- お役立ち記事
- The difference between Statistical Process Control (SPC) and Statistical Quality Control (SQC)
月間76,176名の
製造業ご担当者様が閲覧しています*
*2025年3月31日現在のGoogle Analyticsのデータより
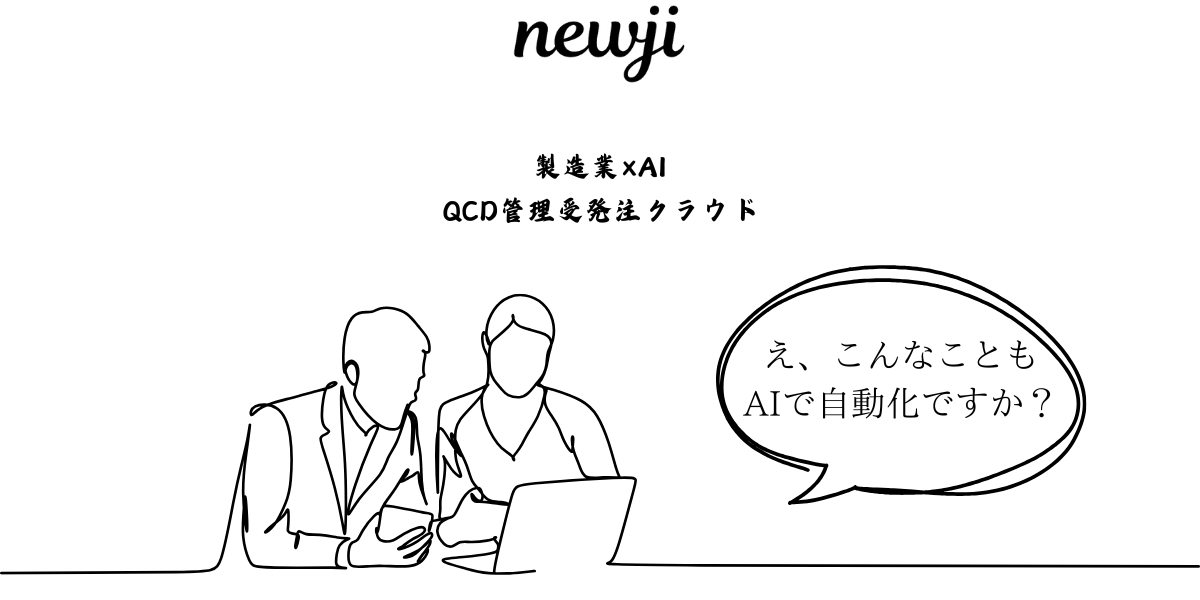
The difference between Statistical Process Control (SPC) and Statistical Quality Control (SQC)
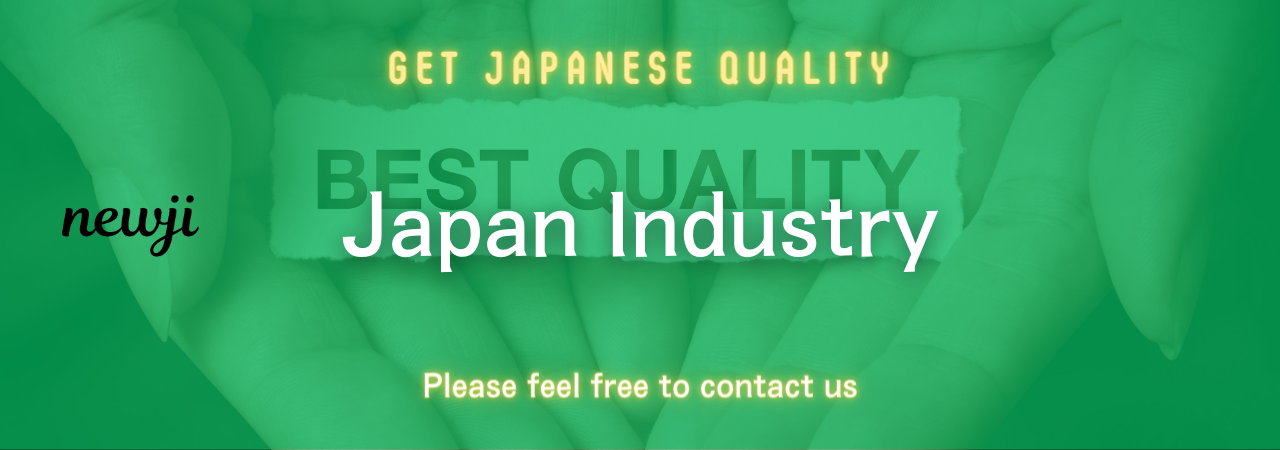
Statistical Process Control (SPC) and Statistical Quality Control (SQC) are crucial methodologies in the field of quality management and improvement.
Though they are often used interchangeably, they serve different purposes and have distinct methodologies.
Understanding these differences can dramatically improve the quality of products and processes in manufacturing and service sectors.
目次
What is Statistical Process Control (SPC)?
Statistical Process Control (SPC) is a method used to monitor and control a process to ensure that it operates at its full potential.
By using statistical techniques, SPC helps to reduce variability and maintain high-quality production.
The primary focus of SPC is on the process itself rather than the final product.
This proactive approach means spotting issues early on, allowing for corrections before producing defective items.
How SPC Works
SPC employs control charts to monitor process behavior over time.
These charts plot data points against time, highlighting variations that may be due to common causes or special causes.
Common causes are inherent to the process and predictably vary.
Special causes are unusual occurrences that require immediate attention.
By identifying and addressing these special causes, the process can be tweaked to return to its optimal state.
Key Benefits of SPC
1. **Early Problem Detection**: SPC provides real-time data, allowing for timely interventions.
2. **Improved Process Efficiency**: By reducing variability, SPC ensures the process is operating at peak performance.
3. **Cost-Effectiveness**: Fewer defects mean lower costs associated with rework, scrap, and customer complaints.
4. **Enhanced Customer Satisfaction**: Consistent, high-quality products lead to happier customers.
What is Statistical Quality Control (SQC)?
Statistical Quality Control (SQC) takes a broader view than SPC by focusing on both the process and the product.
It employs a range of statistical tools to analyze quality and pinpoint areas for improvement.
While SPC can be seen as a subset of SQC, SQC encompasses a more comprehensive set of quality techniques.
How SQC Works
SQC makes use of three primary categories of techniques:
1. **Descriptive Statistics**: This includes mean, median, range, and standard deviation, provides insights into the basic attributes of the data.
2. **Inferential Statistics**: Techniques such as hypothesis testing and regression analysis help make predictions and informed decisions based on data samples.
3. **Control Charts**: Though shared with SPC, control charts in SQC are used in a broader context to monitor both the process and product quality.
Key Benefits of SQC
1. **Holistic Approach**: SQC looks beyond just the process to include product evaluations as well.
2. **Strategic Decision-Making**: By employing a variety of statistical tools, SQC offers insights that guide long-term planning and improvements.
3. **Versatility**: Applicable across various processes and products, SQC is adaptable to different industries and quality needs.
Key Differences Between SPC and SQC
While SPC and SQC share common goals of improving quality and reducing defects, they differ in scope, methodology, and application.
Scope
SPC focuses narrowly on the process, aiming to maintain control and stability.
It’s about keeping the process in check to minimize variability.
In contrast, SQC encompasses both the product and the process.
It provides a broader view that allows for more comprehensive quality improvement strategies.
Methodology
SPC mainly utilizes control charts to monitor process variability over time.
It’s a real-time, ongoing method for spotting deviations and making immediate corrections.
SQC uses a wider range of statistical tools, including descriptive and inferential statistics.
These tools help in comprehensive data analysis, extending beyond the immediate process to include product quality assessments.
Application
In application, SPC is often seen in manufacturing environments where continuous monitoring is crucial.
It’s employed in real-time to ensure processes stay within acceptable limits.
SQC, however, finds use not only in manufacturing but also in service industries, research, and development where comprehensive quality evaluations are needed.
Integration of SPC and SQC
Although SPC and SQC have their unique features, integrating them can offer even more robust quality management solutions.
By combining the proactive, real-time control of SPC with the extensive analytical capabilities of SQC, organizations can achieve superior quality control.
Why Integrate?
1. **Comprehensive Monitoring**: Combining both approaches ensures both the process and final product meet quality standards.
2. **Enhanced Decision-Making**: The varied statistical tools from SQC add depth to the real-time data from SPC, enabling more informed decisions.
3. **Greater Flexibility**: An integrated approach can be adapted to different needs across various stages of production and service delivery.
Steps for Integration
1. **Assess Current Systems**: Examine existing SPC and SQC practices to identify gaps and areas for improvement.
2. **Train Personnel**: Ensure all team members understand both SPC and SQC methodologies and their respective benefits.
3. **Implement Control Charts**: Use control charts from SPC for real-time monitoring while employing SQC tools for comprehensive analysis.
4. **Continuous Review**: Regularly evaluate the integrated system to ensure it meets the desired quality objectives.
Conclusion
Understanding the difference between Statistical Process Control (SPC) and Statistical Quality Control (SQC) is fundamental for effective quality management.
While SPC helps in real-time control by focusing on the process, SQC provides a holistic view encompassing both process and product.
Integrating both approaches can offer a powerful toolset for achieving excellence in quality, enhancing customer satisfaction, and boosting efficiency.
By leveraging the strengths of both SPC and SQC, organizations can maintain superior quality control, reduce costs, and stay competitive in today’s market.
資料ダウンロード
QCD管理受発注クラウド「newji」は、受発注部門で必要なQCD管理全てを備えた、現場特化型兼クラウド型の今世紀最高の受発注管理システムとなります。
ユーザー登録
受発注業務の効率化だけでなく、システムを導入することで、コスト削減や製品・資材のステータス可視化のほか、属人化していた受発注情報の共有化による内部不正防止や統制にも役立ちます。
NEWJI DX
製造業に特化したデジタルトランスフォーメーション(DX)の実現を目指す請負開発型のコンサルティングサービスです。AI、iPaaS、および先端の技術を駆使して、製造プロセスの効率化、業務効率化、チームワーク強化、コスト削減、品質向上を実現します。このサービスは、製造業の課題を深く理解し、それに対する最適なデジタルソリューションを提供することで、企業が持続的な成長とイノベーションを達成できるようサポートします。
製造業ニュース解説
製造業、主に購買・調達部門にお勤めの方々に向けた情報を配信しております。
新任の方やベテランの方、管理職を対象とした幅広いコンテンツをご用意しております。
お問い合わせ
コストダウンが利益に直結する術だと理解していても、なかなか前に進めることができない状況。そんな時は、newjiのコストダウン自動化機能で大きく利益貢献しよう!
(β版非公開)