- お役立ち記事
- The difference between Standard Operating Procedures (SOP) and Work Instructions
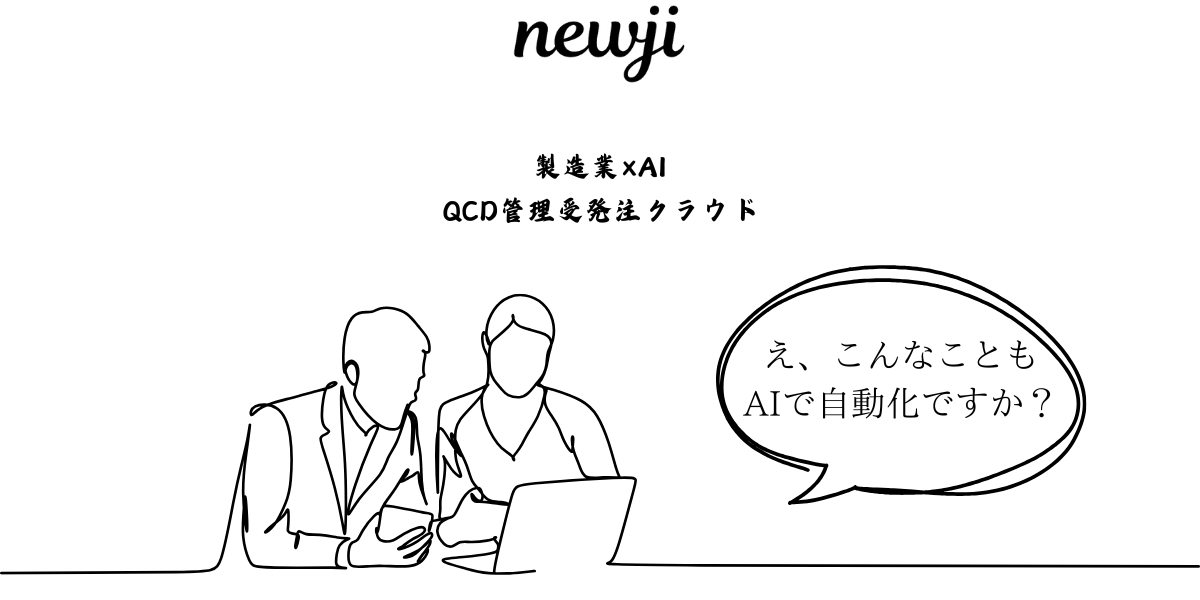
The difference between Standard Operating Procedures (SOP) and Work Instructions
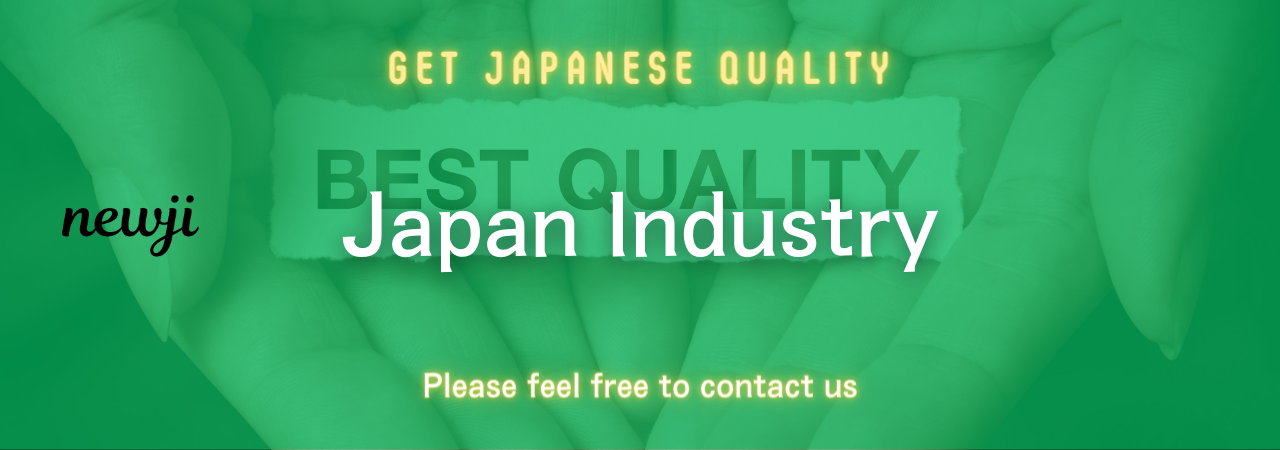
When it comes to running a business efficiently, having clear guidelines and procedures is essential.
Two critical documents that help in this regard are Standard Operating Procedures (SOP) and Work Instructions.
While they might seem similar at first glance, they serve different purposes and offer unique benefits.
Understanding the distinction between SOPs and Work Instructions can significantly improve your organization’s operational effectiveness.
目次
What Are Standard Operating Procedures (SOP)?
Standard Operating Procedures, commonly known as SOPs, are comprehensive guidelines that outline the processes and activities within an organization.
They provide a standard way to perform tasks, ensuring consistency and quality.
SOPs are typically broader in scope and cover multiple aspects of a specific procedure or policy.
An SOP serves as a high-level document, offering a big-picture view of how tasks should be performed.
It encompasses various components such as:
Purpose and Scope
The purpose and scope section explains why the SOP exists and whom it applies to.
This section provides context for the document and helps employees understand its importance.
Roles and Responsibilities
This part outlines who is responsible for carrying out each task within the procedure.
Clearly defining roles helps minimize confusion and ensures accountability.
Step-by-Step Procedures
While not as detailed as Work Instructions, SOPs still offer a step-by-step overview of the procedure.
They give enough information to understand the flow of tasks.
References and Documentation
SOPs may include references to other documents, manuals, or guidelines that are relevant to the procedure.
This section ensures that employees have all the information they need to perform their tasks correctly.
What Are Work Instructions?
Work Instructions are detailed, step-by-step guides that explain how to perform specific tasks.
They are more granular and targeted compared to SOPs.
Where an SOP might outline the procedure for assembling a product, Work Instructions would provide the exact steps and tools needed for each part of the assembly process.
Work Instructions are indispensable for training new employees and for tasks that require high precision.
Here are the primary components of Work Instructions:
Introduction
The introduction provides a brief overview of the task and its importance.
It sets the context for the detailed steps that follow.
Tools and Materials
This section lists all the tools, materials, or equipment necessary to complete the task.
Having a clear list ensures that employees are adequately prepared before they start working.
Detailed Steps
Work Instructions provide an itemized list of each step required to complete the task.
They often include visual aids such as diagrams, illustrations, or photos to enhance understanding.
Safety Guidelines
Safety is paramount in any task, so this section outlines any safety precautions that employees must follow.
This helps in minimizing risks and ensuring a safe working environment.
The Key Differences Between SOPs and Work Instructions
Scope and Detail
The most significant difference between SOPs and Work Instructions lies in their scope and level of detail.
SOPs are broader and cover multiple aspects of a procedure, while Work Instructions are narrowly focused and provide exhaustive details for a specific task.
Purpose
SOPs serve as a high-level guide to ensure standardization and consistency across the organization.
They help in maintaining quality and compliance with industry standards.
In contrast, Work Instructions serve as a training tool and a step-by-step guide to achieving precise results in a specific task.
Flexibility
SOPs are generally more flexible.
They offer a structured yet adaptable framework for performing tasks.
Work Instructions, however, are highly detailed and leave little room for interpretation.
They are designed to be followed exactly as written.
The Importance of Both Documents
Both SOPs and Work Instructions are crucial for different aspects of business operations.
SOPs are vital for maintaining overall quality and consistency.
They serve as a reference point for employees and ensure that everyone is on the same page regarding company procedures.
Work Instructions, on the other hand, are essential for tasks that require specific instructions and precision.
They are invaluable for training new employees and reducing the margin of error in complex tasks.
Implementing SOPs and Work Instructions
Training and Awareness
To effectively implement SOPs and Work Instructions, it’s essential to train employees thoroughly.
They should understand why these documents are important and how to use them correctly.
Regular Updates
Both SOPs and Work Instructions should be regularly reviewed and updated to reflect any changes in procedures or industry standards.
Keeping these documents current ensures that they remain effective.
User Feedback
Encourage employees to provide feedback on the clarity and usefulness of SOPs and Work Instructions.
This feedback can be invaluable for making necessary adjustments and improvements.
Conclusion
Standard Operating Procedures (SOPs) and Work Instructions are indispensable tools for any organization.
While they serve different purposes, both contribute to the overall efficiency, quality, and safety of business operations.
Understanding their differences and properly implementing them can significantly enhance your organization’s operational effectiveness.
By clearly defining tasks and responsibilities, minimizing errors, and ensuring consistency, SOPs and Work Instructions can help your business achieve its goals more efficiently.
Regular updates and employee training are essential to keep these documents effective and relevant.
With the right approach, these tools can make a substantial difference in your organization’s success.
資料ダウンロード
QCD調達購買管理クラウド「newji」は、調達購買部門で必要なQCD管理全てを備えた、現場特化型兼クラウド型の今世紀最高の購買管理システムとなります。
ユーザー登録
調達購買業務の効率化だけでなく、システムを導入することで、コスト削減や製品・資材のステータス可視化のほか、属人化していた購買情報の共有化による内部不正防止や統制にも役立ちます。
NEWJI DX
製造業に特化したデジタルトランスフォーメーション(DX)の実現を目指す請負開発型のコンサルティングサービスです。AI、iPaaS、および先端の技術を駆使して、製造プロセスの効率化、業務効率化、チームワーク強化、コスト削減、品質向上を実現します。このサービスは、製造業の課題を深く理解し、それに対する最適なデジタルソリューションを提供することで、企業が持続的な成長とイノベーションを達成できるようサポートします。
オンライン講座
製造業、主に購買・調達部門にお勤めの方々に向けた情報を配信しております。
新任の方やベテランの方、管理職を対象とした幅広いコンテンツをご用意しております。
お問い合わせ
コストダウンが利益に直結する術だと理解していても、なかなか前に進めることができない状況。そんな時は、newjiのコストダウン自動化機能で大きく利益貢献しよう!
(Β版非公開)