- お役立ち記事
- The difference between Slotting and Broaching
月間76,176名の
製造業ご担当者様が閲覧しています*
*2025年3月31日現在のGoogle Analyticsのデータより
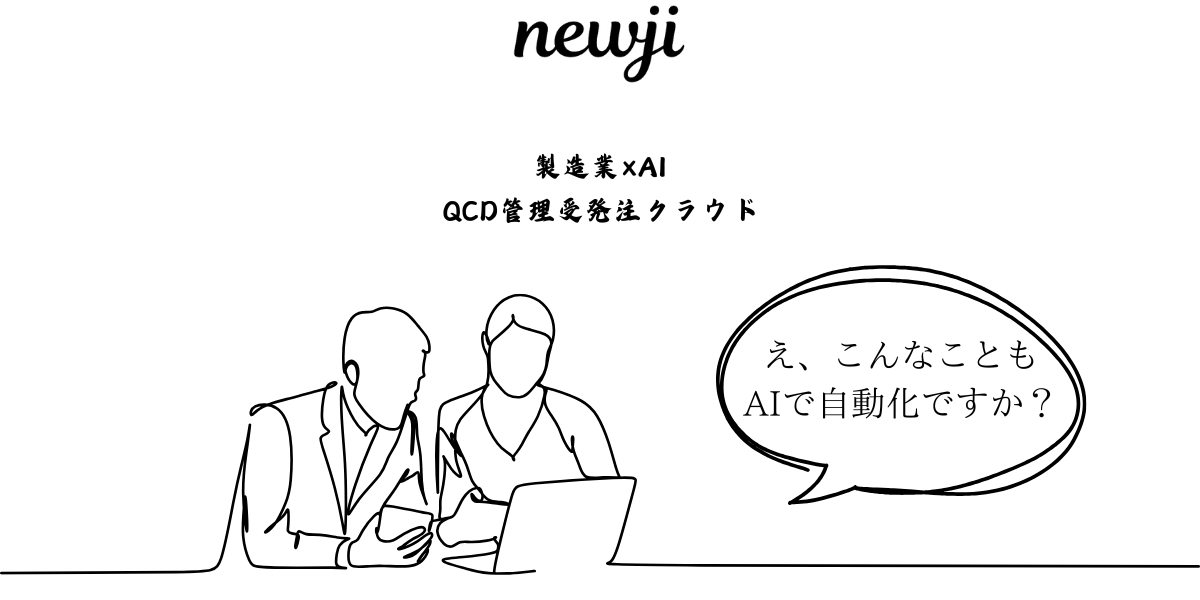
The difference between Slotting and Broaching
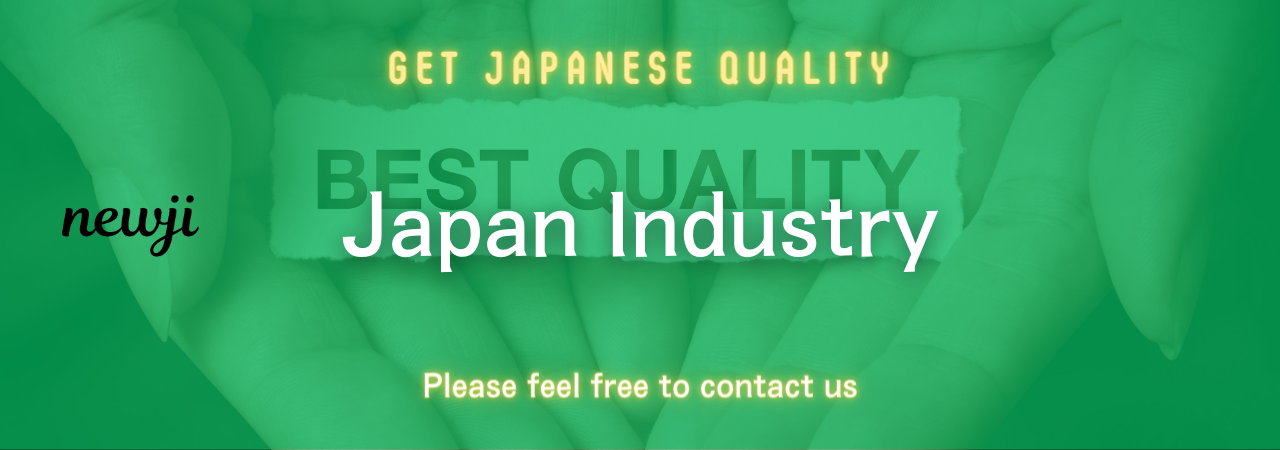
目次
Understanding Slotting
Slotting is a machining process used to cut slots or grooves into a workpiece.
Often employed in mechanical engineering fields, slotting is typically carried out using a slotting machine or vertical shaper.
This process is extremely useful when it comes to making high-precision cuts in metals or other materials.
Slotting machines use a cutting tool to remove material.
The cutting tool moves up and down, making multiple cuts to create a slot.
The workpiece remains stationary while the tool moves, ensuring that the slots are both straight and accurate.
This procedure makes slotting well-suited for creating keyways, splines, and internal gears in various applications.
The key advantage of slotting lies in its ability to machine internal shapes and complex profiles that other processes find difficult to achieve.
Slotting can produce a variety of slot shapes, such as T-slots, dovetail slots, and rectangular slots.
The versatility of slotting makes it an invaluable method for detailed and intricate machining requirements.
How Slotting Works
The tool used in slotting has a vertical motion, moving up and down to remove material from the workpiece.
As the cutting tool moves downward, it removes a small amount of material through shearing action.
When it moves back up, it is repositioned but does not make any cuts.
Once in position, the tool moves down again to continue the process.
Depending on the desired depth and width of the slot, this action may have to be repeated several times.
Computer-controlled slotting machines, or CNC slotting machines, allow for greater precision and can be programmed for complex shapes, making the process significantly faster and more efficient.
Understanding Broaching
Broaching, on the other hand, is a machining process that uses a toothed tool called a broach to remove material.
This process is typically used for precision machining of hard materials.
Broaching can produce very accurate, high-quality finishes, making it ideal for manufacturing parts that require tight tolerances.
A broach is typically a multi-toothed tool.
Each tooth is slightly larger than the previous one, progressively removing material with each pass.
There are two main types of broaching: linear broaching and rotary broaching.
Linear broaching involves the broach moving linearly across the workpiece, while rotary broaching involves the broach rotating around the workpiece.
How Broaching Works
In linear broaching, the broach is pushed or pulled through the workpiece.
The workpiece remains stationary while the broach moves linearly, shearing off material with each tooth.
The first tooth of the broach starts to cut a shallow groove, and each subsequent tooth cuts deeper until the desired depth is achieved.
Rotary broaching, on the other hand, involves a rotating broach that cuts into the workpiece.
This method is often used for creating complex shapes such as hexagons or splines in fastener applications.
Like linear broaching, the multiple teeth progressively remove material.
Broaching is known for its speed and efficiency.
It is particularly suited for high-volume production as each pass of the broach creates a finished product, reducing the need for secondary operations.
Key Differences Between Slotting and Broaching
Slotting and broaching may seem similar at first glance as they both involve removing material from a workpiece.
However, several fundamental differences set these two processes apart.
Method of Material Removal
In slotting, a single cutting tool moves up and down to remove material.
This repeated vertical movement results in the gradual removal of material, making slotting more suited for shallow cuts and internal shapes.
Conversely, broaching uses a multi-toothed tool, with each tooth progressively removing material.
This allows broaching to produce deeper cuts in a single pass.
Speed and Efficiency
Broaching is generally faster and more efficient compared to slotting.
Because broaching removes material in a single pass, it is ideal for high-volume production runs.
Slotting, with its repeated vertical movements, is slower and better suited for smaller production runs or projects requiring detailed internal geometry.
Tolerance and Finish
Broaching often results in higher-quality finishes and more precise tolerances due to its progressive cutting action.
Each tooth of the broach carefully removes a small amount of material, resulting in a smooth surface finish.
Slotting, while capable of achieving good results, may not match the level of precision that broaching can offer, especially for intricate shapes and high-tolerance requirements.
Applications
Slotting is frequently used in creating keyways, splines, and other internal slots that require precision but not necessarily high-speed production.
It is also advantageous for machining complex or hard-to-reach internal features.
Broaching, however, is commonly used in high-precision industries such as automotive and aerospace for producing gears, splines, and other components requiring tight tolerances.
The ability to achieve a high-quality finish in a single pass makes broaching ideal for mass production environments.
Conclusion
Both slotting and broaching serve essential roles in the manufacturing and machining industry.
While slotting is particularly suited for creating internal slots and intricate shapes, broaching excels in high-speed, high-volume production with excellent finish and precision.
Choosing between the two processes depends on the specific requirements of the task, including the type of material, the desired shape, tolerance requirements, and production volume.
Understanding these differences can help engineers and machinists select the best method for their specific machining needs, ultimately leading to higher efficiency and superior product quality.
資料ダウンロード
QCD管理受発注クラウド「newji」は、受発注部門で必要なQCD管理全てを備えた、現場特化型兼クラウド型の今世紀最高の受発注管理システムとなります。
ユーザー登録
受発注業務の効率化だけでなく、システムを導入することで、コスト削減や製品・資材のステータス可視化のほか、属人化していた受発注情報の共有化による内部不正防止や統制にも役立ちます。
NEWJI DX
製造業に特化したデジタルトランスフォーメーション(DX)の実現を目指す請負開発型のコンサルティングサービスです。AI、iPaaS、および先端の技術を駆使して、製造プロセスの効率化、業務効率化、チームワーク強化、コスト削減、品質向上を実現します。このサービスは、製造業の課題を深く理解し、それに対する最適なデジタルソリューションを提供することで、企業が持続的な成長とイノベーションを達成できるようサポートします。
製造業ニュース解説
製造業、主に購買・調達部門にお勤めの方々に向けた情報を配信しております。
新任の方やベテランの方、管理職を対象とした幅広いコンテンツをご用意しております。
お問い合わせ
コストダウンが利益に直結する術だと理解していても、なかなか前に進めることができない状況。そんな時は、newjiのコストダウン自動化機能で大きく利益貢献しよう!
(β版非公開)