- お役立ち記事
- The difference between Reorder Point and Periodic Reorder
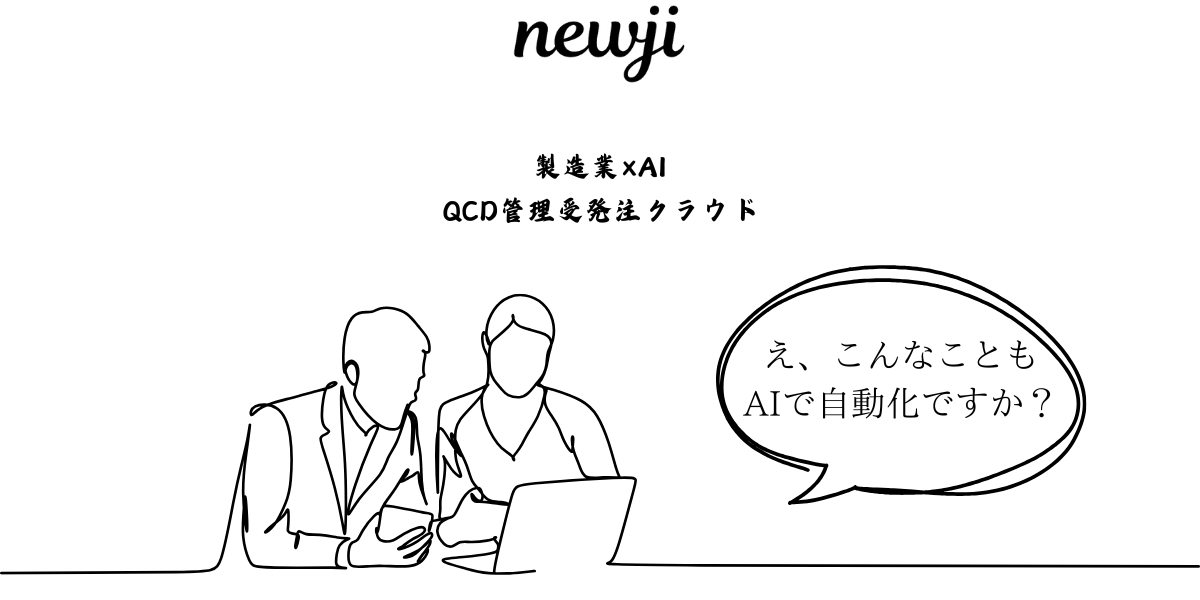
The difference between Reorder Point and Periodic Reorder
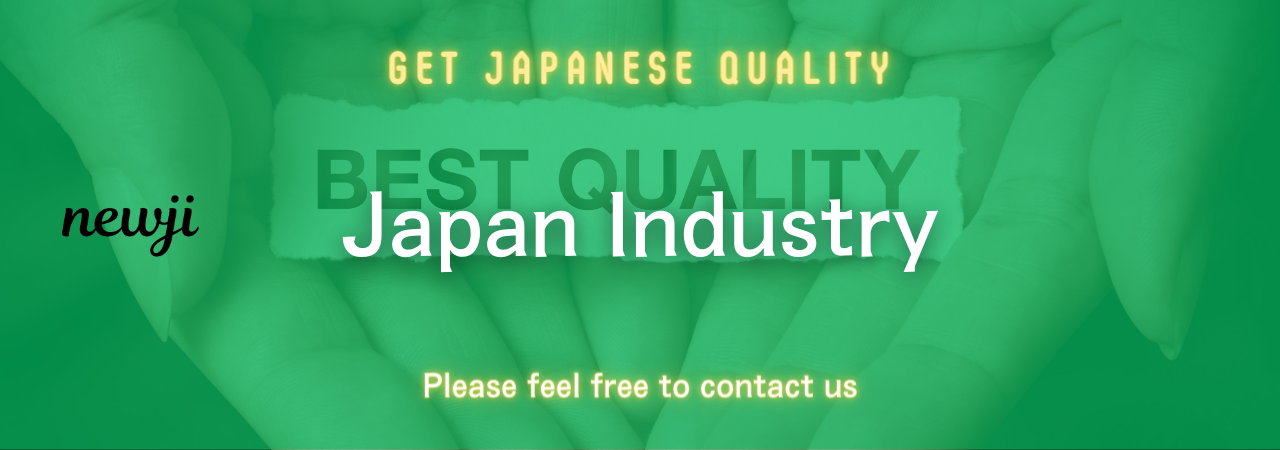
When managing inventory, knowing when to reorder products is crucial for any business.
Two popular methods to determine this are the Reorder Point (ROP) and Periodic Reorder (PR).
Each approach has its own unique characteristics and benefits.
In this article, we will explore the differences between Reorder Point and Periodic Reorder, and help you understand which method might be best suited for your business.
目次
Understanding Reorder Point (ROP)
The Reorder Point (ROP) is a specific inventory level at which new stock should be ordered to replenish inventory before it runs out.
This method relies on constant monitoring of inventory levels and involves placing an order as soon as the stock reaches a predetermined level.
Let’s look more closely at how ROP works.
How is ROP Determined?
The Reorder Point is calculated using the formula:
ROP = (Average Daily Usage * Lead Time) + Safety Stock
– **Average Daily Usage** is the average quantity of items sold per day.
– **Lead Time** is the time it takes for a new shipment to arrive after placing an order.
– **Safety Stock** is an extra quantity ordered to account for unexpected delays in delivery or sudden increases in demand.
For example, if a business sells an average of 50 units per day, has a lead time of 7 days, and keeps a safety stock of 100 units, the ROP would be:
ROP = (50 * 7) + 100 = 450 units
When the inventory level drops to 450 units, an order is placed to replenish stock.
Benefits of ROP
One of the main benefits of the ROP method is that it ensures you always have enough stock on hand to meet customer demand.
It helps in avoiding stockouts and lost sales.
This approach is particularly useful for businesses with stable sales patterns and predictable lead times.
Understanding Periodic Reorder (PR)
Periodic Reorder, also known as Periodic Review, is a method where inventory levels are checked at regular intervals, and orders are placed to replenish stock based on current inventory levels.
Instead of continuously monitoring inventory levels like in ROP, PR involves setting specific review periods.
How is PR Implemented?
In Periodic Reorder, inventory is reviewed at fixed intervals, such as weekly, bi-weekly, or monthly.
During each review, the current inventory level is compared to a predetermined target level.
The order quantity is calculated to bring the inventory back up to the target level.
For example, if a business reviews its inventory every two weeks and aims to maintain a target level of 1,000 units, it will calculate how much to order during the review period.
If the current inventory is 400 units, the business needs to order 600 units to reach the target level of 1,000 units.
Benefits of PR
Periodic Reorder simplifies inventory management by eliminating the need for constant monitoring.
It is ideal for businesses with fluctuating demand or lead times.
PR also allows for bulk ordering, which can lead to cost savings through bulk discounts and reduced shipping costs.
Choosing Between ROP and PR
Now that we have a better understanding of both Reorder Point and Periodic Reorder, let’s discuss how to choose the right method for your business.
Consider Inventory Turnover Rate
If your business has a high inventory turnover rate, where products are sold and restocked frequently, ROP might be more suitable.
ROP ensures continuous monitoring and timely replenishment, which is essential for businesses with rapid inventory movement.
On the other hand, if your business experiences slow-moving inventory, PR might be a better option.
PR allows you to review inventory at regular intervals, making it easier to manage slow-moving stock without the need for constant monitoring.
Assess Sales Patterns and Lead Times
For businesses with stable and predictable sales patterns, ROP is a reliable method.
However, for businesses with unpredictable sales patterns and varying lead times, PR offers more flexibility and reduces the risk of overstocking or understocking.
Evaluate Resources and Tools
Implementing ROP requires setting up a system for constant inventory monitoring and the ability to place orders when necessary.
It might involve using inventory management software to track stock levels in real-time.
If your business has the resources and tools to support this, ROP can be highly effective.
Conversely, PR requires less constant oversight, relying on scheduled reviews.
It can be managed with simpler systems, as long as reviews are conducted consistently.
This approach might be more feasible for smaller businesses or those with limited resources.
Analyze Costs
While both methods aim to optimize inventory levels, they come with different cost implications.
ROP might result in more frequent orders, potentially increasing shipping costs.
However, it can also minimize the cost of lost sales due to stockouts.
PR allows for bulk ordering, which can reduce costs through volume discounts and fewer shipments.
It may also reduce administrative costs associated with placing frequent orders.
Conclusion
Both Reorder Point (ROP) and Periodic Reorder (PR) are valuable methods for managing inventory.
The choice between them depends on your business’s specific needs, sales patterns, lead times, and available resources.
Understanding the differences and benefits of each method will help you make an informed decision that aligns with your business goals.
資料ダウンロード
QCD調達購買管理クラウド「newji」は、調達購買部門で必要なQCD管理全てを備えた、現場特化型兼クラウド型の今世紀最高の購買管理システムとなります。
ユーザー登録
調達購買業務の効率化だけでなく、システムを導入することで、コスト削減や製品・資材のステータス可視化のほか、属人化していた購買情報の共有化による内部不正防止や統制にも役立ちます。
NEWJI DX
製造業に特化したデジタルトランスフォーメーション(DX)の実現を目指す請負開発型のコンサルティングサービスです。AI、iPaaS、および先端の技術を駆使して、製造プロセスの効率化、業務効率化、チームワーク強化、コスト削減、品質向上を実現します。このサービスは、製造業の課題を深く理解し、それに対する最適なデジタルソリューションを提供することで、企業が持続的な成長とイノベーションを達成できるようサポートします。
オンライン講座
製造業、主に購買・調達部門にお勤めの方々に向けた情報を配信しております。
新任の方やベテランの方、管理職を対象とした幅広いコンテンツをご用意しております。
お問い合わせ
コストダウンが利益に直結する術だと理解していても、なかなか前に進めることができない状況。そんな時は、newjiのコストダウン自動化機能で大きく利益貢献しよう!
(Β版非公開)