- お役立ち記事
- The difference between Statistical Quality Control (SQC) and Statistical Process Control (SPC)
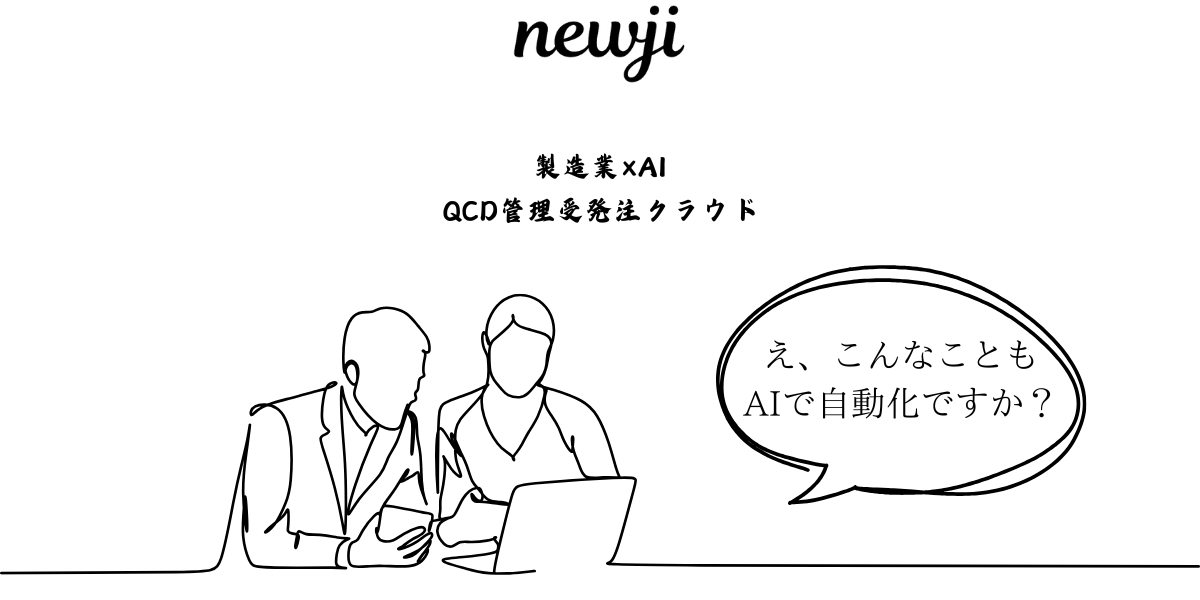
The difference between Statistical Quality Control (SQC) and Statistical Process Control (SPC)
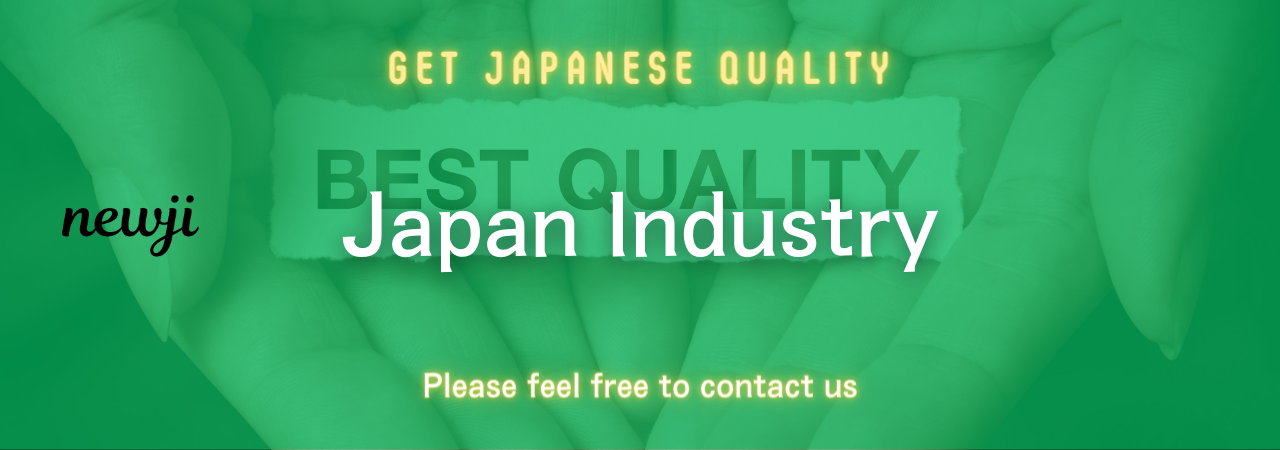
Understanding the nuances between Statistical Quality Control (SQC) and Statistical Process Control (SPC) is essential for businesses aiming to improve their service quality and manufacturing processes.
Both methods are powerful tools used to ensure products meet customer expectations and regulatory requirements.
However, they are distinct in their applications and focus.
目次
Defining Statistical Quality Control (SQC)
Statistical Quality Control is a broad term that encompasses various statistical methodologies used to evaluate a product’s quality during different stages of the production cycle.
SQC provides a holistic view and is used to identify issues, measure performance, and apply remedial actions.
Some of the core functions within SQC include:
Inspection and Testing
Inspection and testing occur at different stages of production.
Lots or batches of products are randomly selected and tested for various quality attributes.
This allows for the identification of defective products before they reach the customer.
Acceptance Sampling
Acceptance sampling is another vital component of SQC.
It involves specifying a sampling plan that defines the number of units to be tested from a batch, and the criteria for accepting or rejecting the lot based on the inspection results.
Control Charts
Control charts are statistical tools used for monitoring the state of control in a production process.
They graph the variations in product quality metrics over time and help identify whether these variations are within acceptable limits or if they signify an underlying issue that requires intervention.
Defining Statistical Process Control (SPC)
Statistical Process Control, on the other hand, is more focused on the processes involved in manufacturing or service delivery.
SPC uses specific statistical methods to monitor and control a process to ensure that it operates at its full potential.
Different tools and techniques of SPC help in identifying and eliminating variability in the process, thus ensuring consistency.
Real-time Monitoring
A key attribute of SPC is real-time monitoring.
Data is collected and analyzed while the process is running.
This allows for immediate corrective actions if any deviation from the set standards occurs, thus preventing flawed products from being produced.
Control Limits
Control limits are pre-defined boundaries within which a process should operate to be considered in control.
These limits are usually set at three standard deviations from the mean.
If data points fall outside these limits, it indicates that the process may have developed a problem requiring corrective measures.
Process Capability Analysis
Process capability analysis is another critical aspect of SPC.
It evaluates the ability of a process to produce products that meet specifications consistently.
Indices such as Cp and Cpk are calculated to understand the extent to which processes can produce outputs within specified limits.
The Key Differences Between SQC and SPC
Although both SQC and SPC use statistical methods, their focus areas and applications differ significantly.
Understanding these differences can help businesses apply the right tool for quality improvement.
Scope and Focus
SQC has a broader scope compared to SPC.
It encompasses various stages of quality checks, from raw material inspection to final product testing.
SPC, however, is more focused on the processes involved in production or service delivery rather than the final product.
Time of Application
SQC methods are often employed after the product has been produced.
Inspections and tests are conducted to ensure that the product meets the predefined quality criteria.
In contrast, SPC is used during the production process.
Its aim is to monitor and control the process to prevent defects from occurring in the first place.
Corrective Measures
Because SQC involves post-production inspection, corrective measures often involve rejecting defective batches and investigating root causes retrospectively.
On the other hand, SPC enables real-time corrective actions, making adjustments as soon as process variability is detected.
Data Usage
In SQC, the data is often historical and used to understand trends and performance over a period.
SPC, however, generates real-time data which is used for immediate decision-making and interventions.
Practical Applications of SQC and SPC
Both SQC and SPC have wide-ranging applications across various industries, each providing unique benefits.
Manufacturing Sector
In manufacturing, SQC is commonly used to ensure that end products meet quality standards before they are shipped to customers.
It is particularly useful in sectors like automotive and aerospace, where product specifications are critical.
SPC, on the other hand, is utilized to monitor machinery and production lines continuously.
This helps in maintaining consistent quality and reducing downtime due to defects or equipment failure.
Service Industry
In the service industry, SQC can be used to assess the quality of services provided.
For instance, customer feedback and satisfaction scores can be analyzed to improve service delivery.
SPC is also vital in services, particularly in roles like call centers where operational processes can be monitored in real-time to ensure efficiency and customer satisfaction.
Healthcare
In healthcare, SQC methods are employed to ensure that medical devices, pharmaceuticals, and clinical practices meet stringent quality norms.
Acceptance sampling and control charts can help in maintaining high levels of patient safety and product efficacy.
SPC in healthcare is used for real-time monitoring of processes such as laboratory tests, surgeries, and patient care routines.
By maintaining tight control over these processes, healthcare providers can ensure better patient outcomes and service quality.
Choosing the Right Approach
Deciding whether to use SQC or SPC depends on the specific needs and objectives of a business.
For organizations looking to improve the end product’s quality and gather performance metrics retrospectively, SQC is the way to go.
However, if the aim is to maintain tight control over the production process and reduce variability, SPC would be more appropriate.
In many cases, combining both SQC and SPC provides a more comprehensive approach to quality management.
Leveraging the strengths of both can help businesses achieve higher levels of efficiency, customer satisfaction, and compliance.
Understanding the distinct yet complementary roles of SQC and SPC can empower businesses to make informed decisions regarding their quality control strategies.
By applying the right methods at the right stages, companies can not only meet but exceed quality expectations, resulting in long-term success and customer loyalty.
資料ダウンロード
QCD調達購買管理クラウド「newji」は、調達購買部門で必要なQCD管理全てを備えた、現場特化型兼クラウド型の今世紀最高の購買管理システムとなります。
ユーザー登録
調達購買業務の効率化だけでなく、システムを導入することで、コスト削減や製品・資材のステータス可視化のほか、属人化していた購買情報の共有化による内部不正防止や統制にも役立ちます。
NEWJI DX
製造業に特化したデジタルトランスフォーメーション(DX)の実現を目指す請負開発型のコンサルティングサービスです。AI、iPaaS、および先端の技術を駆使して、製造プロセスの効率化、業務効率化、チームワーク強化、コスト削減、品質向上を実現します。このサービスは、製造業の課題を深く理解し、それに対する最適なデジタルソリューションを提供することで、企業が持続的な成長とイノベーションを達成できるようサポートします。
オンライン講座
製造業、主に購買・調達部門にお勤めの方々に向けた情報を配信しております。
新任の方やベテランの方、管理職を対象とした幅広いコンテンツをご用意しております。
お問い合わせ
コストダウンが利益に直結する術だと理解していても、なかなか前に進めることができない状況。そんな時は、newjiのコストダウン自動化機能で大きく利益貢献しよう!
(Β版非公開)