- お役立ち記事
- The difference between Standard Cost and Actual Cost
The difference between Standard Cost and Actual Cost
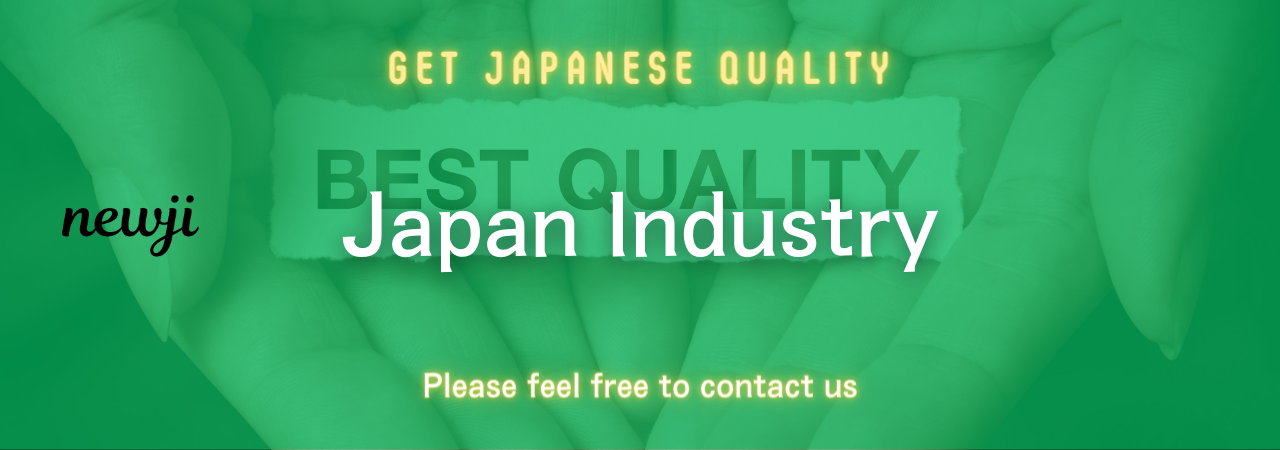
Understanding the difference between standard cost and actual cost is crucial for businesses aiming to streamline their budgeting and cost management processes.
Both these concepts are foundational in cost accounting and can significantly impact the financial health of an organization.
Let’s dive deeper into both standard cost and actual cost to understand their differences and importance.
目次
What is Standard Cost?
Standard cost is a predetermined or estimated cost that companies set for their products or services.
It is based on various factors such as historical data, industry standards, and expected future conditions.
By setting a standard cost, businesses can create a benchmark for evaluating their performance.
For instance, when producing a widget, a company might estimate the cost of raw materials, labor, and overhead needed to produce that widget.
These estimates become the standard costs.
Standard costs serve multiple purposes, including budgeting, performance measurement, and cost control.
By comparing actual costs to standard costs, businesses can identify variances and understand where they are overspending or underspending.
Components of Standard Cost
Direct Materials
Direct materials refer to the raw inputs directly used in the manufacturing of a product.
The standard cost for direct materials includes the estimated price and quantity needed for production.
For example, if producing a table requires wood, nails, and varnish, the standard cost will estimate the amount and price of wood, nails, and varnish needed per table.
Direct Labor
Direct labor is the workforce required to convert raw materials into finished products.
The standard cost for direct labor estimates the number of labor hours needed and the wage rate per hour.
For example, if one table requires 2 hours of labor and the wage rate is $20 per hour, the standard labor cost for one table would be $40.
Manufacturing Overhead
Manufacturing overhead includes all other indirect costs associated with production.
These can be utilities, rent, equipment maintenance, and more.
The standard cost for manufacturing overhead is often calculated as a percentage of direct labor costs or direct materials costs.
What is Actual Cost?
Actual cost is the true amount spent to produce a product or service.
It is the real cost incurred after the production process has been completed.
Unlike standard costs, actual costs reflect real-time spending and can vary due to unforeseen circumstances, such as price fluctuations in raw materials or changes in labor rates.
Actual costs are vital for accurate financial reporting and analysis.
By comparing actual costs with standard costs, businesses can identify variances and investigate the reasons for these differences.
This process helps companies make informed decisions and adjust their strategies to improve efficiency and reduce costs.
Components of Actual Cost
Actual Direct Materials
The actual cost of direct materials is the true amount paid for the raw materials used in production.
These costs can vary due to market price changes, supplier pricing, and quantity discounts or additional costs incurred during procurement.
Actual Direct Labor
The actual cost of direct labor includes the wages paid to workers and any additional costs, such as overtime or training expenses.
This cost can vary depending on labor efficiency, workforce availability, and changes in wage rates.
Actual Manufacturing Overhead
The actual cost of manufacturing overhead encompasses all indirect production costs incurred during the production process.
These costs can fluctuate due to changes in utility rates, maintenance expenses, or other unforeseen factors that impact production.
Comparing Standard Cost and Actual Cost
Variance Analysis
Variance analysis is the process of comparing standard costs to actual costs to identify discrepancies.
These discrepancies, known as variances, can be either favorable or unfavorable.
A favorable variance occurs when the actual cost is lower than the standard cost, while an unfavorable variance occurs when the actual cost is higher than the standard cost.
Variance analysis helps businesses pinpoint areas where they are overspending or underspending and take corrective actions.
For instance, if the actual cost of direct materials is higher than the standard cost, a company might investigate its procurement process or negotiate better prices with suppliers to reduce costs.
Budgeting and Forecasting
Standard costs are instrumental in budgeting and forecasting.
By establishing standard costs, businesses can create more accurate budgets and financial forecasts.
These budgets serve as a roadmap for financial planning and help businesses allocate resources efficiently.
On the other hand, actual costs provide real-time data for tracking spending and evaluating budget performance.
Comparing actual costs to budgeted costs helps businesses stay on track and make necessary adjustments to achieve their financial goals.
Cost Control
Cost control is another area where the difference between standard and actual costs plays a crucial role.
Standard costs provide a benchmark for evaluating performance and implementing cost-control measures.
By monitoring variances, businesses can identify inefficiencies, streamline processes, and reduce waste.
Actual costs, on the other hand, provide insights into real-time cost management.
By analyzing actual costs, businesses can identify cost-saving opportunities, negotiate better deals with suppliers, and implement strategies to improve operational efficiency.
Importance of Understanding the Difference
Understanding the difference between standard cost and actual cost is essential for effective cost management and financial planning.
By comparing standard and actual costs, businesses can identify variances, take corrective actions, and improve efficiency.
This understanding also helps businesses create accurate budgets, allocate resources wisely, and achieve their financial goals.
In summary, both standard cost and actual cost are pivotal components of cost accounting.
While standard costs provide a benchmark for budgeting and performance evaluation, actual costs offer real-time insights into spending and cost management.
By leveraging both concepts, businesses can enhance their financial performance, reduce costs, and achieve long-term success.
資料ダウンロード
QCD調達購買管理クラウド「newji」は、調達購買部門で必要なQCD管理全てを備えた、現場特化型兼クラウド型の今世紀最高の購買管理システムとなります。
ユーザー登録
調達購買業務の効率化だけでなく、システムを導入することで、コスト削減や製品・資材のステータス可視化のほか、属人化していた購買情報の共有化による内部不正防止や統制にも役立ちます。
NEWJI DX
製造業に特化したデジタルトランスフォーメーション(DX)の実現を目指す請負開発型のコンサルティングサービスです。AI、iPaaS、および先端の技術を駆使して、製造プロセスの効率化、業務効率化、チームワーク強化、コスト削減、品質向上を実現します。このサービスは、製造業の課題を深く理解し、それに対する最適なデジタルソリューションを提供することで、企業が持続的な成長とイノベーションを達成できるようサポートします。
オンライン講座
製造業、主に購買・調達部門にお勤めの方々に向けた情報を配信しております。
新任の方やベテランの方、管理職を対象とした幅広いコンテンツをご用意しております。
お問い合わせ
コストダウンが利益に直結する術だと理解していても、なかなか前に進めることができない状況。そんな時は、newjiのコストダウン自動化機能で大きく利益貢献しよう!
(Β版非公開)