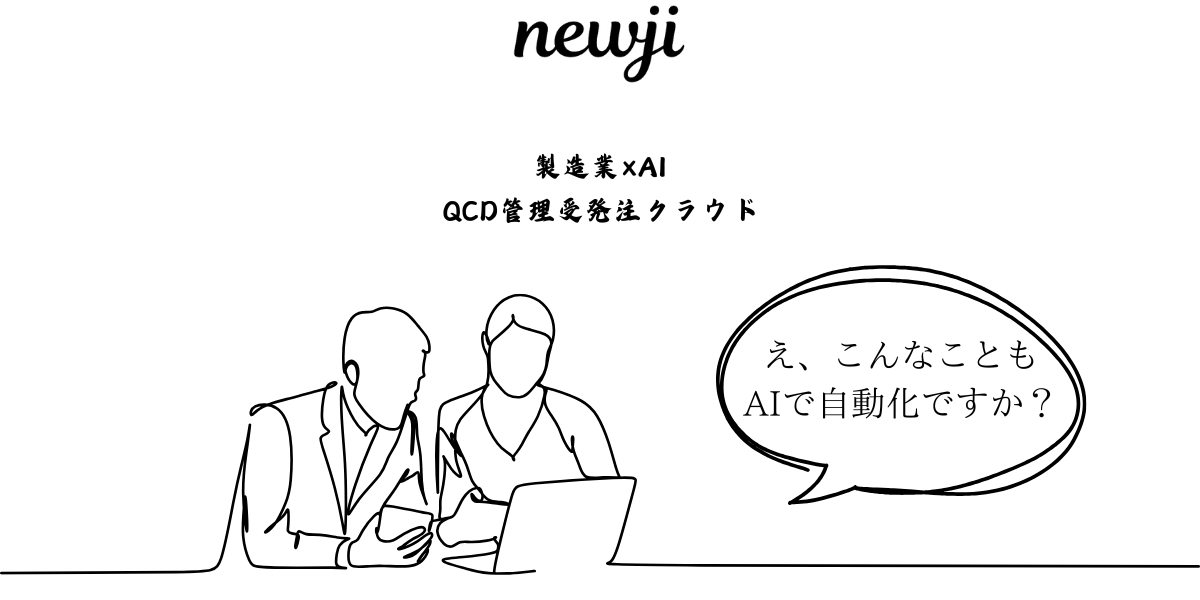
The difference between Quality Verification and Quality Validation
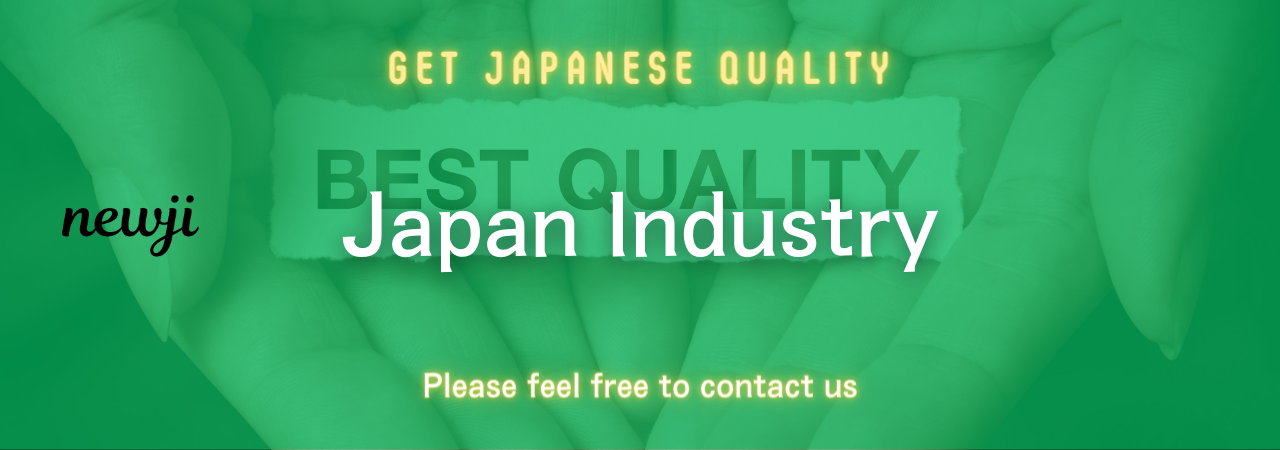
It is crucial to distinguish between quality verification and quality validation when it comes to maintaining high standards in any production or development process.
While both play indispensable roles in ensuring the final product’s quality, they serve different purposes and occur at different stages of the project life cycle.
Below, we dive deeper into the fundamental differences between these two concepts.
目次
Understanding Quality Verification
Quality verification is a process that ensures the product is being built correctly according to the design specifications, guidelines, and requirements.
This activity is conducted during the development or manufacturing phase to catch errors early.
Verification is often considered a static method of checking documents, design, code, and program.
Key Elements of Quality Verification
Verification typically involves activities like inspections, reviews, and walkthroughs.
During inspections, a detailed examination of product features or documents is conducted to find defects.
Reviews are more like group-based meetings where team members assess various aspects of the project to see if they meet the specified requirements.
Walkthroughs are often guided tours where a developer explains the product to a team, ensuring compliance with set guidelines.
Verification Techniques
Common techniques used in quality verification include:
– Peer Reviews: Peers examine each other’s work to catch mistakes early.
– Audits: Formal, structured reviews to ensure procedures and standards are being followed.
– Desk Checks: Informal reviews done individually to identify issues.
These techniques focus on the requirements and design stages and are more prevention-oriented than detection-oriented.
Understanding Quality Validation
Quality validation, on the other hand, is a dynamic process.
It ensures that the final product meets the user’s needs and works as intended in real-world scenarios.
Validation is particularly user-centric, occurring later in the project life cycle, often just before product delivery.
It aims to show that the product is fit for its intended use.
Key Elements of Quality Validation
During quality validation, various forms of testing are conducted to ensure the product performs as expected.
This includes functional testing, user acceptance testing (UAT), and performance testing.
Functional testing ensures that the product performs its intended functions accurately.
UAT involves end-users testing the product in real-life conditions to verify that it solves the user’s problems.
Performance testing checks the product’s responsiveness and stability under specific conditions.
Validation Techniques
Common methods used in the validation process include:
– Black Box Testing: Testing the functionality of the product without looking at the internal code structure.
– End-User Testing: The actual user performs tests to validate the product’s usability and functionality.
– System Testing: The complete integrated system is tested to ensure it meets the specified requirements.
These validation methods are more detection-oriented and aim to ensure that the product is fit for its intended purpose.
Major Differences Between Verification and Validation
Although both verification and validation are essential to the quality assurance process, there are significant differences between the two.
Different Objectives
The primary aim of verification is to ensure that the product is being built according to the initial design specifications and requirements.
It asks the question, “Are we building the product right?”
Validation, however, focuses on checking whether the product meets the needs and expectations of the end users.
It answers the question, “Are we building the right product?”
Different Timing
Verification activities occur during the development or manufacturing stage of the product.
These activities are often conducted before the product reaches the final stages, as early-stage error detection helps in reducing costs and time.
Validation takes place later in the project lifecycle, typically close to the product delivery date.
Its purpose is to ensure the product is ready for real-world use and meets user requirements.
Different Techniques
Verification uses document reviews, peer reviews, and audits as common methods.
These are predominantly static techniques where the product is reviewed without actually executing the software or inspecting the operational product.
Validation, on the other hand, employs dynamic techniques like functional testing and UAT.
In these, the product is executed, and its performance is checked under real-life conditions.
Why Both Are Essential
Skipping either verification or validation can lead to serious issues down the line.
If you don’t verify adequately, you might find design flaws or requirement mismatches too late in the process, making corrections costly and time-consuming.
On the other hand, if you skip validation, you risk a situation where the product, even if built correctly, doesn’t meet user expectations or function properly in real-world conditions.
Cost Implications
Addressing issues identified during verification is often less costly than fixing problems identified during validation.
This is because catching errors early in the design or development stage prevents the need for significant rework.
Customer Satisfaction
Both processes contribute to higher customer satisfaction.
Verification ensures that the product’s foundation is solid and adheres to set guidelines.
Validation ensures that the final product is exactly what the customer needs and performs well in real-world scenarios.
In essence, quality verification and quality validation are two sides of the same coin.
While they serve different functions and occur at different stages, both are necessary to ensure a high-quality product.
Combining both processes effectively can result in a product that not only meets design standards but also exceeds user expectations.
資料ダウンロード
QCD管理受発注クラウド「newji」は、受発注部門で必要なQCD管理全てを備えた、現場特化型兼クラウド型の今世紀最高の受発注管理システムとなります。
ユーザー登録
受発注業務の効率化だけでなく、システムを導入することで、コスト削減や製品・資材のステータス可視化のほか、属人化していた受発注情報の共有化による内部不正防止や統制にも役立ちます。
NEWJI DX
製造業に特化したデジタルトランスフォーメーション(DX)の実現を目指す請負開発型のコンサルティングサービスです。AI、iPaaS、および先端の技術を駆使して、製造プロセスの効率化、業務効率化、チームワーク強化、コスト削減、品質向上を実現します。このサービスは、製造業の課題を深く理解し、それに対する最適なデジタルソリューションを提供することで、企業が持続的な成長とイノベーションを達成できるようサポートします。
製造業ニュース解説
製造業、主に購買・調達部門にお勤めの方々に向けた情報を配信しております。
新任の方やベテランの方、管理職を対象とした幅広いコンテンツをご用意しております。
お問い合わせ
コストダウンが利益に直結する術だと理解していても、なかなか前に進めることができない状況。そんな時は、newjiのコストダウン自動化機能で大きく利益貢献しよう!
(β版非公開)