- お役立ち記事
- The difference between Roll Grinding and Centerless Grinding
この記事は、当社の提供するお役立ち記事の一部です。詳しくは公式サイトをご覧ください。
The difference between Roll Grinding and Centerless Grinding
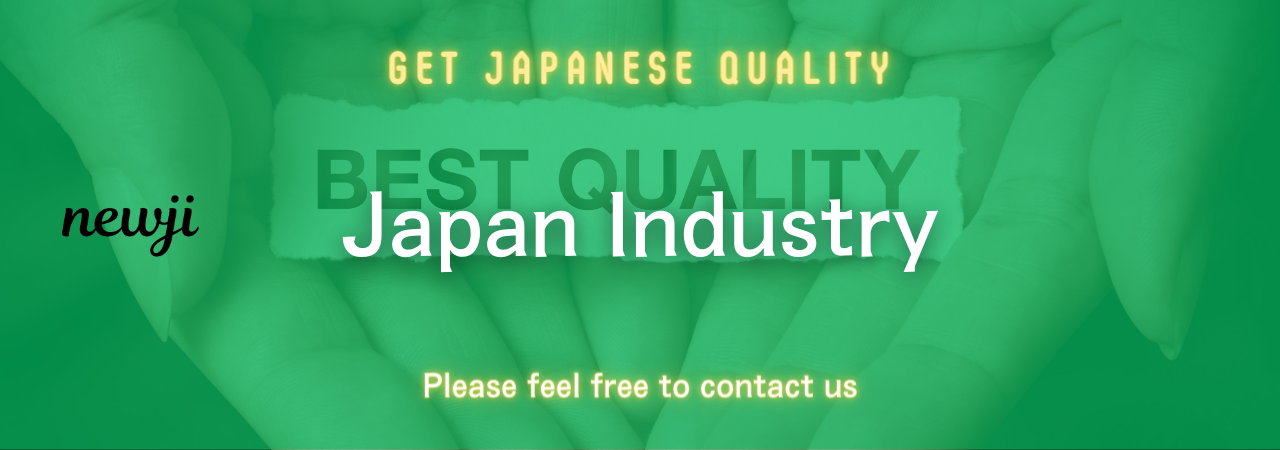
目次
Introduction to Roll Grinding and Centerless Grinding
In the world of manufacturing, precision is key.
Achieving the perfect shape and finish on various materials often requires different grinding techniques.
Two common types of grinding processes are roll grinding and centerless grinding.
Although they serve similar purposes, these methods have distinctive differences that make each one suitable for particular applications.
What is Roll Grinding?
Roll grinding is a specialized form of cylindrical grinding used to process large rolls or cylinders.
These rolls are typically utilized in the printing, paper, and steel industries, where their surface finish and profile are crucial to the manufacturing process.
The Process of Roll Grinding
The roll grinding process involves placing the roll in a machine that spins it while applying a grinding wheel to the surface.
The wheel moves back and forth, fine-tuning the roll’s dimensions and surface finish.
This method ensures high precision and the ability to achieve tight tolerances.
Applications of Roll Grinding
Roll grinding is commonly used in industries where precision rolls play a critical role.
For example, in the printing industry, rolls need to have a smooth and uniform surface to ensure consistent ink application.
In the paper industry, cylindrical rolls are used to press and smooth paper sheets.
Steel manufacturers also rely on roll grinding to shape metal rolls for various applications.
What is Centerless Grinding?
Centerless grinding is another form of cylindrical grinding but with a distinct difference.
In this process, the workpiece is not held between centers, as the name implies.
Instead, it is supported by a blade and is ground by a grinding wheel and a regulating wheel.
The Process of Centerless Grinding
In centerless grinding, the workpiece is placed between a grinding wheel and a smaller regulating wheel.
The grinding wheel does the cutting, while the regulating wheel controls the workpiece’s speed and provides stability.
Both wheels rotate in the same direction, but at different speeds, enabling the grinding wheel to shape the workpiece to the desired dimensions.
Applications of Centerless Grinding
Centerless grinding is versatile and is used for both small and large batches of high-precision components.
This method is ideal for producing cylindrical parts with high accuracy and excellent surface finishes.
Industries such as automotive, aerospace, and medical device manufacturing often use centerless grinding for components like bearing races, bushings, and needle rollers.
The Key Differences Between Roll Grinding and Centerless Grinding
Even though both roll grinding and centerless grinding process materials to achieve precise dimensions and smooth finishes, they have several notable differences.
Workpiece Positioning
In roll grinding, the workpiece is secured and rotated around its axis between centers.
This secure positioning allows for high precision in shaping the surface.
In contrast, centerless grinding does not require centering.
Instead, the workpiece is fed through without being clamped, which speeds up the grinding process, especially for large volumes.
Grinding Wheel Contact
Roll grinding usually involves a single grinding wheel coming into contact with the workpiece.
The wheel moves back and forth, ensuring a consistent finish.
In centerless grinding, the workpiece is sandwiched between two grinding wheels—the larger grinding wheel and the smaller regulating wheel.
This dual contact allows for continuous feeding and high throughput.
Typical Workpiece Shapes and Sizes
Roll grinding is mainly used for large, cylindrical rolls or shafts with lengths that can reach several meters.
In contrast, centerless grinding handles smaller, more uniformly sized cylindrical parts efficiently, making it suitable for high-volume production of small components.
Which Grinding Method Should You Choose?
The decision between roll grinding and centerless grinding depends on several factors, including the size, shape, and volume of the workpieces.
When to Choose Roll Grinding
Roll grinding is the ideal choice when working with large rolls that require precise surface finishes and tight tolerances.
Industries that benefit from roll grinding are those dealing with manufacturing or processing that requires high-quality rolls, such as paper mills, printing companies, and steel manufacturers.
When to Choose Centerless Grinding
Centerless grinding is better suited for the production of smaller cylindrical components in large quantities.
It is highly efficient, producing components with excellent surface finishes and precise dimensions.
This method is optimal for industries like automotive, aerospace, and medical device manufacturing.
Conclusion
Both roll grinding and centerless grinding have their unique advantages and applications.
Understanding the differences between these two grinding methods can help you make an informed decision based on your specific manufacturing needs.
Whether you require the high precision for large rolls provided by roll grinding or the efficiency and accuracy in mass production offered by centerless grinding, each technique plays a crucial role in various industries.
Choose the method that best fits the characteristics of your workpiece and the demands of your production process to achieve optimal results.
資料ダウンロード
QCD調達購買管理クラウド「newji」は、調達購買部門で必要なQCD管理全てを備えた、現場特化型兼クラウド型の今世紀最高の購買管理システムとなります。
ユーザー登録
調達購買業務の効率化だけでなく、システムを導入することで、コスト削減や製品・資材のステータス可視化のほか、属人化していた購買情報の共有化による内部不正防止や統制にも役立ちます。
NEWJI DX
製造業に特化したデジタルトランスフォーメーション(DX)の実現を目指す請負開発型のコンサルティングサービスです。AI、iPaaS、および先端の技術を駆使して、製造プロセスの効率化、業務効率化、チームワーク強化、コスト削減、品質向上を実現します。このサービスは、製造業の課題を深く理解し、それに対する最適なデジタルソリューションを提供することで、企業が持続的な成長とイノベーションを達成できるようサポートします。
オンライン講座
製造業、主に購買・調達部門にお勤めの方々に向けた情報を配信しております。
新任の方やベテランの方、管理職を対象とした幅広いコンテンツをご用意しております。
お問い合わせ
コストダウンが利益に直結する術だと理解していても、なかなか前に進めることができない状況。そんな時は、newjiのコストダウン自動化機能で大きく利益貢献しよう!
(Β版非公開)