- お役立ち記事
- The difference between Servo Control and Inverter Control
The difference between Servo Control and Inverter Control
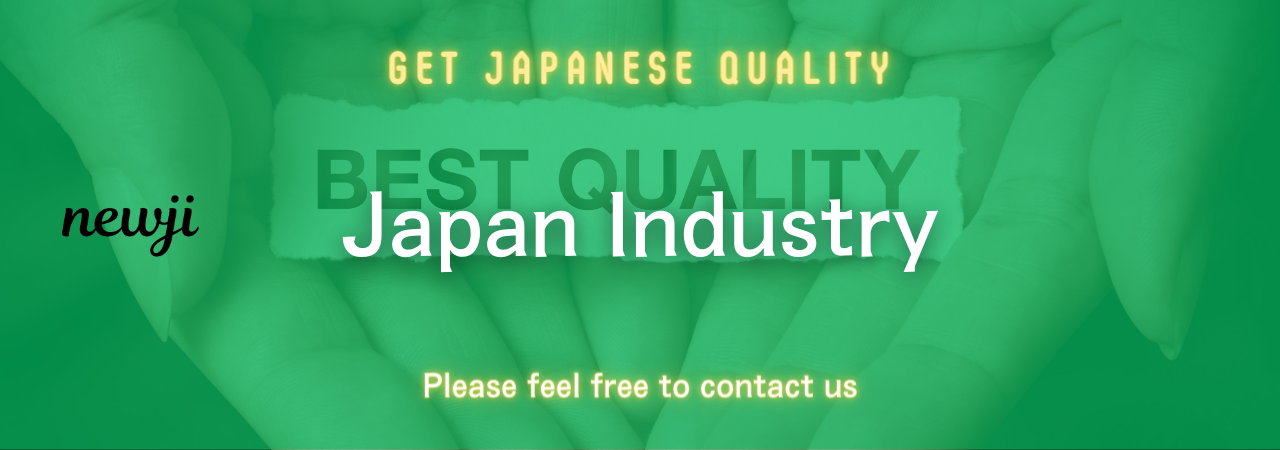
When it comes to controlling the movement and operation of machines, two terms often come up: servo control and inverter control.
Both play integral roles in automation systems, but they each have distinct characteristics that make them suitable for different applications.
Understanding these differences can help you choose the right type of control system for your specific needs.
目次
What is Servo Control?
Servo control refers to a system that uses feedback to achieve precise control of angular or linear position, velocity, and acceleration.
The system usually comprises a servo motor, a controller, and a feedback device such as an encoder.
Components of a Servo System
**Servo Motor**: This is the actuator that responds to the signals from the controller.
**Controller**: This processes the feedback signals and adjusts the motor’s output accordingly.
**Feedback Device**: These sensors provide real-time data to help the controller make accurate adjustments.
How Servo Control Works
The fundamental feature of servo control is its use of feedback.
The feedback device constantly monitors the movement of the motor and sends data back to the controller.
If there’s any deviation from the desired path or speed, the controller makes real-time adjustments to correct it.
This iteration continues until the task is completed to precision.
Applications of Servo Control
Servo control is ideal for applications requiring high precision and dynamic response.
This includes robotic arms, CNC machines, and other automation tasks where exact movements are crucial.
What Is Inverter Control?
Inverter control, often referred to as Variable Frequency Drive (VFD) control, is used to control the speed and torque of electric motors.
It does this by regulating the voltage and frequency of the electrical power supplied to the motor.
Components of an Inverter System
**Inverter**: The core device that converts constant input power into variable output power.
**Electric Motor**: The system often uses an induction motor or synchronous motor.
How Inverter Control Works
In inverter control, the system uses a converter to first transform the input AC power into DC power.
Then, through an inverter mechanism, it converts the DC power back into AC power with a variable frequency and voltage.
By adjusting these parameters, the system can control the motor’s speed and torque.
Applications of Inverter Control
Inverter control is commonly used in applications that need speed control but not necessarily precise positioning.
Examples include HVAC systems, conveyor belts, and various pumping applications.
Main Differences Between Servo Control and Inverter Control
Precision
Servo control offers high precision due to its feedback mechanism, making it ideal for tasks that require exact positioning.
Inverter control, while offering some level of precision, cannot match the accuracy of servo control.
Feedback
Servo systems use real-time feedback to adjust their operations constantly.
In contrast, most inverter systems do not use feedback, although some advanced models incorporate it to improve efficiency and control.
Complexity
Servo systems are generally more complex and require a more sophisticated setup.
Inverter systems are relatively simpler and more straightforward to implement.
Cost
Due to their complexity and the precision they offer, servo systems are usually more expensive.
Inverter systems, being less complex, are generally more cost-effective.
Efficiency
Servo motors tend to be more efficient in terms of power consumption and performance.
In contrast, inverter-driven motors may consume more energy under certain conditions but offer flexibility in applications like fan and pump controls.
Choosing Between Servo Control and Inverter Control
Selecting the right control system depends on your specific needs and the nature of the application.
If your project requires high precision and fast response times, a servo control system is likely the better choice.
However, for applications focused on speed control without the need for exact positioning, an inverter control system will usually suffice.
Factors to Consider
**Application Requirements**: Consider what you need in terms of precision, speed, and torque.
**Budget**: Evaluate your budget, as the costs can significantly differ.
**Complexity**: Determine how comfortable you are with setting up and maintaining complex systems.
Conclusion
Both servo control and inverter control have their own sets of strengths and weaknesses.
Understanding these can help you make an informed decision, ensuring that you choose the best system for your specific needs.
Whether you prioritize precision or speed control, the right system will greatly enhance the performance and efficiency of your application.
資料ダウンロード
QCD調達購買管理クラウド「newji」は、調達購買部門で必要なQCD管理全てを備えた、現場特化型兼クラウド型の今世紀最高の購買管理システムとなります。
ユーザー登録
調達購買業務の効率化だけでなく、システムを導入することで、コスト削減や製品・資材のステータス可視化のほか、属人化していた購買情報の共有化による内部不正防止や統制にも役立ちます。
NEWJI DX
製造業に特化したデジタルトランスフォーメーション(DX)の実現を目指す請負開発型のコンサルティングサービスです。AI、iPaaS、および先端の技術を駆使して、製造プロセスの効率化、業務効率化、チームワーク強化、コスト削減、品質向上を実現します。このサービスは、製造業の課題を深く理解し、それに対する最適なデジタルソリューションを提供することで、企業が持続的な成長とイノベーションを達成できるようサポートします。
オンライン講座
製造業、主に購買・調達部門にお勤めの方々に向けた情報を配信しております。
新任の方やベテランの方、管理職を対象とした幅広いコンテンツをご用意しております。
お問い合わせ
コストダウンが利益に直結する術だと理解していても、なかなか前に進めることができない状況。そんな時は、newjiのコストダウン自動化機能で大きく利益貢献しよう!
(Β版非公開)