- お役立ち記事
- The difference between Six Sigma and Lean Manufacturing
月間76,176名の
製造業ご担当者様が閲覧しています*
*2025年3月31日現在のGoogle Analyticsのデータより
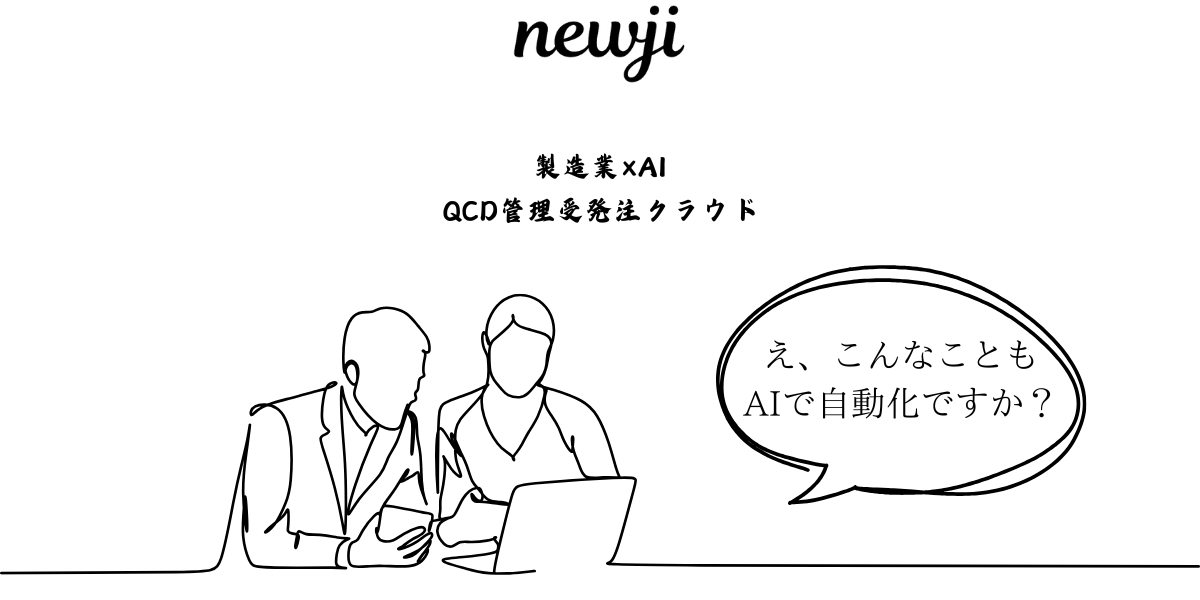
The difference between Six Sigma and Lean Manufacturing
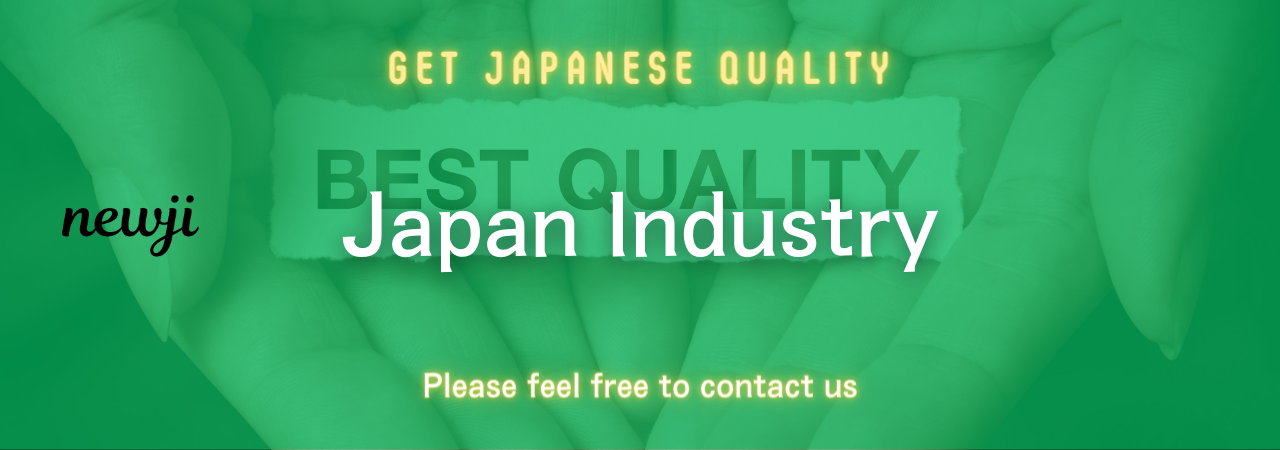
Six Sigma and Lean Manufacturing are two popular methodologies for improving processes and increasing efficiency in businesses.
Both have their roots in manufacturing but have since been applied to various industries.
Understanding the differences between them can help organizations decide which methodology, or combination of methodologies, is best suited for their needs.
目次
What is Six Sigma?
Six Sigma is a data-driven methodology that aims to eliminate defects in any process.
The primary goal is to reduce variability and improve quality by identifying and removing the causes of defects.
Six Sigma uses a set of quality management techniques and statistical methods, and it has a special infrastructure of people within the organization who are experts in these methods.
The Principles of Six Sigma
The core principles of Six Sigma are:
– Customer Focus: Prioritizing customer needs and requirements.
– Measurement: Quantifying every part of the process to identify variations.
– Process Improvement: Continuously improving processes to achieve stable and predictable results.
– Involvement: Engaging all employees at every level of the organization in quality improvement efforts.
The DMAIC Process
Six Sigma projects follow the DMAIC process, which stands for:
– Define: Identify the problem and set goals.
– Measure: Collect data and determine current performance.
– Analyze: Investigate the data to find the root cause of defects.
– Improve: Implement solutions to remove the causes of defects.
– Control: Monitor the changes to ensure sustainable improvements.
What is Lean Manufacturing?
Lean Manufacturing, often simply called Lean, focuses on maximizing value by minimizing waste.
It aims to streamline processes, improve productivity, and deliver better value to customers by eliminating non-value-added activities, known as waste.
The Principles of Lean Manufacturing
The fundamental principles of Lean Manufacturing include:
– Value: Define what is valuable from the customer’s perspective.
– Value Stream: Map all steps in the value stream and eliminate waste.
– Flow: Ensure smooth, uninterrupted flow in the production process.
– Pull: Produce only what is needed when it’s needed.
– Perfection: Continuously strive for improvement in all processes.
The Types of Waste in Lean Manufacturing
Lean identifies eight types of waste, often remembered by the acronym DOWNTIME:
– Defects: Products or services that fail to meet quality standards.
– Overproduction: Producing more than is needed or before it is needed.
– Waiting: Time wasted waiting for the next step in the process.
– Non-Utilized Talent: Underutilizing employee skills and capabilities.
– Transportation: Unnecessary movement of materials or products.
– Inventory: Excess products or materials that are not needed.
– Motion: Unnecessary movements by people.
– Extra-Processing: Doing more work than is necessary to complete a task.
Key Differences Between Six Sigma and Lean Manufacturing
While both Six Sigma and Lean Manufacturing aim to improve processes and efficiency, they have distinct differences in their approaches and methodologies.
Focus and Purpose
Six Sigma focuses primarily on reducing variability and eliminating defects to improve quality.
Its purpose is to achieve stable and predictable process results.
On the other hand, Lean Manufacturing emphasizes eliminating waste and improving flow to maximize value.
Tools and Techniques
Six Sigma relies heavily on statistical tools and techniques to analyze data and identify variations.
It involves more rigorous data analysis and uses specific methodologies like DMAIC.
Lean Manufacturing utilizes various tools to identify and eliminate waste, such as Value Stream Mapping, 5S, and Kaizen.
The focus is more on visualizing processes and making incremental, continuous improvements.
Approach to Problem-Solving
Six Sigma takes a problem-solving approach that is systematic and data-driven.
It involves defining the problem, measuring and analyzing data, implementing solutions, and controlling the changes.
Lean Manufacturing takes a more proactive approach by continuously looking for ways to minimize waste and improve the flow, often involving team-based problem-solving activities like Kaizen events.
Combining Six Sigma and Lean Manufacturing
Many organizations find that combining Six Sigma and Lean Manufacturing, often referred to as Lean Six Sigma, provides the best of both worlds.
This hybrid approach leverages the strengths of both methodologies to achieve enhanced process improvement and operational excellence.
Benefits of Lean Six Sigma
Some of the benefits of integrating Lean and Six Sigma include:
– Improved Quality: By reducing defects and variability, organizations can achieve higher quality standards.
– Enhanced Efficiency: Eliminating waste and optimizing processes leads to more efficient operations.
– Increased Customer Satisfaction: Better quality and faster delivery times improve customer satisfaction.
– Cost Savings: More efficient processes and reduced waste result in cost savings.
– Employee Engagement: Combining the systematic approach of Six Sigma with the collaborative nature of Lean encourages greater employee involvement and engagement.
Conclusion
Understanding the differences between Six Sigma and Lean Manufacturing is crucial for organizations looking to improve their processes and operations.
While Six Sigma focuses on reducing variability and eliminating defects, Lean Manufacturing aims to maximize value by minimizing waste.
Combining these methodologies can provide a comprehensive approach to process improvement, leading to higher quality, efficiency, and customer satisfaction.
資料ダウンロード
QCD管理受発注クラウド「newji」は、受発注部門で必要なQCD管理全てを備えた、現場特化型兼クラウド型の今世紀最高の受発注管理システムとなります。
ユーザー登録
受発注業務の効率化だけでなく、システムを導入することで、コスト削減や製品・資材のステータス可視化のほか、属人化していた受発注情報の共有化による内部不正防止や統制にも役立ちます。
NEWJI DX
製造業に特化したデジタルトランスフォーメーション(DX)の実現を目指す請負開発型のコンサルティングサービスです。AI、iPaaS、および先端の技術を駆使して、製造プロセスの効率化、業務効率化、チームワーク強化、コスト削減、品質向上を実現します。このサービスは、製造業の課題を深く理解し、それに対する最適なデジタルソリューションを提供することで、企業が持続的な成長とイノベーションを達成できるようサポートします。
製造業ニュース解説
製造業、主に購買・調達部門にお勤めの方々に向けた情報を配信しております。
新任の方やベテランの方、管理職を対象とした幅広いコンテンツをご用意しております。
お問い合わせ
コストダウンが利益に直結する術だと理解していても、なかなか前に進めることができない状況。そんな時は、newjiのコストダウン自動化機能で大きく利益貢献しよう!
(β版非公開)