- お役立ち記事
- The difference between Spot Welding and Seam Welding
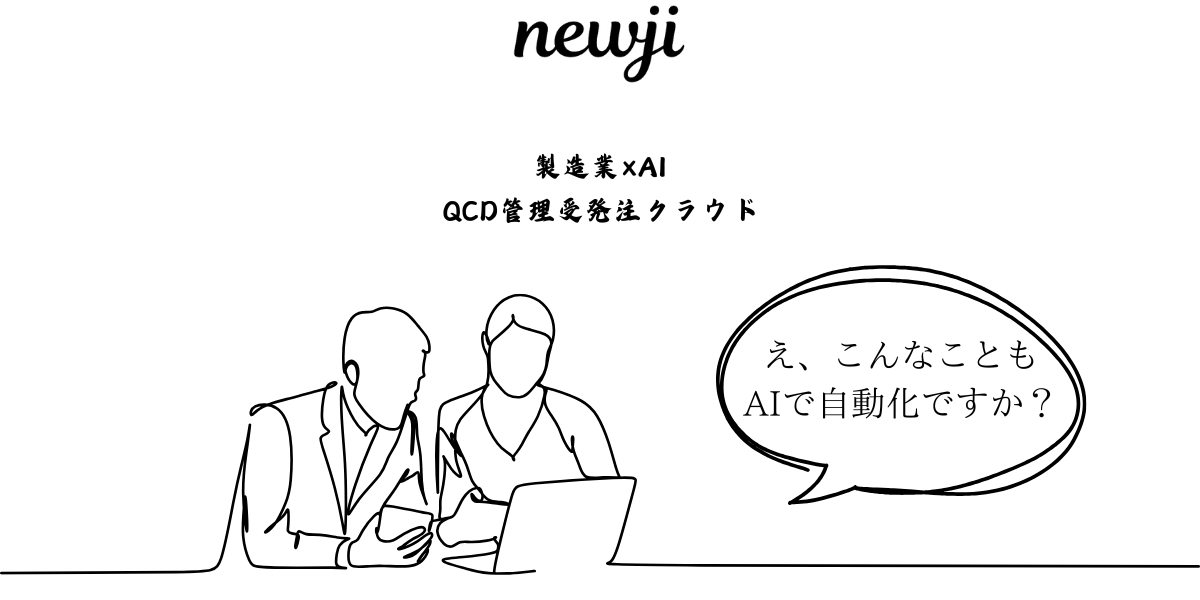
The difference between Spot Welding and Seam Welding
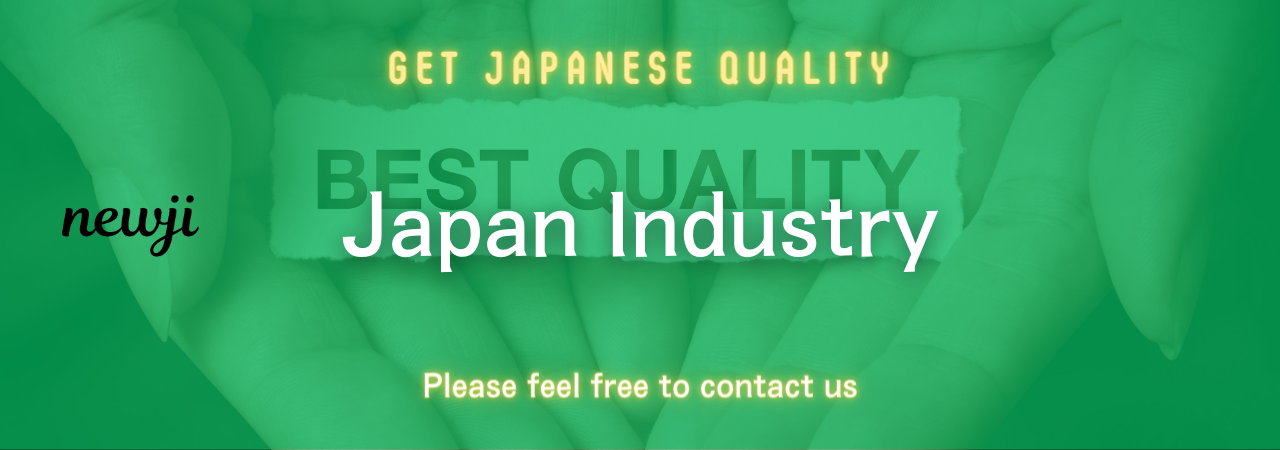
目次
Understanding Welding Basics
Welding is a process used to fuse two materials, usually metals, by heating them to a melting point.
There are various types of welding techniques, each suited to specific applications and materials.
Two of the most commonly used welding methods are spot welding and seam welding.
Despite their similarities, they have distinct differences and uses.
Spot Welding: A Quick and Powerful Method
Spot welding is a resistance welding process commonly used in manufacturing.
It involves applying pressure and electric current to the weld area for a short time.
This causes the metals to melt and fuse together at a single point.
Due to its quick nature, spot welding is highly efficient and widely utilized in automotive and construction industries.
How Spot Welding Works
Spot welding utilizes electrodes made of copper.
These electrodes clamp the workpieces together, applying pressure to both sides of the weld area.
A strong electric current passes through the electrodes, creating heat due to electrical resistance.
The heat causes the metal to melt and forms a weld nugget where the two pieces join.
As the material cools, a solid weld is formed.
Advantages of Spot Welding
One significant advantage of spot welding is its speed.
The process takes only a few seconds, making it ideal for mass production.
It is also highly efficient, as it requires no filler material and minimal clean-up.
Spot welding offers strong welds, provided the materials are suitable and correctly aligned.
Limitations of Spot Welding
Despite its strengths, spot welding has limitations.
It is best suited for thin sheets of metal; thicker materials may require different welding methods.
The process is mostly limited to overlapping joints.
Quality control can be challenging, as improper alignment or insufficient pressure can lead to weak welds.
Seam Welding: Continuous and Sturdy
Seam welding, another resistance welding technique, is similar to spot welding but creates a continuous weld.
This method is often chosen for applications requiring leak-proof and long weld seams.
How Seam Welding Works
Seam welding uses a pair of rotating wheel electrodes.
These wheels clamp the material together and roll along the joint.
As the wheels move, they apply pressure and an electric current.
The resistance heats the metal, creating a continuous weld along the seam.
Seam welding is frequently used to manufacture liquid or gas-tight containers, such as fuel tanks and pipes.
Advantages of Seam Welding
The continuous nature of seam welding makes it ideal for applications requiring consistent and extended welds.
It ensures strong, leak-proof joints, making it suitable for producing sealed containers.
The method is efficient for long, straight welds, providing uniformity and strength along the entire seam.
Limitations of Seam Welding
Seam welding is generally limited to straight or gently curved joints, as the wheels must roll smoothly along the seam.
It requires more complex equipment compared to spot welding.
Additionally, seam welding can be less suitable for thick materials, as excessive heating can occur.
Comparative Analysis
Understanding the differences between spot welding and seam welding helps in choosing the right technique for specific applications.
Both methods share similarities, employing resistance and pressure to fuse metals.
However, their distinct features set them apart.
Application Suitability
Spot welding is perfect for joining thin sheets, especially in automotive bodies, and in areas where multiple overlapping joints are required.
Seam welding, on the other hand, is best for creating long, leak-proof seams in containers used to hold liquids or gases.
Choosing between the two depends on the specific requirements of the project.
Efficiency and Equipment
Both welding methods are efficient, but spot welding often requires simpler equipment.
Seam welding involves more complex machinery, given the need for rotating electrodes.
The setup costs for seam welding can be higher, but it provides continuous welds, whereas spot welding excels in quick, localized joints.
Joint Strength
The strength of the welds is a crucial factor.
Spot welding creates strong, singular points, making it effective for assemblies where multiple spot welds distribute the load.
Seam welding produces a continuous weld, ensuring uniform strength along the entire joint.
This is vital in applications requiring airtight or watertight seals.
Conclusion
Selecting between spot welding and seam welding depends on the nature of the job and the properties of the materials involved.
Spot welding is distinguished by its speed and efficiency for small, individual welds, while seam welding provides robust, continuous seams for leak-proof applications.
Understanding these differences allows manufacturers to make informed decisions and ensures the highest quality and durability in their products.
資料ダウンロード
QCD調達購買管理クラウド「newji」は、調達購買部門で必要なQCD管理全てを備えた、現場特化型兼クラウド型の今世紀最高の購買管理システムとなります。
ユーザー登録
調達購買業務の効率化だけでなく、システムを導入することで、コスト削減や製品・資材のステータス可視化のほか、属人化していた購買情報の共有化による内部不正防止や統制にも役立ちます。
NEWJI DX
製造業に特化したデジタルトランスフォーメーション(DX)の実現を目指す請負開発型のコンサルティングサービスです。AI、iPaaS、および先端の技術を駆使して、製造プロセスの効率化、業務効率化、チームワーク強化、コスト削減、品質向上を実現します。このサービスは、製造業の課題を深く理解し、それに対する最適なデジタルソリューションを提供することで、企業が持続的な成長とイノベーションを達成できるようサポートします。
オンライン講座
製造業、主に購買・調達部門にお勤めの方々に向けた情報を配信しております。
新任の方やベテランの方、管理職を対象とした幅広いコンテンツをご用意しております。
お問い合わせ
コストダウンが利益に直結する術だと理解していても、なかなか前に進めることができない状況。そんな時は、newjiのコストダウン自動化機能で大きく利益貢献しよう!
(Β版非公開)