- お役立ち記事
- The difference between Spinning and Deep Drawing
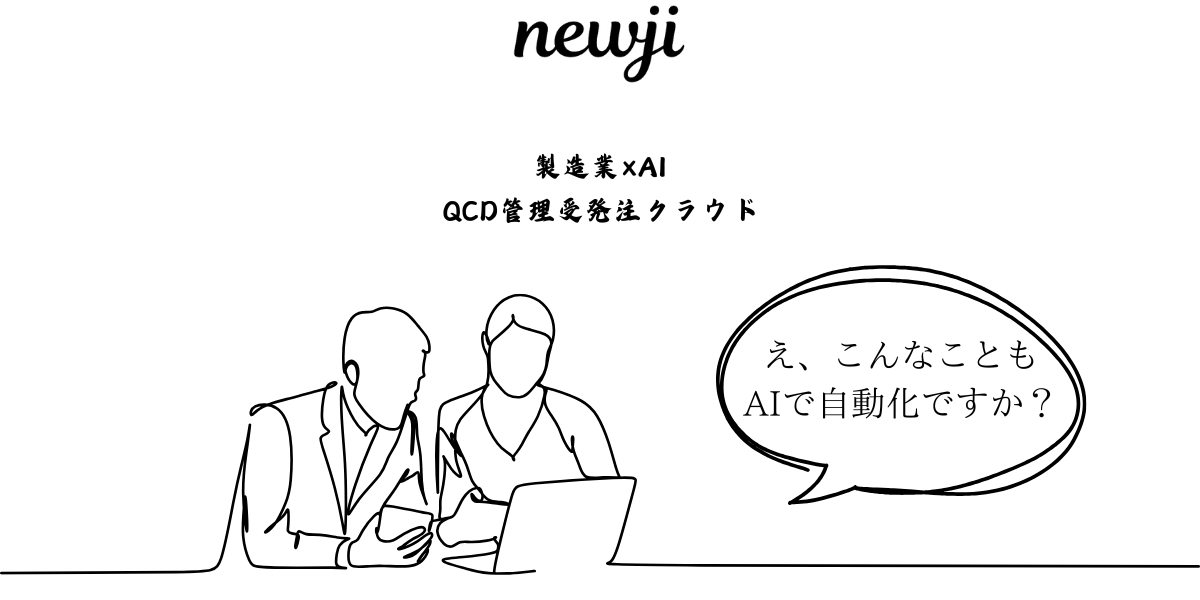
The difference between Spinning and Deep Drawing
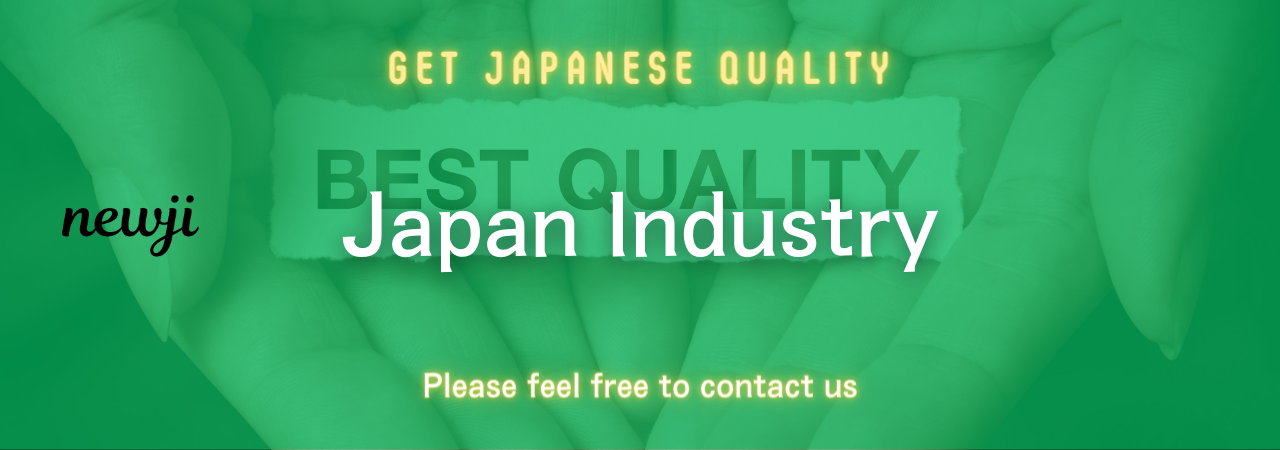
目次
Understanding Spinning
Spinning is a metalworking process where a disc or tube of metal is rotated at high speed.
A roller or a tool then shapes the metal by pressing it against a form, often called a mandrel.
This method is also known as metal spinning or spin forming.
It is widely used to create symmetrical, round objects such as bowls, pots, and even components for aerospace applications.
The process begins with clamping a flat sheet of metal onto a lathe.
As the lathe spins, the metal is gradually pushed over the mandrel using a tool.
This step-by-step approach helps the metal to stretch and mold into the desired shape without tearing or breaking.
The operator can manually control the tool or use automated machinery to perform the task.
One of the key advantages of spinning is its minimal material waste.
Since the metal is stretched rather than cut, very little is lost in the process.
It’s also a cost-effective method for producing small to medium-sized batches of parts.
The tools required for spinning are relatively inexpensive compared to those needed for other metalworking processes like stamping or forging.
Additionally, spinning can produce components with higher strength and uniformity.
However, spinning does have some limitations.
The process is generally less suitable for high-volume production runs.
It also requires skilled operators, especially for more complex shapes.
There’s also a limit to the types of metals that can be spun effectively; while aluminum, brass, and copper are ideal, harder metals can be more challenging to work with.
Delving into Deep Drawing
Deep drawing is another common metal forming technique.
In this process, a sheet of metal is radially drawn into a forming die by the mechanical action of a punch.
The result is a drawn part, usually cylindrical in shape, although other geometries are possible.
Think of items like aluminum cans, kitchen sinks, and automotive components.
The basic principle involves placing a metal blank over a die, and then using a punch to push the material into the die cavity.
The metal flows between the punch and the die, forming the desired shape.
Because the process involves significant deformation, the material must have good ductility.
Materials like aluminum and stainless steel are often used in deep drawing.
One of the main benefits of deep drawing is its capability to produce complex, high-precision parts with a seamless finish.
It’s particularly advantageous for mass production due to the speed and efficiency of the process.
Additionally, deep drawing results in parts that are both strong and lightweight, making it ideal for the automotive and aerospace industries.
Deep drawing can also accommodate a wider range of materials compared to spinning.
Advanced lubrication and coating technologies further enhance the possibility of drawing harder materials.
However, deep drawing has its own set of challenges.
It requires a significant upfront investment in tooling, which can be expensive.
The dies and punches involved must be precisely manufactured and carefully maintained.
Additionally, the process can produce a lot of material waste, especially if the initial blank is significantly larger than the final part.
Comparing Spinning and Deep Drawing
While both spinning and deep drawing aim to shape metal into useful forms, they each have unique advantages and drawbacks.
Understanding these differences can help in choosing the right process for a particular application.
Production Volume
Spinning is generally better suited for low to medium production volumes.
The process is relatively flexible and can be adapted for custom shapes and sizes without significant changes in tooling.
On the other hand, deep drawing excels in high-volume production runs, thanks to its rapid cycle times and ability to produce complex parts consistently.
Material Waste
Material waste is minimal in spinning since the process involves stretching rather than cutting.
Deep drawing, however, often results in more waste due to the need for trimming and cutting excess material.
This factor can significantly affect the cost-effectiveness of the process, especially for expensive materials.
Tooling Costs
Tooling for spinning is generally less expensive compared to deep drawing.
Spinning tools are simpler and more versatile, whereas deep drawing requires highly precise dies and punches.
The upfront costs for deep drawing can be quite high, making it less viable for small production runs.
Component Strength
Both processes can produce strong components, but the strength characteristics can differ.
Spun parts typically have uniform wall thickness and good overall strength due to the metal’s even stretching.
Deep-drawn parts can also be very strong, especially when dealing with cylindrical shapes, but may require additional processes to ensure consistent wall thickness.
Flexibility in Design
Spinning offers more flexibility in terms of design changes.
Adjustments to the process can be made relatively easily without significant alterations to the tooling.
Deep drawing, though capable of producing intricate designs, is less flexible once the tools are set.
Any changes to the design would require new or modified dies and punches, leading to higher costs and longer lead times.
Material Compatibility
Spinning works best with softer metals like aluminum, brass, and copper.
Harder metals can pose challenges and may require specialized equipment.
Deep drawing, meanwhile, can handle a wider variety of materials, including tougher metals like stainless steel.
The use of lubricants and coatings can further expand the range of materials suitable for deep drawing.
Choosing the Right Process
Choosing between spinning and deep drawing depends on several factors:
– The production volume
– Material type
– Design complexity
– Cost considerations.
Spinning is ideal for smaller runs, custom designs, and projects where minimal material waste is crucial.
Deep drawing is more suitable for high-volume production and applications requiring intricate, high-precision components.
Both methods have their unique strengths and limitations.
A thorough understanding of each process will enable you to make an informed decision, ensuring the final product meets your quality, strength, and cost requirements.
In summary, both spinning and deep drawing are versatile metal forming processes with distinct advantages.
Assessing your specific needs and constraints will help in selecting the process that offers the best balance between functionality, efficiency, and cost.
資料ダウンロード
QCD調達購買管理クラウド「newji」は、調達購買部門で必要なQCD管理全てを備えた、現場特化型兼クラウド型の今世紀最高の購買管理システムとなります。
ユーザー登録
調達購買業務の効率化だけでなく、システムを導入することで、コスト削減や製品・資材のステータス可視化のほか、属人化していた購買情報の共有化による内部不正防止や統制にも役立ちます。
NEWJI DX
製造業に特化したデジタルトランスフォーメーション(DX)の実現を目指す請負開発型のコンサルティングサービスです。AI、iPaaS、および先端の技術を駆使して、製造プロセスの効率化、業務効率化、チームワーク強化、コスト削減、品質向上を実現します。このサービスは、製造業の課題を深く理解し、それに対する最適なデジタルソリューションを提供することで、企業が持続的な成長とイノベーションを達成できるようサポートします。
オンライン講座
製造業、主に購買・調達部門にお勤めの方々に向けた情報を配信しております。
新任の方やベテランの方、管理職を対象とした幅広いコンテンツをご用意しております。
お問い合わせ
コストダウンが利益に直結する術だと理解していても、なかなか前に進めることができない状況。そんな時は、newjiのコストダウン自動化機能で大きく利益貢献しよう!
(Β版非公開)