- お役立ち記事
- The difference between Standard Work and Work Standard
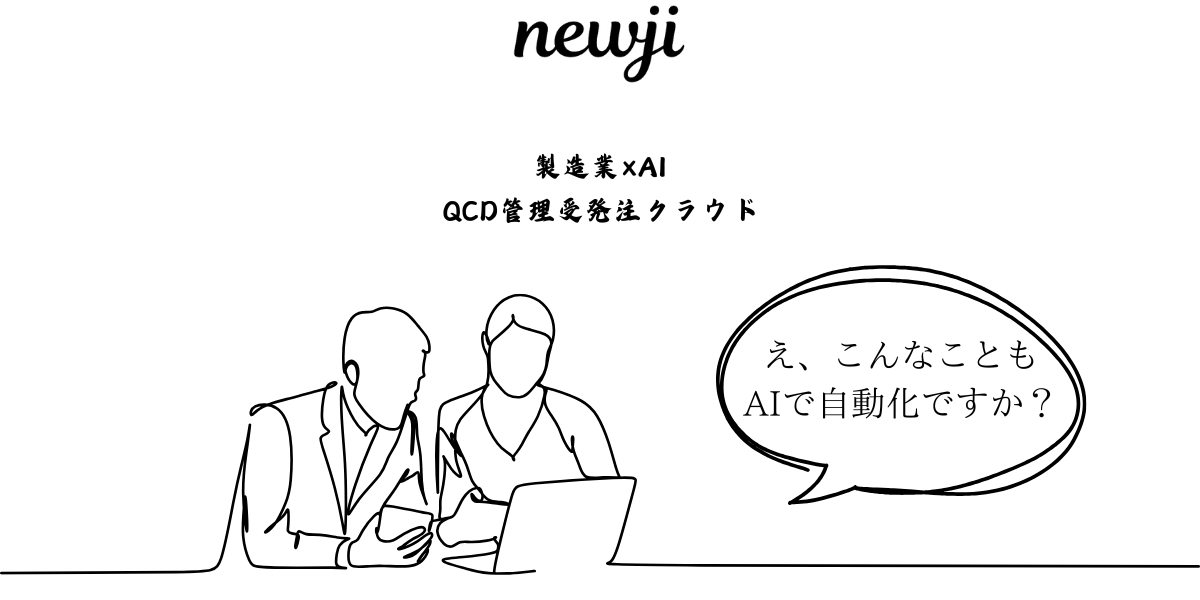
The difference between Standard Work and Work Standard
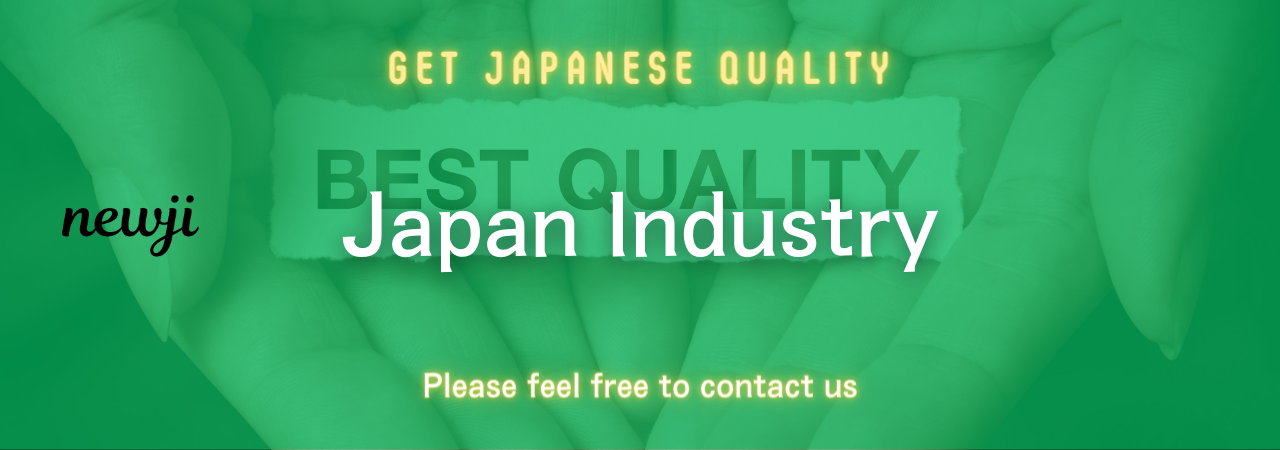
When we talk about improving efficiency in the workplace, terms like “Standard Work” and “Work Standard” often come up.
They might sound similar, but they really mean different things.
Let’s dive into the distinction between these two concepts and why they matter for any organization striving for excellence.
目次
Understanding Standard Work
Standard Work is a term used to describe the most efficient and effective way to complete a particular task.
It includes detailed instructions that outline every step of an activity, ensuring consistency across the board.
Standard Work is a critical component of Lean manufacturing and other process improvement methodologies.
The Key Components of Standard Work
Standard Work typically comprises three main elements:
1. **Takt Time**: This is the rate at which products need to be produced to meet customer demand.
2. **Work Sequence**: The specific order of tasks that need to be followed.
3. **Standard Inventory**: The minimum amount of materials and supplies required to keep the process running smoothly.
When all three elements are well-defined and adhered to, it ensures that every worker performs the task in the same, optimal way.
This results in improved quality, reduced waste, and higher efficiency.
Advantages of Standard Work
One of the biggest benefits of Standard Work is that it brings consistency.
When everyone follows the same steps, the outcome is predictable.
This makes it easier to identify issues and implement improvements.
Another advantage is training.
New employees can quickly get up to speed by following the documented procedures.
It serves as a baseline for measuring performance, which is crucial for continuous improvement.
Understanding Work Standard
On the other hand, Work Standard refers to the norms and criteria that define acceptable performance levels for a given task.
While Standard Work provides the “how,” Work Standard provides the “what.”
It sets the benchmarks for quality, speed, and efficiency that need to be achieved.
The Elements of Work Standard
Work Standard generally includes:
1. **Quality Standards**: The level of quality that the products or services must meet.
2. **Time Standards**: The amount of time allowed to complete a task.
3. **Performance Metrics**: The measurements used to gauge efficiency, such as error rates or output levels.
These criteria help organizations maintain a consistent level of excellence.
They also serve as a basis for evaluating worker performance and identifying areas needing improvement.
Benefits of Work Standard
The primary benefit of Work Standard is quality assurance.
By setting clear criteria, it ensures that every product or service meets customer expectations.
It also helps in identifying deviations from the norm, allowing for quick corrective actions.
Work Standard facilitates performance assessment.
By having predefined metrics, managers can easily evaluate whether employees are meeting the expected performance levels.
This aids in identifying high-performers and those who may need additional training or support.
Key Differences
While both concepts aim to improve efficiency and quality, their roles are distinct.
**Purpose**:
– **Standard Work**: Defines the best way to perform a task.
– **Work Standard**: Sets the criteria for acceptable performance.
**Focus**:
– **Standard Work**: The “how” of task completion.
– **Work Standard**: The “what” of performance expectations.
**Application**:
– **Standard Work**: Used for documenting procedures and training.
– **Work Standard**: Used for evaluating performance and quality.
When to Use Each
Understanding when to apply each concept can significantly impact your organization’s efficiency and effectiveness.
**Use Standard Work**:
– When documenting procedures to ensure consistency.
– When training new employees.
– When looking to improve existing workflows.
**Use Work Standard**:
– When defining performance metrics and expectations.
– When assessing the quality of products or services.
– When evaluating employee performance.
Ideally, both concepts should be used together.
Standard Work ensures that tasks are performed consistently, while Work Standard ensures that the performance of these tasks meets predefined criteria.
Together, they create a comprehensive framework for operational excellence.
Implementing Standard Work and Work Standard
Successfully implementing these concepts requires a thoughtful approach.
Steps to Implement Standard Work
1. **Identify Key Processes**: Focus on processes that have the most impact on your operations.
2. **Document Procedures**: Capture every step of the task in detail.
3. **Train Employees**: Ensure that everyone follows the documented procedures.
4. **Monitor and Improve**: Continuously observe the process and make necessary adjustments.
Steps to Implement Work Standard
1. **Define Quality and Performance Criteria**: Establish clear benchmarks for acceptable performance.
2. **Communicate Expectations**: Make sure all employees understand the criteria.
3. **Measure Performance**: Regularly assess whether employees are meeting the benchmarks.
4. **Provide Feedback**: Offer constructive feedback to help employees improve.
Case Studies
Let’s look at a couple of examples to explain the practical applications of Standard Work and Work Standard.
Example 1: Manufacturing
In a manufacturing setting, Standard Work might involve documenting the exact steps for assembling a product.
From selecting materials to using specific tools, everything is detailed to ensure consistency.
The Work Standard in this scenario would set the acceptable tolerances and quality criteria for the final product.
For example, all assembled products must pass a quality check to ensure they meet predefined standards.
Example 2: Customer Service
For a customer service team, Standard Work might involve creating scripts for handling common customer inquiries.
This helps ensure that all customers receive consistent and accurate information.
The Work Standard would define the acceptable response time and resolution rate.
For example, all customer inquiries should be resolved within 24 hours, and the resolution rate should be at least 95%.
Conclusion
Understanding the difference between Standard Work and Work Standard is crucial for any organization aiming to improve efficiency and quality.
While Standard Work focuses on the best way to perform a task, Work Standard sets the criteria for acceptable performance.
By implementing both, you can create a robust framework that ensures consistency, quality, and continuous improvement.
Whether you are in manufacturing, customer service, or any other field, these principles can help you achieve operational excellence.
資料ダウンロード
QCD調達購買管理クラウド「newji」は、調達購買部門で必要なQCD管理全てを備えた、現場特化型兼クラウド型の今世紀最高の購買管理システムとなります。
ユーザー登録
調達購買業務の効率化だけでなく、システムを導入することで、コスト削減や製品・資材のステータス可視化のほか、属人化していた購買情報の共有化による内部不正防止や統制にも役立ちます。
NEWJI DX
製造業に特化したデジタルトランスフォーメーション(DX)の実現を目指す請負開発型のコンサルティングサービスです。AI、iPaaS、および先端の技術を駆使して、製造プロセスの効率化、業務効率化、チームワーク強化、コスト削減、品質向上を実現します。このサービスは、製造業の課題を深く理解し、それに対する最適なデジタルソリューションを提供することで、企業が持続的な成長とイノベーションを達成できるようサポートします。
オンライン講座
製造業、主に購買・調達部門にお勤めの方々に向けた情報を配信しております。
新任の方やベテランの方、管理職を対象とした幅広いコンテンツをご用意しております。
お問い合わせ
コストダウンが利益に直結する術だと理解していても、なかなか前に進めることができない状況。そんな時は、newjiのコストダウン自動化機能で大きく利益貢献しよう!
(Β版非公開)