- お役立ち記事
- The difference between Spot Welding and Arc Welding
月間76,176名の
製造業ご担当者様が閲覧しています*
*2025年3月31日現在のGoogle Analyticsのデータより
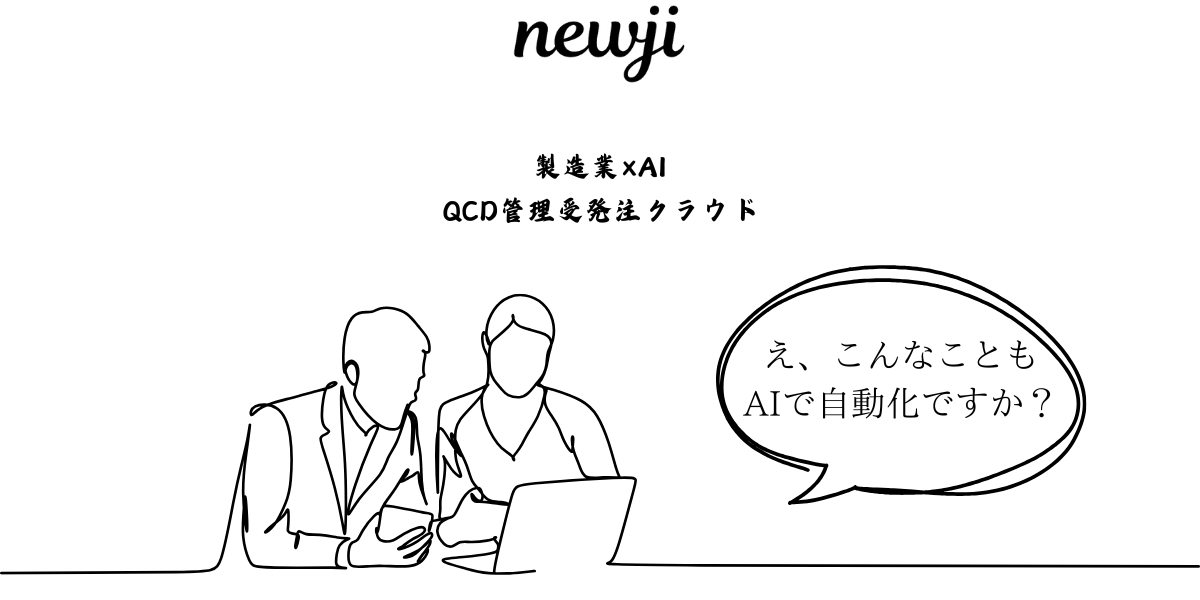
The difference between Spot Welding and Arc Welding
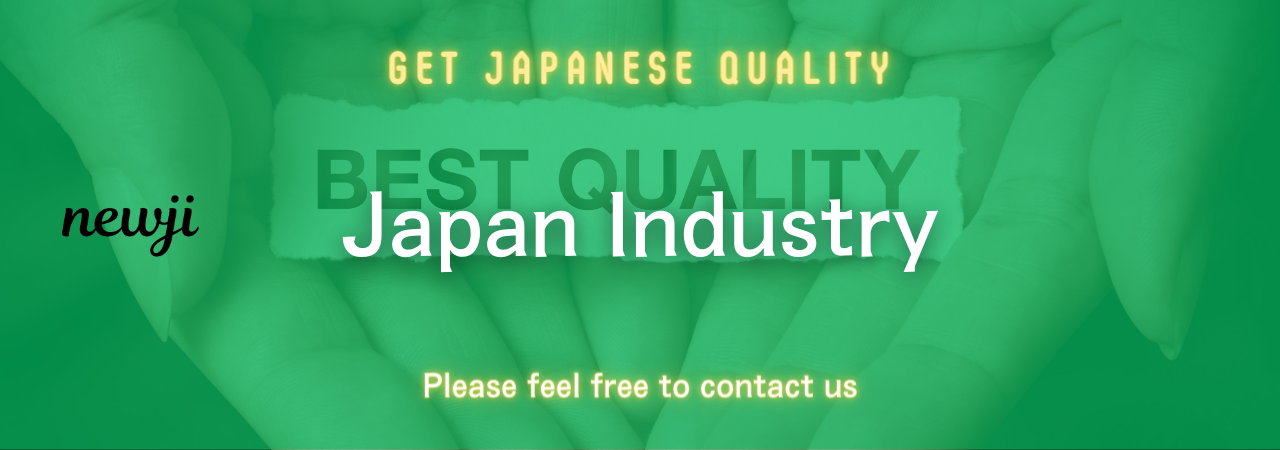
When it comes to joining metals, welding is a widely used technique. Two common types of welding are spot welding and arc welding. Each of these methods has its own unique advantages and is suited for specific applications. In this article, we will explore the differences between spot welding and arc welding, helping you understand which is best for your needs.
目次
What is Spot Welding?
Spot welding is a process used to join two or more metal sheets together by applying pressure and heat. The heat is generated through electrical resistance. This technique is commonly used in industries such as automotive manufacturing, where it is essential to join metal sheets quickly and efficiently.
How Spot Welding Works
During spot welding, two copper alloy electrodes hold and press the metal sheets together. An electrical current passes through the electrodes and the metal, causing resistance. This resistance generates heat, melting the metal at the spot where the electrodes meet. The molten metal cools and solidifies, forming the weld.
Advantages of Spot Welding
Spot welding offers several advantages. Firstly, it is a quick process, making it ideal for high-speed production environments. It also requires less precision compared to other welding techniques, reducing setup time. Additionally, spot welding doesn’t require filler materials, which helps to keep costs low.
Common Applications of Spot Welding
Spot welding is commonly used in the automotive industry to join metal sheets in car bodies. It is also employed in the manufacture of metal furniture, appliances, and various metal components. The process is suitable for materials like steel, stainless steel, and certain aluminum alloys.
What is Arc Welding?
Arc welding is another popular welding technique that uses an electric arc to create heat, which melts the metal and forms a weld. Unlike spot welding, arc welding is versatile and can be used on a variety of metal types and thicknesses.
How Arc Welding Works
In arc welding, an electric arc is formed between an electrode and the metal workpiece. The intense heat from the arc melts both the electrode and the workpiece. The molten electrode material acts as a filler, creating a strong weld as it cools and solidifies.
Advantages of Arc Welding
Arc welding is highly versatile and can be used on different types of metals, including steel, stainless steel, aluminum, and cast iron. It allows for welding in various positions, such as flat, vertical, and overhead. Arc welding also provides strong, durable welds suitable for structural applications.
Common Applications of Arc Welding
Arc welding is commonly used in construction, shipbuilding, aerospace, and general fabrication. It is also utilized in repair and maintenance work, making it a valuable tool for industries that require durable and reliable welds.
Key Differences Between Spot Welding and Arc Welding
While both spot welding and arc welding are techniques for joining metals, they have distinct differences that set them apart.
Process and Technique
Spot welding focuses on joining metal sheets at specific points using pressure and electrical resistance. Arc welding, on the other hand, uses an electric arc to melt the metal and filler material, creating a continuous weld.
Speed and Efficiency
Spot welding is faster and more efficient for mass production, making it ideal for industries like automotive manufacturing. Arc welding, although slightly slower, offers versatility and can be used on various metal types and thicknesses.
Material and Thickness Compatibility
Spot welding is best suited for thin metal sheets, typically up to 3 millimeters thick. Arc welding, on the other hand, can handle a wider range of metal thicknesses, making it more versatile for different applications.
Joint Strength
Arc welding provides stronger weld joints compared to spot welding. This is because arc welding creates a continuous weld, allowing for greater structural integrity. Spot welding is still strong enough for applications requiring the joining of thin sheets.
Equipment and Costs
Spot welding equipment is generally more specialized and may come with higher initial costs. However, it does not require filler materials, reducing overall expenses. Arc welding equipment is more versatile and can be used for various welding jobs but may require additional costs for filler materials.
Choosing the Right Welding Method
When choosing between spot welding and arc welding, it is important to consider the specific requirements of your project.
Consider the Material
Evaluate the type of metal and its thickness. For joining thin sheets of metal, spot welding may be the most efficient choice. If you need to weld thicker materials or different types of metals, arc welding is likely the better option.
Evaluate the Application
Consider the end use of the welded product. For applications needing high structural integrity, such as construction or shipbuilding, arc welding provides the necessary strength. For high-speed production environments with thin sheet metals, spot welding is more suitable.
Analyze Costs and Equipment
Take into account the initial costs of equipment and ongoing expenses. If cost-efficiency is a priority, spot welding might be advantageous due to the lack of filler materials. However, if you need versatility in your welding tasks, investing in arc welding equipment could be more beneficial in the long run.
Conclusion
Spot welding and arc welding are both valuable techniques for joining metals, each with its own set of advantages and specific uses. Spot welding is ideal for quick, efficient joining of thin metal sheets, while arc welding offers versatility and strength for various applications. By understanding the differences between these welding methods, you can make an informed decision and choose the right welding technique for your needs.
資料ダウンロード
QCD管理受発注クラウド「newji」は、受発注部門で必要なQCD管理全てを備えた、現場特化型兼クラウド型の今世紀最高の受発注管理システムとなります。
ユーザー登録
受発注業務の効率化だけでなく、システムを導入することで、コスト削減や製品・資材のステータス可視化のほか、属人化していた受発注情報の共有化による内部不正防止や統制にも役立ちます。
NEWJI DX
製造業に特化したデジタルトランスフォーメーション(DX)の実現を目指す請負開発型のコンサルティングサービスです。AI、iPaaS、および先端の技術を駆使して、製造プロセスの効率化、業務効率化、チームワーク強化、コスト削減、品質向上を実現します。このサービスは、製造業の課題を深く理解し、それに対する最適なデジタルソリューションを提供することで、企業が持続的な成長とイノベーションを達成できるようサポートします。
製造業ニュース解説
製造業、主に購買・調達部門にお勤めの方々に向けた情報を配信しております。
新任の方やベテランの方、管理職を対象とした幅広いコンテンツをご用意しております。
お問い合わせ
コストダウンが利益に直結する術だと理解していても、なかなか前に進めることができない状況。そんな時は、newjiのコストダウン自動化機能で大きく利益貢献しよう!
(β版非公開)