- お役立ち記事
- The difference between Safety Stock and Risk Buffer
The difference between Safety Stock and Risk Buffer
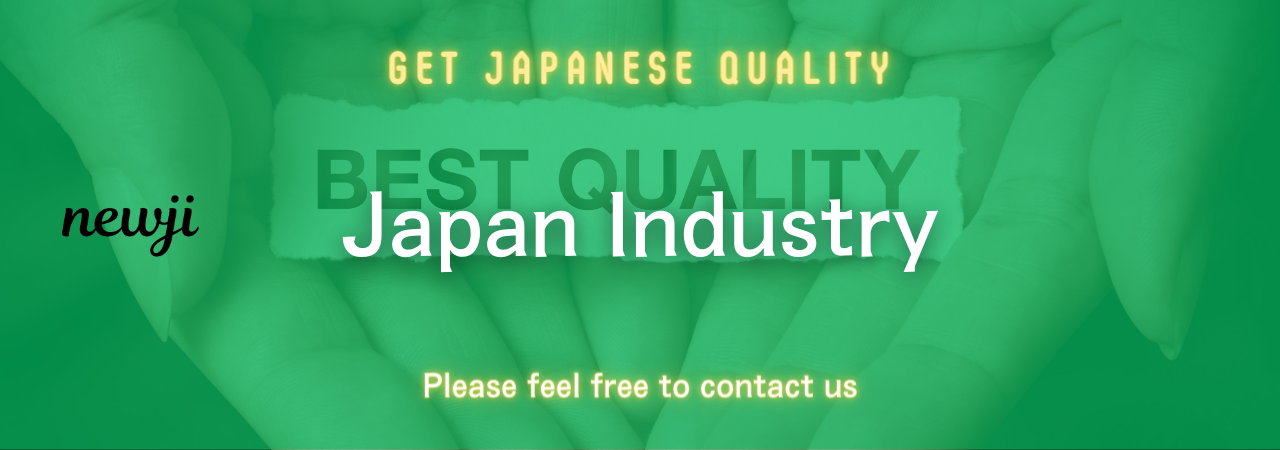
When it comes to inventory management, understanding the concepts of safety stock and risk buffer can make a significant difference in your operations.
Both terms relate to how a business handles uncertainties in supply chain and demand, yet they are distinct in their functions and applications.
In this article, we will explore the differences between safety stock and risk buffer, and how leveraging both can improve your inventory management strategies.
目次
What is Safety Stock?
Safety stock refers to the extra inventory held to mitigate the risk of stockouts caused by uncertainties in supply and demand.
It serves as a buffer to protect against unexpected spikes in customer demand or unforeseen supply chain disruptions.
The primary objective of safety stock is to ensure that a company does not run out of products, thereby preventing potential lost sales and maintaining customer satisfaction.
Calculating Safety Stock
The calculation of safety stock typically involves factors such as average demand, lead time, and standard deviation of both demand and lead time.
Various formulas can be used, but a common method is the following:
Safety Stock = Z * √(σd² * LT + D² * σlt²)
Where Z is the service level factor (usually associated with the desired service level), σd is the standard deviation of demand, LT is the lead time, D is the average demand, and σlt is the standard deviation of lead time.
By using this formula, businesses can determine an optimal level of safety stock that adequately covers potential variability, thereby enhancing their service levels.
What is Risk Buffer?
Risk buffer, on the other hand, is a broader concept that encompasses various strategies to mitigate risks within the supply chain.
Unlike safety stock, which primarily focuses on inventory, a risk buffer can be related to processes, suppliers, and even financial reserves.
The risk buffer is designed to ensure business continuity and resilience in the face of potential disruptions, such as natural disasters, geopolitical events, or significant market fluctuations.
Components of Risk Buffer
Risk buffer strategies can be divided into several categories, including:
1. Process Flexibility
Having adaptable processes allows a business to quickly adjust to changes within the supply chain.
For example, a flexible manufacturing system can switch between producing different products based on shifting market demands.
2. Supplier Diversification
Relying on multiple suppliers reduces the risk of supply chain disruptions if one supplier faces an issue.
Having alternative suppliers ensures continuous operations even if there is a problem with one source.
3. Financial Reserves
Maintaining financial reserves can help a company absorb the costs associated with supply chain disruptions or demand spikes.
This ensures that the business can continue to function smoothly during unexpected situations.
Key Differences Between Safety Stock and Risk Buffer
Although both safety stock and risk buffer aim to protect against uncertainties, there are key differences between the two:
1. Scope
Safety stock focuses specifically on inventory levels and is a quantitative measure calculated based on demand and supply variability.
Risk buffer encompasses a broader range of strategies, including process flexibility, supplier diversification, and financial reserves.
2. Function
The primary function of safety stock is to prevent stockouts and ensure product availability.
In contrast, the risk buffer seeks to enhance overall business resilience and continuity by employing various risk mitigation strategies.
3. Implementation
Safety stock is typically calculated using statistical methods and is relatively straightforward to implement.
Risk buffer strategies require a comprehensive risk assessment and a multifaceted approach, often involving changes to processes, supplier relationships, and financial planning.
Integrating Safety Stock and Risk Buffer in Inventory Management
For effective inventory management, it is essential to integrate both safety stock and risk buffer strategies.
Here are some steps to achieve this integration:
1. Conduct a Risk Assessment
Begin by identifying potential risks within your supply chain, such as supplier reliability, lead time variability, and demand fluctuations.
Evaluate the likelihood and impact of each risk to prioritize your mitigation efforts.
2. Calculate Optimal Safety Stock
Use statistical methods to calculate the optimal level of safety stock needed to cover demand and supply variability.
Regularly review and adjust these calculations based on changing market conditions and historical data.
3. Develop a Risk Mitigation Plan
Create a comprehensive risk mitigation plan that includes strategies for process flexibility, supplier diversification, and financial reserves.
Consider collaborating with key stakeholders, such as suppliers and logistics providers, to strengthen your supply chain resilience.
4. Monitor and Adjust
Continuously monitor your inventory levels, supplier performance, and market trends.
Make adjustments to your safety stock levels and risk buffer strategies as needed to address changing conditions and emerging risks.
Benefits of Integrating Safety Stock and Risk Buffer
By integrating both safety stock and risk buffer strategies, businesses can enjoy several benefits, including:
1. Improved Customer Satisfaction
Maintaining adequate safety stock levels ensures that products are available when customers need them, reducing the risk of stockouts and enhancing customer satisfaction.
2. Enhanced Supply Chain Resilience
A well-developed risk buffer strategy enhances overall supply chain resilience, allowing businesses to quickly adapt to disruptions and maintain continuous operations.
3. Cost Savings
While holding excess inventory can be costly, the costs associated with stockouts and supply chain disruptions can be even higher.
By optimizing safety stock levels and implementing risk buffer strategies, businesses can achieve a balance that minimizes costs while ensuring smooth operations.
In conclusion, understanding the differences between safety stock and risk buffer and integrating these strategies can significantly improve your inventory management.
By focusing on both inventory levels and broader risk mitigation efforts, businesses can enhance their resilience, reduce the risk of disruptions, and maintain high levels of customer satisfaction.
資料ダウンロード
QCD調達購買管理クラウド「newji」は、調達購買部門で必要なQCD管理全てを備えた、現場特化型兼クラウド型の今世紀最高の購買管理システムとなります。
ユーザー登録
調達購買業務の効率化だけでなく、システムを導入することで、コスト削減や製品・資材のステータス可視化のほか、属人化していた購買情報の共有化による内部不正防止や統制にも役立ちます。
NEWJI DX
製造業に特化したデジタルトランスフォーメーション(DX)の実現を目指す請負開発型のコンサルティングサービスです。AI、iPaaS、および先端の技術を駆使して、製造プロセスの効率化、業務効率化、チームワーク強化、コスト削減、品質向上を実現します。このサービスは、製造業の課題を深く理解し、それに対する最適なデジタルソリューションを提供することで、企業が持続的な成長とイノベーションを達成できるようサポートします。
オンライン講座
製造業、主に購買・調達部門にお勤めの方々に向けた情報を配信しております。
新任の方やベテランの方、管理職を対象とした幅広いコンテンツをご用意しております。
お問い合わせ
コストダウンが利益に直結する術だと理解していても、なかなか前に進めることができない状況。そんな時は、newjiのコストダウン自動化機能で大きく利益貢献しよう!
(Β版非公開)